Information injection-pump assembly
BOSCH
9 400 610 197
9400610197
ZEXEL
101601-3170
1016013170
KOMATSU
6138721110
6138721110
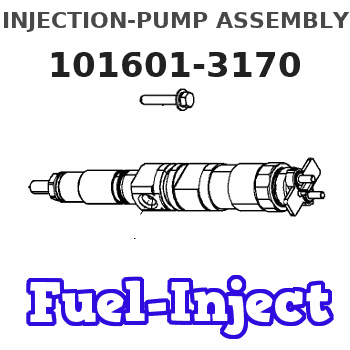
Rating:
Compare Prices: .
As an associate, we earn commssions on qualifying purchases through the links below
Service parts 101601-3170 INJECTION-PUMP ASSEMBLY:
1.
_
7.
COUPLING PLATE
8.
_
9.
_
11.
Nozzle and Holder
6138-12-3300
12.
Open Pre:MPa(Kqf/cm2)
24.5{250}
15.
NOZZLE SET
Cross reference number
BOSCH
9 400 610 197
9400610197
ZEXEL
101601-3170
1016013170
KOMATSU
6138721110
6138721110
Zexel num
Bosch num
Firm num
Name
9 400 610 197
6138721110 KOMATSU
INJECTION-PUMP ASSEMBLY
SA6D110 K 14BF INJECTION PUMP ASSY PE6AD PE
SA6D110 K 14BF INJECTION PUMP ASSY PE6AD PE
Calibration Data:
Adjustment conditions
Test oil
1404 Test oil ISO4113 or {SAEJ967d}
1404 Test oil ISO4113 or {SAEJ967d}
Test oil temperature
degC
40
40
45
Nozzle and nozzle holder
105780-8140
Bosch type code
EF8511/9A
Nozzle
105780-0000
Bosch type code
DN12SD12T
Nozzle holder
105780-2080
Bosch type code
EF8511/9
Opening pressure
MPa
17.2
Opening pressure
kgf/cm2
175
Injection pipe
Outer diameter - inner diameter - length (mm) mm 6-2-600
Outer diameter - inner diameter - length (mm) mm 6-2-600
Tester oil delivery pressure
kPa
157
157
157
Tester oil delivery pressure
kgf/cm2
1.6
1.6
1.6
Direction of rotation (viewed from drive side)
Right R
Right R
Injection timing adjustment
Direction of rotation (viewed from drive side)
Right R
Right R
Injection order
1-5-3-6-
2-4
Pre-stroke
mm
4
3.95
4.05
Beginning of injection position
Drive side NO.1
Drive side NO.1
Difference between angles 1
Cal 1-5 deg. 60 59.5 60.5
Cal 1-5 deg. 60 59.5 60.5
Difference between angles 2
Cal 1-3 deg. 120 119.5 120.5
Cal 1-3 deg. 120 119.5 120.5
Difference between angles 3
Cal 1-6 deg. 180 179.5 180.5
Cal 1-6 deg. 180 179.5 180.5
Difference between angles 4
Cyl.1-2 deg. 240 239.5 240.5
Cyl.1-2 deg. 240 239.5 240.5
Difference between angles 5
Cal 1-4 deg. 300 299.5 300.5
Cal 1-4 deg. 300 299.5 300.5
Injection quantity adjustment
Adjusting point
A
Rack position
10.5
Pump speed
r/min
1100
1100
1100
Average injection quantity
mm3/st.
85.8
84.8
86.8
Max. variation between cylinders
%
0
-2
2
Basic
*
Fixing the lever
*
Boost pressure
kPa
40
40
Boost pressure
mmHg
300
300
Injection quantity adjustment_02
Adjusting point
B
Rack position
7.4+-0.5
Pump speed
r/min
375
375
375
Average injection quantity
mm3/st.
15.5
14.3
16.7
Max. variation between cylinders
%
0
-10
10
Fixing the rack
*
Boost pressure
kPa
0
0
0
Boost pressure
mmHg
0
0
0
Boost compensator adjustment
Pump speed
r/min
600
600
600
Rack position
10..5
Boost pressure
kPa
10.7
8
13.4
Boost pressure
mmHg
80
60
100
Boost compensator adjustment_02
Pump speed
r/min
600
600
600
Rack position
11.5
Boost pressure
kPa
26.7
26.7
26.7
Boost pressure
mmHg
200
200
200
Timer adjustment
Pump speed
r/min
750--
Advance angle
deg.
0
0
0
Remarks
Start
Start
Timer adjustment_02
Pump speed
r/min
700
Advance angle
deg.
0.5
Timer adjustment_03
Pump speed
r/min
900
Advance angle
deg.
1.4
0.9
1.9
Timer adjustment_04
Pump speed
r/min
1100
Advance angle
deg.
2.8
2.3
3.3
Timer adjustment_05
Pump speed
r/min
-
Advance angle
deg.
5
4.5
5.5
Remarks
Measure the actual speed, stop
Measure the actual speed, stop
Test data Ex:
Governor adjustment

N:Pump speed
R:Rack position (mm)
(1)Target notch: K
(2)Boost compensator stroke
(3)Rack difference between N = N1 and N = N2
(4)Rack difference between N = N3 and N = N4
----------
K=16 N1=1100r/min N2=750r/min N3=1100r/min N4=400r/min
----------
----------
K=16 N1=1100r/min N2=750r/min N3=1100r/min N4=400r/min
----------
Speed control lever angle

F:Full speed
I:Idle
(1)Stopper bolt setting
----------
----------
a=8deg+-5deg b=23deg+-5deg
----------
----------
a=8deg+-5deg b=23deg+-5deg
Stop lever angle

N:Pump normal
S:Stop the pump.
(1)At shipping
(2)Set the stopper bolt at speed = aa and rack position = bb (seal for delivery after setting the stopper bolt).
----------
aa=0r/min bb=1-0.2mm
----------
a=21deg+-5deg b=(52deg)
----------
aa=0r/min bb=1-0.2mm
----------
a=21deg+-5deg b=(52deg)
Timing setting

(1)Pump vertical direction
(2)Coupling's key groove position at No 1 cylinder's beginning of injection
(3)-
(4)-
----------
----------
a=(0deg)
----------
----------
a=(0deg)
Information:
Introduction
Diesel Particulate Filters (DPF) and Catalytic Converter Mufflers (CCM) are not applicable to all engines. Some engines contain a DPF and a CCM device that were installed as original equipment to meet engine emissions certification requirements. However, some engines may have had the devices installed during a retrofit program for emissions reduction.
Do not perform any procedure in this Special Instruction until you read this information and you understand this information.Procedure for Shipping the Diesel Particulate Filters (DPF)
Wear goggles, gloves, protective clothing, and a National Institute for Occupational Safety and Health (NIOSH) approved P95 or N95 half-face respirator when handling a used Diesel Particulate Filter or Catalytic Converter Muffler. Failure to do so could result in personal injury.
Place all the used Diesel Particulate Filter (DPF) center sections, regardless of condition, into a 0.152 mm (0.006 inch) thick plastic bag. Make sure that the bag is sealed before placing the DPF into a shipping container. This must be performed in order to contain any constituents from the used DPF during shipping. New replacement diesel particulate filters may come with a 0.152 mm (0.006 inch) plastic bag that can be used for wrapping the used DPF.Procedure for Shipping the Catalytic Converter Mufflers (CCM)
Seal the inlet port and the outlet port on all used Catalytic Converter Mufflers (CCM) with rubber caps or plastic caps. Various sized plastic caps can be ordered from the Cat Shop Supplies and Hand Tools catalog. Reference caps and plugs under the Shop Supplies section. An alternative is to seal the inlet ports and outlet ports with a 0.152 mm (0.006 inch) thick sheet of plastic and 50 mm (2 inch) wide sealing tape with good adhesive properties before shipping. Sealing or capping must be performed in order to contain any constituents from the used CCM during shipping.
Diesel Particulate Filters (DPF) and Catalytic Converter Mufflers (CCM) are not applicable to all engines. Some engines contain a DPF and a CCM device that were installed as original equipment to meet engine emissions certification requirements. However, some engines may have had the devices installed during a retrofit program for emissions reduction.
Do not perform any procedure in this Special Instruction until you read this information and you understand this information.Procedure for Shipping the Diesel Particulate Filters (DPF)
Wear goggles, gloves, protective clothing, and a National Institute for Occupational Safety and Health (NIOSH) approved P95 or N95 half-face respirator when handling a used Diesel Particulate Filter or Catalytic Converter Muffler. Failure to do so could result in personal injury.
Place all the used Diesel Particulate Filter (DPF) center sections, regardless of condition, into a 0.152 mm (0.006 inch) thick plastic bag. Make sure that the bag is sealed before placing the DPF into a shipping container. This must be performed in order to contain any constituents from the used DPF during shipping. New replacement diesel particulate filters may come with a 0.152 mm (0.006 inch) plastic bag that can be used for wrapping the used DPF.Procedure for Shipping the Catalytic Converter Mufflers (CCM)
Seal the inlet port and the outlet port on all used Catalytic Converter Mufflers (CCM) with rubber caps or plastic caps. Various sized plastic caps can be ordered from the Cat Shop Supplies and Hand Tools catalog. Reference caps and plugs under the Shop Supplies section. An alternative is to seal the inlet ports and outlet ports with a 0.152 mm (0.006 inch) thick sheet of plastic and 50 mm (2 inch) wide sealing tape with good adhesive properties before shipping. Sealing or capping must be performed in order to contain any constituents from the used CCM during shipping.