Information injection-pump assembly
ZEXEL
101482-9080
1014829080
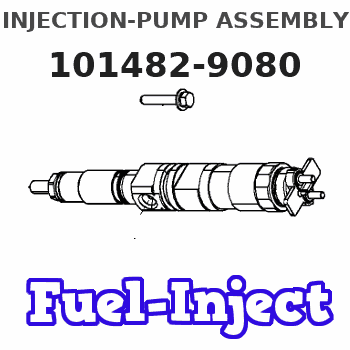
Rating:
Service parts 101482-9080 INJECTION-PUMP ASSEMBLY:
1.
_
5.
AUTOM. ADVANCE MECHANIS
6.
COUPLING PLATE
7.
COUPLING PLATE
8.
_
9.
_
11.
Nozzle and Holder
1660054T01
12.
Open Pre:MPa(Kqf/cm2)
18.1(185)
15.
NOZZLE SET
Cross reference number
ZEXEL
101482-9080
1014829080
Zexel num
Bosch num
Firm num
Name
101482-9080
INJECTION-PUMP ASSEMBLY
Calibration Data:
Adjustment conditions
Test oil
1404 Test oil ISO4113 or {SAEJ967d}
1404 Test oil ISO4113 or {SAEJ967d}
Test oil temperature
degC
40
40
45
Nozzle and nozzle holder
105780-8140
Bosch type code
EF8511/9A
Nozzle
105780-0000
Bosch type code
DN12SD12T
Nozzle holder
105780-2080
Bosch type code
EF8511/9
Opening pressure
MPa
17.2
Opening pressure
kgf/cm2
175
Injection pipe
Outer diameter - inner diameter - length (mm) mm 6-2-600
Outer diameter - inner diameter - length (mm) mm 6-2-600
Overflow valve
132424-0620
Overflow valve opening pressure
kPa
157
123
191
Overflow valve opening pressure
kgf/cm2
1.6
1.25
1.95
Tester oil delivery pressure
kPa
157
157
157
Tester oil delivery pressure
kgf/cm2
1.6
1.6
1.6
Direction of rotation (viewed from drive side)
Right R
Right R
Injection timing adjustment
Direction of rotation (viewed from drive side)
Right R
Right R
Injection order
1-3-4-2
Pre-stroke
mm
3.2
3.15
3.25
Beginning of injection position
Drive side NO.1
Drive side NO.1
Difference between angles 1
Cal 1-3 deg. 90 89.5 90.5
Cal 1-3 deg. 90 89.5 90.5
Difference between angles 2
Cal 1-4 deg. 180 179.5 180.5
Cal 1-4 deg. 180 179.5 180.5
Difference between angles 3
Cyl.1-2 deg. 270 269.5 270.5
Cyl.1-2 deg. 270 269.5 270.5
Injection quantity adjustment
Adjusting point
A
Rack position
10.7
Pump speed
r/min
1200
1200
1200
Average injection quantity
mm3/st.
59.9
58.9
60.9
Max. variation between cylinders
%
0
-3.5
3.5
Basic
*
Fixing the lever
*
Injection quantity adjustment_02
Adjusting point
-
Rack position
9.2+-0.5
Pump speed
r/min
450
450
450
Average injection quantity
mm3/st.
8
6
10
Max. variation between cylinders
%
0
-10
10
Fixing the rack
*
Remarks
Adjust only variation between cylinders; adjust governor according to governor specifications.
Adjust only variation between cylinders; adjust governor according to governor specifications.
Injection quantity adjustment_03
Adjusting point
D
Rack position
-
Pump speed
r/min
100
100
100
Average injection quantity
mm3/st.
62
62
72
Fixing the lever
*
Rack limit
*
Test data Ex:
Governor adjustment

N:Pump speed
R:Rack position (mm)
(1)Target notch: K
(2)RACK LIMIT
(3)Set idle sub-spring
(4)Main spring setting
----------
K=13
----------
----------
K=13
----------
Speed control lever angle
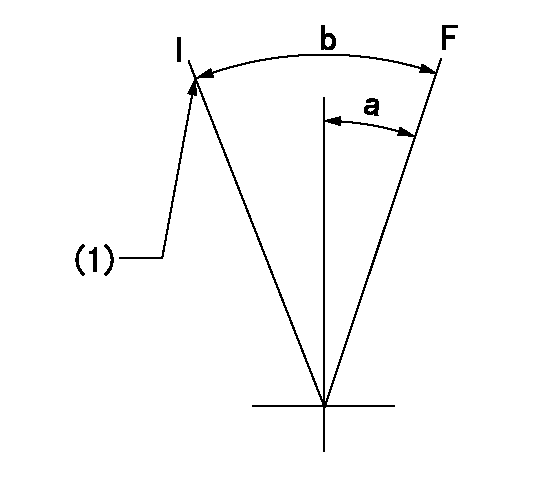
F:Full speed
I:Idle
(1)Stopper bolt setting
----------
----------
a=10deg+-5deg b=19deg+-5deg
----------
----------
a=10deg+-5deg b=19deg+-5deg
Stop lever angle
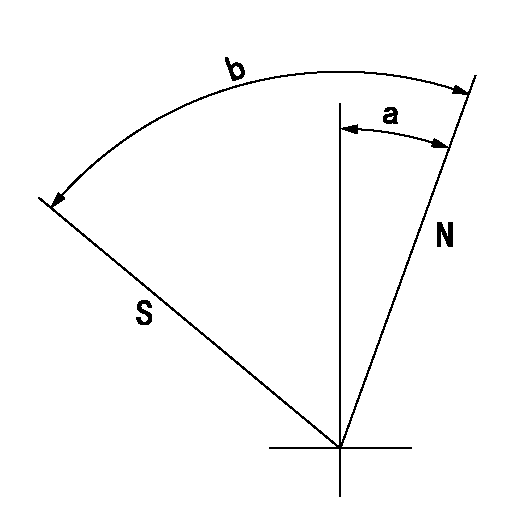
N:Pump normal
S:Stop the pump.
----------
----------
a=12deg+-5deg b=53deg+-5deg
----------
----------
a=12deg+-5deg b=53deg+-5deg
Timing setting
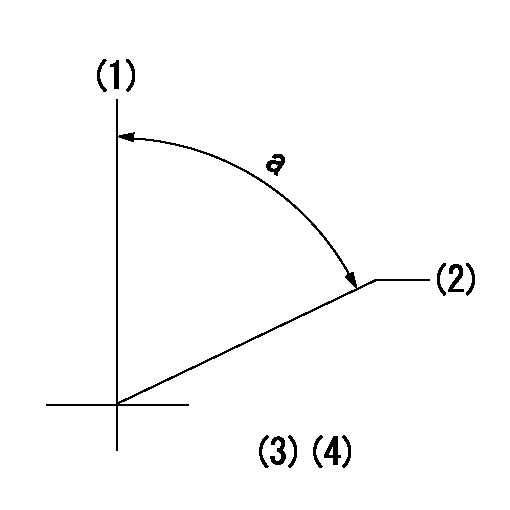
(1)Pump vertical direction
(2)Position of camshaft's key groove at No 1 cylinder's beginning of injection
(3)-
(4)-
----------
----------
a=(60deg)
----------
----------
a=(60deg)
Information:
1. Overview of Radiator-Equipped Engine's Cooling System
Flow of coolant2. Water Pump
2.1 Removal and Inspection
Removal sequence and points to check on water pump1 Cooling fan2 Water pump pulley3 Fan belt4 Water bypass hose5 Water pump assembly KEY POINTS FOR REMOVALRemoval of the water pump pulley and fan belt is possible after loosening slightly both the nut (1) on the alternator support bolt and the adjusting bolt (2). This allows the alternator to be moved and then the V-belt slackened.
Removing water pump pulley KEY POINTS FOR INSPECTIONTurn the pump by hand to check the impeller and shaft for smooth and quiet rotation. If irregular or noisy rotation is detected, replace them as an assembly.
Inspecting impeller and shaft rotation2.2 Installation
Correct locations of water pump mounting bolts KEY POINTS FOR INSPECTION(1) Install the six water pump mounting bolts in their correct locations by referring to the figure on the right for the nominal diameters and lengths from bottom of head.(2) Use a new gasket when installing the water pump.(3) Adjust the fan belt tension according to the following specification.
Fan belt tension adjustment
Unit: mm (in.)3. Thermostat
3.1 Disassembly
Removal sequence and points to check on thermostat1 Water outlet fitting2 Thermostat3 Thermostat fitting4 Water joint5 Temperature joint6 Thermounit3.2 Inspection KEY POINTS FOR INSPECTION(1) Operation Test of ThermostatPut the thermostat in a container of water. Heat the water and record both of the temperatures at which the valve starts to open and at which the valve lift reaches 8 mm (0.3 in.). If the readings do not conform to the specification below, replace the thermostat.
Carry out this operation with extreme care to avoid burns and prevent fire.
Operation test of thermostat(2) Thermounit InspectionPlace the temperature sensing section of the thermounit in a container of oil. Heat the oil to a temperature in each of the ranges shown below and measure the resistance between the terminal and body for each of the temperature. If the resistances are largely different from those specified below, replace the thermounit.
Unit: Ohms
Carry out this operation with extreme care to avoid burns and prevent fire.
Thermounit inspection3.3 InstallationExcept that the instructions shown below are to be followed, perform installation by following the removal sequence in reverse. KEY POINTS FOR INSTALLATION(1) Temperature jointApply sealant to the threads and tighten to the specified torque. (2) ThermostatMake sure that the thermostat flange is correctly fit into the counterbore in the intake manifold.
Installing temperature joint
Installing thermostat
Flow of coolant2. Water Pump
2.1 Removal and Inspection
Removal sequence and points to check on water pump1 Cooling fan2 Water pump pulley3 Fan belt4 Water bypass hose5 Water pump assembly KEY POINTS FOR REMOVALRemoval of the water pump pulley and fan belt is possible after loosening slightly both the nut (1) on the alternator support bolt and the adjusting bolt (2). This allows the alternator to be moved and then the V-belt slackened.
Removing water pump pulley KEY POINTS FOR INSPECTIONTurn the pump by hand to check the impeller and shaft for smooth and quiet rotation. If irregular or noisy rotation is detected, replace them as an assembly.
Inspecting impeller and shaft rotation2.2 Installation
Correct locations of water pump mounting bolts KEY POINTS FOR INSPECTION(1) Install the six water pump mounting bolts in their correct locations by referring to the figure on the right for the nominal diameters and lengths from bottom of head.(2) Use a new gasket when installing the water pump.(3) Adjust the fan belt tension according to the following specification.
Fan belt tension adjustment
Unit: mm (in.)3. Thermostat
3.1 Disassembly
Removal sequence and points to check on thermostat1 Water outlet fitting2 Thermostat3 Thermostat fitting4 Water joint5 Temperature joint6 Thermounit3.2 Inspection KEY POINTS FOR INSPECTION(1) Operation Test of ThermostatPut the thermostat in a container of water. Heat the water and record both of the temperatures at which the valve starts to open and at which the valve lift reaches 8 mm (0.3 in.). If the readings do not conform to the specification below, replace the thermostat.
Carry out this operation with extreme care to avoid burns and prevent fire.
Operation test of thermostat(2) Thermounit InspectionPlace the temperature sensing section of the thermounit in a container of oil. Heat the oil to a temperature in each of the ranges shown below and measure the resistance between the terminal and body for each of the temperature. If the resistances are largely different from those specified below, replace the thermounit.
Unit: Ohms
Carry out this operation with extreme care to avoid burns and prevent fire.
Thermounit inspection3.3 InstallationExcept that the instructions shown below are to be followed, perform installation by following the removal sequence in reverse. KEY POINTS FOR INSTALLATION(1) Temperature jointApply sealant to the threads and tighten to the specified torque. (2) ThermostatMake sure that the thermostat flange is correctly fit into the counterbore in the intake manifold.
Installing temperature joint
Installing thermostat
Have questions with 101482-9080?
Group cross 101482-9080 ZEXEL
Daewoo
Nissan-Diesel
Nissan-Diesel
Nissan-Diesel
Nissan-Diesel
101482-9080
INJECTION-PUMP ASSEMBLY