Information injection-pump assembly
BOSCH
F 019 Z10 337
f019z10337
ZEXEL
101493-9240
1014939240
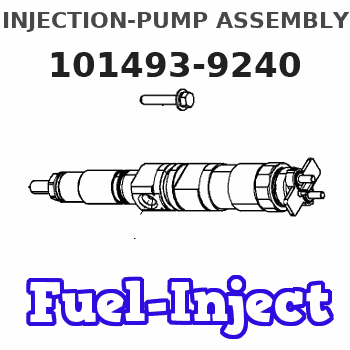
Rating:
Service parts 101493-9240 INJECTION-PUMP ASSEMBLY:
1.
_
6.
COUPLING PLATE
7.
COUPLING PLATE
8.
_
9.
_
11.
Nozzle and Holder
16600-0T003
12.
Open Pre:MPa(Kqf/cm2)
18.6{190}
15.
NOZZLE SET
Cross reference number
BOSCH
F 019 Z10 337
f019z10337
ZEXEL
101493-9240
1014939240
Zexel num
Bosch num
Firm num
Name
Calibration Data:
Adjustment conditions
Test oil
1404 Test oil ISO4113 or {SAEJ967d}
1404 Test oil ISO4113 or {SAEJ967d}
Test oil temperature
degC
40
40
45
Nozzle and nozzle holder
105780-8140
Bosch type code
EF8511/9A
Nozzle
105780-0000
Bosch type code
DN12SD12T
Nozzle holder
105780-2080
Bosch type code
EF8511/9
Opening pressure
MPa
17.2
Opening pressure
kgf/cm2
175
Injection pipe
Outer diameter - inner diameter - length (mm) mm 6-2-600
Outer diameter - inner diameter - length (mm) mm 6-2-600
Overflow valve
131424-1520
Overflow valve opening pressure
kPa
157
123
191
Overflow valve opening pressure
kgf/cm2
1.6
1.25
1.95
Tester oil delivery pressure
kPa
157
157
157
Tester oil delivery pressure
kgf/cm2
1.6
1.6
1.6
Direction of rotation (viewed from drive side)
Right R
Right R
Injection timing adjustment
Direction of rotation (viewed from drive side)
Right R
Right R
Injection order
1-3-4-2
Pre-stroke
mm
3.2
3.15
3.25
Rack position
Point A R=A
Point A R=A
Beginning of injection position
Drive side NO.1
Drive side NO.1
Difference between angles 1
Cal 1-3 deg. 90 89.5 90.5
Cal 1-3 deg. 90 89.5 90.5
Difference between angles 2
Cal 1-4 deg. 180 179.5 180.5
Cal 1-4 deg. 180 179.5 180.5
Difference between angles 3
Cyl.1-2 deg. 270 269.5 270.5
Cyl.1-2 deg. 270 269.5 270.5
Injection quantity adjustment
Adjusting point
-
Rack position
12.7
Pump speed
r/min
1000
1000
1000
Average injection quantity
mm3/st.
74
72.4
75.6
Max. variation between cylinders
%
0
-3.5
3.5
Basic
*
Fixing the rack
*
Standard for adjustment of the maximum variation between cylinders
*
Injection quantity adjustment_02
Adjusting point
H
Rack position
9.5+-0.5
Pump speed
r/min
325
325
325
Average injection quantity
mm3/st.
10
8.2
11.8
Max. variation between cylinders
%
0
-10
10
Fixing the rack
*
Standard for adjustment of the maximum variation between cylinders
*
Injection quantity adjustment_03
Adjusting point
A
Rack position
R1(12.7)
Pump speed
r/min
1000
1000
1000
Average injection quantity
mm3/st.
74
73
75
Basic
*
Fixing the lever
*
Injection quantity adjustment_04
Adjusting point
B
Rack position
R1-0.2
Pump speed
r/min
1600
1600
1600
Average injection quantity
mm3/st.
80.9
76.9
84.9
Fixing the lever
*
Injection quantity adjustment_05
Adjusting point
I
Rack position
-
Pump speed
r/min
100
100
100
Average injection quantity
mm3/st.
100
84
116
Fixing the lever
*
Timer adjustment
Pump speed
r/min
1010--
Advance angle
deg.
0
0
0
Remarks
Start
Start
Timer adjustment_02
Pump speed
r/min
960
Advance angle
deg.
0.3
Timer adjustment_03
Pump speed
r/min
(1000)
Advance angle
deg.
0.8
0.5
1.1
Remarks
Measure the actual speed.
Measure the actual speed.
Timer adjustment_04
Pump speed
r/min
1330+30-
20
Advance angle
deg.
0.8
0.5
1.1
Timer adjustment_05
Pump speed
r/min
1500
Advance angle
deg.
3.45
3.45
3.45
Timer adjustment_06
Pump speed
r/min
1600
Advance angle
deg.
5
4.5
5.5
Remarks
Finish
Finish
Test data Ex:
Governor adjustment
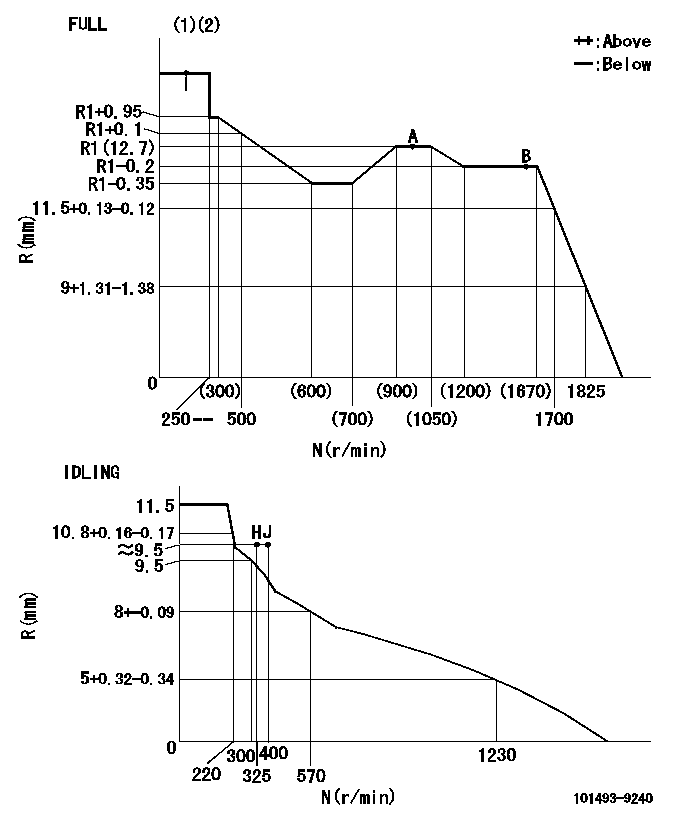
N:Pump speed
R:Rack position (mm)
(1)Torque cam stamping: T1
(2)Tolerance for racks not indicated: +-0.05mm.
----------
T1=H91
----------
----------
T1=H91
----------
Speed control lever angle
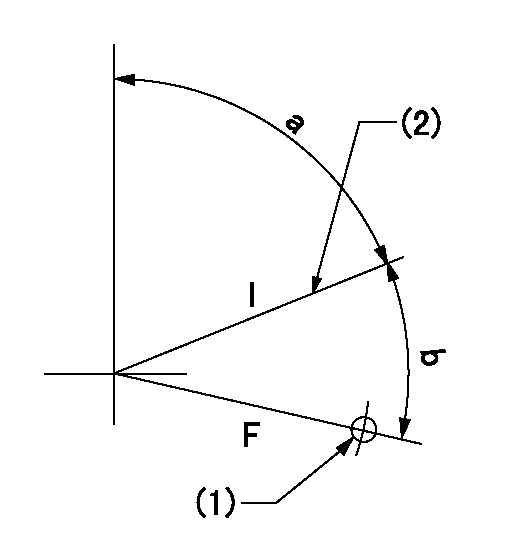
F:Full speed
I:Idle
(1)Use the hole at R = aa
(2)Stopper bolt set position 'H'
----------
aa=32mm
----------
a=71deg+-5deg b=(36deg)+-3deg
----------
aa=32mm
----------
a=71deg+-5deg b=(36deg)+-3deg
Stop lever angle

N:Pump normal
S:Stop the pump.
(1)Use the pin at R = aa
----------
aa=12mm
----------
a=29deg+-5deg b=10deg+-5deg
----------
aa=12mm
----------
a=29deg+-5deg b=10deg+-5deg
0000001501 POTENTIO METER
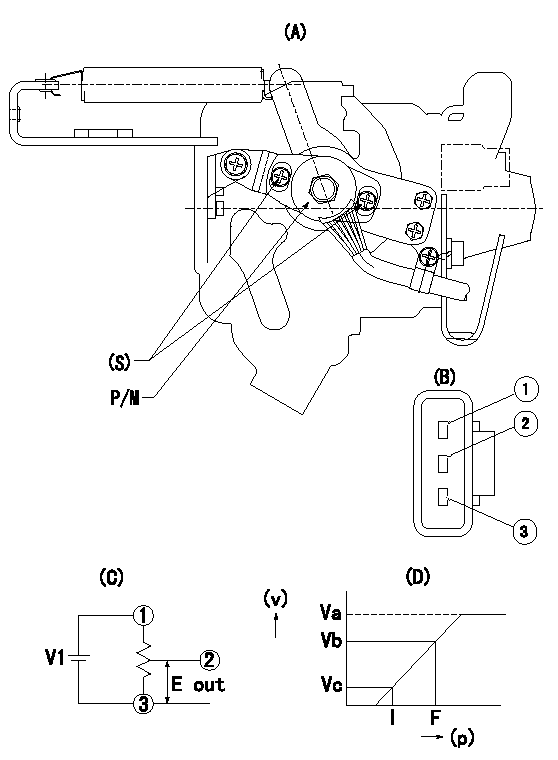
(A) : Governor plan view
(B): Potentiometer harness terminal
(C): Potentiometer connection diagram
(D) : Output voltage standard value
(S): Voltage
P/M: potentiometer
(v): output voltage (V)
(p): direction of potentiometer rotation
1. Adjustment procedures
(1)Apply DCV1 to potentiometer harness terminal (B) to obtain the specified output voltage.
(2)Fix the speed lever at the full side.
(3)Loosen the bolt (S), and move the potentiometer from left and right.
(4)Adjust so that the output voltage at full is within the standard values.
(5)Fix bolt (S).
(6)Repeatedly move the speed lever from the full side to the idle side.
(7)Check that it is within the standard values at full and idle.
----------
V1=5+-0.02V
----------
V1=5+-0.02V Va=(5)V Vb=3.65+-0.2V Vc=0.48+-0.3V
----------
V1=5+-0.02V
----------
V1=5+-0.02V Va=(5)V Vb=3.65+-0.2V Vc=0.48+-0.3V
Timing setting
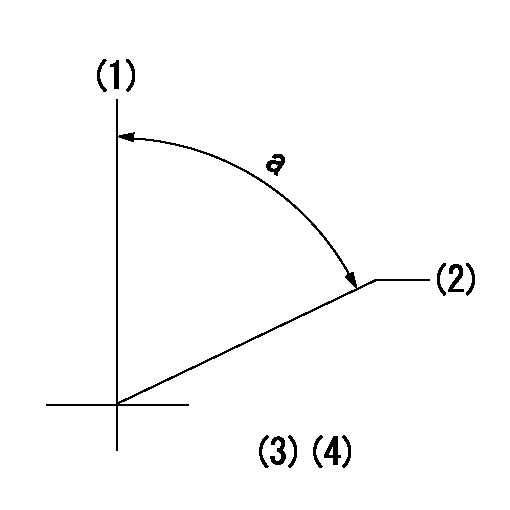
(1)Pump vertical direction
(2)Position of gear's standard threaded hole (position of gear mark 'S') at No 1 cylinder's beginning of injection
(3)B.T.D.C.: aa
(4)-
----------
aa=12deg
----------
a=(60deg)
----------
aa=12deg
----------
a=(60deg)
Information:
Introduction
The problem that is identified below does not have a known permanent solution. Until a permanent solution is known, use the solution that is identified below.Problem
Some of the 3408E engines and 3412E engines in the above listed machines may experience hard starting or low power due to oil that is leaking past the poppet valve in the injector. The oil leakage is caused by the operating conditions at either low idle or high idle. Excessive oil leakage can reduce actuation pressure to the fuel injector. This may prevent fuel injection.Solution
Electrical shock hazard. The electronic unit injector system uses 90-120 volts.
Follow the proper troubleshooting procedure for the correct engine. If the problem is not located and the symptoms that are listed above continue, remove the engine valve covers. Electrically disable the injectors. Crank the engine. Watch the spill ports of the injector for oil leakage. A small amount of oil leakage is acceptable. A continuous stream of oil may mean leakage from the poppet valve. Excessive leakage from the poppet valve may prevent fuel injection.Note: Normal oil pressure during cranking should be 5 MPa (725 psi). Oil pressure below 5 MPa (725 psi) may indicate excessive oil leakage in injectors. Do not replace the oil pump. Service personnel should replace the injectors that have a continuous flow of oil from the oil ports. Injectors that have a continuous flow of oil and injectors that are within the guidelines of warranty can be returned. Injectors that do not have a continuous flow of oil should not be replaced. Injectors that do not have a continuous flow of oil should not be returned.Note: For additional information on the operation of Hydraulic Electronic Unit Injectors HEUI, refer to CD, RENR1390.
Illustration 1 g01308874
(1) Oil drain portThe oil drain ports are located underneath the solenoid. This will direct the oil flow downward. Some oil may also leak from the rectangular slots at the side of the solenoid. Excess oil leakage will still be visible on the cylinder head.
The problem that is identified below does not have a known permanent solution. Until a permanent solution is known, use the solution that is identified below.Problem
Some of the 3408E engines and 3412E engines in the above listed machines may experience hard starting or low power due to oil that is leaking past the poppet valve in the injector. The oil leakage is caused by the operating conditions at either low idle or high idle. Excessive oil leakage can reduce actuation pressure to the fuel injector. This may prevent fuel injection.Solution
Electrical shock hazard. The electronic unit injector system uses 90-120 volts.
Follow the proper troubleshooting procedure for the correct engine. If the problem is not located and the symptoms that are listed above continue, remove the engine valve covers. Electrically disable the injectors. Crank the engine. Watch the spill ports of the injector for oil leakage. A small amount of oil leakage is acceptable. A continuous stream of oil may mean leakage from the poppet valve. Excessive leakage from the poppet valve may prevent fuel injection.Note: Normal oil pressure during cranking should be 5 MPa (725 psi). Oil pressure below 5 MPa (725 psi) may indicate excessive oil leakage in injectors. Do not replace the oil pump. Service personnel should replace the injectors that have a continuous flow of oil from the oil ports. Injectors that have a continuous flow of oil and injectors that are within the guidelines of warranty can be returned. Injectors that do not have a continuous flow of oil should not be replaced. Injectors that do not have a continuous flow of oil should not be returned.Note: For additional information on the operation of Hydraulic Electronic Unit Injectors HEUI, refer to CD, RENR1390.
Illustration 1 g01308874
(1) Oil drain portThe oil drain ports are located underneath the solenoid. This will direct the oil flow downward. Some oil may also leak from the rectangular slots at the side of the solenoid. Excess oil leakage will still be visible on the cylinder head.