Information injection-pump assembly
ZEXEL
101601-2440
1016012440
HINO
220002240B
220002240b
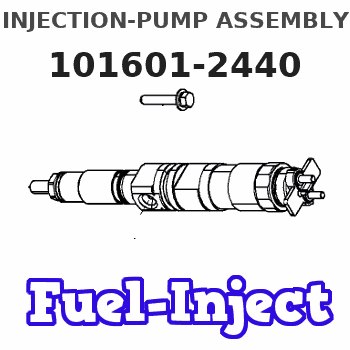
Rating:
Cross reference number
ZEXEL
101601-2440
1016012440
HINO
220002240B
220002240b
Zexel num
Bosch num
Firm num
Name
Calibration Data:
Adjustment conditions
Test oil
1404 Test oil ISO4113 or {SAEJ967d}
1404 Test oil ISO4113 or {SAEJ967d}
Test oil temperature
degC
40
40
45
Nozzle and nozzle holder
105780-8140
Bosch type code
EF8511/9A
Nozzle
105780-0000
Bosch type code
DN12SD12T
Nozzle holder
105780-2080
Bosch type code
EF8511/9
Opening pressure
MPa
17.2
Opening pressure
kgf/cm2
175
Injection pipe
Outer diameter - inner diameter - length (mm) mm 6-2-600
Outer diameter - inner diameter - length (mm) mm 6-2-600
Overflow valve
134424-0920
Overflow valve opening pressure
kPa
162
147
177
Overflow valve opening pressure
kgf/cm2
1.65
1.5
1.8
Tester oil delivery pressure
kPa
157
157
157
Tester oil delivery pressure
kgf/cm2
1.6
1.6
1.6
Direction of rotation (viewed from drive side)
Right R
Right R
Injection timing adjustment
Direction of rotation (viewed from drive side)
Right R
Right R
Injection order
1-4-2-6-
3-5
Pre-stroke
mm
3.1
3.07
3.13
Beginning of injection position
Drive side NO.1
Drive side NO.1
Difference between angles 1
Cal 1-4 deg. 60 59.75 60.25
Cal 1-4 deg. 60 59.75 60.25
Difference between angles 2
Cyl.1-2 deg. 120 119.75 120.25
Cyl.1-2 deg. 120 119.75 120.25
Difference between angles 3
Cal 1-6 deg. 180 179.75 180.25
Cal 1-6 deg. 180 179.75 180.25
Difference between angles 4
Cal 1-3 deg. 240 239.75 240.25
Cal 1-3 deg. 240 239.75 240.25
Difference between angles 5
Cal 1-5 deg. 300 299.75 300.25
Cal 1-5 deg. 300 299.75 300.25
Injection quantity adjustment
Adjusting point
A
Rack position
6.6
Pump speed
r/min
1000
1000
1000
Average injection quantity
mm3/st.
65.6
64.6
66.6
Max. variation between cylinders
%
0
-3.5
3.5
Basic
*
Fixing the lever
*
Injection quantity adjustment_02
Adjusting point
B
Rack position
6.6
Pump speed
r/min
1500
1500
1500
Average injection quantity
mm3/st.
65.5
64
67
Max. variation between cylinders
%
0
-5
5
Fixing the lever
*
Injection quantity adjustment_03
Adjusting point
C
Rack position
5.2+-0.5
Pump speed
r/min
375
375
375
Average injection quantity
mm3/st.
8
7
9
Max. variation between cylinders
%
0
-10
10
Fixing the rack
*
Remarks
Adjust only variation between cylinders; adjust governor according to governor specifications.
Adjust only variation between cylinders; adjust governor according to governor specifications.
Timer adjustment
Pump speed
r/min
1350
Advance angle
deg.
0.5
Timer adjustment_02
Pump speed
r/min
1400
Advance angle
deg.
1.5
Timer adjustment_03
Pump speed
r/min
1600
Advance angle
deg.
5
4.7
5.3
Remarks
Finish
Finish
Test data Ex:
Governor adjustment
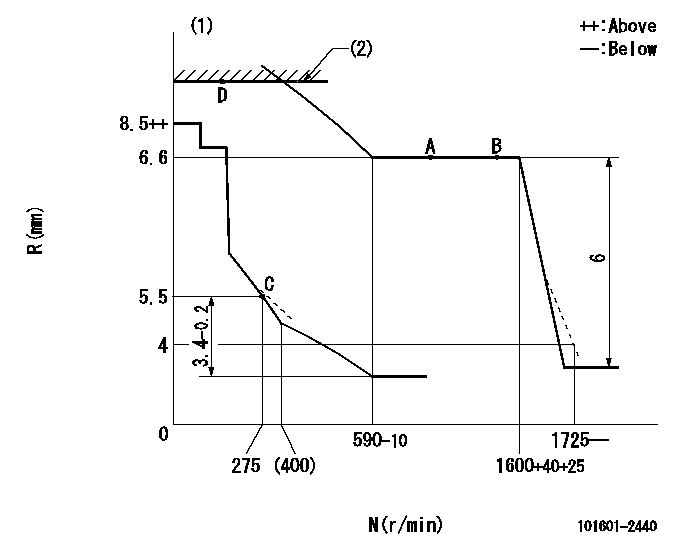
N:Pump speed
R:Rack position (mm)
(1)Beginning of damper spring operation: DL
(2)RACK LIMIT: RAL
----------
DL=5.7-0.2mm RAL=9.8+0.2mm
----------
----------
DL=5.7-0.2mm RAL=9.8+0.2mm
----------
Speed control lever angle

F:Full speed
----------
----------
a=15deg+-5deg
----------
----------
a=15deg+-5deg
0000000901

F:Full load
I:Idle
(1)Stopper bolt setting
----------
----------
a=24deg+-5deg b=26deg+-3deg
----------
----------
a=24deg+-5deg b=26deg+-3deg
Stop lever angle

N:Pump normal
S:Stop the pump.
----------
----------
a=21deg+-5deg b=69deg+-5deg
----------
----------
a=21deg+-5deg b=69deg+-5deg
0000001501 MICRO SWITCH
Switch adjustment
Adjust the bolt so that the lower lever position is obtained when the switch is turned ON.
(1)Speed N1
(2)Rack position Ra
----------
N1=375-25r/min Ra=5.5mm
----------
----------
N1=375-25r/min Ra=5.5mm
----------
Information:
1. Remove all of bolts (1) and bolts (2) and (3).2. Use two 3/8"-16 NC forcing screws and remove stator (4) from the flywheel housing. 3. If necessary remove the lip type seal from stator (4) with a hammer and punch. 4. Remove the six O-ring seals (6) from the flywheel housing.5. Remove rotor (5) from the crankshaft. 6. Remove the seal ring from carrier (8).7. If necessary remove carrier (8) and sleeve (7) from rotor (5). The carrier and sleeve will have damage after removal. Use new parts for replacement.Install BrakeSaver
1. If the carrier and sleeve were removed from the rotor, heat the new parts to a maximum temperature of 300° F (149° C). 2. Install carrier (2) on rotor (3).3. Put 7M7260 Liquid Gasket Material on the outside diameter (4) of rotor (3) and let it dry. Install sleeve (1) on rotor (3) as shown. 4. Install seal ring (5) in the carrier. 5. Install two 3/4"-16 NF guide bolts (6) a minimum of 5 in. long in the crankshaft.6. Make sure the O-ring seal is on rear face of the crankshaft seal carrier and install rotor (3) on the guide bolts with the marked bolt hole of the rotor in alignment with the marked hole of the crankshaft. 7. Use tool (A) and a press to install the seal in stator (7) as shown. 8. Install O-ring seal in position on stator (7). Install O-ring seals (8) in the flywheel housing.9. Put stator (7) in position on the flywheel housing. 10. Put 9S3263 Thread Lock on the threads of the bolts that hold the stator and install them. Tighten all of bolts (9) evenly to a torque of 40 5 lb. ft. (55 7 N m). Tighten bolts (10) and (11) to a torque of 90 10 lb. ft. (120 14 N m).end by: a) install flywheel
1. If the carrier and sleeve were removed from the rotor, heat the new parts to a maximum temperature of 300° F (149° C). 2. Install carrier (2) on rotor (3).3. Put 7M7260 Liquid Gasket Material on the outside diameter (4) of rotor (3) and let it dry. Install sleeve (1) on rotor (3) as shown. 4. Install seal ring (5) in the carrier. 5. Install two 3/4"-16 NF guide bolts (6) a minimum of 5 in. long in the crankshaft.6. Make sure the O-ring seal is on rear face of the crankshaft seal carrier and install rotor (3) on the guide bolts with the marked bolt hole of the rotor in alignment with the marked hole of the crankshaft. 7. Use tool (A) and a press to install the seal in stator (7) as shown. 8. Install O-ring seal in position on stator (7). Install O-ring seals (8) in the flywheel housing.9. Put stator (7) in position on the flywheel housing. 10. Put 9S3263 Thread Lock on the threads of the bolts that hold the stator and install them. Tighten all of bolts (9) evenly to a torque of 40 5 lb. ft. (55 7 N m). Tighten bolts (10) and (11) to a torque of 90 10 lb. ft. (120 14 N m).end by: a) install flywheel