Information injection-pump assembly
BOSCH
9 400 610 244
9400610244
ZEXEL
101601-3211
1016013211
KOMATSU
6138721160
6138721160
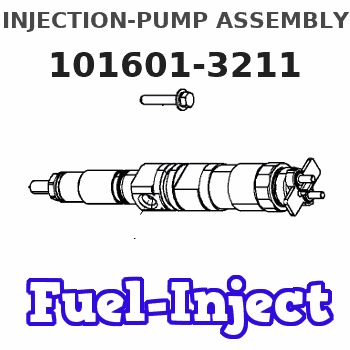
Rating:
Service parts 101601-3211 INJECTION-PUMP ASSEMBLY:
1.
_
7.
COUPLING PLATE
8.
_
9.
_
11.
Nozzle and Holder
6138-12-3300
12.
Open Pre:MPa(Kqf/cm2)
24.5{250}
15.
NOZZLE SET
Cross reference number
BOSCH
9 400 610 244
9400610244
ZEXEL
101601-3211
1016013211
KOMATSU
6138721160
6138721160
Zexel num
Bosch num
Firm num
Name
9 400 610 244
6138721160 KOMATSU
INJECTION-PUMP ASSEMBLY
S6D110 * K 14BF INJECTION PUMP ASSY PE6AD PE
S6D110 * K 14BF INJECTION PUMP ASSY PE6AD PE
Calibration Data:
Adjustment conditions
Test oil
1404 Test oil ISO4113 or {SAEJ967d}
1404 Test oil ISO4113 or {SAEJ967d}
Test oil temperature
degC
40
40
45
Nozzle and nozzle holder
105780-8140
Bosch type code
EF8511/9A
Nozzle
105780-0000
Bosch type code
DN12SD12T
Nozzle holder
105780-2080
Bosch type code
EF8511/9
Opening pressure
MPa
17.2
Opening pressure
kgf/cm2
175
Injection pipe
Outer diameter - inner diameter - length (mm) mm 6-2-600
Outer diameter - inner diameter - length (mm) mm 6-2-600
Tester oil delivery pressure
kPa
157
157
157
Tester oil delivery pressure
kgf/cm2
1.6
1.6
1.6
Direction of rotation (viewed from drive side)
Right R
Right R
Injection timing adjustment
Direction of rotation (viewed from drive side)
Right R
Right R
Injection order
1-5-3-6-
2-4
Pre-stroke
mm
4
3.95
4.05
Beginning of injection position
Drive side NO.1
Drive side NO.1
Difference between angles 1
Cal 1-5 deg. 60 59.5 60.5
Cal 1-5 deg. 60 59.5 60.5
Difference between angles 2
Cal 1-3 deg. 120 119.5 120.5
Cal 1-3 deg. 120 119.5 120.5
Difference between angles 3
Cal 1-6 deg. 180 179.5 180.5
Cal 1-6 deg. 180 179.5 180.5
Difference between angles 4
Cyl.1-2 deg. 240 239.5 240.5
Cyl.1-2 deg. 240 239.5 240.5
Difference between angles 5
Cal 1-4 deg. 300 299.5 300.5
Cal 1-4 deg. 300 299.5 300.5
Injection quantity adjustment
Adjusting point
A
Rack position
10
Pump speed
r/min
1100
1100
1100
Average injection quantity
mm3/st.
77
76
78
Max. variation between cylinders
%
0
-2
2
Basic
*
Fixing the lever
*
Injection quantity adjustment_02
Adjusting point
B
Rack position
8+-0.5
Pump speed
r/min
350
350
350
Average injection quantity
mm3/st.
12.3
11.1
13.5
Max. variation between cylinders
%
0
-10
10
Fixing the rack
*
Remarks
Adjust only variation between cylinders; adjust governor according to governor specifications.
Adjust only variation between cylinders; adjust governor according to governor specifications.
Timer adjustment
Pump speed
r/min
750--
Advance angle
deg.
0
0
0
Remarks
Start
Start
Timer adjustment_02
Pump speed
r/min
700
Advance angle
deg.
0.5
Timer adjustment_03
Pump speed
r/min
900
Advance angle
deg.
1.4
0.9
1.9
Timer adjustment_04
Pump speed
r/min
1100
Advance angle
deg.
2.8
2.3
3.3
Timer adjustment_05
Pump speed
r/min
-
Advance angle
deg.
5
4.5
5.5
Remarks
Measure the actual speed, stop
Measure the actual speed, stop
Test data Ex:
Governor adjustment
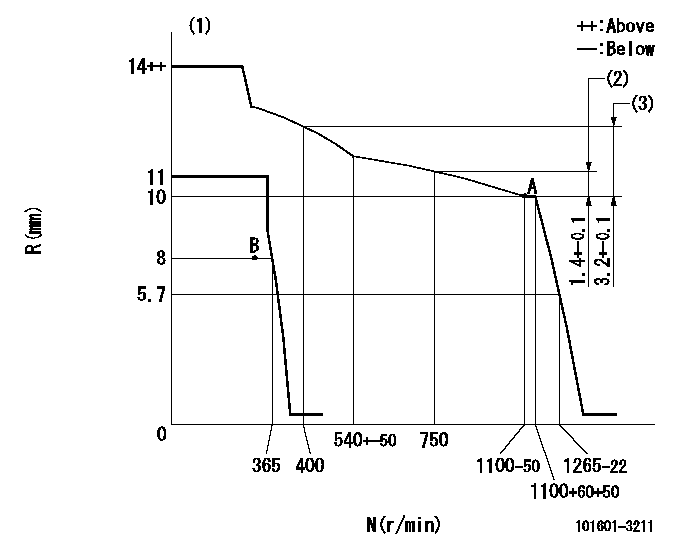
N:Pump speed
R:Rack position (mm)
(1)Target notch: K
(2)Rack difference between N = N1 and N = N2
(3)Rack difference between N = N3 and N = N4
----------
K=14 N1=1100r/min N2=750r/min N3=1100r/min N4=400r/min
----------
----------
K=14 N1=1100r/min N2=750r/min N3=1100r/min N4=400r/min
----------
Speed control lever angle
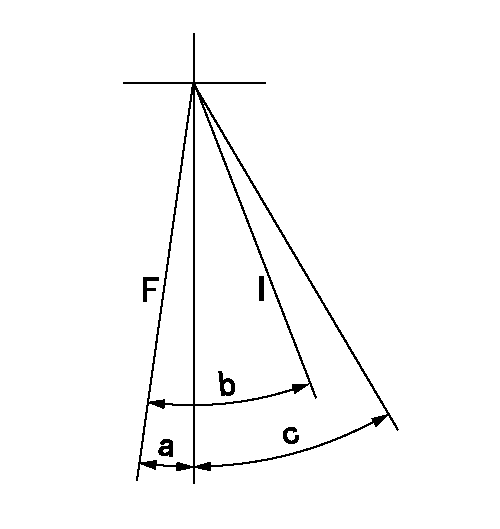
F:Full speed
I:Idle
----------
----------
a=8deg+-5deg b=24deg+-5deg c=32deg+-3deg
----------
----------
a=8deg+-5deg b=24deg+-5deg c=32deg+-3deg
0000001501 LEVER

(F) P/N: Part number of the shim
L1:Thickness (mm)
1. Adjustment of the control lever
(1)Perform idling with the control lever (A) contacting the pushrod (B). At this time, confirm that the spring (C) is not compressed by control lever (A)'s operating torque.
(2)To set the stop position, compress spring (C) using the control lever (A) and adjust the rack so that it contacts the guide screw (D) at position L2. Then, set and fix using the lock nut (E). Adjust the rack position L2 at this time using the shim (F).
(3)Confirm that the control lever (A) returns to the idling position when pulled in the stop direction and then released.
----------
L2=0.2~2mm
----------
----------
L2=0.2~2mm
----------
Timing setting

(1)Pump vertical direction
(2)Coupling's key groove position at No 1 cylinder's beginning of injection
(3)-
(4)-
----------
----------
a=(0deg)
----------
----------
a=(0deg)
Information:
(1) Diameter of the surfaces (journals) for the camshaft bearings (new) ... 63.500 0.013 mm (2.5000 .0005 in) Bore in the five bearings for the camshaft (new) ... 63.589 0.038 mm (2.5035 .0015 in)Maximum permissible clearance between bearing and bearing surface (journal) (worn) ... 0.18 mm (.007 in)(2) Tight fit between the gear and camshaft ... 0.030 to 0.071 mm (.0012 to .0028 in) Maximum permissible temperature of the gear for installation on the camshaft (do not use a torch) ... 315°C (600°F)(3) End play for the camshaft ... 0.18 0.08 mm (.007 .003 in) Maximum permissible end play (worn) ... 0.51 mm (.020 in)(4) Width of thrust groove in camshaft (new) ... 9.14 0.05 mm (.360 .002 in) Diameter of thrust pin (new) ... 8.97 0.03 mm (.353 .001 in)Torque for thrust pin ... 48 7 N m (35 5 lb ft)(5) Height of camshaft lobes.To find lobe lift, use the procedure that follows:A. Measure camshaft lobe height (5).B. Measure base circle (7).C. Subtract base circle (Step B) from lobe height (Step A). The difference is actual lobe lift (6).D. Specified camshaft lobe lift (6) is: 9N5230 Camshaft used with roller lifters: a. Exhaust lobe ... 9.40 mm (.370 in) b. Intake lobe ... 9.33 mm (.367 in)2W4238 Camshaft used with flat face lifters: c. Exhaust lobe ... 9.40 mm (.370 in) d. Intake lobe ... 9.06 mm (.357 in)Maximum permissible difference between actual lobe lift (Step C) and specified lobe lift (Step D) is 0.25 mm (.010 in).
Camshaft Gear Assembly
View A-A(8) Distance from the end of 9N5771 Dowell to the face of gear ... 11.81 0.13 mm(.465 .005 in)
View B-B(9) Distance from the end of 5P4283 Dowel to the face of camshaft ... 2.00 0.25 mm(.079 .010 in)Camshaft Installation
For installation of camshaft, the timing mark on the camshaft gear tooth must be in alignment with the timing mark on the tooth space of the crankshaft gear.Intake Valve Timing
1. Check the No. 1 intake valve clearance with the engine stopped. The valve clearance must be 0.30 to 0.46 mm (.012 to .018 in). If the valve clearance is not in this range, adjust the clearance to 0.38 mm (.015 in).2. Mark Top Center Position of the crankshaft on the vibration damper or pulley.3. Use a dial indicator to measure the intake valve movement.4. Rotate the crankshaft in the direction of normal engine rotation. Stop when the intake valve is 1.91 mm (.075 in) off its seat in the opening sequence. At this point the crankshaft must be 10 2° After Top Center.
Camshaft Gear Assembly
View A-A(8) Distance from the end of 9N5771 Dowell to the face of gear ... 11.81 0.13 mm(.465 .005 in)
View B-B(9) Distance from the end of 5P4283 Dowel to the face of camshaft ... 2.00 0.25 mm(.079 .010 in)Camshaft Installation
For installation of camshaft, the timing mark on the camshaft gear tooth must be in alignment with the timing mark on the tooth space of the crankshaft gear.Intake Valve Timing
1. Check the No. 1 intake valve clearance with the engine stopped. The valve clearance must be 0.30 to 0.46 mm (.012 to .018 in). If the valve clearance is not in this range, adjust the clearance to 0.38 mm (.015 in).2. Mark Top Center Position of the crankshaft on the vibration damper or pulley.3. Use a dial indicator to measure the intake valve movement.4. Rotate the crankshaft in the direction of normal engine rotation. Stop when the intake valve is 1.91 mm (.075 in) off its seat in the opening sequence. At this point the crankshaft must be 10 2° After Top Center.