Information injection-pump assembly
ZEXEL
101491-9531
1014919531
MAZDA
SLF113800A
slf113800a
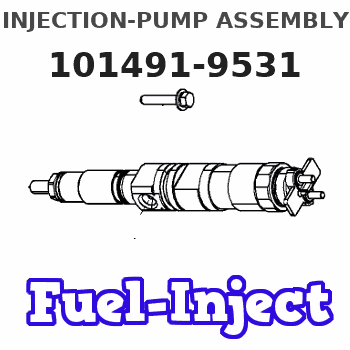
Rating:
Service parts 101491-9531 INJECTION-PUMP ASSEMBLY:
1.
_
6.
COUPLING PLATE
7.
COUPLING PLATE
8.
_
9.
_
11.
Nozzle and Holder
SL50 13 H50A
12.
Open Pre:MPa(Kqf/cm2)
16.7{170}
15.
NOZZLE SET
Cross reference number
ZEXEL
101491-9531
1014919531
MAZDA
SLF113800A
slf113800a
Zexel num
Bosch num
Firm num
Name
Calibration Data:
Adjustment conditions
Test oil
1404 Test oil ISO4113 or {SAEJ967d}
1404 Test oil ISO4113 or {SAEJ967d}
Test oil temperature
degC
40
40
45
Nozzle and nozzle holder
105780-8140
Bosch type code
EF8511/9A
Nozzle
105780-0000
Bosch type code
DN12SD12T
Nozzle holder
105780-2080
Bosch type code
EF8511/9
Opening pressure
MPa
17.2
Opening pressure
kgf/cm2
175
Injection pipe
Outer diameter - inner diameter - length (mm) mm 6-2-600
Outer diameter - inner diameter - length (mm) mm 6-2-600
Overflow valve
131424-3420
Overflow valve opening pressure
kPa
255
221
289
Overflow valve opening pressure
kgf/cm2
2.6
2.25
2.95
Tester oil delivery pressure
kPa
157
157
157
Tester oil delivery pressure
kgf/cm2
1.6
1.6
1.6
Direction of rotation (viewed from drive side)
Right R
Right R
Injection timing adjustment
Direction of rotation (viewed from drive side)
Right R
Right R
Injection order
1-3-4-2
Pre-stroke
mm
3.2
3.15
3.25
Beginning of injection position
Drive side NO.1
Drive side NO.1
Difference between angles 1
Cal 1-3 deg. 90 89.5 90.5
Cal 1-3 deg. 90 89.5 90.5
Difference between angles 2
Cal 1-4 deg. 180 179.5 180.5
Cal 1-4 deg. 180 179.5 180.5
Difference between angles 3
Cyl.1-2 deg. 270 269.5 270.5
Cyl.1-2 deg. 270 269.5 270.5
Injection quantity adjustment
Adjusting point
-
Rack position
12.77+-0
.02
Pump speed
r/min
1000
1000
1000
Average injection quantity
mm3/st.
73.2
72.7
73.7
Max. variation between cylinders
%
0
-2.5
2.5
Basic
*
Fixing the rack
*
Standard for adjustment of the maximum variation between cylinders
*
Injection quantity adjustment_02
Adjusting point
-
Rack position
10.1+-0.
5
Pump speed
r/min
340
340
340
Average injection quantity
mm3/st.
10
8
12
Max. variation between cylinders
%
0
-14
14
Fixing the rack
*
Standard for adjustment of the maximum variation between cylinders
*
Remarks
Adjust only variation between cylinders; adjust governor according to governor specifications.
Adjust only variation between cylinders; adjust governor according to governor specifications.
Injection quantity adjustment_03
Adjusting point
A
Rack position
12.77+-0
.5
Pump speed
r/min
1000
1000
1000
Average injection quantity
mm3/st.
73.2
72.7
73.7
Basic
*
Fixing the lever
*
Boost pressure
kPa
21.3
21.3
Boost pressure
mmHg
160
160
Injection quantity adjustment_04
Adjusting point
B
Rack position
12.91+-0
.5
Pump speed
r/min
1600
1600
1600
Average injection quantity
mm3/st.
83.7
81.7
85.7
Fixing the lever
*
Boost pressure
kPa
21.3
21.3
Boost pressure
mmHg
160
160
Injection quantity adjustment_05
Adjusting point
C
Rack position
11.97+-0
.5
Pump speed
r/min
750
750
750
Average injection quantity
mm3/st.
49.3
47.3
51.3
Fixing the lever
*
Boost pressure
kPa
21.3
21.3
Boost pressure
mmHg
160
160
Injection quantity adjustment_06
Adjusting point
I
Rack position
-
Pump speed
r/min
100
100
100
Average injection quantity
mm3/st.
75
70
85
Fixing the lever
*
Boost pressure
kPa
0
0
0
Boost pressure
mmHg
0
0
0
Rack limit
*
Boost compensator adjustment
Pump speed
r/min
600
600
600
Rack position
10.49+-0
.05
Boost pressure
kPa
2
2
4.7
Boost pressure
mmHg
15
15
35
Boost compensator adjustment_02
Pump speed
r/min
600
600
600
Rack position
11.69+-0
.02
Boost pressure
kPa
12
9.3
14.7
Boost pressure
mmHg
90
70
110
Timer adjustment
Pump speed
r/min
1500+-25
Advance angle
deg.
0
0
0
Remarks
Start
Start
Timer adjustment_02
Pump speed
r/min
1750
Advance angle
deg.
3
2.7
3.3
Remarks
Finish
Finish
Test data Ex:
Governor adjustment
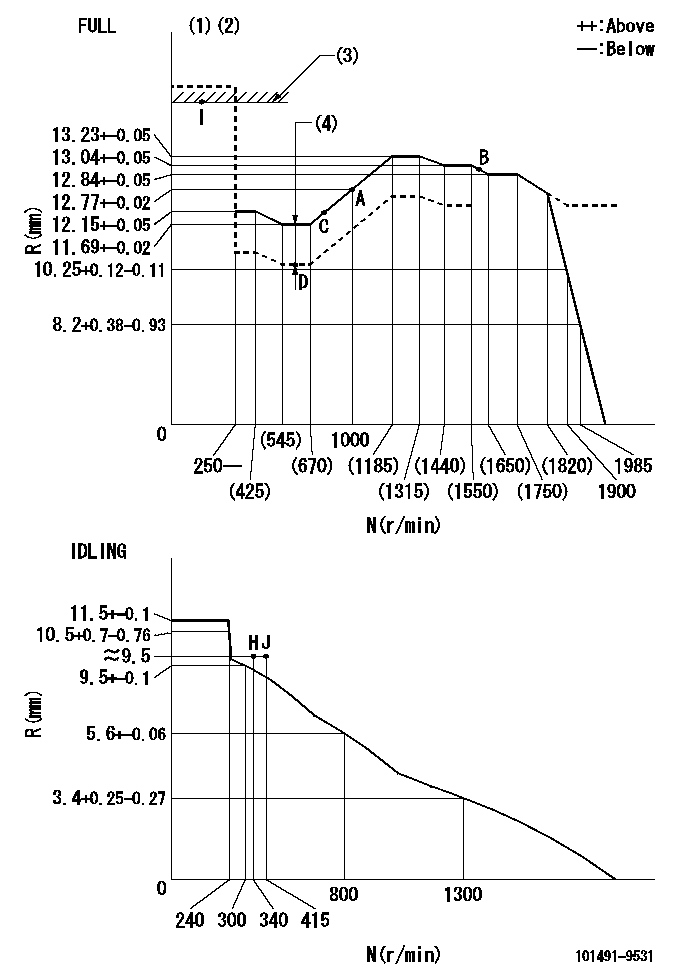
N:Pump speed
R:Rack position (mm)
(1)Torque cam stamping: T1
(2)Tolerance for racks not indicated: R1, speed N1
(3)RACK LIMIT
(4)Boost compensator stroke: BCL
----------
T1=M87 R1=+-0.02mm N1=+-3r/min BCL=1.2+-0.1mm
----------
----------
T1=M87 R1=+-0.02mm N1=+-3r/min BCL=1.2+-0.1mm
----------
Speed control lever angle

F:Full speed
I:Idle
(1)Use the hole at R = aa
(2)Stopper bolt set position 'H'
----------
aa=36mm
----------
a=20deg+-5deg b=43deg+-3deg
----------
aa=36mm
----------
a=20deg+-5deg b=43deg+-3deg
Stop lever angle

N:Pump normal
S:Engine stop
(1)Use the hole at R = aa
(2)Set the stop adjuster screw
----------
aa=39mm
----------
a=14deg+-5deg b=(29deg)+-5deg
----------
aa=39mm
----------
a=14deg+-5deg b=(29deg)+-5deg
0000001501 GOV RACK POSITION CONFIRM
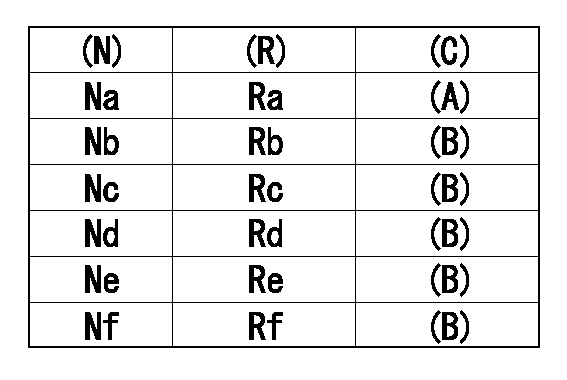
Confirm the governor adjustment rack position.
(N): Speed of the pump
(R) Rack position (mm)
Standard point A
(B) Confirmation
Remarks C
----------
----------
Na=1000r/min Nb=625r/min Nc=1700r/min Nd=1500r/min Ne=1250r/min Nf=400r/min Ra=12.77+-0.02mm Rb=11.69+-0.02mm Rc=12.84+-0.05mm Rd=13.04+-0.05mm Re=13.23+-0.05mm Rf=12.15+-0.05mm
----------
----------
Na=1000r/min Nb=625r/min Nc=1700r/min Nd=1500r/min Ne=1250r/min Nf=400r/min Ra=12.77+-0.02mm Rb=11.69+-0.02mm Rc=12.84+-0.05mm Rd=13.04+-0.05mm Re=13.23+-0.05mm Rf=12.15+-0.05mm
0000001601 LEVER

CL:Center line of camshaft
ST:Stop adjuster screw
f1:Direction for pulling the speed lever
f2:Direction for pulling the stop lever
1. Stop lever adjustment outline
(1)After completing all adjustments, confirm that the lever angle is within the specifications in the normal position.
(2)Set the speed lever in the full speed position.
(3)At pump speed Na, position the rack at non-injection position Ra.
(4)Set the stop adjusting screw to fix the speed lever in the idling position.
(5)Confirm that there is no injection at pump speed Nb.
----------
Na=1825r/min Nb=340r/min Ra=5.1+-0.3mm
----------
----------
Na=1825r/min Nb=340r/min Ra=5.1+-0.3mm
----------
Timing setting

(1)Pump vertical direction
(2)Position of gear mark 'CC' at No 1 cylinder's beginning of injection
(3)-
(4)-
----------
----------
a=(130deg)
----------
----------
a=(130deg)
Information:
Stopping the engine immediately after it has been working under load can result in overheating and accelerated wear of the engine components. Allow the engine to engine cool down before stopping. Avoiding hot engine shutdowns will maximize turbocharger shaft and bearing life.
If the engine has been operating at high load, run at low idle for at least three minutes before stopping. This cool down will reduce and stabilize internal engine coolant and oil temperatures before stopping the engine.If the engine has been operating at low loads, run the engine at low idle for 30 seconds before stopping.Make sure the shutoff procedure is understood. Refer to the Stopping the Engine instructions in the Generator Set Control Panel topic in this publication. Use the following general guidelines for stopping the engine.1. Open the Main electrical circuit breaker/Remove load from engine.2. Move the governor control to no more than half engine speed. Run the engine for three to five minutes.3. Reduce the engine speed to low idle.4. The engine may be stopped by using the Woodward Governor (if equipped), the Mechanical Governor (if equipped), or the solenoid shutoff switch.Woodward Actuator (If Equipped)
If equipped with a Woodward Actuator, move the control lever upward or forward, depending on the installation. Hold the lever to the OFF or STOP position until the engine stops.Mechanical Governor Control
A manual shutoff lever is provided to shut off the fuel from the fuel injection pump and override the governor control. The manual shutoff lever is located on the side of the pump.The engine can be shut OFF by rotating and holding the manual shutoff lever in the clockwise (CW) direction. If equipped with a Mechanical Governor Control, to move control to the SHUT OFF position: pull upward on the vernier hand grip while pushing down on thumb button. This shutdown will only move the fuel control linkage (rack) to the FUEL-OFF position. This does not shut off the air inlet.Solenoid Shutoff
Move the Control Panel Engine Control Switch (ECS, if equipped) to the STOP position.After Stopping the Engine
1. Fill the fuel tank to prevent accumulation of moisture in the fuel.2. Check the coolant level. Maintain the cooling system to 13 mm (1/2 inch) from bottom of the fill pipe. If freezing temperatures are expected, allow the radiator and engine jacket water system to cool, then check the coolant for proper antifreeze protection. The cooling system must be protected against freezing to the lowest expected ambient (outside) temperature. Add the proper coolant and water mixture if necessary.3. Check the crankcase oil level. Maintain the oil level between the ADD and FULL marks in the FULL RANGE zone on the dipstick.4. Repair any leaks, perform minor adjustments, tighten loose bolts, etc. 5. Note the service hour meter reading. Perform periodic maintenance as instructed in the Maintenance Schedule.