Information injection-pump assembly
BOSCH
9 400 614 419
9400614419
ZEXEL
101492-0960
1014920960
ISUZU
8972110560
8972110560
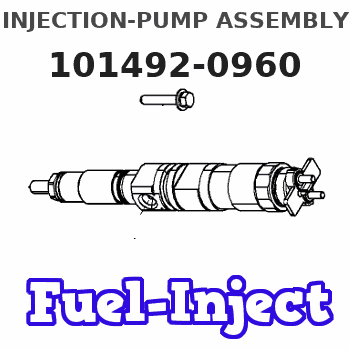
Rating:
Service parts 101492-0960 INJECTION-PUMP ASSEMBLY:
1.
_
5.
AUTOM. ADVANCE MECHANIS
6.
COUPLING PLATE
8.
_
9.
_
11.
Nozzle and Holder
8-94451-183-3
12.
Open Pre:MPa(Kqf/cm2)
19.6{200}
15.
NOZZLE SET
Cross reference number
BOSCH
9 400 614 419
9400614419
ZEXEL
101492-0960
1014920960
ISUZU
8972110560
8972110560
Zexel num
Bosch num
Firm num
Name
101492-0960
9 400 614 419
8972110560 ISUZU
INJECTION-PUMP ASSEMBLY
4JB1 K 14BC INJECTION PUMP ASSY PE4A,5A, PE
4JB1 K 14BC INJECTION PUMP ASSY PE4A,5A, PE
Calibration Data:
Adjustment conditions
Test oil
1404 Test oil ISO4113 or {SAEJ967d}
1404 Test oil ISO4113 or {SAEJ967d}
Test oil temperature
degC
40
40
45
Nozzle and nozzle holder
105780-8140
Bosch type code
EF8511/9A
Nozzle
105780-0000
Bosch type code
DN12SD12T
Nozzle holder
105780-2080
Bosch type code
EF8511/9
Opening pressure
MPa
17.2
Opening pressure
kgf/cm2
175
Injection pipe
Outer diameter - inner diameter - length (mm) mm 6-2-600
Outer diameter - inner diameter - length (mm) mm 6-2-600
Overflow valve
131424-0820
Overflow valve opening pressure
kPa
127
107
147
Overflow valve opening pressure
kgf/cm2
1.3
1.1
1.5
Tester oil delivery pressure
kPa
157
157
157
Tester oil delivery pressure
kgf/cm2
1.6
1.6
1.6
Direction of rotation (viewed from drive side)
Left L
Left L
Injection timing adjustment
Direction of rotation (viewed from drive side)
Left L
Left L
Injection order
1-3-4-2
Pre-stroke
mm
3.3
3.25
3.35
Beginning of injection position
Drive side NO.1
Drive side NO.1
Difference between angles 1
Cal 1-3 deg. 90 89.5 90.5
Cal 1-3 deg. 90 89.5 90.5
Difference between angles 2
Cal 1-4 deg. 180 179.5 180.5
Cal 1-4 deg. 180 179.5 180.5
Difference between angles 3
Cyl.1-2 deg. 270 269.5 270.5
Cyl.1-2 deg. 270 269.5 270.5
Injection quantity adjustment
Adjusting point
A
Rack position
10.8
Pump speed
r/min
1600
1600
1600
Average injection quantity
mm3/st.
83.2
82.2
84.2
Max. variation between cylinders
%
0
-2.5
2.5
Basic
*
Fixing the rack
*
Injection quantity adjustment_02
Adjusting point
B
Rack position
7.6+-0.5
Pump speed
r/min
275
275
275
Average injection quantity
mm3/st.
8
6
10
Max. variation between cylinders
%
0
-15
15
Fixing the rack
*
Test data Ex:
Governor adjustment
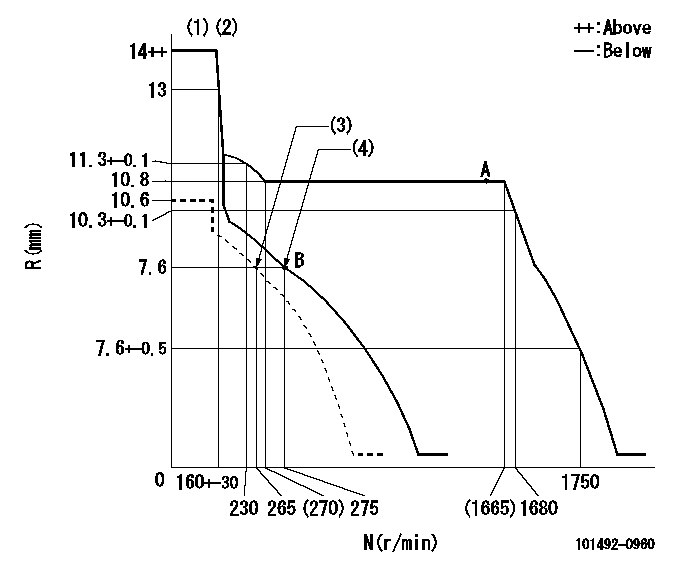
N:Pump speed
R:Rack position (mm)
(1)Target notch: K
(2)Tolerance for racks not indicated: +-0.05mm.
(3)Set idle sub-spring
(4)Main spring setting
----------
K=12
----------
----------
K=12
----------
Speed control lever angle

F:Full speed
I:Idle
(1)Stopper bolt setting
----------
----------
a=19deg+-5deg b=32deg+-5deg
----------
----------
a=19deg+-5deg b=32deg+-5deg
Stop lever angle

N:Pump normal
S:Stop the pump.
----------
----------
a=2.5deg+-5deg b=53deg+-5deg
----------
----------
a=2.5deg+-5deg b=53deg+-5deg
Timing setting

(1)Pump vertical direction
(2)Position of gear mark 'V' at No 1 cylinder's beginning of injection
(3)B.T.D.C.: aa
(4)-
----------
aa=18deg
----------
a=(200deg)
----------
aa=18deg
----------
a=(200deg)
Information:
Start By:a. remove flywheel
The crankshaft rear seal and wear sleeve must both be removed because they must be replaced as a new set. The new seal set must not be separated.
1. Use a sharp punch and a hammer to put four equally spaced holes in seal (1).2. Install the tip of Tool (A) into the seal, and use the slide hammer to pull it out of the flywheel housing. Change the location of Tool (A) in the seal in order to pull the seal out evenly. 3. Install two 5/8 "-18 NF × 4 in. (102 mm) long bolts (2) to hold the crankshaft rear gear in position.4. Install 5P-7314 Distorter Ring (3) [part of Tooling (B)] in the space where the seal was removed.
Be careful not to damage the crankshaft rear gear.
5. Use 5P-7312 Distorter Ring (4) [part of Tooling (B)] to distort the wear sleeve. Put the end of the distorter in the space where the seal was removed.6. Turn the distorter to cause distortion to the wear sleeve. Move the distorter to another position, and turn the distorter again. Do this procedure until the wear sleeve is loose on the crankshaft.7. Remove the distorter, distorter ring and wear sleeve.Install Crankshaft Rear Seal & Wear Sleeve
The front and rear seals and wear sleeves have different spiral grooves in the seal. Because of this type of design, the front seal group for an engine is different from the rear seal group. If a seal group is installed on the wrong end of the engine, oil can actually be taken out of the engine instead of moving the oil back into the engine.
1. Fasten Tooling (A) to the crankshaft rear gear.2. Use 6V-1541 Quick Cure Primer to clean the outside diameter of the crankshaft rear gear and inside diameter of the wear sleeve in seal assembly (1).3. Put 9S-3265 Retaining Compound on the outside diameter of the crankshaft rear gear and the inside diameter of the wear sleeve in seal assembly (1).
Do not separate the lip-type seal from the wear sleeve. The material in the large lip of the seal can be damaged easily. A scratch or rub (not visible) from a finger can damage the seal enough that it cannot be used. Install the sleeve in the seal. Once there is separation of the sleeve and lip-type seal they cannot be used again and must be replaced with a new seal group. Do not use any type of lubrication during installation of the seal group. If any type of lubrication is used in the installation of the seal group, early seal failure can result.
4. Put seal group (1) in position on Tooling (A). Be sure direction arrows on the seal are the same as crankshaft rotation. 5. Put clean engine oil on the face of washer on nut (2) [part of Tooling (B)] that contacts the installer.6. Install Tooling (B) onto Tooling (A), and install nut (2) [part of Tooling (B)] on the threaded shaft of Tooling
The crankshaft rear seal and wear sleeve must both be removed because they must be replaced as a new set. The new seal set must not be separated.
1. Use a sharp punch and a hammer to put four equally spaced holes in seal (1).2. Install the tip of Tool (A) into the seal, and use the slide hammer to pull it out of the flywheel housing. Change the location of Tool (A) in the seal in order to pull the seal out evenly. 3. Install two 5/8 "-18 NF × 4 in. (102 mm) long bolts (2) to hold the crankshaft rear gear in position.4. Install 5P-7314 Distorter Ring (3) [part of Tooling (B)] in the space where the seal was removed.
Be careful not to damage the crankshaft rear gear.
5. Use 5P-7312 Distorter Ring (4) [part of Tooling (B)] to distort the wear sleeve. Put the end of the distorter in the space where the seal was removed.6. Turn the distorter to cause distortion to the wear sleeve. Move the distorter to another position, and turn the distorter again. Do this procedure until the wear sleeve is loose on the crankshaft.7. Remove the distorter, distorter ring and wear sleeve.Install Crankshaft Rear Seal & Wear Sleeve
The front and rear seals and wear sleeves have different spiral grooves in the seal. Because of this type of design, the front seal group for an engine is different from the rear seal group. If a seal group is installed on the wrong end of the engine, oil can actually be taken out of the engine instead of moving the oil back into the engine.
1. Fasten Tooling (A) to the crankshaft rear gear.2. Use 6V-1541 Quick Cure Primer to clean the outside diameter of the crankshaft rear gear and inside diameter of the wear sleeve in seal assembly (1).3. Put 9S-3265 Retaining Compound on the outside diameter of the crankshaft rear gear and the inside diameter of the wear sleeve in seal assembly (1).
Do not separate the lip-type seal from the wear sleeve. The material in the large lip of the seal can be damaged easily. A scratch or rub (not visible) from a finger can damage the seal enough that it cannot be used. Install the sleeve in the seal. Once there is separation of the sleeve and lip-type seal they cannot be used again and must be replaced with a new seal group. Do not use any type of lubrication during installation of the seal group. If any type of lubrication is used in the installation of the seal group, early seal failure can result.
4. Put seal group (1) in position on Tooling (A). Be sure direction arrows on the seal are the same as crankshaft rotation. 5. Put clean engine oil on the face of washer on nut (2) [part of Tooling (B)] that contacts the installer.6. Install Tooling (B) onto Tooling (A), and install nut (2) [part of Tooling (B)] on the threaded shaft of Tooling
Have questions with 101492-0960?
Group cross 101492-0960 ZEXEL
Isuzu
101492-0960
9 400 614 419
8972110560
INJECTION-PUMP ASSEMBLY
4JB1
4JB1