Information injection-pump assembly
BOSCH
F 019 Z10 487
f019z10487
ZEXEL
101493-9190
1014939190
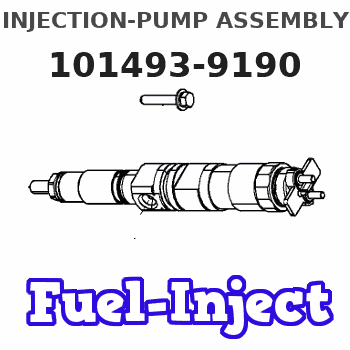
Rating:
Service parts 101493-9190 INJECTION-PUMP ASSEMBLY:
1.
_
6.
COUPLING PLATE
7.
COUPLING PLATE
8.
_
9.
_
11.
Nozzle and Holder
12.
Open Pre:MPa(Kqf/cm2)
18.6(190)
15.
NOZZLE SET
Cross reference number
BOSCH
F 019 Z10 487
f019z10487
ZEXEL
101493-9190
1014939190
Zexel num
Bosch num
Firm num
Name
Calibration Data:
Adjustment conditions
Test oil
1404 Test oil ISO4113 or {SAEJ967d}
1404 Test oil ISO4113 or {SAEJ967d}
Test oil temperature
degC
40
40
45
Nozzle and nozzle holder
105780-8140
Bosch type code
EF8511/9A
Nozzle
105780-0000
Bosch type code
DN12SD12T
Nozzle holder
105780-2080
Bosch type code
EF8511/9
Opening pressure
MPa
17.2
Opening pressure
kgf/cm2
175
Injection pipe
Outer diameter - inner diameter - length (mm) mm 6-2-600
Outer diameter - inner diameter - length (mm) mm 6-2-600
Overflow valve
131424-1520
Overflow valve opening pressure
kPa
157
123
191
Overflow valve opening pressure
kgf/cm2
1.6
1.25
1.95
Tester oil delivery pressure
kPa
157
157
157
Tester oil delivery pressure
kgf/cm2
1.6
1.6
1.6
Direction of rotation (viewed from drive side)
Right R
Right R
Injection timing adjustment
Direction of rotation (viewed from drive side)
Right R
Right R
Injection order
1-3-4-2
Pre-stroke
mm
3.2
3.15
3.25
Rack position
Point A R=A
Point A R=A
Beginning of injection position
Drive side NO.1
Drive side NO.1
Difference between angles 1
Cal 1-3 deg. 90 89.5 90.5
Cal 1-3 deg. 90 89.5 90.5
Difference between angles 2
Cal 1-4 deg. 180 179.5 180.5
Cal 1-4 deg. 180 179.5 180.5
Difference between angles 3
Cyl.1-2 deg. 270 269.5 270.5
Cyl.1-2 deg. 270 269.5 270.5
Injection quantity adjustment
Adjusting point
-
Rack position
12.1
Pump speed
r/min
900
900
900
Average injection quantity
mm3/st.
62.5
60.9
64.1
Max. variation between cylinders
%
0
-2.5
2.5
Basic
*
Fixing the rack
*
Standard for adjustment of the maximum variation between cylinders
*
Injection quantity adjustment_02
Adjusting point
H
Rack position
9.5+-0.5
Pump speed
r/min
300
300
300
Average injection quantity
mm3/st.
9.3
7.5
11.1
Max. variation between cylinders
%
0
-15
15
Fixing the rack
*
Standard for adjustment of the maximum variation between cylinders
*
Injection quantity adjustment_03
Adjusting point
A
Rack position
R1(12.1)
Pump speed
r/min
900
900
900
Average injection quantity
mm3/st.
62.5
61.5
63.5
Basic
*
Fixing the lever
*
Injection quantity adjustment_04
Adjusting point
B
Rack position
R1-0.05
Pump speed
r/min
1500
1500
1500
Average injection quantity
mm3/st.
71
67
75
Fixing the lever
*
Injection quantity adjustment_05
Adjusting point
C
Rack position
R1+0.25
Pump speed
r/min
500
500
500
Average injection quantity
mm3/st.
51
47
55
Fixing the lever
*
Injection quantity adjustment_06
Adjusting point
I
Rack position
-
Pump speed
r/min
100
100
100
Average injection quantity
mm3/st.
101
85
117
Fixing the lever
*
Timer adjustment
Pump speed
r/min
(740)
Advance angle
deg.
0
0
0
Remarks
Measure speed (beginning of operation).
Measure speed (beginning of operation).
Timer adjustment_02
Pump speed
r/min
1040
Advance angle
deg.
1
0.5
1.5
Timer adjustment_03
Pump speed
r/min
1500
Advance angle
deg.
5
4.5
5.5
Remarks
Finish
Finish
Test data Ex:
Governor adjustment
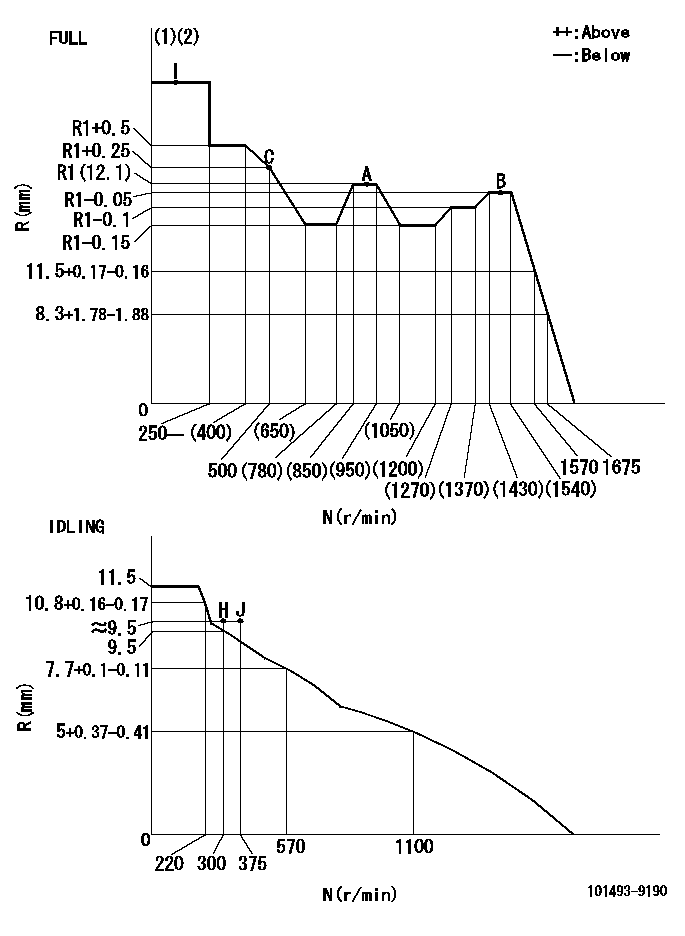
N:Pump speed
R:Rack position (mm)
(1)Torque cam stamping: T1
(2)Tolerance for racks not indicated: +-0.05mm.
----------
T1=H39
----------
----------
T1=H39
----------
Speed control lever angle
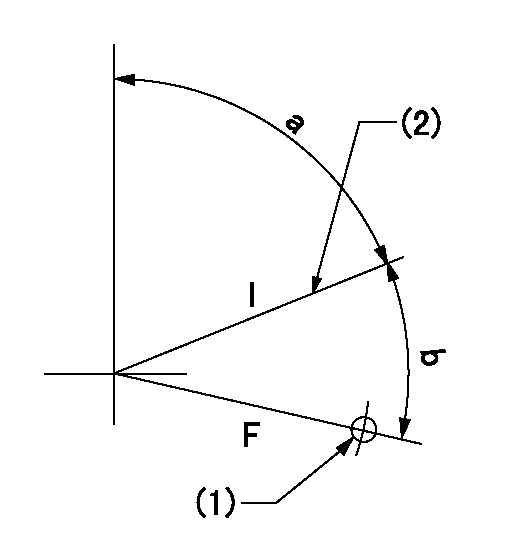
F:Full speed
I:Idle
(1)Use the hole at R = aa
(2)Stopper bolt set position 'H'
----------
aa=32mm
----------
a=70deg+-5deg b=39deg+-3deg
----------
aa=32mm
----------
a=70deg+-5deg b=39deg+-3deg
Stop lever angle

N:Pump normal
S:Stop the pump.
(1)Use the pin at R = aa
----------
aa=12mm
----------
a=29deg+-5deg b=10deg+-5deg
----------
aa=12mm
----------
a=29deg+-5deg b=10deg+-5deg
Timing setting
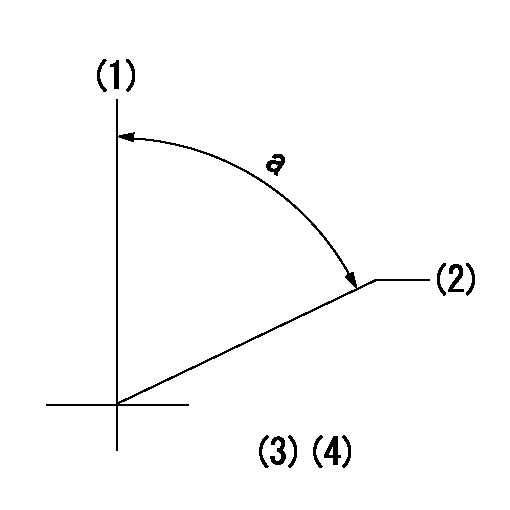
(1)Pump vertical direction
(2)Position of gear's standard threaded hole (position of gear mark 'S') at No 1 cylinder's beginning of injection
(3)B.T.D.C.: aa
(4)-
----------
aa=11deg
----------
a=(60deg)
----------
aa=11deg
----------
a=(60deg)
Information:
Problem 5
The engine shutdown occurs after the engine runs for more than 3 minutes.
Check the overspeed setting on the electronic speed switch (ESS).
Observe the indicator lamp on the ESS.
Reset the air shutoff lever, if equipped.
Crank the engine. Stop the engine with the emergency stop switch, if trouble occurs.Result
The indicator lamp on the ESS is turned on.Overspeed is indicated as the cause of the engine shutdown. Press the "RESET" button of the ESS. Find the cause of the overspeed. Refer to Testing and Adjusting, "Overspeed Verification Test" and Testing and Adjusting, "Overspeed Calibration". If the overspeed is adjusted properly and the problem persists, check the shielded cable. Only the shield should be connected to terminal 2 on the ESS. STOP.
The indicator lamp is turned off.Go to Step 2.
Check the protection switches.
Remove the jumper that is between terminals (TS-9) and (TS-10) of the junction box.
Crank the engine. Stop the engine with the emergency stop switch, if trouble occurs.Result
The engine starts and the engine runs.The problem is in the oil pressure switches or the water temperature contactor switch. Go to Step 8 of "Problem 1".
The engine starts but engine shutdown occurs immediately.Go to Step 1 of "Problem 3".
The engine starts and the engine runs but engine shutdown occurs after the engine runs for more than 3 minutes.Go to Step 3.
The engine cranks but the engine does not start.Go to Step 1 of "Problem 1".
Check the start/stop switch.
Disconnect the wire in the junction box that connects terminal (SR1-85) of the slave relay (SR1) to terminal (TD-7) of the time delay relay (TD).
Disconnect the wire from terminal (TD-7) and insulate the exposed wire.
Crank the engine. Stop the engine with the emergency stop switch, if trouble occurs.Result
The engine starts and the engine runs.The start/stop switch has a short circuit or a wiring problem is causing a voltage at terminal (TD-7). Reconnect the wire to the terminal.
Check the start/stop switch.
Disconnect the wire that runs from the STOP position of terminal (SSS-6) to terminal (TD-6). Terminal (SSS-6) is on the start/stop switch.
Disconnect the wire at terminal (TD-7).
Crank the engine. Stop the engine with the emergency stop switch, if trouble occurs.Result
The engine starts and the engine runs.The start/stop switch is faulty. Replace the switch. STOP.
Engine shutdown still occurs.Reconnect the wire to terminal (TD-7). Go to Step 5
Check the slave relay (SR1).
Disconnect the wire that connects terminal (TS-10) of the junction box to terminal (TD-6) of the time delay relay.
Disconnect the wire at terminal (TD-6).
Crank the engine. Stop the engine with the emergency stop switch, if trouble occurs.Result
The engine starts and the engine runs.The start/stop switch is faulty. Replace the start/stop switch. STOP.
Engine shutdown still occurs.The contacts of SR1 periodically close. The problem may also be with the governor or the fuel supply to the engine. Refer to the Engine Service Manual. If a 2301A Electric Governor is used, the SR1 contacts may be opening. Refer to 2301A Electric Governor Service Manual, SENR3585. Test SR1. Refer to Testing and Adjusting, "Slave Relay Test".Problem 6
Engine shutdown does not occur
The engine shutdown occurs after the engine runs for more than 3 minutes.
Check the overspeed setting on the electronic speed switch (ESS).
Observe the indicator lamp on the ESS.
Reset the air shutoff lever, if equipped.
Crank the engine. Stop the engine with the emergency stop switch, if trouble occurs.Result
The indicator lamp on the ESS is turned on.Overspeed is indicated as the cause of the engine shutdown. Press the "RESET" button of the ESS. Find the cause of the overspeed. Refer to Testing and Adjusting, "Overspeed Verification Test" and Testing and Adjusting, "Overspeed Calibration". If the overspeed is adjusted properly and the problem persists, check the shielded cable. Only the shield should be connected to terminal 2 on the ESS. STOP.
The indicator lamp is turned off.Go to Step 2.
Check the protection switches.
Remove the jumper that is between terminals (TS-9) and (TS-10) of the junction box.
Crank the engine. Stop the engine with the emergency stop switch, if trouble occurs.Result
The engine starts and the engine runs.The problem is in the oil pressure switches or the water temperature contactor switch. Go to Step 8 of "Problem 1".
The engine starts but engine shutdown occurs immediately.Go to Step 1 of "Problem 3".
The engine starts and the engine runs but engine shutdown occurs after the engine runs for more than 3 minutes.Go to Step 3.
The engine cranks but the engine does not start.Go to Step 1 of "Problem 1".
Check the start/stop switch.
Disconnect the wire in the junction box that connects terminal (SR1-85) of the slave relay (SR1) to terminal (TD-7) of the time delay relay (TD).
Disconnect the wire from terminal (TD-7) and insulate the exposed wire.
Crank the engine. Stop the engine with the emergency stop switch, if trouble occurs.Result
The engine starts and the engine runs.The start/stop switch has a short circuit or a wiring problem is causing a voltage at terminal (TD-7). Reconnect the wire to the terminal.
Check the start/stop switch.
Disconnect the wire that runs from the STOP position of terminal (SSS-6) to terminal (TD-6). Terminal (SSS-6) is on the start/stop switch.
Disconnect the wire at terminal (TD-7).
Crank the engine. Stop the engine with the emergency stop switch, if trouble occurs.Result
The engine starts and the engine runs.The start/stop switch is faulty. Replace the switch. STOP.
Engine shutdown still occurs.Reconnect the wire to terminal (TD-7). Go to Step 5
Check the slave relay (SR1).
Disconnect the wire that connects terminal (TS-10) of the junction box to terminal (TD-6) of the time delay relay.
Disconnect the wire at terminal (TD-6).
Crank the engine. Stop the engine with the emergency stop switch, if trouble occurs.Result
The engine starts and the engine runs.The start/stop switch is faulty. Replace the start/stop switch. STOP.
Engine shutdown still occurs.The contacts of SR1 periodically close. The problem may also be with the governor or the fuel supply to the engine. Refer to the Engine Service Manual. If a 2301A Electric Governor is used, the SR1 contacts may be opening. Refer to 2301A Electric Governor Service Manual, SENR3585. Test SR1. Refer to Testing and Adjusting, "Slave Relay Test".Problem 6
Engine shutdown does not occur