Information injection-pump assembly
ZEXEL
101441-9840
1014419840
NISSAN-DIESEL
1671290176
1671290176
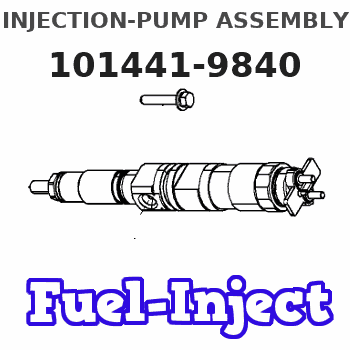
Rating:
Service parts 101441-9840 INJECTION-PUMP ASSEMBLY:
1.
_
6.
COUPLING PLATE
7.
COUPLING PLATE
8.
_
9.
_
11.
Nozzle and Holder
16600-43G02
12.
Open Pre:MPa(Kqf/cm2)
9.8{100}
15.
NOZZLE SET
Cross reference number
ZEXEL
101441-9840
1014419840
NISSAN-DIESEL
1671290176
1671290176
Zexel num
Bosch num
Firm num
Name
Calibration Data:
Adjustment conditions
Test oil
1404 Test oil ISO4113 or {SAEJ967d}
1404 Test oil ISO4113 or {SAEJ967d}
Test oil temperature
degC
40
40
45
Nozzle and nozzle holder
105780-8140
Bosch type code
EF8511/9A
Nozzle
105780-0000
Bosch type code
DN12SD12T
Nozzle holder
105780-2080
Bosch type code
EF8511/9
Opening pressure
MPa
17.2
Opening pressure
kgf/cm2
175
Injection pipe
Outer diameter - inner diameter - length (mm) mm 6-2-600
Outer diameter - inner diameter - length (mm) mm 6-2-600
Tester oil delivery pressure
kPa
157
157
157
Tester oil delivery pressure
kgf/cm2
1.6
1.6
1.6
Direction of rotation (viewed from drive side)
Right R
Right R
Injection timing adjustment
Direction of rotation (viewed from drive side)
Right R
Right R
Injection order
1-3-4-2
Pre-stroke
mm
2.15
2.1
2.2
Beginning of injection position
Drive side NO.1
Drive side NO.1
Difference between angles 1
Cal 1-3 deg. 90 89.5 90.5
Cal 1-3 deg. 90 89.5 90.5
Difference between angles 2
Cal 1-4 deg. 180 179.5 180.5
Cal 1-4 deg. 180 179.5 180.5
Difference between angles 3
Cyl.1-2 deg. 270 269.5 270.5
Cyl.1-2 deg. 270 269.5 270.5
Injection quantity adjustment
Adjusting point
A
Rack position
12.7
Pump speed
r/min
750
750
750
Average injection quantity
mm3/st.
51
50
52
Max. variation between cylinders
%
0
-2.5
2.5
Basic
*
Fixing the lever
*
Injection quantity adjustment_02
Adjusting point
-
Rack position
8.8+-0.5
Pump speed
r/min
300
300
300
Average injection quantity
mm3/st.
8
6.9
9.1
Max. variation between cylinders
%
0
-15
15
Fixing the rack
*
Remarks
Adjust only variation between cylinders; adjust governor according to governor specifications.
Adjust only variation between cylinders; adjust governor according to governor specifications.
Timer adjustment
Pump speed
r/min
(N1+50)-
-
Advance angle
deg.
0
0
0
Remarks
Start
Start
Timer adjustment_02
Pump speed
r/min
N1
Advance angle
deg.
0.5
Remarks
Measure the actual speed.
Measure the actual speed.
Timer adjustment_03
Pump speed
r/min
900
Remarks
Measure the actual advance angle.
Measure the actual advance angle.
Timer adjustment_04
Pump speed
r/min
-
Advance angle
deg.
7.3
7.3
7.3
Remarks
Measure the actual speed, stop
Measure the actual speed, stop
Test data Ex:
Governor adjustment
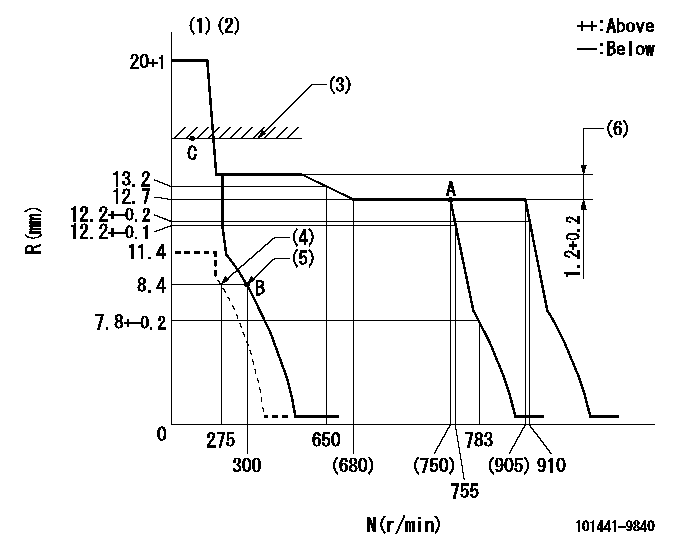
N:Pump speed
R:Rack position (mm)
(1)Target notch: K
(2)Tolerance for racks not indicated: +-0.05mm.
(3)RACK LIMIT: RAL
(4)Set idle sub-spring
(5)Main spring setting
(6)Rack difference between N = N1 and N = N2
----------
K=7 RAL=14.2+-0.1mm N1=750r/min N2=400r/min
----------
----------
K=7 RAL=14.2+-0.1mm N1=750r/min N2=400r/min
----------
Speed control lever angle
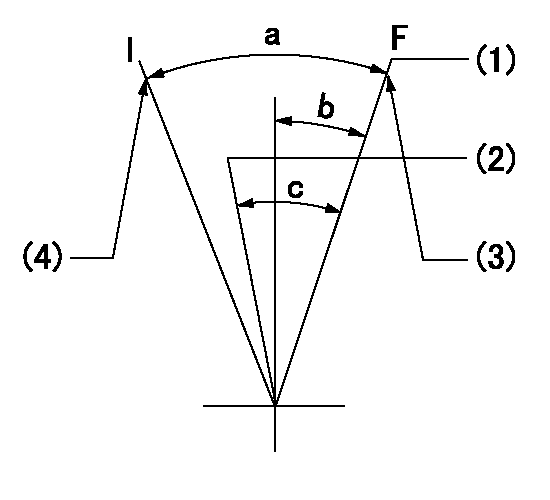
F:Full speed
I:Idle
(1)Set the pump speed at aa. ( At delivery )
(2)When pump speed set at bb
(3)Stopper bolt setting
(4)Stopper bolt setting
----------
aa=910r/min bb=755r/min
----------
a=24deg+-5deg b=0deg+-5deg c=6deg+-5deg
----------
aa=910r/min bb=755r/min
----------
a=24deg+-5deg b=0deg+-5deg c=6deg+-5deg
Stop lever angle
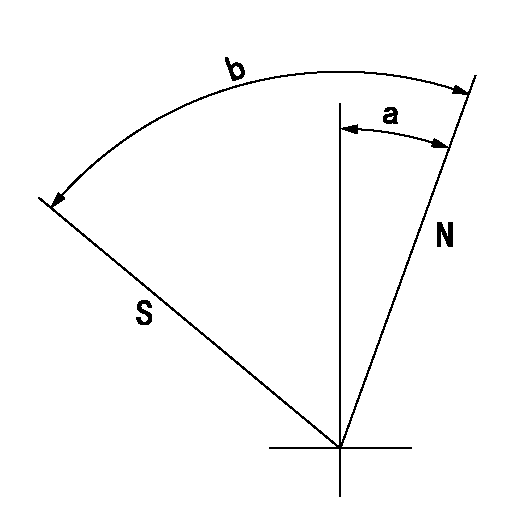
N:Pump normal
S:Stop the pump.
----------
----------
a=12deg+-5deg b=53deg+-5deg
----------
----------
a=12deg+-5deg b=53deg+-5deg
0000001501 GOV FULL LOAD ADJUSTMENT
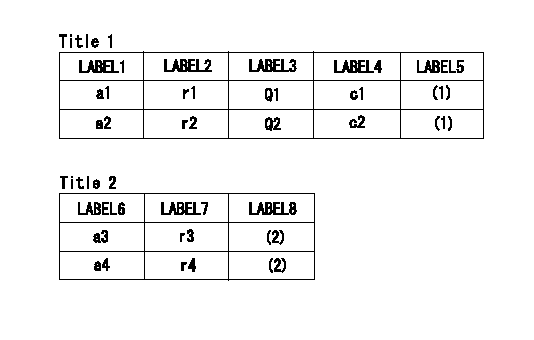
Title1:Full load stopper adjustment
Title2:Governor set speed
LABEL1:Distinguishing
LABEL2:Pump speed (r/min)
LABEL3:Ave. injection quantity (mm3/st)
LABEL4:Max. var. bet. cyl.
LABEL5:Remarks
LABEL6:Distinguishing
LABEL7:Governor set speed (r/min)
LABEL8:Remarks
(1)Adjustment conditions are the same as those for measuring injection quantity.
(2)-
----------
----------
a1=A a2=B r1=750r/min r2=750r/min Q1=51+-1mm3/st Q2=- c1=+-2.5% c2=+-2.5% a3=18 a4=15 r3=900r/min r4=750r/min
----------
----------
a1=A a2=B r1=750r/min r2=750r/min Q1=51+-1mm3/st Q2=- c1=+-2.5% c2=+-2.5% a3=18 a4=15 r3=900r/min r4=750r/min
Timing setting

(1)Pump vertical direction
(2)Position of gear mark 'ZZ' at No 1 cylinder's beginning of injection
(3)B.T.D.C.: aa
(4)-
----------
aa=16deg
----------
a=(100deg)
----------
aa=16deg
----------
a=(100deg)
Information:
Introduction
The problem that is identified below does not have a known permanent solution. Until a permanent solution is known, use the solution that is identified below.Problem
A customer experienced an early hour failure of the injector harness. Incorrect harness routing allowed the wiring harness to contact the valve spring.Solution
Illustration 1 g02703456
If the harness (1) has contacted the valve spring (2), inspect the wiring for cuts or exposed wire. If the harness is cut or has exposed wiring, replace the harness. When the harness is torqued down, make sure that the harness clips stay straight. If the clips rotate when torqued, the harness could contact the valve spring. Refer to Illustration 1.
Illustration 2 g02703161
If the harness has contacted the valve spring but does not have any cuts or exposed wire, disconnect the injector connector. Rotate the connector 360 degrees away from the valve spring and reconnect the connector. This rotation should twist the wires slightly and pull the wires to the correct location. Refer to Illustration 2.
The problem that is identified below does not have a known permanent solution. Until a permanent solution is known, use the solution that is identified below.Problem
A customer experienced an early hour failure of the injector harness. Incorrect harness routing allowed the wiring harness to contact the valve spring.Solution
Illustration 1 g02703456
If the harness (1) has contacted the valve spring (2), inspect the wiring for cuts or exposed wire. If the harness is cut or has exposed wiring, replace the harness. When the harness is torqued down, make sure that the harness clips stay straight. If the clips rotate when torqued, the harness could contact the valve spring. Refer to Illustration 1.
Illustration 2 g02703161
If the harness has contacted the valve spring but does not have any cuts or exposed wire, disconnect the injector connector. Rotate the connector 360 degrees away from the valve spring and reconnect the connector. This rotation should twist the wires slightly and pull the wires to the correct location. Refer to Illustration 2.