Information injection-pump assembly
ZEXEL
101491-1071
1014911071
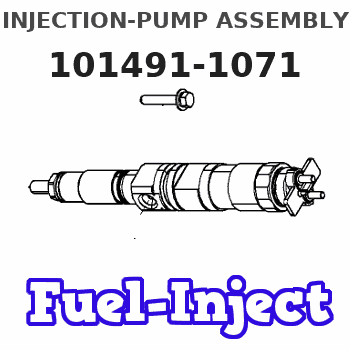
Rating:
Service parts 101491-1071 INJECTION-PUMP ASSEMBLY:
1.
_
3.
GOVERNOR
6.
COUPLING PLATE
7.
COUPLING PLATE
8.
_
9.
_
11.
Nozzle and Holder
ME790067
12.
Open Pre:MPa(Kqf/cm2)
21.6{220}
15.
NOZZLE SET
Cross reference number
ZEXEL
101491-1071
1014911071
Zexel num
Bosch num
Firm num
Name
Calibration Data:
Adjustment conditions
Test oil
1404 Test oil ISO4113 or {SAEJ967d}
1404 Test oil ISO4113 or {SAEJ967d}
Test oil temperature
degC
40
40
45
Nozzle and nozzle holder
105780-8140
Bosch type code
EF8511/9A
Nozzle
105780-0000
Bosch type code
DN12SD12T
Nozzle holder
105780-2080
Bosch type code
EF8511/9
Opening pressure
MPa
17.2
Opening pressure
kgf/cm2
175
Injection pipe
Outer diameter - inner diameter - length (mm) mm 6-2-600
Outer diameter - inner diameter - length (mm) mm 6-2-600
Overflow valve
131424-5620
Overflow valve opening pressure
kPa
157
123
191
Overflow valve opening pressure
kgf/cm2
1.6
1.25
1.95
Tester oil delivery pressure
kPa
157
157
157
Tester oil delivery pressure
kgf/cm2
1.6
1.6
1.6
Direction of rotation (viewed from drive side)
Right R
Right R
Injection timing adjustment
Direction of rotation (viewed from drive side)
Right R
Right R
Injection order
1-3-4-2
Pre-stroke
mm
3.5
3.45
3.55
Beginning of injection position
Drive side NO.1
Drive side NO.1
Difference between angles 1
Cal 1-3 deg. 90 89.5 90.5
Cal 1-3 deg. 90 89.5 90.5
Difference between angles 2
Cal 1-4 deg. 180 179.5 180.5
Cal 1-4 deg. 180 179.5 180.5
Difference between angles 3
Cyl.1-2 deg. 270 269.5 270.5
Cyl.1-2 deg. 270 269.5 270.5
Injection quantity adjustment
Adjusting point
-
Rack position
11.2
Pump speed
r/min
900
900
900
Average injection quantity
mm3/st.
59.5
58.5
60.5
Max. variation between cylinders
%
0
-2.5
2.5
Basic
*
Fixing the rack
*
Standard for adjustment of the maximum variation between cylinders
*
Injection quantity adjustment_02
Adjusting point
H
Rack position
9.7+-0.5
Pump speed
r/min
325
325
325
Average injection quantity
mm3/st.
10
8.7
11.3
Max. variation between cylinders
%
0
-10
10
Fixing the rack
*
Standard for adjustment of the maximum variation between cylinders
*
Remarks
Adjust only variation between cylinders; adjust governor according to governor specifications.
Adjust only variation between cylinders; adjust governor according to governor specifications.
Injection quantity adjustment_03
Adjusting point
A
Rack position
R1(11.2)
Pump speed
r/min
900
900
900
Average injection quantity
mm3/st.
59.5
58.5
60.5
Basic
*
Fixing the lever
*
Boost pressure
kPa
44
44
Boost pressure
mmHg
330
330
Injection quantity adjustment_04
Adjusting point
B
Rack position
R1+0.3
Pump speed
r/min
1750
1750
1750
Average injection quantity
mm3/st.
71
67
75
Fixing the lever
*
Boost pressure
kPa
44
44
Boost pressure
mmHg
330
330
Injection quantity adjustment_05
Adjusting point
C
Rack position
R1-0.4
Pump speed
r/min
700
700
700
Average injection quantity
mm3/st.
44.5
40.5
48.5
Fixing the lever
*
Boost pressure
kPa
0
0
0
Boost pressure
mmHg
0
0
0
Injection quantity adjustment_06
Adjusting point
I
Rack position
14.8+-0.
5
Pump speed
r/min
100
100
100
Average injection quantity
mm3/st.
66
66
71
Fixing the lever
*
Rack limit
*
Injection quantity adjustment_07
Adjusting point
D
Rack position
R1-0.25
Pump speed
r/min
500
500
500
Average injection quantity
mm3/st.
36.5
32.5
40.5
Fixing the lever
*
Boost pressure
kPa
0
0
0
Boost pressure
mmHg
0
0
0
Boost compensator adjustment
Pump speed
r/min
700
700
700
Rack position
R1-0.4
Boost pressure
kPa
12
12
12
Boost pressure
mmHg
90
90
90
Boost compensator adjustment_02
Pump speed
r/min
700
700
700
Rack position
R1-0.2
Boost pressure
kPa
20
18.7
21.3
Boost pressure
mmHg
150
140
160
Boost compensator adjustment_03
Pump speed
r/min
700
700
700
Rack position
R1(11.2)
Boost pressure
kPa
30.7
24
37.4
Boost pressure
mmHg
230
180
280
Timer adjustment
Pump speed
r/min
(1400+70
)
Advance angle
deg.
0
0
0
Remarks
Start
Start
Timer adjustment_02
Pump speed
r/min
1750
Advance angle
deg.
5
4.5
5.5
Remarks
Finish
Finish
Test data Ex:
Governor adjustment
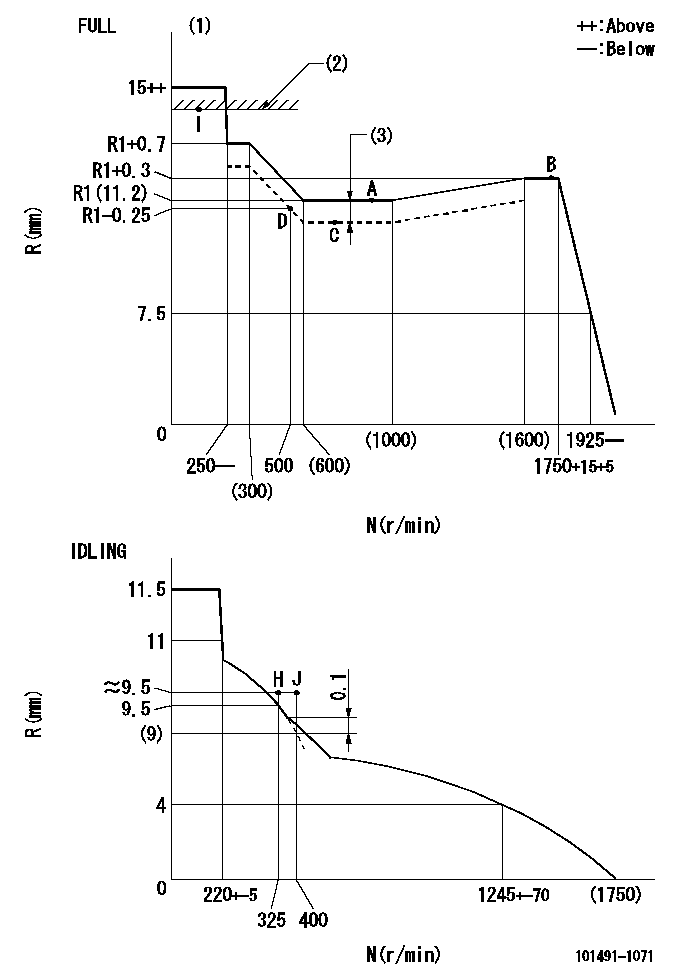
N:Pump speed
R:Rack position (mm)
(1)Torque cam stamping: T1
(2)RACK LIMIT: RAL
(3)Boost compensator stroke: BCL
----------
T1=A43 RAL=(14.8)mm BCL=0.4+-0.1mm
----------
----------
T1=A43 RAL=(14.8)mm BCL=0.4+-0.1mm
----------
Speed control lever angle
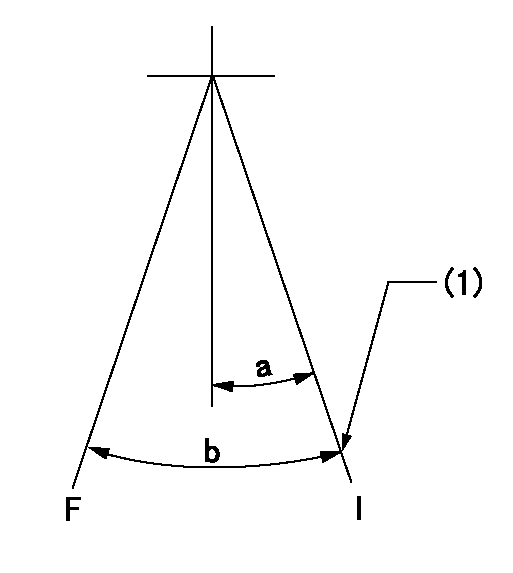
F:Full speed
I:Idle
(1)Stopper bolt set position 'H'
----------
----------
a=26deg+-5deg b=42deg+-3deg
----------
----------
a=26deg+-5deg b=42deg+-3deg
Stop lever angle
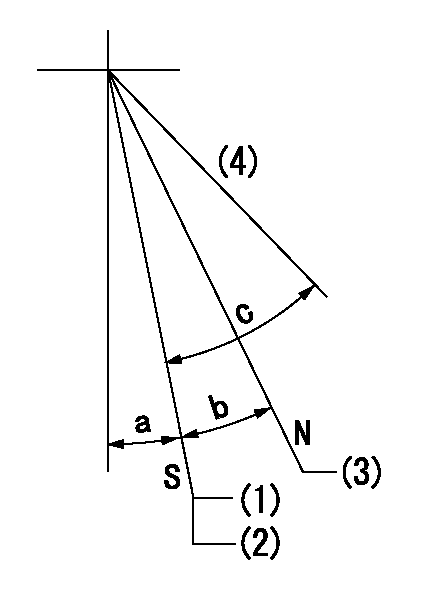
N:Pump normal
S:Stop the pump.
(1)Set the stopper bolt at speed = aa and rack position = bb.
(2)After setting the stopper bolt, confirm non-injection at speed = cc. Rack position = dd or less.
(3)Rack position = approximately ee.
(4)Free (at shipping)
----------
aa=1700r/min bb=6.5-0.5mm cc=325r/min dd=8mm ee=16mm
----------
a=8deg+-5deg b=15deg+-3deg c=25deg+-5deg
----------
aa=1700r/min bb=6.5-0.5mm cc=325r/min dd=8mm ee=16mm
----------
a=8deg+-5deg b=15deg+-3deg c=25deg+-5deg
0000001501 MICRO SWITCH
Adjustment of the micro-switch
Adjust the bolt to obtain the following lever position when the micro-switch is ON.
(1)Speed N1
(2)Rack position Ra
----------
N1=350r/min Ra=9.5mm
----------
----------
N1=350r/min Ra=9.5mm
----------
Timing setting

(1)Pump vertical direction
(2)Position of gear mark '3' at No 1 cylinder's beginning of injection
(3)B.T.D.C.: aa
(4)-
----------
aa=10deg
----------
a=(130deg)
----------
aa=10deg
----------
a=(130deg)
Information:
Start By:a. remove rocker shaft assembly and push rodsb. remove exhaust manifoldc. remove air cleaner groupd. remove aftercooler The procedure which follows was done on a 3306 Engine. 1. Remove bolts (1), mounting bracket and pipe assembly (2) and lifting bracket (3) from the cylinder head assembly. 2. Remove temperature sending unit (5) from elbow (4).3. Loosen clamp (6), and remove the bolts that hold elbow (4) to the water pump and cylinder head assembly. Remove the elbow and gaskets from the engine. 4. Install Tool (A) on the cylinder head assembly as shown, and fasten a hoist on it.
Do not set the cylinder head assembly on a flat surface because of possible damage to the fuel injection nozzle tips.
5. Remove all bolts (7) and (8) that hold the cylinder head assembly to the cylinder block. Remove the cylinder head assembly. The weight of the cylinder head assembly (3304) is 64 kg (142 lb). The weight of the cylinder head assembly (3306) is 95 kg (210 lb). 6. Remove head gasket (9), water seals (11) and the O-ring seal from dowel (10). Remove spacer plate (12), the spacer plate gasket and the O-ring seal from dowel (10).Install Cylinder Head Assembly & Spacer Plate
The procedure which follows was done on a 3306 Engine.
When the cylinder head assembly is removed a new spacer plate gasket and a new cylinder head gasket must be installed. Do not use any adhesive or other substances on these gaskets or the surfaces they contact.
1. Thoroughly clean the spacer plate, cylinder head and cylinder block surfaces. If dowel (1) was removed for any reason, install a new dowel until it extends 16.0 0.5 mm (.63 .02 in) from the cylinder block.2. Install the O-ring seal on dowel (1) against the cylinder block. Install spacer plate gasket (2) and spacer plate (3) on the cylinder block.3. Check the cylinder liner projection height. See topic, "Install Cylinder Liners". 4. Install the O-ring seal on top of the spacer plate around dowel (1). Install cylinder head gasket (4) and water seals (5). 5. Install Tool (A) on the cylinder head assembly as shown. Fasten a hoist to it. Put the cylinder head assembly in position on the engine.6. Put 2P2506 Thread Lubricant on all the cylinder head bolts. Install them until they are finger tight. Remove Tool (A) from the engine. 7. Install push rods (6). Make sure they are installed in their original locations. Be sure the push rods are in position in the valve lifters.8. Loosen the adjusting screws on the rocker arms for valve clearance. This will prevent a bend valve or push rod during installation of the rocker shaft assembly.9. Install a new O-ring seal in the rear rocker arm support bracket.10. Put 2P2506 Thread Lubricant on all of the rocker shaft bolts except the one that goes through the rear rocker arm support bracket.11. Put rocker shaft assembly (7) in position on the cylinder head assembly. Make sure the dowels in
Do not set the cylinder head assembly on a flat surface because of possible damage to the fuel injection nozzle tips.
5. Remove all bolts (7) and (8) that hold the cylinder head assembly to the cylinder block. Remove the cylinder head assembly. The weight of the cylinder head assembly (3304) is 64 kg (142 lb). The weight of the cylinder head assembly (3306) is 95 kg (210 lb). 6. Remove head gasket (9), water seals (11) and the O-ring seal from dowel (10). Remove spacer plate (12), the spacer plate gasket and the O-ring seal from dowel (10).Install Cylinder Head Assembly & Spacer Plate
The procedure which follows was done on a 3306 Engine.
When the cylinder head assembly is removed a new spacer plate gasket and a new cylinder head gasket must be installed. Do not use any adhesive or other substances on these gaskets or the surfaces they contact.
1. Thoroughly clean the spacer plate, cylinder head and cylinder block surfaces. If dowel (1) was removed for any reason, install a new dowel until it extends 16.0 0.5 mm (.63 .02 in) from the cylinder block.2. Install the O-ring seal on dowel (1) against the cylinder block. Install spacer plate gasket (2) and spacer plate (3) on the cylinder block.3. Check the cylinder liner projection height. See topic, "Install Cylinder Liners". 4. Install the O-ring seal on top of the spacer plate around dowel (1). Install cylinder head gasket (4) and water seals (5). 5. Install Tool (A) on the cylinder head assembly as shown. Fasten a hoist to it. Put the cylinder head assembly in position on the engine.6. Put 2P2506 Thread Lubricant on all the cylinder head bolts. Install them until they are finger tight. Remove Tool (A) from the engine. 7. Install push rods (6). Make sure they are installed in their original locations. Be sure the push rods are in position in the valve lifters.8. Loosen the adjusting screws on the rocker arms for valve clearance. This will prevent a bend valve or push rod during installation of the rocker shaft assembly.9. Install a new O-ring seal in the rear rocker arm support bracket.10. Put 2P2506 Thread Lubricant on all of the rocker shaft bolts except the one that goes through the rear rocker arm support bracket.11. Put rocker shaft assembly (7) in position on the cylinder head assembly. Make sure the dowels in