Information injection-pump assembly
ZEXEL
101472-3570
1014723570
KOMATSU
6144711121
6144711121
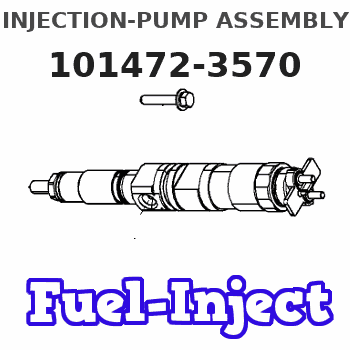
Rating:
Service parts 101472-3570 INJECTION-PUMP ASSEMBLY:
1.
_
5.
AUTOM. ADVANCE MECHANIS
6.
COUPLING PLATE
7.
COUPLING PLATE
8.
_
9.
_
11.
Nozzle and Holder
6142-12-3300
12.
Open Pre:MPa(Kqf/cm2)
11.8{120}
15.
NOZZLE SET
Cross reference number
ZEXEL
101472-3570
1014723570
KOMATSU
6144711121
6144711121
Zexel num
Bosch num
Firm num
Name
Calibration Data:
Adjustment conditions
Test oil
1404 Test oil ISO4113 or {SAEJ967d}
1404 Test oil ISO4113 or {SAEJ967d}
Test oil temperature
degC
40
40
45
Nozzle and nozzle holder
105780-8140
Bosch type code
EF8511/9A
Nozzle
105780-0000
Bosch type code
DN12SD12T
Nozzle holder
105780-2080
Bosch type code
EF8511/9
Opening pressure
MPa
17.2
Opening pressure
kgf/cm2
175
Injection pipe
Outer diameter - inner diameter - length (mm) mm 6-2-600
Outer diameter - inner diameter - length (mm) mm 6-2-600
Tester oil delivery pressure
kPa
157
157
157
Tester oil delivery pressure
kgf/cm2
1.6
1.6
1.6
Direction of rotation (viewed from drive side)
Right R
Right R
Injection timing adjustment
Direction of rotation (viewed from drive side)
Right R
Right R
Injection order
1-2-4-3
Pre-stroke
mm
2.2
2.15
2.25
Beginning of injection position
Drive side NO.1
Drive side NO.1
Difference between angles 1
Cyl.1-2 deg. 90 89.5 90.5
Cyl.1-2 deg. 90 89.5 90.5
Difference between angles 2
Cal 1-4 deg. 180 179.5 180.5
Cal 1-4 deg. 180 179.5 180.5
Difference between angles 3
Cal 1-3 deg. 270 269.5 270.5
Cal 1-3 deg. 270 269.5 270.5
Injection quantity adjustment
Adjusting point
A
Rack position
9.2
Pump speed
r/min
1200
1200
1200
Average injection quantity
mm3/st.
44.3
43.3
45.3
Max. variation between cylinders
%
0
-2
2
Basic
*
Fixing the rack
*
Injection quantity adjustment_02
Adjusting point
C
Rack position
7.2+-0.5
Pump speed
r/min
350
350
350
Average injection quantity
mm3/st.
9
8.2
9.8
Max. variation between cylinders
%
0
-15
15
Fixing the rack
*
Remarks
Adjust only variation between cylinders; adjust governor according to governor specifications.
Adjust only variation between cylinders; adjust governor according to governor specifications.
Test data Ex:
Governor adjustment
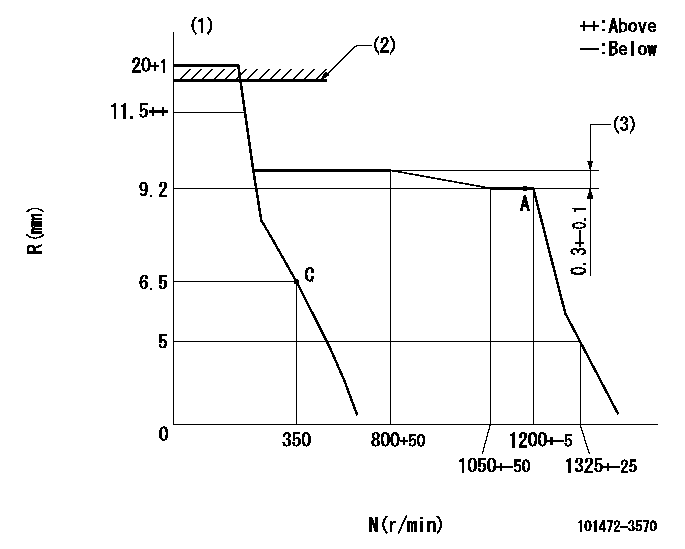
N:Pump speed
R:Rack position (mm)
(1)Target notch: K
(2)RACK CAP: R1
(3)Rack difference between N = N1 and N = N2
----------
K=11 R1=18+1mm N1=1200r/min N2=800r/min
----------
----------
K=11 R1=18+1mm N1=1200r/min N2=800r/min
----------
Speed control lever angle
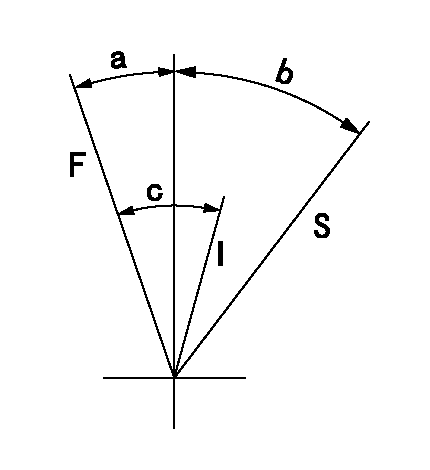
F:Full speed
I:Idle
S:Stop
----------
----------
a=14deg+-5deg b=32deg+-3deg c=22deg+-5deg
----------
----------
a=14deg+-5deg b=32deg+-3deg c=22deg+-5deg
0000001501 LEVER
(F) P/N: Part number of the shim
L1:Thickness (mm)
1. Adjustment of the control lever
(1)Perform idling with the control lever (A) contacting the pushrod (B). At this time, confirm that the spring (C) is not compressed by control lever (A)'s operating torque.
(2)To set the stop position, compress spring (C) using the control lever (A) and adjust the rack so that it contacts the guide screw (D) at position L2. Then, set and fix using the lock nut (E). Adjust the rack position L2 at this time using the shim (F).
(3)Confirm that the control lever (A) returns to the idling position when pulled in the stop direction and then released.
----------
L2=0.2~2mm
----------
----------
L2=0.2~2mm
----------
Information:
Introduction
The problem that is identified below does not have a known permanent solution. Until a permanent solution is known, use the solution that is identified below.Problem
There have been some isolated instances of issues with the Diesel Particulate Filter (DPF) on certain C3.4B engines.Solution
Caterpillar is aware of this problem. Follow the procedure that is detailed below.
Table 1
Required Tools
Tool Part Number Part Description Qty
A 233-7191 Hose Cleaner Gp 1
Obtain a fuel sample from the engine.
Obtain a lubricating oil sample from the engine.
Attach a copy of the full service history of the engine to the Service Information Systems (SIMSi) report. Include the change history of the following components:
Engine oil
Engine oil filter
Engine fuel filter
Crankcase breather filter
Ensure that the breather element is clean and free from wear or damage. Replace the breather element. Refer to Operation and Maintenance Manual, Engine Crankcase Breather Element - Replace for the correct procedure. Ensure that the inlet hose is clean and free from restriction. If the inlet hose requires replacing, refer to Disassembly and Assembly, Crankcase Breather - Install for the correct procedure.
Determine the service hours of the engine air cleaner element. Ensure that the engine air cleaner element is clean and free from wear, damage, or restriction. If necessary, replace the engine air cleaner element. Refer to Operation and Maintenance Manual, Engine Air Cleaner Element (Single Element) - Inspect/Clean/Replace for the correct procedure. Ensure that the hose assemblies are clean and free from restriction and dust.
Inspect the inlet and outlet hoses of the turbocharger for the presence of excessive lubricating oil. If necessary, take photographs inside both inlet and outlet hoses. If necessary, take photographs inside the compressor housing for the inlet and outlet. If excessive lubricating oil is found, replace the turbocharger. Refer to Disassembly and Assembly, Turbocharger
The problem that is identified below does not have a known permanent solution. Until a permanent solution is known, use the solution that is identified below.Problem
There have been some isolated instances of issues with the Diesel Particulate Filter (DPF) on certain C3.4B engines.Solution
Caterpillar is aware of this problem. Follow the procedure that is detailed below.
Table 1
Required Tools
Tool Part Number Part Description Qty
A 233-7191 Hose Cleaner Gp 1
Obtain a fuel sample from the engine.
Obtain a lubricating oil sample from the engine.
Attach a copy of the full service history of the engine to the Service Information Systems (SIMSi) report. Include the change history of the following components:
Engine oil
Engine oil filter
Engine fuel filter
Crankcase breather filter
Ensure that the breather element is clean and free from wear or damage. Replace the breather element. Refer to Operation and Maintenance Manual, Engine Crankcase Breather Element - Replace for the correct procedure. Ensure that the inlet hose is clean and free from restriction. If the inlet hose requires replacing, refer to Disassembly and Assembly, Crankcase Breather - Install for the correct procedure.
Determine the service hours of the engine air cleaner element. Ensure that the engine air cleaner element is clean and free from wear, damage, or restriction. If necessary, replace the engine air cleaner element. Refer to Operation and Maintenance Manual, Engine Air Cleaner Element (Single Element) - Inspect/Clean/Replace for the correct procedure. Ensure that the hose assemblies are clean and free from restriction and dust.
Inspect the inlet and outlet hoses of the turbocharger for the presence of excessive lubricating oil. If necessary, take photographs inside both inlet and outlet hoses. If necessary, take photographs inside the compressor housing for the inlet and outlet. If excessive lubricating oil is found, replace the turbocharger. Refer to Disassembly and Assembly, Turbocharger