Information injection-pump assembly
BOSCH
F 019 Z10 480
f019z10480
ZEXEL
101491-9976
1014919976
NISSAN-DIESEL
167000T072
167000t072
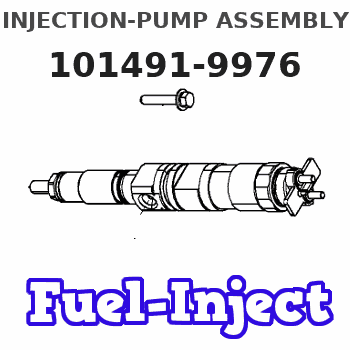
Rating:
Service parts 101491-9976 INJECTION-PUMP ASSEMBLY:
1.
_
6.
COUPLING PLATE
7.
COUPLING PLATE
8.
_
9.
_
11.
Nozzle and Holder
166000T003
12.
Open Pre:MPa(Kqf/cm2)
18.6(190)
15.
NOZZLE SET
Cross reference number
BOSCH
F 019 Z10 480
f019z10480
ZEXEL
101491-9976
1014919976
NISSAN-DIESEL
167000T072
167000t072
Zexel num
Bosch num
Firm num
Name
Calibration Data:
Adjustment conditions
Test oil
1404 Test oil ISO4113 or {SAEJ967d}
1404 Test oil ISO4113 or {SAEJ967d}
Test oil temperature
degC
40
40
45
Nozzle and nozzle holder
105780-8140
Bosch type code
EF8511/9A
Nozzle
105780-0000
Bosch type code
DN12SD12T
Nozzle holder
105780-2080
Bosch type code
EF8511/9
Opening pressure
MPa
17.2
Opening pressure
kgf/cm2
175
Injection pipe
Outer diameter - inner diameter - length (mm) mm 6-2-600
Outer diameter - inner diameter - length (mm) mm 6-2-600
Overflow valve
131424-1520
Overflow valve opening pressure
kPa
157
123
191
Overflow valve opening pressure
kgf/cm2
1.6
1.25
1.95
Tester oil delivery pressure
kPa
157
157
157
Tester oil delivery pressure
kgf/cm2
1.6
1.6
1.6
Direction of rotation (viewed from drive side)
Right R
Right R
Injection timing adjustment
Direction of rotation (viewed from drive side)
Right R
Right R
Injection order
1-3-4-2
Pre-stroke
mm
3.2
3.15
3.25
Rack position
Point A R=A
Point A R=A
Beginning of injection position
Drive side NO.1
Drive side NO.1
Difference between angles 1
Cal 1-3 deg. 90 89.5 90.5
Cal 1-3 deg. 90 89.5 90.5
Difference between angles 2
Cal 1-4 deg. 180 179.5 180.5
Cal 1-4 deg. 180 179.5 180.5
Difference between angles 3
Cyl.1-2 deg. 270 269.5 270.5
Cyl.1-2 deg. 270 269.5 270.5
Injection quantity adjustment
Adjusting point
-
Rack position
12.5
Pump speed
r/min
1000
1000
1000
Average injection quantity
mm3/st.
71
69.4
72.6
Max. variation between cylinders
%
0
-3.5
3.5
Basic
*
Fixing the rack
*
Standard for adjustment of the maximum variation between cylinders
*
Injection quantity adjustment_02
Adjusting point
H
Rack position
9.5+-0.5
Pump speed
r/min
300
300
300
Average injection quantity
mm3/st.
9.6
7.8
11.4
Max. variation between cylinders
%
0
-10
10
Fixing the rack
*
Standard for adjustment of the maximum variation between cylinders
*
Injection quantity adjustment_03
Adjusting point
A
Rack position
R1(12.5)
Pump speed
r/min
1000
1000
1000
Average injection quantity
mm3/st.
71
70
72
Basic
*
Fixing the lever
*
Injection quantity adjustment_04
Adjusting point
B
Rack position
R1-0.2
Pump speed
r/min
1600
1600
1600
Average injection quantity
mm3/st.
79
75
83
Fixing the lever
*
Injection quantity adjustment_05
Adjusting point
I
Rack position
-
Pump speed
r/min
100
100
100
Average injection quantity
mm3/st.
100
84
116
Fixing the lever
*
Timer adjustment
Pump speed
r/min
1010--
Advance angle
deg.
0
0
0
Remarks
Start
Start
Timer adjustment_02
Pump speed
r/min
960
Advance angle
deg.
0.3
Timer adjustment_03
Pump speed
r/min
(1000)
Advance angle
deg.
0.8
0.5
1.1
Remarks
Measure the actual speed.
Measure the actual speed.
Timer adjustment_04
Pump speed
r/min
1330+30-
20
Advance angle
deg.
0.8
0.5
1.1
Timer adjustment_05
Pump speed
r/min
1500
Advance angle
deg.
3.45
3.45
3.45
Timer adjustment_06
Pump speed
r/min
1600
Advance angle
deg.
5
4.5
5.5
Remarks
Finish
Finish
Test data Ex:
Governor adjustment
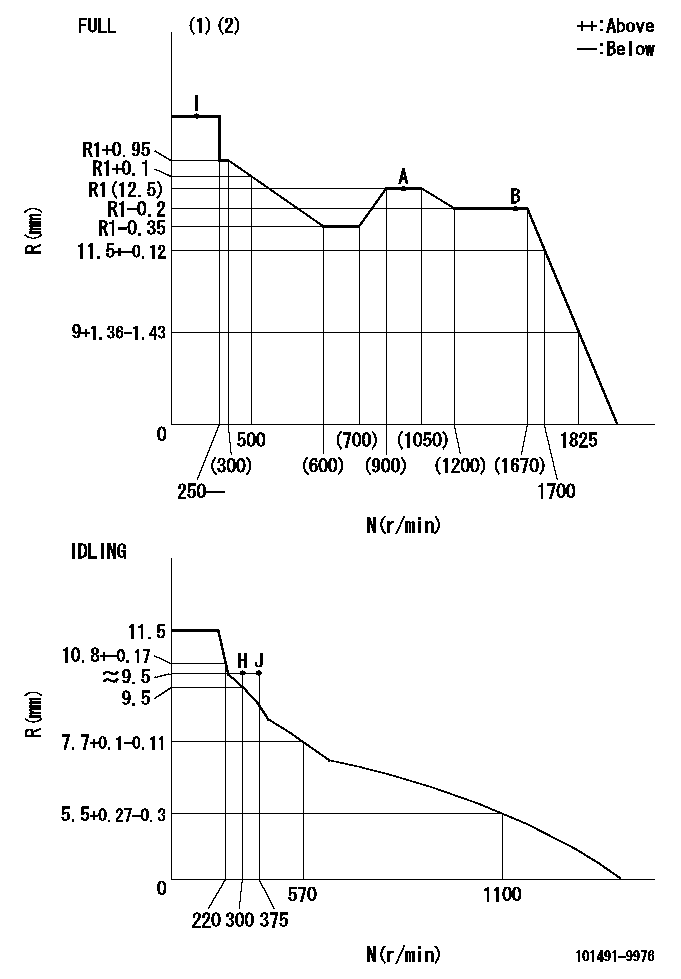
N:Pump speed
R:Rack position (mm)
(1)Torque cam stamping: T1
(2)Tolerance for racks not indicated: +-0.05mm.
----------
T1=G84
----------
----------
T1=G84
----------
Speed control lever angle
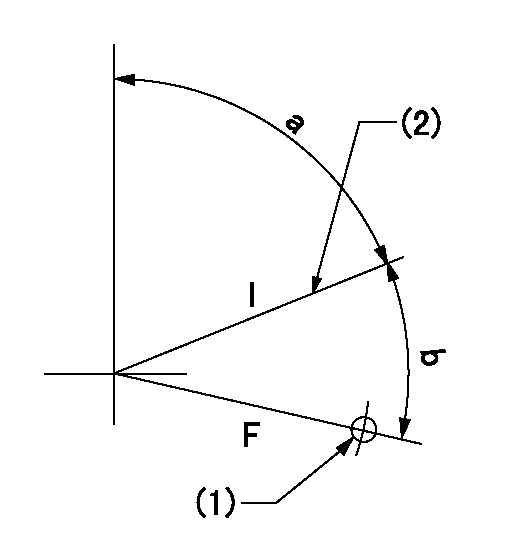
F:Full speed
I:Idle
(1)Use the hole at R = aa
(2)Stopper bolt set position 'H'
----------
aa=32mm
----------
a=70deg+-5deg b=37deg+-3deg
----------
aa=32mm
----------
a=70deg+-5deg b=37deg+-3deg
Stop lever angle

N:Pump normal
S:Stop the pump.
(1)Use the pin at R = aa
----------
aa=12mm
----------
a=29deg+-5deg b=10deg+-5deg
----------
aa=12mm
----------
a=29deg+-5deg b=10deg+-5deg
0000001501 LEVER
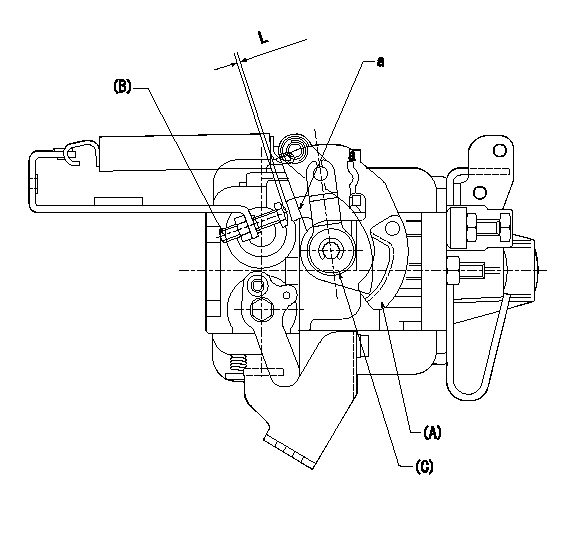
(A) Speed lever (lower)
(B) Stopper bolt
(C) Special lever (upper)
a:Point A (inside lever)
1. Special lever adjustment
(1)With the speed lever at the idle position, set the accelerator lever stopper bolt so that the accelerator lever contacts the speed lever at point a.
(2)Back off the stopper bolt L and set.
----------
L=1+0.5mm
----------
----------
L=1+0.5mm
----------
Timing setting
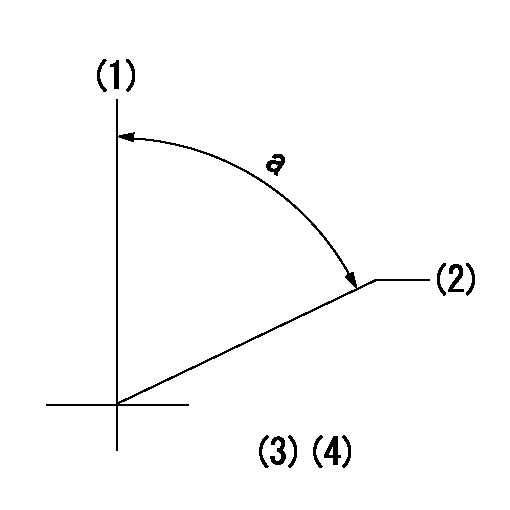
(1)Pump vertical direction
(2)Position of gear's standard threaded hole (position of gear mark 'S') at No 1 cylinder's beginning of injection
(3)B.T.D.C.: aa
(4)-
----------
aa=12deg
----------
a=(60deg)
----------
aa=12deg
----------
a=(60deg)
Information:
2. Locate wire 405-GY on the main cab harness near the connector exiting the cab wall on the right hand side, as shown by arrow.Cut this wire close to the connector. Splice it and the wire just assembled using an 8S4626 Splice. Be sure to splice to the portion of the wire that goes into the cab harness.3. Connect the 7N9738 Housing to the two pin connector on the 8X9862 Harness Assembly (housing containing 405-GY). Clip with a 3T3048 Clip Assembly.Installation of Ether (Chassis) Wiring Harness
The ether chassis harness for MPPS is different than the one called out in the AEIS Special Instruction.* Substitute 8X8468 Harness Assembly for 8X7653 Harness Assembly on the 785 Trucks.* Substitute 8X8467 Harness Assembly for 8X7652 Harness Assembly on the 789 Trucks.Follow the installation procedure outlined in the AEIS Special Instruction for the Ether Chassis Harness Assembly. Be sure to use the 8X8466 Wire Assembly for the 785 Trucks or the 8X8429 Wire Assembly for the 789 Trucks. This is the new harness code plug required with MPPS.Installation of 8X8469 Ether (Engine) Wiring Harness
The 8X7106 Engine Harness on the AEIS is replaced with 8X8469 Harness Assembly.Follow the installation procedure outlined in the AEIS Special Instruction for the 8X7106 Harness Assembly. In addition, the following steps need to be performed. 1. Route the end of the harness with the 8T8732 Receptacle to the 3E3530 Electronic Control Group (oil pressure sensor) installed at the right rear of the engine as shown.2. Connect the three pin receptacle to the connector on the 3E3530 Electronic Control Group (2) and clip into the 9X3495 Clip Assembly (7) installed earlier. Use 3S2093 Straps (8) to loosely secure the harness to the top rear of the engine as shown.3. Remove the 8W3048 Harness Assembly that is connected to the remaining 6T7663 Oil Pressure Switch (9) and was connected to the 6T7663 Oil Pressure Switch (9) that was removed.4. Connect an 8X8337 Harness Assembly (10) to the one remaining oil pressure switch and reconnect to the engine harness. Clip with the existing clip. DO NOT tighten the straps or clips until all new wiring harnesses have been installed so any repositioning or adjustments can be made as necessary.Checking the Automatic Ether Injection System
* The system check-out will be same as for the AEIS with the following change: "A5" harness code on the 785 (indicates 3512 application) or "A6" harness code on the 789 (indicates 3516 application) for two seconds.Retrofit to an Existing AEIS System
Necessary Parts
Installation of 3E3778 Ether Control Group
The 3E3778 Control Group is required for the MPPS System.Check the electronic control box installed with the AEIS to see if it is a 3E3778 or a 9X5303 Control Group. If a 9X5303 control Group is installed, replace it with 3E3778 Control Group and 3E3779 Film.Follow the "Installation of 9X5303 Ether Control Group" instructions outlined in the AEIS installation Special Instruction, SEHS9293. Be sure to install the 8X8398 Wire Assembly between the control and mounting plate. If an MPPS identification film is
The ether chassis harness for MPPS is different than the one called out in the AEIS Special Instruction.* Substitute 8X8468 Harness Assembly for 8X7653 Harness Assembly on the 785 Trucks.* Substitute 8X8467 Harness Assembly for 8X7652 Harness Assembly on the 789 Trucks.Follow the installation procedure outlined in the AEIS Special Instruction for the Ether Chassis Harness Assembly. Be sure to use the 8X8466 Wire Assembly for the 785 Trucks or the 8X8429 Wire Assembly for the 789 Trucks. This is the new harness code plug required with MPPS.Installation of 8X8469 Ether (Engine) Wiring Harness
The 8X7106 Engine Harness on the AEIS is replaced with 8X8469 Harness Assembly.Follow the installation procedure outlined in the AEIS Special Instruction for the 8X7106 Harness Assembly. In addition, the following steps need to be performed. 1. Route the end of the harness with the 8T8732 Receptacle to the 3E3530 Electronic Control Group (oil pressure sensor) installed at the right rear of the engine as shown.2. Connect the three pin receptacle to the connector on the 3E3530 Electronic Control Group (2) and clip into the 9X3495 Clip Assembly (7) installed earlier. Use 3S2093 Straps (8) to loosely secure the harness to the top rear of the engine as shown.3. Remove the 8W3048 Harness Assembly that is connected to the remaining 6T7663 Oil Pressure Switch (9) and was connected to the 6T7663 Oil Pressure Switch (9) that was removed.4. Connect an 8X8337 Harness Assembly (10) to the one remaining oil pressure switch and reconnect to the engine harness. Clip with the existing clip. DO NOT tighten the straps or clips until all new wiring harnesses have been installed so any repositioning or adjustments can be made as necessary.Checking the Automatic Ether Injection System
* The system check-out will be same as for the AEIS with the following change: "A5" harness code on the 785 (indicates 3512 application) or "A6" harness code on the 789 (indicates 3516 application) for two seconds.Retrofit to an Existing AEIS System
Necessary Parts
Installation of 3E3778 Ether Control Group
The 3E3778 Control Group is required for the MPPS System.Check the electronic control box installed with the AEIS to see if it is a 3E3778 or a 9X5303 Control Group. If a 9X5303 control Group is installed, replace it with 3E3778 Control Group and 3E3779 Film.Follow the "Installation of 9X5303 Ether Control Group" instructions outlined in the AEIS installation Special Instruction, SEHS9293. Be sure to install the 8X8398 Wire Assembly between the control and mounting plate. If an MPPS identification film is