Information injection-pump assembly
BOSCH
9 400 614 122
9400614122
ZEXEL
101433-9180
1014339180
NISSAN-DIESEL
1671290062
1671290062

Rating:
Service parts 101433-9180 INJECTION-PUMP ASSEMBLY:
1.
_
6.
COUPLING PLATE
7.
COUPLING PLATE
8.
_
9.
_
11.
Nozzle and Holder
16600-90019
12.
Open Pre:MPa(Kqf/cm2)
9.8{100}
15.
NOZZLE SET
Include in #1:
101433-9180
as INJECTION-PUMP ASSEMBLY
Include in #2:
105866-3121
as _
Cross reference number
BOSCH
9 400 614 122
9400614122
ZEXEL
101433-9180
1014339180
NISSAN-DIESEL
1671290062
1671290062
Zexel num
Bosch num
Firm num
Name
9 400 614 122
1671290062 NISSAN-DIESEL
INJECTION-PUMP ASSEMBLY
SD22 * K 14BC INJECTION PUMP ASSY PE4A,5A, PE
SD22 * K 14BC INJECTION PUMP ASSY PE4A,5A, PE
Calibration Data:
Adjustment conditions
Test oil
1404 Test oil ISO4113 or {SAEJ967d}
1404 Test oil ISO4113 or {SAEJ967d}
Test oil temperature
degC
40
40
45
Nozzle and nozzle holder
105780-8140
Bosch type code
EF8511/9A
Nozzle
105780-0000
Bosch type code
DN12SD12T
Nozzle holder
105780-2080
Bosch type code
EF8511/9
Opening pressure
MPa
17.2
Opening pressure
kgf/cm2
175
Injection pipe
Outer diameter - inner diameter - length (mm) mm 6-2-600
Outer diameter - inner diameter - length (mm) mm 6-2-600
Tester oil delivery pressure
kPa
157
157
157
Tester oil delivery pressure
kgf/cm2
1.6
1.6
1.6
Direction of rotation (viewed from drive side)
Right R
Right R
Injection timing adjustment
Direction of rotation (viewed from drive side)
Right R
Right R
Injection order
1-3-4-2
Pre-stroke
mm
2.3
2.25
2.35
Beginning of injection position
Drive side NO.1
Drive side NO.1
Difference between angles 1
Cal 1-3 deg. 90 89.5 90.5
Cal 1-3 deg. 90 89.5 90.5
Difference between angles 2
Cal 1-4 deg. 180 179.5 180.5
Cal 1-4 deg. 180 179.5 180.5
Difference between angles 3
Cyl.1-2 deg. 270 269.5 270.5
Cyl.1-2 deg. 270 269.5 270.5
Injection quantity adjustment
Adjusting point
A
Rack position
14.7
Pump speed
r/min
750
750
750
Average injection quantity
mm3/st.
35
34
36
Max. variation between cylinders
%
0
-2.5
2.5
Basic
*
Fixing the lever
*
Injection quantity adjustment_02
Adjusting point
B
Rack position
14
Pump speed
r/min
750
750
750
Average injection quantity
mm3/st.
32
30.5
33.5
Max. variation between cylinders
%
0
-4
4
Fixing the rack
*
Injection quantity adjustment_03
Adjusting point
C
Rack position
10.8+-0.
5
Pump speed
r/min
300
300
300
Average injection quantity
mm3/st.
7.5
6.4
8.6
Max. variation between cylinders
%
0
-15
15
Fixing the rack
*
Remarks
Adjust only variation between cylinders; adjust governor according to governor specifications.
Adjust only variation between cylinders; adjust governor according to governor specifications.
Timer adjustment
Pump speed
r/min
500
Advance angle
deg.
0.5
Timer adjustment_02
Pump speed
r/min
550
Advance angle
deg.
0.7
Timer adjustment_03
Pump speed
r/min
700
Advance angle
deg.
1
0.5
1.5
Timer adjustment_04
Pump speed
r/min
(895)
Advance angle
deg.
2
1.5
2.5
Timer adjustment_05
Pump speed
r/min
-
Advance angle
deg.
5
5
5
Remarks
Measure the actual speed, stop
Measure the actual speed, stop
Test data Ex:
Governor adjustment
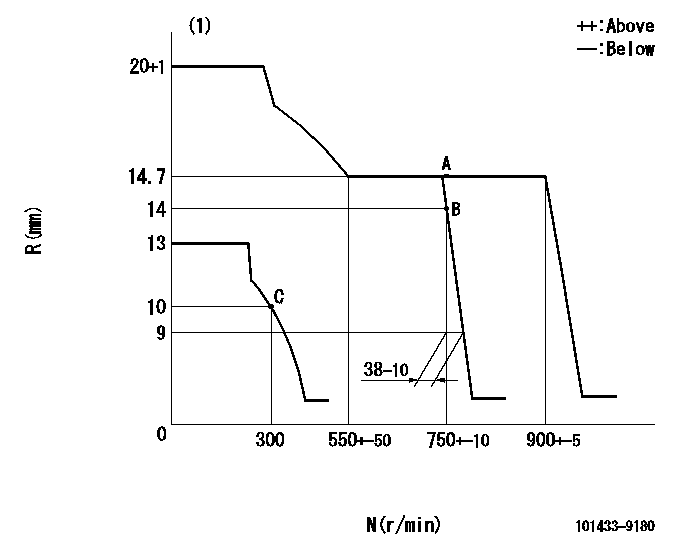
N:Pump speed
R:Rack position (mm)
(1)Target notch: K
----------
K=13
----------
----------
K=13
----------
Speed control lever angle

F:Full speed
I:Idle
S:Stop
(1)Speed set at aa (setting at shipping)
(2)Set the pump speed at bb.
----------
aa=900r/min bb=750r/min
----------
a=10deg+-5deg b=31deg+-5deg c=32deg+-3deg d=7.5deg+-5deg
----------
aa=900r/min bb=750r/min
----------
a=10deg+-5deg b=31deg+-5deg c=32deg+-3deg d=7.5deg+-5deg
Stop lever angle
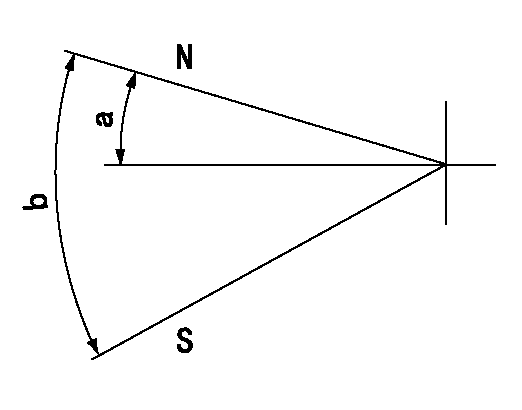
N:Pump normal
S:Stop the pump.
----------
----------
a=19deg+-5deg b=53deg+-5deg
----------
----------
a=19deg+-5deg b=53deg+-5deg
0000001501 GOV FULL LOAD ADJUSTMENT
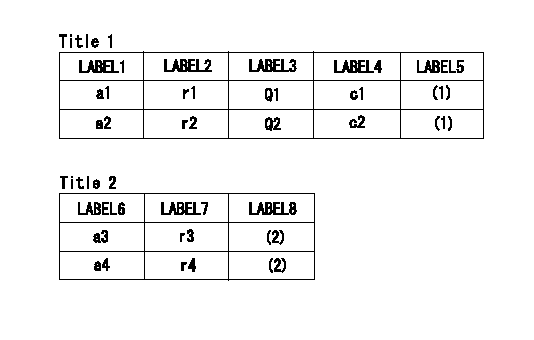
Title1:Full load stopper adjustment
Title2:Governor set speed
LABEL1:Distinguishing
LABEL2:Pump speed (r/min)
LABEL3:Ave. injection quantity (mm3/st)
LABEL4:Max. var. bet. cyl.
LABEL5:Remarks
LABEL6:Distinguishing
LABEL7:Governor set speed (r/min)
LABEL8:Remarks
(1)Adjustment conditions are the same as those for measuring injection quantity.
(2)-
----------
----------
a1=B a2=- r1=750r/min r2=- Q1=35+-1mm3/st Q2=- c1=+-2.5% c2=- a3=18 a4=15 r3=900r/min r4=750r/min
----------
----------
a1=B a2=- r1=750r/min r2=- Q1=35+-1mm3/st Q2=- c1=+-2.5% c2=- a3=18 a4=15 r3=900r/min r4=750r/min
Timing setting
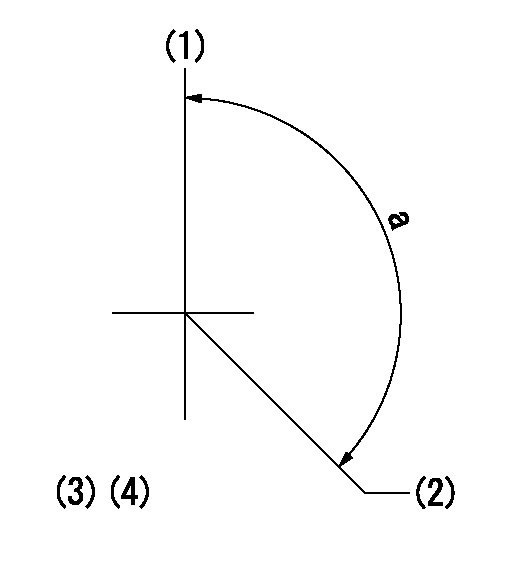
(1)Pump vertical direction
(2)Position of gear mark 'Y' at No 1 cylinder's beginning of injection
(3)-
(4)-
----------
----------
a=(130deg)
----------
----------
a=(130deg)
Information:
Start By:a. remove rocker arm assemblies and push rods 1. Remove injector hold down bolt (1).
Do not pry on the injector hold down bracket. Damage to the injector could occur. The injector has a notch in it on the side opposite the rack. This notch is used for prying the injector loose. Also, do not move the fuel injector rack without the injector spring slightly compressed. Damage to the injector could occur.
2. Use Tool (A) to loosen the fuel injector; then rotate the fuel injector to disengage the injector rack from the fuel control linkage. Remove the fuel injector. Be sure both O-ring seals (2) are on the fuel injector. The following steps are for the installation of the unit fuel injectors.3. Check the condition of O-ring seals (2). If the seals are damaged, use new parts for replacement. Install the O-ring seals on in the fuel injector.4. Lubricate the O-ring seals on the fuel injector with clean engine oil.5. Position the fuel injector in the cylinder head assembly; then rotate it to engage the injector rack with the fuel control linkage. Push down on the top of the fuel injector so the O-ring seals slide into the bore in the cylinder head assembly. Be sure the fuel injector is seated properly before installing bolt (1) that holds it in position. Do not use bolt (1) to pull the fuel injector down into the cylinder head assembly.6. Install bolt (1), and tighten it.7. After installation of the rocker arm assemblies and push rods, Check and/or adjust the following: Injector Synchronization, Fuel Setting, Fuel Timing, Valve Lash. See the 3114 & 3116 Diesel Truck Engines Systems Operation Testing & Adjusting module, Form No. SENR6437 to check and/or adjust the above items.End By:a. install rocker arm assemblies and push rods
Do not pry on the injector hold down bracket. Damage to the injector could occur. The injector has a notch in it on the side opposite the rack. This notch is used for prying the injector loose. Also, do not move the fuel injector rack without the injector spring slightly compressed. Damage to the injector could occur.
2. Use Tool (A) to loosen the fuel injector; then rotate the fuel injector to disengage the injector rack from the fuel control linkage. Remove the fuel injector. Be sure both O-ring seals (2) are on the fuel injector. The following steps are for the installation of the unit fuel injectors.3. Check the condition of O-ring seals (2). If the seals are damaged, use new parts for replacement. Install the O-ring seals on in the fuel injector.4. Lubricate the O-ring seals on the fuel injector with clean engine oil.5. Position the fuel injector in the cylinder head assembly; then rotate it to engage the injector rack with the fuel control linkage. Push down on the top of the fuel injector so the O-ring seals slide into the bore in the cylinder head assembly. Be sure the fuel injector is seated properly before installing bolt (1) that holds it in position. Do not use bolt (1) to pull the fuel injector down into the cylinder head assembly.6. Install bolt (1), and tighten it.7. After installation of the rocker arm assemblies and push rods, Check and/or adjust the following: Injector Synchronization, Fuel Setting, Fuel Timing, Valve Lash. See the 3114 & 3116 Diesel Truck Engines Systems Operation Testing & Adjusting module, Form No. SENR6437 to check and/or adjust the above items.End By:a. install rocker arm assemblies and push rods