Information injection-pump assembly
ZEXEL
101491-9630
1014919630
MAZDA
SLB113800
slb113800
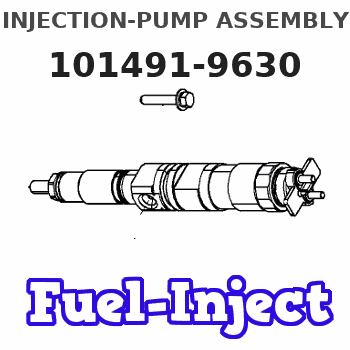
Rating:
Service parts 101491-9630 INJECTION-PUMP ASSEMBLY:
1.
_
6.
COUPLING PLATE
7.
COUPLING PLATE
8.
_
9.
_
11.
Nozzle and Holder
SL50 13 H50A
12.
Open Pre:MPa(Kqf/cm2)
16.7{170}
15.
NOZZLE SET
Cross reference number
ZEXEL
101491-9630
1014919630
MAZDA
SLB113800
slb113800
Zexel num
Bosch num
Firm num
Name
Calibration Data:
Adjustment conditions
Test oil
1404 Test oil ISO4113 or {SAEJ967d}
1404 Test oil ISO4113 or {SAEJ967d}
Test oil temperature
degC
40
40
45
Nozzle and nozzle holder
105780-8140
Bosch type code
EF8511/9A
Nozzle
105780-0000
Bosch type code
DN12SD12T
Nozzle holder
105780-2080
Bosch type code
EF8511/9
Opening pressure
MPa
17.2
Opening pressure
kgf/cm2
175
Injection pipe
Outer diameter - inner diameter - length (mm) mm 6-2-600
Outer diameter - inner diameter - length (mm) mm 6-2-600
Overflow valve opening pressure
kPa
157
123
191
Overflow valve opening pressure
kgf/cm2
1.6
1.25
1.95
Tester oil delivery pressure
kPa
157
157
157
Tester oil delivery pressure
kgf/cm2
1.6
1.6
1.6
Direction of rotation (viewed from drive side)
Right R
Right R
Injection timing adjustment
Direction of rotation (viewed from drive side)
Right R
Right R
Injection order
1-3-4-2
Pre-stroke
mm
3.4
3.35
3.45
Beginning of injection position
Drive side NO.1
Drive side NO.1
Difference between angles 1
Cal 1-3 deg. 90 89.5 90.5
Cal 1-3 deg. 90 89.5 90.5
Difference between angles 2
Cal 1-4 deg. 180 179.5 180.5
Cal 1-4 deg. 180 179.5 180.5
Difference between angles 3
Cyl.1-2 deg. 270 269.5 270.5
Cyl.1-2 deg. 270 269.5 270.5
Injection quantity adjustment
Adjusting point
-
Rack position
11.21+-0
.02
Pump speed
r/min
1000
1000
1000
Average injection quantity
mm3/st.
56.8
56.3
57.3
Max. variation between cylinders
%
0
-2.5
2.5
Basic
*
Fixing the rack
*
Standard for adjustment of the maximum variation between cylinders
*
Injection quantity adjustment_02
Adjusting point
-
Rack position
9.6+-0.5
Pump speed
r/min
325
325
325
Average injection quantity
mm3/st.
9
7
11
Max. variation between cylinders
%
0
-14
14
Fixing the rack
*
Standard for adjustment of the maximum variation between cylinders
*
Remarks
Adjust only variation between cylinders; adjust governor according to governor specifications.
Adjust only variation between cylinders; adjust governor according to governor specifications.
Injection quantity adjustment_03
Adjusting point
A
Rack position
11.21+-0
.5
Pump speed
r/min
1000
1000
1000
Average injection quantity
mm3/st.
56.8
56.3
57.3
Basic
*
Fixing the lever
*
Injection quantity adjustment_04
Adjusting point
B
Rack position
11.48+-0
.5
Pump speed
r/min
1700
1700
1700
Average injection quantity
mm3/st.
68.9
66.9
70.9
Fixing the lever
*
Injection quantity adjustment_05
Adjusting point
C
Rack position
11.32+-0
.5
Pump speed
r/min
625
625
625
Average injection quantity
mm3/st.
42
40
44
Fixing the lever
*
Injection quantity adjustment_06
Adjusting point
I
Rack position
16.3+-0.
5
Pump speed
r/min
100
100
100
Average injection quantity
mm3/st.
91
81
96
Fixing the lever
*
Rack limit
*
Injection quantity adjustment_07
Adjusting point
H
Rack position
9.3+-0.5
Pump speed
r/min
325
325
325
Average injection quantity
mm3/st.
7
6.5
7.5
Fixing the lever
*
Timer adjustment
Pump speed
r/min
1350+-25
Advance angle
deg.
0
0
0
Remarks
Start
Start
Timer adjustment_02
Pump speed
r/min
1700
Advance angle
deg.
3.5
3.2
3.8
Remarks
Finish
Finish
Test data Ex:
Governor adjustment
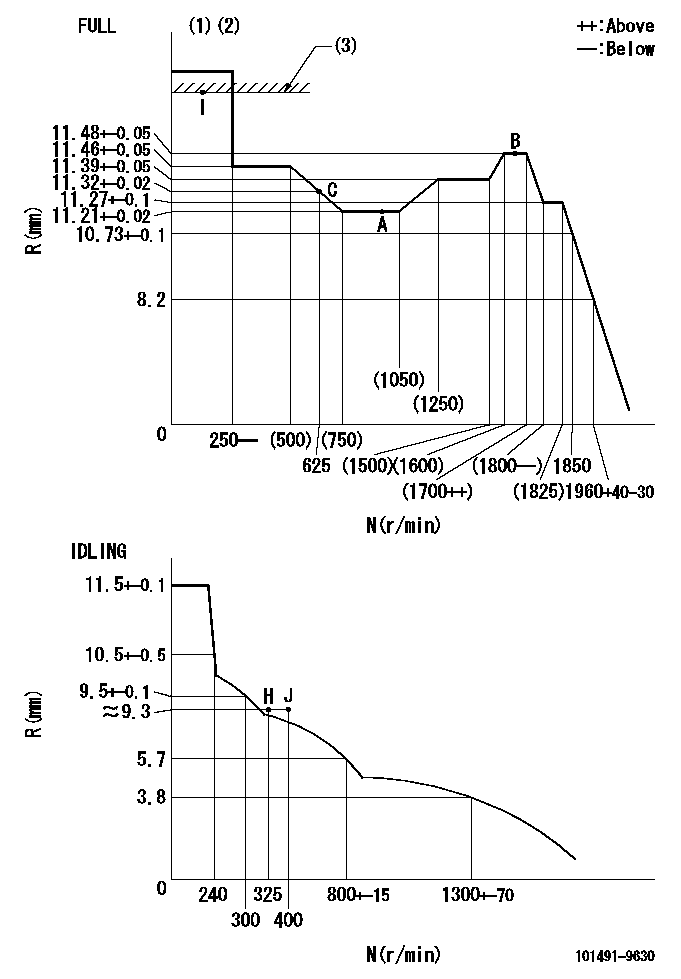
N:Pump speed
R:Rack position (mm)
(1)Torque cam stamping: T1
(2)Tolerance for racks not indicated: R1, speed N1
(3)RACK LIMIT
----------
T1=C83 R1=+-0.02mm N1=+-3r/min
----------
----------
T1=C83 R1=+-0.02mm N1=+-3r/min
----------
Speed control lever angle
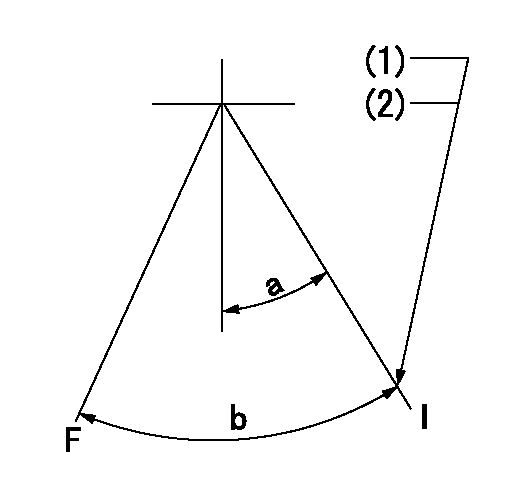
F:Full speed
I:Idle
(1)Stopper bolt setting
(2)Rack position = aa, speed = bb
----------
aa=(9.3)mm bb=325r/min
----------
a=20deg+-5deg b=41deg+-3deg
----------
aa=(9.3)mm bb=325r/min
----------
a=20deg+-5deg b=41deg+-3deg
Stop lever angle

N:Pump normal
S:Engine stop
(1)Use the hole at R = aa
(2)Set the stop adjuster screw
----------
aa=39mm
----------
a=14deg+-5deg b=(29deg)+-5deg
----------
aa=39mm
----------
a=14deg+-5deg b=(29deg)+-5deg
0000001501 GOV RACK POSITION CONFIRM
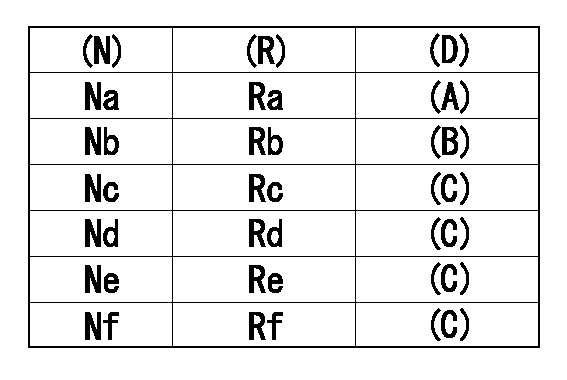
Confirm the governor adjustment rack position.
Standard point A
Set the torque cam B.
(C) Confirmation
(D) Remarks
(N): Speed of the pump
(R) Rack position (mm)
----------
----------
Na=1000r/min Nb=625r/min Nc=1800r/min Nd=1700r/min Ne=1400r/min Nf=450r/min Ra=11.21+-0.02mm Rb=11.32+-0.02mm Rc=11.27+-0.1mm Rd=11.48+-0.05mm Re=11.39+-0.05mm Rf=11.46+-0.05mm
----------
----------
Na=1000r/min Nb=625r/min Nc=1800r/min Nd=1700r/min Ne=1400r/min Nf=450r/min Ra=11.21+-0.02mm Rb=11.32+-0.02mm Rc=11.27+-0.1mm Rd=11.48+-0.05mm Re=11.39+-0.05mm Rf=11.46+-0.05mm
0000001601 LEVER

CL:Center line of camshaft
ST:Stop adjuster screw
f1:Direction for pulling the speed lever
f2:Direction for pulling the stop lever
1. Stop lever adjustment outline
(1)After completing all adjustments, confirm that the lever angle is within the specifications in the normal position.
(2)Set the speed lever in the full speed position.
(3)At pump speed Na, position the rack at non-injection position Ra.
(4)Set the stop adjusting screw to fix the speed lever in the idling position.
(5)Confirm that there is no injection at pump speed Nb.
----------
Na=1825r/min Nb=325r/min Ra=5.3-0.5mm
----------
----------
Na=1825r/min Nb=325r/min Ra=5.3-0.5mm
----------
Timing setting

(1)Pump vertical direction
(2)Position of gear mark 'CC' at No 1 cylinder's beginning of injection
(3)-
(4)-
----------
----------
a=(130deg)
----------
----------
a=(130deg)
Information:
Operating Cost Information
The term "Life Cycle Costs" can be defined as the sum of the individual costs experienced by an engine from the day of purchase until the day of retirement. In other words, the total Owning and Operating Costs. Owning Costs are fixed costs such as initial purchase price, interest on borrowed money, depreciation and taxes. Operating Costs are a combination of fixed and variable costs such as fuel, oil, operator expenses, equipment maintenance and repair, engine maintenance and repair, and downtime.The difference between revenues generated and Life Cycle Costs (total Owning and Operating Costs) is profit.Caterpillar and your Caterpillar dealer cannot guarantee that you will make a profit. However, Caterpillar and your Caterpillar dealer can provide you with a variety of services that can help you reduce the costs that impact your profits.An Engine Operating Cost Analysis is a service provided by your dealer that was developed by Caterpillar to help you reduce the Life Cycle Cost of your engine. More specifically, an Engine Operating Cost Analysis is a computerized program that examines current and prospective oil, fuel, maintenance, minor repair, overhaul and downtime costs for the period of time you expect to own the engine. It also calculates the operating cost per hour.This useful tool provides your dealer with the specific information needed to develop a customized Maintenance Management program for your operation which will minimize your engine's operating costs.Before a cost analysis can be performed, your dealer needs to gather as much information as possible about your operation. He will need to know the length of time you plan to keep your engine, your average cost of fuel and oil as well as a variety of other ownership and cost related facts and figures.Once this information is obtained, your dealer will enter the data into an established computerized program to produce an Engine Operating Cost Analysis printout reflecting your current and projected operating costs per hour. Current and expected cost information is reflected in the data provided by you. These are the costs that affect your engine's operating cost.The General Information section contains basic user data such as name, business, location, ownership, usage per year, etc., information.The Engine Operating Information section is divided into eight subsections that address fuel consumption, oil consumption, preventive maintenance, component repairs such as water pumps, turbochargers, air compressors, etc., before failure repairs, after failure repairs, user's revenue rate per hour and lastly, miscellaneous costs such as operator wages, insurance premiums, etc.Engine Operating Cost Summary
The Operating Cost Summary is exactly what it implies, a summary. Here the total dollar expense and percentage of the total operating expense is calculated for each subsection. The individual elements are then totaled and divided by the ownership period to yield the cost per hour. Similar calculations are also made for only the maintenance and repair portion of the total operating cost.An Engine Operating Cost Analysis is a useful tool that can be used to: * Project the expected operating cost of a Caterpillar engine.*
The term "Life Cycle Costs" can be defined as the sum of the individual costs experienced by an engine from the day of purchase until the day of retirement. In other words, the total Owning and Operating Costs. Owning Costs are fixed costs such as initial purchase price, interest on borrowed money, depreciation and taxes. Operating Costs are a combination of fixed and variable costs such as fuel, oil, operator expenses, equipment maintenance and repair, engine maintenance and repair, and downtime.The difference between revenues generated and Life Cycle Costs (total Owning and Operating Costs) is profit.Caterpillar and your Caterpillar dealer cannot guarantee that you will make a profit. However, Caterpillar and your Caterpillar dealer can provide you with a variety of services that can help you reduce the costs that impact your profits.An Engine Operating Cost Analysis is a service provided by your dealer that was developed by Caterpillar to help you reduce the Life Cycle Cost of your engine. More specifically, an Engine Operating Cost Analysis is a computerized program that examines current and prospective oil, fuel, maintenance, minor repair, overhaul and downtime costs for the period of time you expect to own the engine. It also calculates the operating cost per hour.This useful tool provides your dealer with the specific information needed to develop a customized Maintenance Management program for your operation which will minimize your engine's operating costs.Before a cost analysis can be performed, your dealer needs to gather as much information as possible about your operation. He will need to know the length of time you plan to keep your engine, your average cost of fuel and oil as well as a variety of other ownership and cost related facts and figures.Once this information is obtained, your dealer will enter the data into an established computerized program to produce an Engine Operating Cost Analysis printout reflecting your current and projected operating costs per hour. Current and expected cost information is reflected in the data provided by you. These are the costs that affect your engine's operating cost.The General Information section contains basic user data such as name, business, location, ownership, usage per year, etc., information.The Engine Operating Information section is divided into eight subsections that address fuel consumption, oil consumption, preventive maintenance, component repairs such as water pumps, turbochargers, air compressors, etc., before failure repairs, after failure repairs, user's revenue rate per hour and lastly, miscellaneous costs such as operator wages, insurance premiums, etc.Engine Operating Cost Summary
The Operating Cost Summary is exactly what it implies, a summary. Here the total dollar expense and percentage of the total operating expense is calculated for each subsection. The individual elements are then totaled and divided by the ownership period to yield the cost per hour. Similar calculations are also made for only the maintenance and repair portion of the total operating cost.An Engine Operating Cost Analysis is a useful tool that can be used to: * Project the expected operating cost of a Caterpillar engine.*