Information injection-pump assembly
BOSCH
9 400 614 557
9400614557
ZEXEL
101502-9120
1015029120
KUBOTA
1G41651011
1g41651011

Rating:
Service parts 101502-9120 INJECTION-PUMP ASSEMBLY:
1.
_
6.
COUPLING PLATE
7.
COUPLING PLATE
8.
_
9.
_
11.
Nozzle and Holder
12.
Open Pre:MPa(Kqf/cm2)
18.6{190}/22.6{230}
15.
NOZZLE SET
Cross reference number
BOSCH
9 400 614 557
9400614557
ZEXEL
101502-9120
1015029120
KUBOTA
1G41651011
1g41651011
Zexel num
Bosch num
Firm num
Name
9 400 614 557
1G41651011 KUBOTA
INJECTION-PUMP ASSEMBLY
F5802 K 14BZ INJECTION PUMP ASSY PE
F5802 K 14BZ INJECTION PUMP ASSY PE
Calibration Data:
Adjustment conditions
Test oil
1404 Test oil ISO4113 or {SAEJ967d}
1404 Test oil ISO4113 or {SAEJ967d}
Test oil temperature
degC
40
40
45
Nozzle and nozzle holder
105780-8140
Bosch type code
EF8511/9A
Nozzle
105780-0000
Bosch type code
DN12SD12T
Nozzle holder
105780-2080
Bosch type code
EF8511/9
Opening pressure
MPa
17.2
Opening pressure
kgf/cm2
175
Injection pipe
Outer diameter - inner diameter - length (mm) mm 6-2-600
Outer diameter - inner diameter - length (mm) mm 6-2-600
Overflow valve
134424-4120
Overflow valve opening pressure
kPa
255
221
289
Overflow valve opening pressure
kgf/cm2
2.6
2.25
2.95
Tester oil delivery pressure
kPa
255
255
255
Tester oil delivery pressure
kgf/cm2
2.6
2.6
2.6
Direction of rotation (viewed from drive side)
Left L
Left L
Injection timing adjustment
Direction of rotation (viewed from drive side)
Left L
Left L
Injection order
1-3-5-4-
2
Pre-stroke
mm
4
3.95
4.05
Rack position
Point A R=A
Point A R=A
Beginning of injection position
Drive side NO.1
Drive side NO.1
Difference between angles 1
Cal 1-3 deg. 72 71.5 72.5
Cal 1-3 deg. 72 71.5 72.5
Difference between angles 2
Cal 1-5 deg. 144 143.5 144.5
Cal 1-5 deg. 144 143.5 144.5
Difference between angles 3
Cal 1-4 deg. 216 215.5 216.5
Cal 1-4 deg. 216 215.5 216.5
Difference between angles 4
Cyl.1-2 deg. 288 287.5 288.5
Cyl.1-2 deg. 288 287.5 288.5
Injection quantity adjustment
Adjusting point
A
Rack position
11.6
Pump speed
r/min
1200
1200
1200
Average injection quantity
mm3/st.
105
104
106
Max. variation between cylinders
%
0
-2.5
2.5
Basic
*
Fixing the lever
*
Injection quantity adjustment_02
Adjusting point
B
Rack position
10.95
Pump speed
r/min
650
650
650
Average injection quantity
mm3/st.
111
101
121
Fixing the lever
*
Injection quantity adjustment_03
Adjusting point
C
Rack position
6.1+-0.5
Pump speed
r/min
350
350
350
Average injection quantity
mm3/st.
12
10
14
Max. variation between cylinders
%
0
-15
15
Fixing the rack
*
Timer adjustment
Pump speed
r/min
(800)
Advance angle
deg.
0.5
Timer adjustment_02
Pump speed
r/min
(1100)
Advance angle
deg.
2
1.7
2.3
Remarks
Finish
Finish
Test data Ex:
Governor adjustment
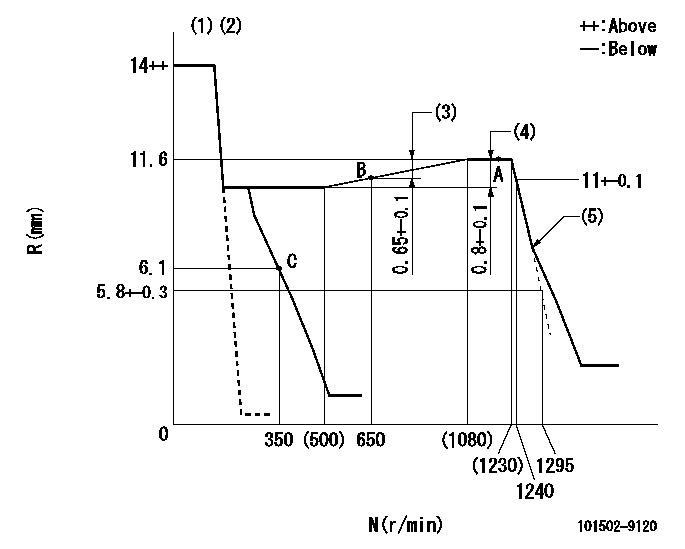
N:Pump speed
R:Rack position (mm)
(1)Target notch: K
(2)Tolerance for racks not indicated: +-0.05mm.
(3)Rack difference between N = N1 and N = N2
(4)Rack difference between N = N3 and N = N4
(5)Idle sub spring setting: L1.
----------
K=10 N1=1200r/min N2=650r/min N3=1200r/min N4=350r/min L1=6.7-0.5mm
----------
----------
K=10 N1=1200r/min N2=650r/min N3=1200r/min N4=350r/min L1=6.7-0.5mm
----------
Speed control lever angle

F:Full speed
I:Idle
(1)Stopper bolt setting
----------
----------
a=37deg+-5deg b=17deg+-5deg
----------
----------
a=37deg+-5deg b=17deg+-5deg
Stop lever angle
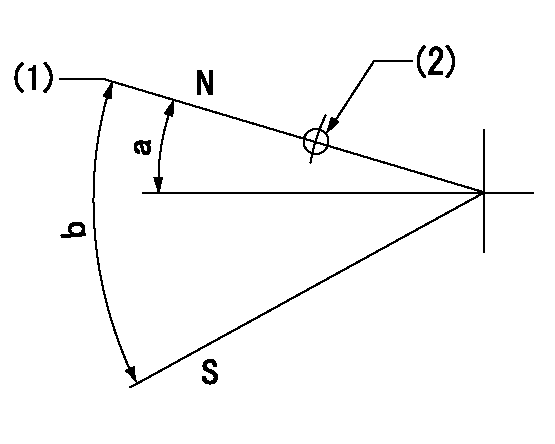
N:Pump normal
S:Stop the pump.
(1)Normal
(2)Use the hole at R = aa
----------
aa=60mm
----------
a=19deg+-5deg b=53deg+-5deg
----------
aa=60mm
----------
a=19deg+-5deg b=53deg+-5deg
Timing setting
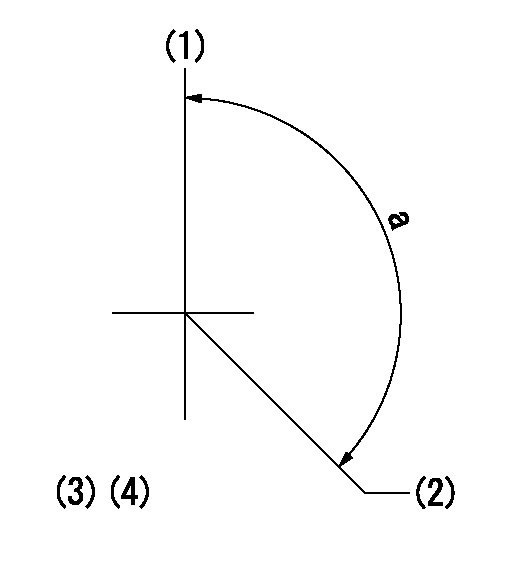
(1)Pump vertical direction
(2)Position of camshaft's key groove at No 1 cylinder's beginning of injection
(3)At rack position = aa
(4)-
----------
aa=(11.6mm)
----------
a=(130deg)
----------
aa=(11.6mm)
----------
a=(130deg)
Information:
start by: a) remove pistons1. Check to be sure all coolant has been removed from the cylinder block.2. Put protection over the crankshaft bearing journals before removing cylinder liners.3. Put location marks on the cylinder liners with respect to their location in block. 4. Use tool setup (A) to remove the cylinder liners from block.5. Remove the seals from cylinder liners.6. Use a straight blade scraper to loosen the spacer plate (1) from cylinder block.
Use care when loosening the plate from cylinder block or damage to plate may result.
7. Remove the spacer plate (1).Install Cylinder Liners
1. Thoroughly clean both sides of spacer plate and top surface of block. Install spacer plate gasket and spacer plate on the cylinder block.
Make sure both sides of plate and top of block are clean and dry before installing gasket and plate. Do not put gasket adhesives or any other substance on these surfaces.
2. Put the cylinder liners in their respective positions in cylinder block. Install tool setup (B) and two cylinder head bolts and washers. Tighten the bolts to 70 5 lb.ft. (9.7 0.7 mkg).3. Check the cylinder liner projection using tool setup (C) as follows: a) Install the four spacers from tool group and four cylinder head bolts and washers. Tighten bolts to 70 5 lb.ft. (9.7 0.7 mkg).b) Use dial indicator, block, and gauge from the tool group to check liner projection at four locations around the liner.c) Cylinder liner projection must be .0030 to .0076 in. (0.076 to 0.193 mm). Projection between liners next to each other must not be different by more than .001 in. (0.025 mm). 4. Remove tool setup (B) and (C). Remove the liners from cylinder block.5. Install the O-ring seals on bottom of liners. Put liquid soap on the seals.
TYPICAL EXAMPLE6. Put oil on the filler band seal, and install the seal on top end of liner. Install the cylinder liners immediately into their respective locations in cylinder block using tool (A).
Do not let the filler band seal stay in oil except for a very short time because the oil will make the seal much bigger very fast. After putting oil on the filler band seal, install the liner immediately into block.
end by: a) install pistons.
Use care when loosening the plate from cylinder block or damage to plate may result.
7. Remove the spacer plate (1).Install Cylinder Liners
1. Thoroughly clean both sides of spacer plate and top surface of block. Install spacer plate gasket and spacer plate on the cylinder block.
Make sure both sides of plate and top of block are clean and dry before installing gasket and plate. Do not put gasket adhesives or any other substance on these surfaces.
2. Put the cylinder liners in their respective positions in cylinder block. Install tool setup (B) and two cylinder head bolts and washers. Tighten the bolts to 70 5 lb.ft. (9.7 0.7 mkg).3. Check the cylinder liner projection using tool setup (C) as follows: a) Install the four spacers from tool group and four cylinder head bolts and washers. Tighten bolts to 70 5 lb.ft. (9.7 0.7 mkg).b) Use dial indicator, block, and gauge from the tool group to check liner projection at four locations around the liner.c) Cylinder liner projection must be .0030 to .0076 in. (0.076 to 0.193 mm). Projection between liners next to each other must not be different by more than .001 in. (0.025 mm). 4. Remove tool setup (B) and (C). Remove the liners from cylinder block.5. Install the O-ring seals on bottom of liners. Put liquid soap on the seals.
TYPICAL EXAMPLE6. Put oil on the filler band seal, and install the seal on top end of liner. Install the cylinder liners immediately into their respective locations in cylinder block using tool (A).
Do not let the filler band seal stay in oil except for a very short time because the oil will make the seal much bigger very fast. After putting oil on the filler band seal, install the liner immediately into block.
end by: a) install pistons.