Information injection-pump assembly
ZEXEL
101481-0152
1014810152
ISUZU
8970106482
8970106482
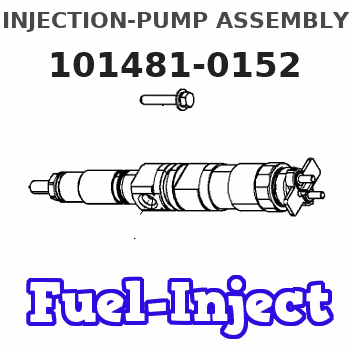
Rating:
Cross reference number
ZEXEL
101481-0152
1014810152
ISUZU
8970106482
8970106482
Zexel num
Bosch num
Firm num
Name
Calibration Data:
Adjustment conditions
Test oil
1404 Test oil ISO4113 or {SAEJ967d}
1404 Test oil ISO4113 or {SAEJ967d}
Test oil temperature
degC
40
40
45
Nozzle and nozzle holder
105780-8140
Bosch type code
EF8511/9A
Nozzle
105780-0000
Bosch type code
DN12SD12T
Nozzle holder
105780-2080
Bosch type code
EF8511/9
Opening pressure
MPa
17.2
Opening pressure
kgf/cm2
175
Injection pipe
Outer diameter - inner diameter - length (mm) mm 6-2-600
Outer diameter - inner diameter - length (mm) mm 6-2-600
Overflow valve
131424-4920
Overflow valve opening pressure
kPa
127
107
147
Overflow valve opening pressure
kgf/cm2
1.3
1.1
1.5
Tester oil delivery pressure
kPa
157
157
157
Tester oil delivery pressure
kgf/cm2
1.6
1.6
1.6
Direction of rotation (viewed from drive side)
Right R
Right R
Injection timing adjustment
Direction of rotation (viewed from drive side)
Right R
Right R
Injection order
1-3-4-2
Pre-stroke
mm
2.8
2.75
2.85
Rack position
Point A R=A
Point A R=A
Beginning of injection position
Drive side NO.1
Drive side NO.1
Difference between angles 1
Cal 1-3 deg. 90 89.5 90.5
Cal 1-3 deg. 90 89.5 90.5
Difference between angles 2
Cal 1-4 deg. 180 179.5 180.5
Cal 1-4 deg. 180 179.5 180.5
Difference between angles 3
Cyl.1-2 deg. 270 269.5 270.5
Cyl.1-2 deg. 270 269.5 270.5
Injection quantity adjustment
Adjusting point
-
Rack position
12.1
Pump speed
r/min
950
950
950
Average injection quantity
mm3/st.
76.8
75.2
78.4
Max. variation between cylinders
%
0
-4
4
Basic
*
Fixing the rack
*
Standard for adjustment of the maximum variation between cylinders
*
Injection quantity adjustment_02
Adjusting point
H
Rack position
9.5+-0.5
Pump speed
r/min
365
365
365
Average injection quantity
mm3/st.
9
7.7
10.3
Max. variation between cylinders
%
0
-14
14
Fixing the rack
*
Standard for adjustment of the maximum variation between cylinders
*
Injection quantity adjustment_03
Adjusting point
A
Rack position
R1(12.1)
Pump speed
r/min
950
950
950
Average injection quantity
mm3/st.
76.8
75.8
77.8
Basic
*
Fixing the lever
*
Boost pressure
kPa
24
24
Boost pressure
mmHg
180
180
Injection quantity adjustment_04
Adjusting point
B
Rack position
R1-0.5
Pump speed
r/min
1500
1500
1500
Average injection quantity
mm3/st.
72.4
68.4
76.4
Fixing the lever
*
Boost pressure
kPa
24
24
Boost pressure
mmHg
180
180
Injection quantity adjustment_05
Adjusting point
C
Rack position
R2(R1-0.
15)
Pump speed
r/min
650
650
650
Average injection quantity
mm3/st.
67.5
63.5
71.5
Fixing the lever
*
Boost pressure
kPa
24
24
Boost pressure
mmHg
180
180
Injection quantity adjustment_06
Adjusting point
D
Rack position
R2-0.3
Pump speed
r/min
650
650
650
Average injection quantity
mm3/st.
60.8
56.8
64.8
Fixing the lever
*
Boost pressure
kPa
0
0
0
Boost pressure
mmHg
0
0
0
Injection quantity adjustment_07
Adjusting point
I
Rack position
-
Pump speed
r/min
150
150
150
Average injection quantity
mm3/st.
93
93
109
Fixing the lever
*
Boost pressure
kPa
0
0
0
Boost pressure
mmHg
0
0
0
Boost compensator adjustment
Pump speed
r/min
650
650
650
Rack position
R2-0.3
Boost pressure
kPa
6.7
6.7
9.4
Boost pressure
mmHg
50
50
70
Boost compensator adjustment_02
Pump speed
r/min
650
650
650
Rack position
R2(R1-0.
15)
Boost pressure
kPa
10.7
10.7
10.7
Boost pressure
mmHg
80
80
80
Timer adjustment
Pump speed
r/min
550--
Advance angle
deg.
0
0
0
Remarks
Start
Start
Timer adjustment_02
Pump speed
r/min
500
Advance angle
deg.
0.5
Timer adjustment_03
Pump speed
r/min
1500
Advance angle
deg.
3.9
3.4
4.4
Remarks
Finish
Finish
Test data Ex:
Governor adjustment
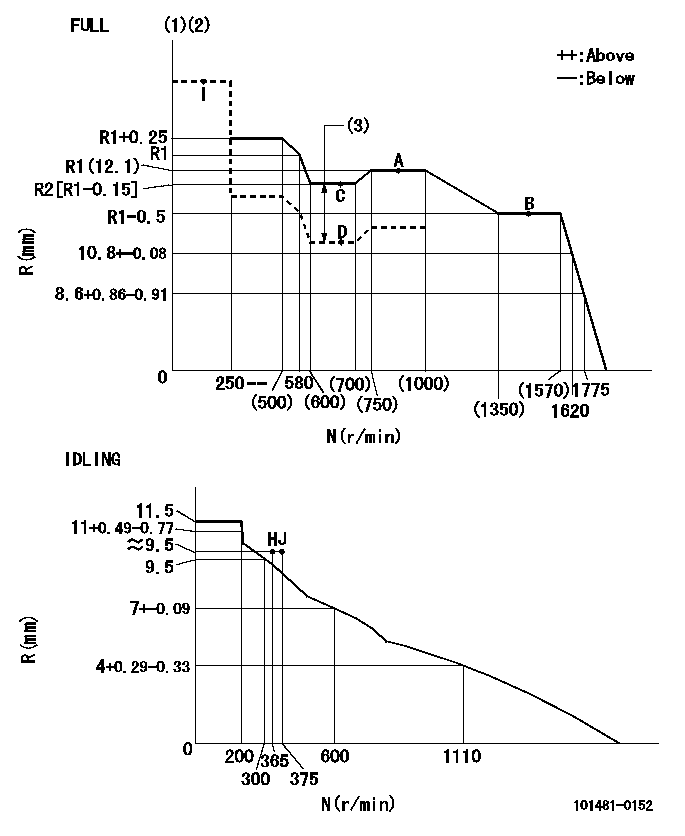
N:Pump speed
R:Rack position (mm)
(1)Torque cam stamping: T1
(2)Tolerance for racks not indicated: +-0.05mm.
(3)Boost compensator stroke: BCL
----------
T1=F86 BCL=0.3+-0.1mm
----------
----------
T1=F86 BCL=0.3+-0.1mm
----------
Speed control lever angle
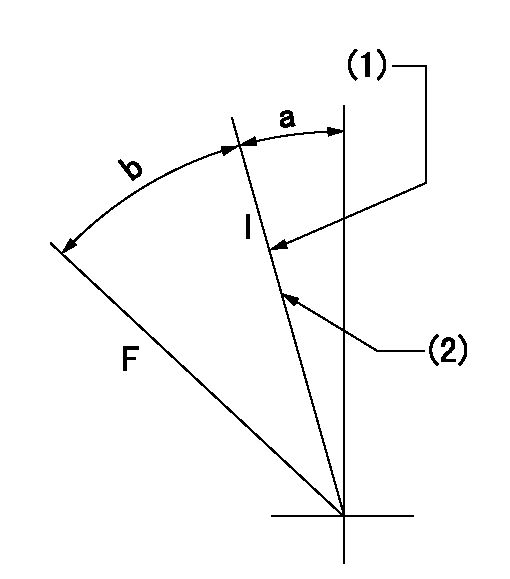
F:Full speed
I:Idle
(1)Stopper bolt setting
(2)At M/S adjustment, confirm that M/S turns ON when speed lever is returned from full to idle and gap between speed lever and idle side stopper bolt is aa. Confirm that M/S turns OFF when speed lever is again returned from full to idle at gap bb.
----------
aa=0.1mm bb=0.25mm
----------
a=6.5deg+-5deg b=32deg+-3deg
----------
aa=0.1mm bb=0.25mm
----------
a=6.5deg+-5deg b=32deg+-3deg
Stop lever angle
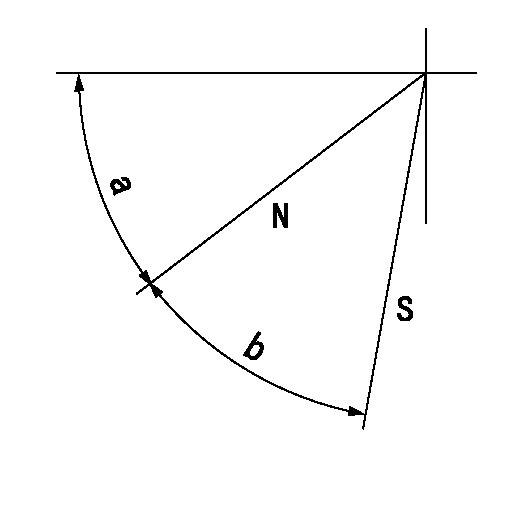
N:Pump normal
S:Stop the pump.
----------
----------
a=45deg+-5deg b=29deg+-5deg
----------
----------
a=45deg+-5deg b=29deg+-5deg
0000001501 ACS
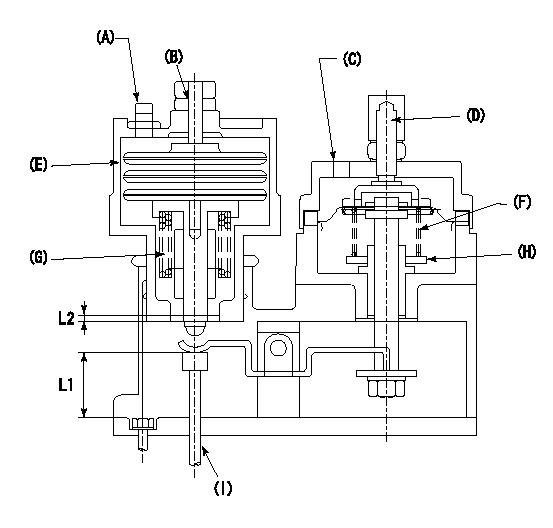
(A) Aneroid compensator
(B) Set screw
(C) Boost pressure inlet
(D) Rack positioning screw
(E): Aneroid compensator main body
(F) Boost compensator spring
(G): Aneroid compensator spring
(H): Adjusting notch
(I) Push rod
1. Instructions for adjusting the boost compensator with the aneroid compensator
(1)Select a pushrod to obtain L1 at full boost.
(2)Remove the aneroid compensator main body.
(3)Adjust the booster compensator stroke by turning the screw at (D.
(4)Adjust the beginning of boost compensator operation by turning the notch at (H).
(5)Install the aneroid compensator at full boost state.
(6)Turn (B)'s set screw so that the distance between the snapring and the body is L2.
(7)Screw in the aneroid compensator main body and adjust the point where it comes into play.
----------
L1=24+-0.5mm L2=1.5+-0.5mm
----------
----------
L1=24+-0.5mm L2=1.5+-0.5mm
----------
0000001601 ACS
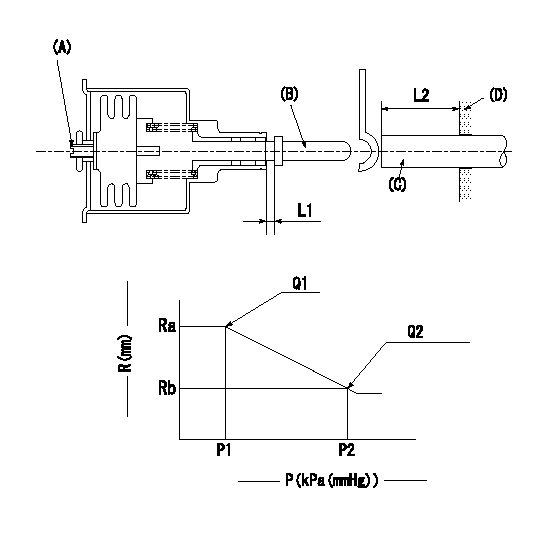
(A) Set screw
(B) Push rod 1
(C) Push rod 2
1. Adjustment of the aneroid compensator itself and the adjustment after mounting the governor
(1)Set the speed of the pump to N1 r/min and fix the control lever at the full set position.
(2)Screw in (A) to obtain the performance shown in the graph (to obtain L1).
(3)Adjust the (D) spacer so that dimension L2 is obtained.
(4)As there is hysterisis, measure when the absolute pressure drops.
(5)Hysterisis must not exceed rack position = h1.
----------
N1=950r/min L1=1.5+-0.5mm L2=24+-0.5mm h1=0.15mm
----------
Ra=R1(12.1)mm Rb=R1-0.25mm P1=74.6+-2.7kPa(560+-20mmHg) P2=61.6+-0.7kPa(462+-5mmHg) Q1=76.8+-1cm3/1000st Q2=(70.7)+-2cm3/1000st
----------
N1=950r/min L1=1.5+-0.5mm L2=24+-0.5mm h1=0.15mm
----------
Ra=R1(12.1)mm Rb=R1-0.25mm P1=74.6+-2.7kPa(560+-20mmHg) P2=61.6+-0.7kPa(462+-5mmHg) Q1=76.8+-1cm3/1000st Q2=(70.7)+-2cm3/1000st
0000001701 FICD
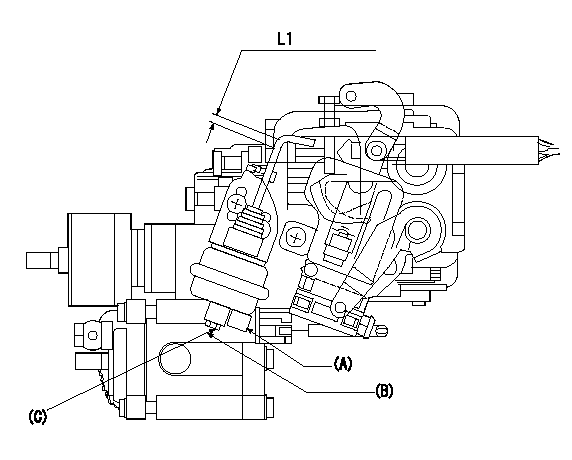
(a) actuator
(B) Screw
(c) Nut
1. FICD adjustment
(1)Set the clearance between the actuator rod and speed lever to approx. L1.
(2)Loosen nut (C) and fully screw in the actuator (A)'s screw (B).
(3)Apply negative pressure P1 to the actuator (A) and fully screw in screw (B).
(4)Set the pump speed at N1
(5)Set the rack position at R1.
(6)Tighten the actuator (A)'s screw (B) and fix using the nut (C).
(7)Apply P2 to negative pressure port A and confirm that the FICD operates normally.
----------
L1=(3)mm P1=53.3kPa(400mmHg) P2=53.3kPa(400mmHg) N1=450r/min R1=9.3+-0.1mm
----------
----------
L1=(3)mm P1=53.3kPa(400mmHg) P2=53.3kPa(400mmHg) N1=450r/min R1=9.3+-0.1mm
----------
Timing setting

(1)Pump vertical direction
(2)Position of gear mark 'CC' at No 1 cylinder's beginning of injection
(3)B.T.D.C.: aa
(4)-
----------
aa=8deg
----------
a=(100deg)
----------
aa=8deg
----------
a=(100deg)
Information:
Do not operate or work on this product unless you have read and understood the instruction and warnings in the relevant Operation and Maintenance Manuals and relevant service literature. Failure to follow the instructions or heed the warnings could result in injury or death. Proper care is your responsibility.
Table 1
Existing Part Number New Part Number Description
459-7216 471-6029 DEF Injector & Mounting Gp
540-0883 554-8955 24V DEF Pump Software
481-5823 554-8956 12V DEF Pump Software Refer to Disassembly and Assembly, DEF Injector and Mounting - Remove and Install for the correct procedure to install the new DEF injector.Refer to Troubleshooting, ECM Software - Install for the correct procedure to install the new software.