Information injection-pump assembly
ZEXEL
101482-9310
1014829310
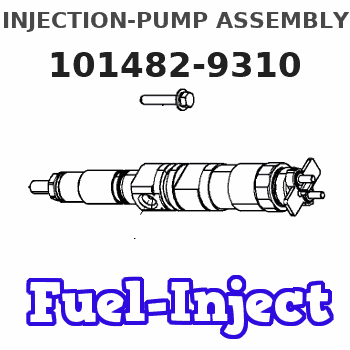
Rating:
Service parts 101482-9310 INJECTION-PUMP ASSEMBLY:
1.
_
5.
AUTOM. ADVANCE MECHANIS
6.
COUPLING PLATE
8.
_
9.
_
11.
Nozzle and Holder
16600-90104
12.
Open Pre:MPa(Kqf/cm2)
18.1{185}
15.
NOZZLE SET
Cross reference number
ZEXEL
101482-9310
1014829310
Zexel num
Bosch num
Firm num
Name
101482-9310
INJECTION-PUMP ASSEMBLY
Calibration Data:
Adjustment conditions
Test oil
1404 Test oil ISO4113 or {SAEJ967d}
1404 Test oil ISO4113 or {SAEJ967d}
Test oil temperature
degC
40
40
45
Nozzle and nozzle holder
105780-8140
Bosch type code
EF8511/9A
Nozzle
105780-0000
Bosch type code
DN12SD12T
Nozzle holder
105780-2080
Bosch type code
EF8511/9
Opening pressure
MPa
17.2
Opening pressure
kgf/cm2
175
Injection pipe
Outer diameter - inner diameter - length (mm) mm 6-2-600
Outer diameter - inner diameter - length (mm) mm 6-2-600
Overflow valve
131424-1520
Overflow valve opening pressure
kPa
157
123
191
Overflow valve opening pressure
kgf/cm2
1.6
1.25
1.95
Tester oil delivery pressure
kPa
157
157
157
Tester oil delivery pressure
kgf/cm2
1.6
1.6
1.6
Direction of rotation (viewed from drive side)
Right R
Right R
Injection timing adjustment
Direction of rotation (viewed from drive side)
Right R
Right R
Injection order
1-3-4-2
Pre-stroke
mm
3.2
3.15
3.25
Beginning of injection position
Drive side NO.1
Drive side NO.1
Difference between angles 1
Cal 1-3 deg. 90 89.5 90.5
Cal 1-3 deg. 90 89.5 90.5
Difference between angles 2
Cal 1-4 deg. 180 179.5 180.5
Cal 1-4 deg. 180 179.5 180.5
Difference between angles 3
Cyl.1-2 deg. 270 269.5 270.5
Cyl.1-2 deg. 270 269.5 270.5
Injection quantity adjustment
Adjusting point
A
Rack position
10.4
Pump speed
r/min
1075
1075
1075
Average injection quantity
mm3/st.
45.4
44.4
46.4
Max. variation between cylinders
%
0
-3.5
3.5
Basic
*
Fixing the lever
*
Injection quantity adjustment_02
Adjusting point
-
Rack position
9.2+-0.5
Pump speed
r/min
450
450
450
Average injection quantity
mm3/st.
8
6
10
Max. variation between cylinders
%
0
-10
10
Fixing the rack
*
Remarks
Adjust only variation between cylinders; adjust governor according to governor specifications.
Adjust only variation between cylinders; adjust governor according to governor specifications.
Injection quantity adjustment_03
Adjusting point
D
Rack position
-
Pump speed
r/min
100
100
100
Average injection quantity
mm3/st.
62
62
72
Fixing the lever
*
Rack limit
*
Test data Ex:
Governor adjustment
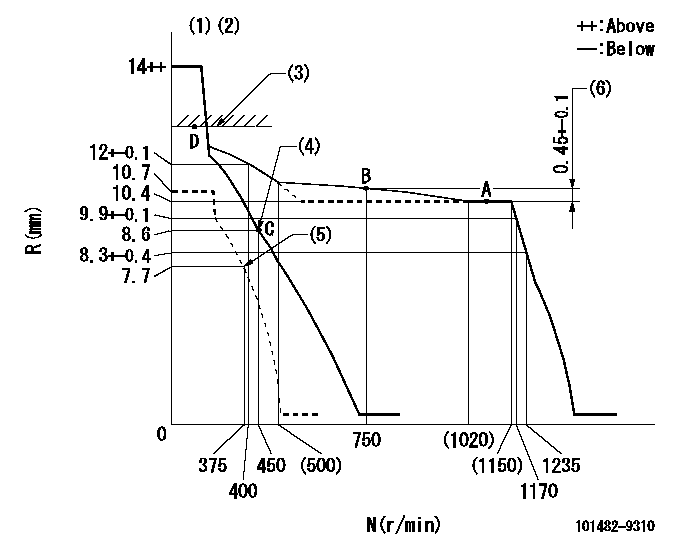
N:Pump speed
R:Rack position (mm)
(1)Target notch: K
(2)Tolerance for racks not indicated: +-0.05mm.
(3)RACK LIMIT
(4)Main spring setting
(5)Set idle sub-spring
(6)Rack difference from N = N1
----------
K=16 N1=1075r/min
----------
----------
K=16 N1=1075r/min
----------
Speed control lever angle
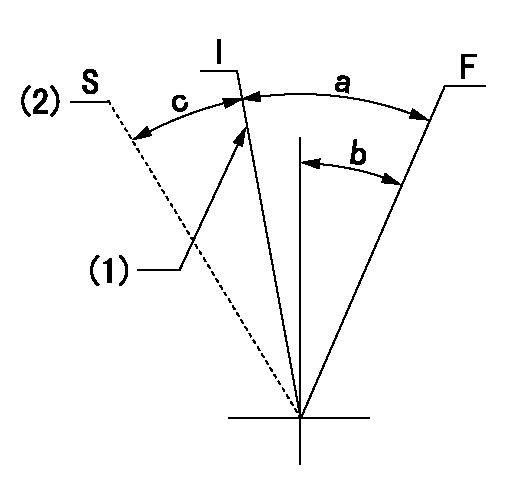
F:Full speed
I:Idle
S:Stop
(1)Set the stopper bolt at delivery
(2)Confirmation
----------
----------
a=(15eg)+-5deg b=(12deg)+-5deg c=(32deg)+-5deg
----------
----------
a=(15eg)+-5deg b=(12deg)+-5deg c=(32deg)+-5deg
Stop lever angle
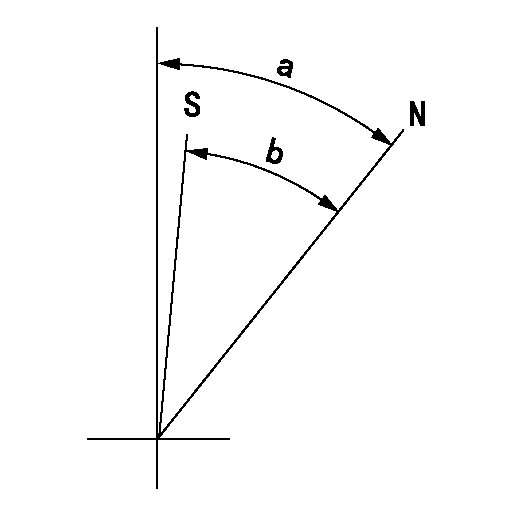
N:Pump normal
S:Stop the pump.
----------
----------
a=56.5deg+-5deg b=53deg+-5deg
----------
----------
a=56.5deg+-5deg b=53deg+-5deg
Timing setting

(1)Pump vertical direction
(2)Position of gear mark 'ZZ' at No 1 cylinder's beginning of injection
(3)-
(4)-
----------
----------
a=(100deg)
----------
----------
a=(100deg)
Information:
Adjustment of valve clearanceFuel System Bleeding
(1) Loosen the air vent plug of the fuel filter. (approx. 1.5 turns)(2) Move the priming pump for the filter up and down.(3) When fuel flowing from the vent hole no longer contains air bubbles, tighten the air vent plug.
Fuel system bleedingInspection and Adjustment of No-Load Minimum (Low Idling) Speed and Maximum Speed
(a) The following adjustments were inspected and set for each engine on the test bench at the factory, and the set bolts are sealed. These settings should be checked and adjusted only at our designated service shop.(b) After the governor parts are adjusted, all external stoppers must be sealed in the same way as when adjustments were made at the factory.(c) Whether the seals are intact or not has important bearing on the validity of claims under warranty. Be sure to seal all the specified sections.(d) When inspecting or adjusting, be ready to operate the engine stop lever manually in case the engine overruns (engine operation at extremely high speed).
Prior to inspection and adjustment, conduct a warm-up operation until the coolant and oil temperatures rise above 70 °C [158 °F].(1) Starting the engine(a) Pull the speed control lever toward the HIGH SPEED side, and operate the starter switch.(b) The engine ignites when the rotation speed reaches approximately 150 min-1, and the engine speed rises. Operate the speed control lever to maintain the engine speed between 800 and 1000 min-1.(c) After the engine speed stabilizes, return the speed control lever to the low idling position.
Inspection and adjustment of no-load minimum (low idling) speed and maximum speed(2) Low idling setting (no-load minimum rotation speed setting)Hold the speed control lever at the position of no-load minimum rotation speed, then secure the lever in that position using the idling adjustment screw.
If there is speed range which causes dangerous torsional vibration, avoid setting the engine speed in that range.
(3) Governor setting (maximum rotation speed setting)(a) Keep the speed control lever at the position of the specified maximum rotation speed.(b) With the speed control lever held in that position, adjust and set the governor set bolt (maximum rotation speed set screw) to the specified rotation speed).Inspection of V-Belt Tension
(1) Press the V-belt at a midpoint between the alternator and crankshaft pulley to check the mount of belt deflection.
Inspection of V-belt tension(2) If the amount of belt deflection does not conform to the standard value, loosen the adjusting bolt and move the alternator to adjust the belt tension.Engine Break-in Operation
When the engine is overhauled, it should be mounted on a dynamometer and operated for break-in and inspection.Starting Up
(1) Before starting the engine, check the levels of coolant, engine oil and fuel, and bleed the fuel and cooling system.(2) With the fuel supply cut off, operate the starter and crank the engine for about 15 seconds to circulate engine oil.(3) Move the speed control lever slightly in the direction for increased fuel (do not move it to "full injection" position), then turn the starter switch key to the [START]
Have questions with 101482-9310?
Group cross 101482-9310 ZEXEL
Dpico
101482-9310
INJECTION-PUMP ASSEMBLY