Information injection-pump assembly
BOSCH
9 400 614 255
9400614255
ZEXEL
101482-4510
1014824510
ISUZU
8970885990
8970885990
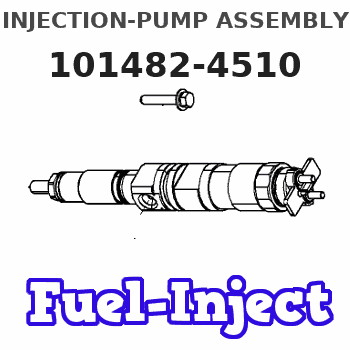
Rating:
Service parts 101482-4510 INJECTION-PUMP ASSEMBLY:
1.
_
5.
AUTOM. ADVANCE MECHANIS
6.
COUPLING PLATE
8.
_
9.
_
11.
Nozzle and Holder
8-94122-262-5
12.
Open Pre:MPa(Kqf/cm2)
18.1{185}
15.
NOZZLE SET
Cross reference number
BOSCH
9 400 614 255
9400614255
ZEXEL
101482-4510
1014824510
ISUZU
8970885990
8970885990
Zexel num
Bosch num
Firm num
Name
101482-4510
9 400 614 255
8970885990 ISUZU
INJECTION-PUMP ASSEMBLY
4JB1 * K 14BC INJECTION PUMP ASSY PE4A,5A, PE
4JB1 * K 14BC INJECTION PUMP ASSY PE4A,5A, PE
Calibration Data:
Adjustment conditions
Test oil
1404 Test oil ISO4113 or {SAEJ967d}
1404 Test oil ISO4113 or {SAEJ967d}
Test oil temperature
degC
40
40
45
Nozzle and nozzle holder
105780-8140
Bosch type code
EF8511/9A
Nozzle
105780-0000
Bosch type code
DN12SD12T
Nozzle holder
105780-2080
Bosch type code
EF8511/9
Opening pressure
MPa
17.2
Opening pressure
kgf/cm2
175
Injection pipe
Outer diameter - inner diameter - length (mm) mm 6-2-600
Outer diameter - inner diameter - length (mm) mm 6-2-600
Tester oil delivery pressure
kPa
157
157
157
Tester oil delivery pressure
kgf/cm2
1.6
1.6
1.6
Direction of rotation (viewed from drive side)
Left L
Left L
Injection timing adjustment
Direction of rotation (viewed from drive side)
Left L
Left L
Injection order
1-3-4-2
Pre-stroke
mm
3.3
3.25
3.35
Beginning of injection position
Drive side NO.1
Drive side NO.1
Difference between angles 1
Cal 1-3 deg. 90 89.5 90.5
Cal 1-3 deg. 90 89.5 90.5
Difference between angles 2
Cal 1-4 deg. 180 179.5 180.5
Cal 1-4 deg. 180 179.5 180.5
Difference between angles 3
Cyl.1-2 deg. 270 269.5 270.5
Cyl.1-2 deg. 270 269.5 270.5
Injection quantity adjustment
Adjusting point
A
Rack position
9.8
Pump speed
r/min
1500
1500
1500
Average injection quantity
mm3/st.
49.7
48.7
50.7
Max. variation between cylinders
%
0
-2.5
2.5
Basic
*
Fixing the lever
*
Injection quantity adjustment_02
Adjusting point
B
Rack position
7.6+-0.5
Pump speed
r/min
300
300
300
Average injection quantity
mm3/st.
8
6
10
Max. variation between cylinders
%
0
-15
15
Fixing the rack
*
Test data Ex:
Governor adjustment
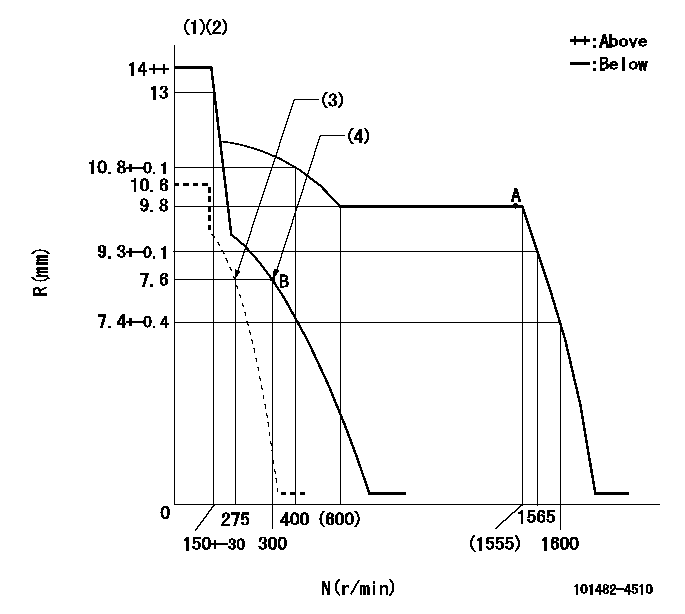
N:Pump speed
R:Rack position (mm)
(1)Target notch: K
(2)Tolerance for racks not indicated: +-0.05mm.
(3)Set idle sub-spring
(4)Main spring setting
----------
K=7
----------
----------
K=7
----------
Speed control lever angle

F:Full speed
I:Idle
S:Stop
----------
----------
a=11deg+-5deg b=29deg+-5deg c=35deg+-3deg
----------
----------
a=11deg+-5deg b=29deg+-5deg c=35deg+-3deg
Stop lever angle

N:Pump normal
S:Stop the pump.
----------
----------
a=22.5deg+-5deg b=53deg+-5deg
----------
----------
a=22.5deg+-5deg b=53deg+-5deg
Timing setting

(1)Pump vertical direction
(2)Position of gear mark 'V' at No 1 cylinder's beginning of injection
(3)B.T.D.C.: aa
(4)-
----------
aa=20deg
----------
a=(200deg)
----------
aa=20deg
----------
a=(200deg)
Information:
The front plate is bolted inside the timing gear case. Do not attempt to remove this plate along with the timing gear case by tapping.
Front plate attaching bolts8. Timing gear backlash measurement Measure the backlash of each gear and keep a record of it for correct installation. Replace the gears if the backlash exceeds the limit.
Unit: mm (in.)
Measuring timing gear backlash9. Idler gear removal To remove the idler gear, rotate the gear in a direction of the helix of the teeth to pull it out of mesh.
Removing idler gear10. Camshaft removal (1) Remove the bolts that hold the thrust plate. (2) Pull the camshaft out of the cylinder block.
Do not cause damage to the lobes or bearing journals when removing the camshaft.
Removing camshaft11. Fuel injection pump camshaft removal(1) Remove the stopper bolt.
Removing camshaft stopper bolt(2) Tap the rear end of the camshaft with a copper bar to push it out of the front side of the cylinder block.
Removing fuel injection pump camshaft12. Gear removal (when required) To remove the gears from the camshaft and fuel injection pump camshaft, use an arbor press.13. Oil pump removal Remove the bolts that hold the oil pump to the cylinder block and remove the pump.
Removing oil pump14. Front plate removal Remove four bolts that hold the front plate in position. Tap the plate lightly with a plastic hammer to separate the gasket.
Removing front plateCYLINDER BLOCK, CRANKSHAFT, PISTONS AND OIL PAN
1 Oil pan2 Oil screen3 Connecting rod cap4 Connecting rod bearing (lower half) (Remove 5 thru 10 as an assembly.)5 Connecting rod6 Piston pin7 No. 1 ring8 No. 2 ring9 Oil ring10 Piston11 Connecting rod bearing (upper half)12 Main bearing cap13 Main bearing (lower half)14 Crankshaft15 Main bearing (upper half)16 Cylinder block When the cylinder block is to be discarded, remove the components (pressure relief valve, etc.) from the block for reuse. 1. Oil pan removal (1) Turn the engine upside down.(2) Tap the bottom corners of the oil pan with a plastic hammer to remove the oil pan.
Do not attempt to pry off the oil pan by inserting a screwdriver or a chisel between the oil pan and cylinder block. Damage to the oil pan can be the result.
Removing oil pan2. Oil screen removal Loosen the nut that holds the oil screen in position and remove the screen.
Removing oil screen3. Thrust clearance measurement for connecting rod big endInstall the connecting rod to its crankpin and tighten the cap nuts to the specified torque. Measure the thrust clearance with a feeler gauge. If the clearance exceeds the limit, replace the connecting rod.
Measuring thrust clearance for connecting rod big end
Unit: mm (in.)4. Connecting rod cap removal (1) Lay the cylinder block on its side.(2) Put identification on each connecting rod and cap combination as to its location in the engine.(3) Remove the caps.
Removing connecting rod caps5. Piston removal (1) Turn the crankshaft until the piston is at top center. (2) Push the piston and connecting rod away from the crankshaft with the handle of
Front plate attaching bolts8. Timing gear backlash measurement Measure the backlash of each gear and keep a record of it for correct installation. Replace the gears if the backlash exceeds the limit.
Unit: mm (in.)
Measuring timing gear backlash9. Idler gear removal To remove the idler gear, rotate the gear in a direction of the helix of the teeth to pull it out of mesh.
Removing idler gear10. Camshaft removal (1) Remove the bolts that hold the thrust plate. (2) Pull the camshaft out of the cylinder block.
Do not cause damage to the lobes or bearing journals when removing the camshaft.
Removing camshaft11. Fuel injection pump camshaft removal(1) Remove the stopper bolt.
Removing camshaft stopper bolt(2) Tap the rear end of the camshaft with a copper bar to push it out of the front side of the cylinder block.
Removing fuel injection pump camshaft12. Gear removal (when required) To remove the gears from the camshaft and fuel injection pump camshaft, use an arbor press.13. Oil pump removal Remove the bolts that hold the oil pump to the cylinder block and remove the pump.
Removing oil pump14. Front plate removal Remove four bolts that hold the front plate in position. Tap the plate lightly with a plastic hammer to separate the gasket.
Removing front plateCYLINDER BLOCK, CRANKSHAFT, PISTONS AND OIL PAN
1 Oil pan2 Oil screen3 Connecting rod cap4 Connecting rod bearing (lower half) (Remove 5 thru 10 as an assembly.)5 Connecting rod6 Piston pin7 No. 1 ring8 No. 2 ring9 Oil ring10 Piston11 Connecting rod bearing (upper half)12 Main bearing cap13 Main bearing (lower half)14 Crankshaft15 Main bearing (upper half)16 Cylinder block When the cylinder block is to be discarded, remove the components (pressure relief valve, etc.) from the block for reuse. 1. Oil pan removal (1) Turn the engine upside down.(2) Tap the bottom corners of the oil pan with a plastic hammer to remove the oil pan.
Do not attempt to pry off the oil pan by inserting a screwdriver or a chisel between the oil pan and cylinder block. Damage to the oil pan can be the result.
Removing oil pan2. Oil screen removal Loosen the nut that holds the oil screen in position and remove the screen.
Removing oil screen3. Thrust clearance measurement for connecting rod big endInstall the connecting rod to its crankpin and tighten the cap nuts to the specified torque. Measure the thrust clearance with a feeler gauge. If the clearance exceeds the limit, replace the connecting rod.
Measuring thrust clearance for connecting rod big end
Unit: mm (in.)4. Connecting rod cap removal (1) Lay the cylinder block on its side.(2) Put identification on each connecting rod and cap combination as to its location in the engine.(3) Remove the caps.
Removing connecting rod caps5. Piston removal (1) Turn the crankshaft until the piston is at top center. (2) Push the piston and connecting rod away from the crankshaft with the handle of
Have questions with 101482-4510?
Group cross 101482-4510 ZEXEL
Isuzu
101482-4510
9 400 614 255
8970885990
INJECTION-PUMP ASSEMBLY
4JB1
4JB1