Information injection-pump assembly
BOSCH
9 400 614 181
9400614181
ZEXEL
101452-3090
1014523090
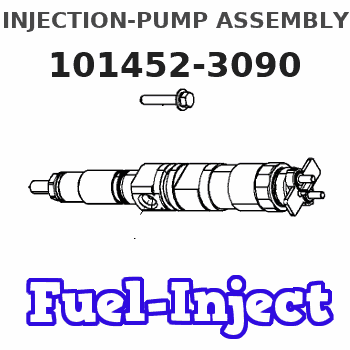
Rating:
Service parts 101452-3090 INJECTION-PUMP ASSEMBLY:
1.
_
5.
AUTOM. ADVANCE MECHANIS
6.
COUPLING PLATE
7.
COUPLING PLATE
8.
_
9.
_
11.
Nozzle and Holder
6202-12-3100
12.
Open Pre:MPa(Kqf/cm2)
11.8{120}
15.
NOZZLE SET
Cross reference number
BOSCH
9 400 614 181
9400614181
ZEXEL
101452-3090
1014523090
Zexel num
Bosch num
Firm num
Name
Calibration Data:
Adjustment conditions
Test oil
1404 Test oil ISO4113 or {SAEJ967d}
1404 Test oil ISO4113 or {SAEJ967d}
Test oil temperature
degC
40
40
45
Nozzle and nozzle holder
105780-8140
Bosch type code
EF8511/9A
Nozzle
105780-0000
Bosch type code
DN12SD12T
Nozzle holder
105780-2080
Bosch type code
EF8511/9
Opening pressure
MPa
17.2
Opening pressure
kgf/cm2
175
Injection pipe
Outer diameter - inner diameter - length (mm) mm 6-2-600
Outer diameter - inner diameter - length (mm) mm 6-2-600
Tester oil delivery pressure
kPa
157
157
157
Tester oil delivery pressure
kgf/cm2
1.6
1.6
1.6
Direction of rotation (viewed from drive side)
Right R
Right R
Injection timing adjustment
Direction of rotation (viewed from drive side)
Right R
Right R
Injection order
1-2-4-3
Pre-stroke
mm
1.5
1.45
1.55
Beginning of injection position
Drive side NO.1
Drive side NO.1
Difference between angles 1
Cyl.1-2 deg. 90 89.5 90.5
Cyl.1-2 deg. 90 89.5 90.5
Difference between angles 2
Cal 1-4 deg. 180 179.5 180.5
Cal 1-4 deg. 180 179.5 180.5
Difference between angles 3
Cal 1-3 deg. 270 269.5 270.5
Cal 1-3 deg. 270 269.5 270.5
Injection quantity adjustment
Adjusting point
A
Rack position
12
Pump speed
r/min
900
900
900
Average injection quantity
mm3/st.
45.8
44.8
46.8
Max. variation between cylinders
%
0
-2.5
2.5
Basic
*
Fixing the lever
*
Injection quantity adjustment_02
Adjusting point
-
Rack position
8.3+-0.5
Pump speed
r/min
400
400
400
Average injection quantity
mm3/st.
11
10
12
Max. variation between cylinders
%
0
-15
15
Fixing the rack
*
Remarks
Adjust only variation between cylinders; adjust governor according to governor specifications.
Adjust only variation between cylinders; adjust governor according to governor specifications.
Test data Ex:
Governor adjustment
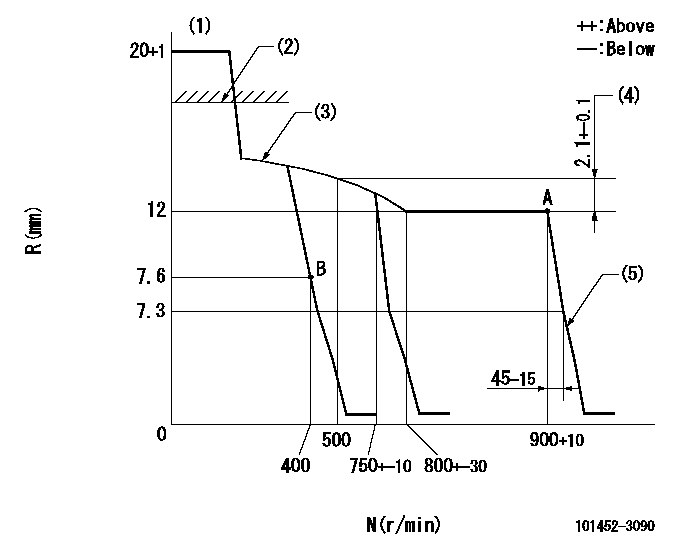
N:Pump speed
R:Rack position (mm)
(1)Target notch: K
(2)RACK CAP: R1
(3)The torque control spring must does not have a set force.
(4)Rack difference between N = N1 and N = N2
(5)Idle sub spring setting: L1.
----------
K=15 R1=(17.5)mm N1=900r/min N2=500r/min L1=7.3-0.5mm
----------
----------
K=15 R1=(17.5)mm N1=900r/min N2=500r/min L1=7.3-0.5mm
----------
Speed control lever angle
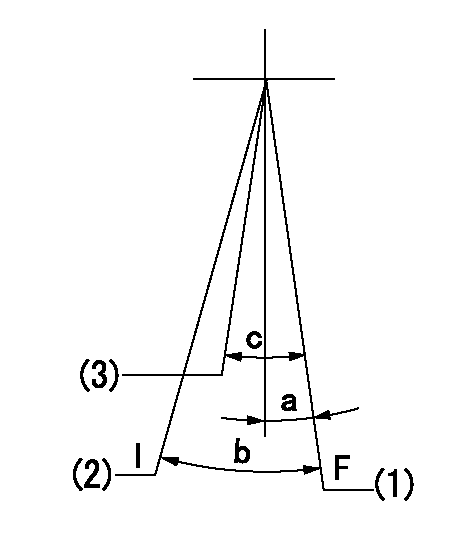
F:Full speed
I:Idle
(1)Set the pump speed at aa. ( At delivery )
(2)Stopper bolt setting
(3)Pump speed = bb
----------
aa=900r/min bb=750r/min
----------
a=2deg+-5deg b=26deg+-5deg c=7deg+-5deg
----------
aa=900r/min bb=750r/min
----------
a=2deg+-5deg b=26deg+-5deg c=7deg+-5deg
Stop lever angle
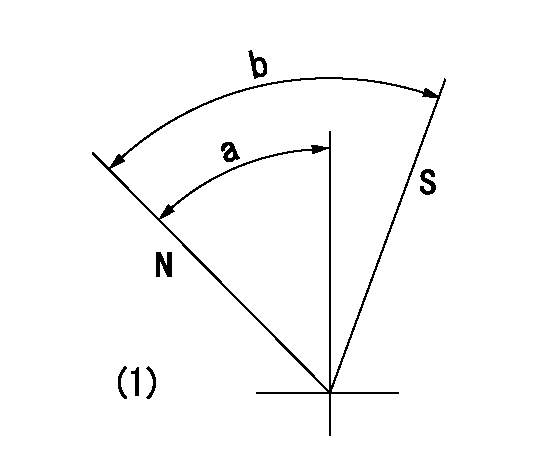
N:Pump normal
S:Stop the pump.
(1)No return spring
----------
----------
a=43.5deg+-5deg b=53deg+-5deg
----------
----------
a=43.5deg+-5deg b=53deg+-5deg
Timing setting
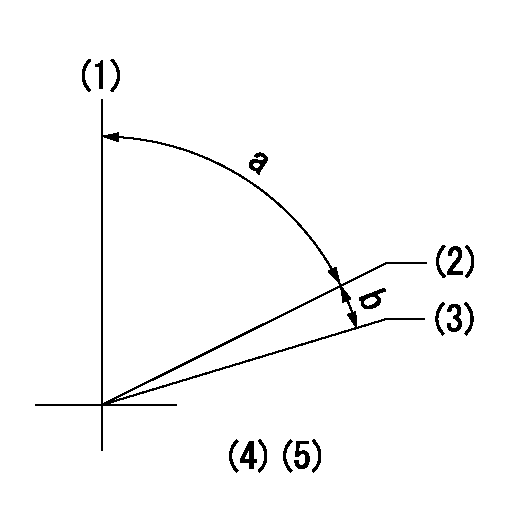
(1)Pump vertical direction
(2)Position of key groove at No 1 cylinder's beginning of injection
(3)Stamp aligning marks on the pump housing flange.
(4)-
----------
----------
a=46deg18min+-3deg b=13deg42min+-30min
----------
----------
a=46deg18min+-3deg b=13deg42min+-30min
Information:
Do not operate or work on this product unless you have read and understood the instruction and warnings in the relevant Operation and Maintenance Manuals and relevant service literature. Failure to follow the instructions or heed the warnings could result in injury or death. Proper care is your responsibility.
There have been instances of diagnostic code E931 - Aftertreatment#1 SCR Dosing Reagent Absolute Pressure : Low (4334-18 - Aftertreatment #1 DEF #1 Pressure (absolute) : Low – moderate severity) becoming active. This code can be generated by a blocked 495-1507 Diesel Exhaust Fluid Filter Gp, due to the filter not being replaced at the correct maintenance interval.The maintenance interval schedule for the DEF pump filter is every 1500 hours. Ensure that the filter is replaced at the correct service interval. Refer to Operation and Maintenance Manual, Maintenance Interval Schedule for the correct procedure.