Information injection-pump assembly
BOSCH
9 400 611 689
9400611689
ZEXEL
101482-9330
1014829330
NISSAN-DIESEL
1679090413
1679090413
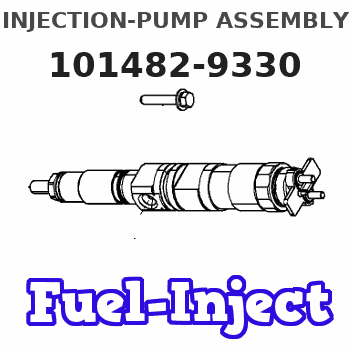
Rating:
Service parts 101482-9330 INJECTION-PUMP ASSEMBLY:
1.
_
5.
AUTOM. ADVANCE MECHANIS
6.
COUPLING PLATE
8.
_
9.
_
11.
Nozzle and Holder
16600-90104
12.
Open Pre:MPa(Kqf/cm2)
18.1{185}
15.
NOZZLE SET
Cross reference number
BOSCH
9 400 611 689
9400611689
ZEXEL
101482-9330
1014829330
NISSAN-DIESEL
1679090413
1679090413
Zexel num
Bosch num
Firm num
Name
101482-9330
9 400 611 689
1679090413 NISSAN-DIESEL
INJECTION-PUMP ASSEMBLY
BD30 K
BD30 K
Calibration Data:
Adjustment conditions
Test oil
1404 Test oil ISO4113 or {SAEJ967d}
1404 Test oil ISO4113 or {SAEJ967d}
Test oil temperature
degC
40
40
45
Nozzle and nozzle holder
105780-8140
Bosch type code
EF8511/9A
Nozzle
105780-0000
Bosch type code
DN12SD12T
Nozzle holder
105780-2080
Bosch type code
EF8511/9
Opening pressure
MPa
17.2
Opening pressure
kgf/cm2
175
Injection pipe
Outer diameter - inner diameter - length (mm) mm 6-2-600
Outer diameter - inner diameter - length (mm) mm 6-2-600
Overflow valve
131424-1520
Overflow valve opening pressure
kPa
157
123
191
Overflow valve opening pressure
kgf/cm2
1.6
1.25
1.95
Tester oil delivery pressure
kPa
157
157
157
Tester oil delivery pressure
kgf/cm2
1.6
1.6
1.6
Direction of rotation (viewed from drive side)
Right R
Right R
Injection timing adjustment
Direction of rotation (viewed from drive side)
Right R
Right R
Injection order
1-3-4-2
Pre-stroke
mm
3.2
3.15
3.25
Beginning of injection position
Drive side NO.1
Drive side NO.1
Difference between angles 1
Cal 1-3 deg. 90 89.5 90.5
Cal 1-3 deg. 90 89.5 90.5
Difference between angles 2
Cal 1-4 deg. 180 179.5 180.5
Cal 1-4 deg. 180 179.5 180.5
Difference between angles 3
Cyl.1-2 deg. 270 269.5 270.5
Cyl.1-2 deg. 270 269.5 270.5
Injection quantity adjustment
Adjusting point
A
Rack position
10.9
Pump speed
r/min
750
750
750
Average injection quantity
mm3/st.
44.7
43.7
45.7
Max. variation between cylinders
%
0
-3.5
3.5
Basic
*
Fixing the lever
*
Injection quantity adjustment_02
Adjusting point
-
Rack position
9.2+-0.5
Pump speed
r/min
450
450
450
Average injection quantity
mm3/st.
8
6
10
Max. variation between cylinders
%
0
-10
10
Fixing the rack
*
Remarks
Adjust only variation between cylinders; adjust governor according to governor specifications.
Adjust only variation between cylinders; adjust governor according to governor specifications.
Injection quantity adjustment_03
Adjusting point
C
Rack position
-
Pump speed
r/min
100
100
100
Average injection quantity
mm3/st.
62
62
72
Fixing the lever
*
Rack limit
*
Test data Ex:
Governor adjustment
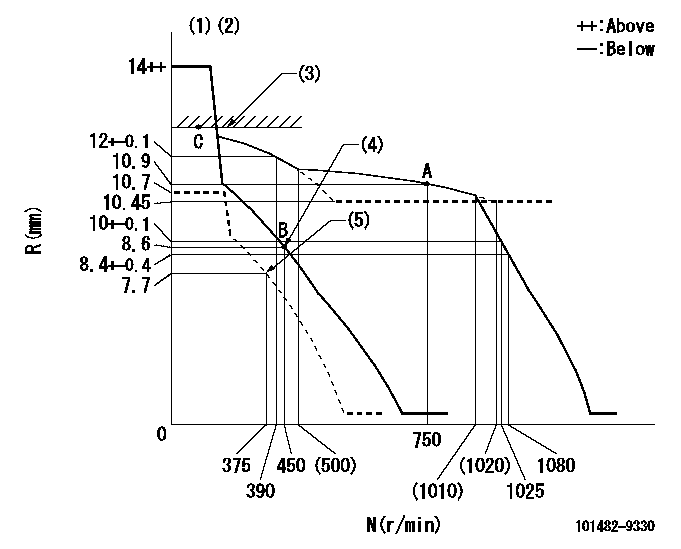
N:Pump speed
R:Rack position (mm)
(1)Target notch: K
(2)Tolerance for racks not indicated: +-0.05mm.
(3)RACK LIMIT
(4)Main spring setting
(5)Set idle sub-spring
----------
K=10
----------
----------
K=10
----------
Speed control lever angle
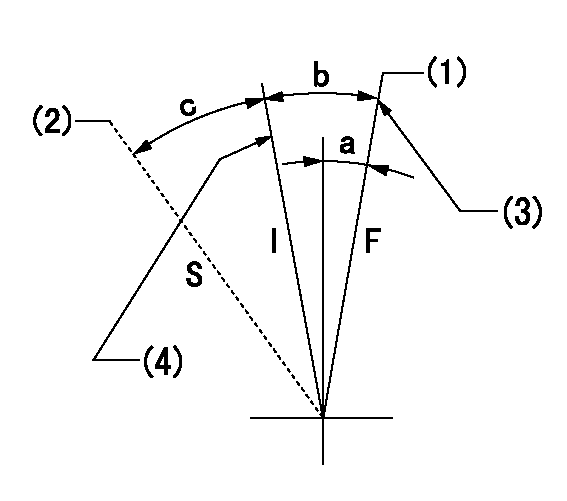
F:Full speed
I:Idle
S:Stop
(1)Set the pump speed at aa
(2)Confirmation
(3)Stopper bolt setting
(4)Stopper bolt setting
----------
aa=1025r/min
----------
a=4deg+-5deg b=13deg+-5deg c=26deg+-5deg
----------
aa=1025r/min
----------
a=4deg+-5deg b=13deg+-5deg c=26deg+-5deg
Stop lever angle

N:Pump normal
S:Stop the pump.
(1)Normal
----------
----------
a=12deg+-5deg b=53deg+-5deg
----------
----------
a=12deg+-5deg b=53deg+-5deg
Timing setting

(1)Pump vertical direction
(2)Position of gear mark 'ZZ' at No 1 cylinder's beginning of injection
(3)-
(4)-
----------
----------
a=(100deg)
----------
----------
a=(100deg)
Information:
(a) When regrinding journals of the crankshaft, be sure to refinish all journals to the same dimension.(b) Finish the fillet radius to R3 0.2 mm [0.1181 0.0079 in.].
Inspection of Oil Seal Contact Surface
Check the oil seal contact surface of the crankshaft back-end, and, if the crankshaft face has been excessively worn by the oil seal, replace the oil seal and oil sleeve with replacement parts.
Inspection of oil seal contact surface(1) Installation of oil seal sleeveTo install the oil seal sleeve, coat the inner surface of the sleeve with oil, and use the crankshaft sleeve installer for driving the sleeve into place.
Be careful not to dent or scratch the outer surface of the oil seal sleeve.
When the oil seal slinger becomes worn after engine operation, remove the oil seal sleeve by following the procedure below, and replace it with a replacement oil seal assembly (oil seal and oil seal sleeve).
Inspection of oil seal sleeve
Inspection of oil seal contact surface(2) Removal of oil seal sleeveAt three locations on the sleeve end face, hold a chisel at a right angle to the sleeve and strike with a hammer, and remove the sleeve when it becomes loose.If this method does not allow the removal of the sleeve, hold the chisel in the axial direction and lightly tap to expand and loosen the sleeve.
Be careful not to damage the crankshaft with the chisel when removing the oil seal sleeve.
Removal of oil seal sleeveMeasurement of Crankshaft Runout
Support the crankshaft on its front and rear journals in V-blocks, and measure the runout at the center journal with a dial gage. Compare the amount of runout with the standard. If the runout is small, correct by grinding. If the runout is large, straighten with a press.If the runout exceeds the limit significantly, replace the crankshaft.
Measurement of crankshaft runoutRemoval of Crankshaft Gear
Use the gear puller to remove the crankshaft gear. Do not remove the crankshaft gear unless the crankshaft or gear is replaced.
Removal of crankshaft gearInstallation of Crankshaft Gear
(1) Heat the gear to a temperature of 100 to 150 °C [212 to 302 °F].(2) Install the key to the crankshaft.(3) Align the gear with key and insert the gear fully.
Installation of crankshaft gearMeasurement of Cylinder Bore
(1) Using a cylinder gage, measure the cylinder bore and cylindricity. If the limit value is exceeded even at one place, bore all cylinders and replace the pistons and piston rings with oversize pistons and piston rings. Measure at three locations each in directions A and B shown in the diagram.
Measurement of inside diameter of cylinder(2) Boring of cylinders(a) Since there are two piston oversizes (0.25 mm [0.0098 in.] and 0.50 mm [0.0197 in.] oversize) as indicated above, determine the appropriate piston size to be used based on the largest cylinder bore diameter.(b) Measure the outside diameter of the piston to be used. The piston diameter measuring points are shown in the diagram.(c) Based on the measurements of the piston outside diameter, calculate the finishing dimension to be achieved by
Inspection of Oil Seal Contact Surface
Check the oil seal contact surface of the crankshaft back-end, and, if the crankshaft face has been excessively worn by the oil seal, replace the oil seal and oil sleeve with replacement parts.
Inspection of oil seal contact surface(1) Installation of oil seal sleeveTo install the oil seal sleeve, coat the inner surface of the sleeve with oil, and use the crankshaft sleeve installer for driving the sleeve into place.
Be careful not to dent or scratch the outer surface of the oil seal sleeve.
When the oil seal slinger becomes worn after engine operation, remove the oil seal sleeve by following the procedure below, and replace it with a replacement oil seal assembly (oil seal and oil seal sleeve).
Inspection of oil seal sleeve
Inspection of oil seal contact surface(2) Removal of oil seal sleeveAt three locations on the sleeve end face, hold a chisel at a right angle to the sleeve and strike with a hammer, and remove the sleeve when it becomes loose.If this method does not allow the removal of the sleeve, hold the chisel in the axial direction and lightly tap to expand and loosen the sleeve.
Be careful not to damage the crankshaft with the chisel when removing the oil seal sleeve.
Removal of oil seal sleeveMeasurement of Crankshaft Runout
Support the crankshaft on its front and rear journals in V-blocks, and measure the runout at the center journal with a dial gage. Compare the amount of runout with the standard. If the runout is small, correct by grinding. If the runout is large, straighten with a press.If the runout exceeds the limit significantly, replace the crankshaft.
Measurement of crankshaft runoutRemoval of Crankshaft Gear
Use the gear puller to remove the crankshaft gear. Do not remove the crankshaft gear unless the crankshaft or gear is replaced.
Removal of crankshaft gearInstallation of Crankshaft Gear
(1) Heat the gear to a temperature of 100 to 150 °C [212 to 302 °F].(2) Install the key to the crankshaft.(3) Align the gear with key and insert the gear fully.
Installation of crankshaft gearMeasurement of Cylinder Bore
(1) Using a cylinder gage, measure the cylinder bore and cylindricity. If the limit value is exceeded even at one place, bore all cylinders and replace the pistons and piston rings with oversize pistons and piston rings. Measure at three locations each in directions A and B shown in the diagram.
Measurement of inside diameter of cylinder(2) Boring of cylinders(a) Since there are two piston oversizes (0.25 mm [0.0098 in.] and 0.50 mm [0.0197 in.] oversize) as indicated above, determine the appropriate piston size to be used based on the largest cylinder bore diameter.(b) Measure the outside diameter of the piston to be used. The piston diameter measuring points are shown in the diagram.(c) Based on the measurements of the piston outside diameter, calculate the finishing dimension to be achieved by
Have questions with 101482-9330?
Group cross 101482-9330 ZEXEL
Dpico
Nissan-Diesel
Yanmar
Nissan-Diesel
101482-9330
9 400 611 689
1679090413
INJECTION-PUMP ASSEMBLY
BD30
BD30