Information injection-pump assembly
BOSCH
9 400 614 035
9400614035
ZEXEL
101402-9921
1014029921
YANMAR
12391151020
12391151020
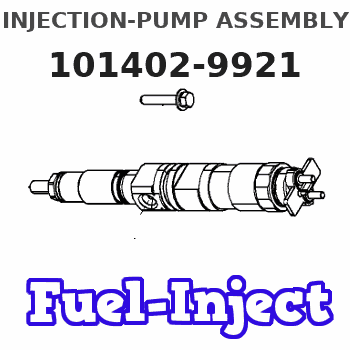
Rating:
Service parts 101402-9921 INJECTION-PUMP ASSEMBLY:
1.
_
5.
AUTOM. ADVANCE MECHANIS
6.
COUPLING PLATE
7.
COUPLING PLATE
8.
_
9.
_
10.
NOZZLE AND HOLDER ASSY
11.
Nozzle and Holder
12.
Open Pre:MPa(Kqf/cm2)
13.
NOZZLE-HOLDER
14.
NOZZLE
15.
NOZZLE SET
Cross reference number
BOSCH
9 400 614 035
9400614035
ZEXEL
101402-9921
1014029921
YANMAR
12391151020
12391151020
Zexel num
Bosch num
Firm num
Name
101402-9921
9 400 614 035
12391151020 YANMAR
INJECTION-PUMP ASSEMBLY
4TNE106 K 14BC INJECTION PUMP ASSY PE4A,5A, PE
4TNE106 K 14BC INJECTION PUMP ASSY PE4A,5A, PE
Calibration Data:
Adjustment conditions
Test oil
1404 Test oil ISO4113 or {SAEJ967d}
1404 Test oil ISO4113 or {SAEJ967d}
Test oil temperature
degC
40
40
45
Nozzle and nozzle holder
105780-8140
Bosch type code
EF8511/9A
Nozzle
105780-0000
Bosch type code
DN12SD12T
Nozzle holder
105780-2080
Bosch type code
EF8511/9
Opening pressure
MPa
17.2
Opening pressure
kgf/cm2
175
Injection pipe
Outer diameter - inner diameter - length (mm) mm 6-2-600
Outer diameter - inner diameter - length (mm) mm 6-2-600
Overflow valve
131424-1520
Overflow valve opening pressure
kPa
157
157
157
Overflow valve opening pressure
kgf/cm2
1.6
1.6
1.6
Tester oil delivery pressure
kPa
157
157
157
Tester oil delivery pressure
kgf/cm2
1.6
1.6
1.6
Direction of rotation (viewed from drive side)
Right R
Right R
Injection timing adjustment
Direction of rotation (viewed from drive side)
Right R
Right R
Injection order
1-3-4-2
Pre-stroke
mm
3.3
3.25
3.35
Beginning of injection position
Drive side NO.1
Drive side NO.1
Difference between angles 1
Cal 1-3 deg. 90 89.5 90.5
Cal 1-3 deg. 90 89.5 90.5
Difference between angles 2
Cal 1-4 deg. 180 179.5 180.5
Cal 1-4 deg. 180 179.5 180.5
Difference between angles 3
Cyl.1-2 deg. 270 269.5 270.5
Cyl.1-2 deg. 270 269.5 270.5
Injection quantity adjustment
Adjusting point
A
Rack position
10.4
Pump speed
r/min
1150
1150
1150
Average injection quantity
mm3/st.
66.5
65.5
67.5
Max. variation between cylinders
%
0
-2.5
2.5
Basic
*
Fixing the lever
*
Injection quantity adjustment_02
Adjusting point
C
Rack position
7+-0.5
Pump speed
r/min
550
550
550
Average injection quantity
mm3/st.
9
8
10
Max. variation between cylinders
%
0
-15
15
Fixing the rack
*
Injection quantity adjustment_03
Adjusting point
D
Rack position
12.1++
Pump speed
r/min
100
100
100
Average injection quantity
mm3/st.
90
90
100
Fixing the lever
*
Rack limit
*
Test data Ex:
Governor adjustment
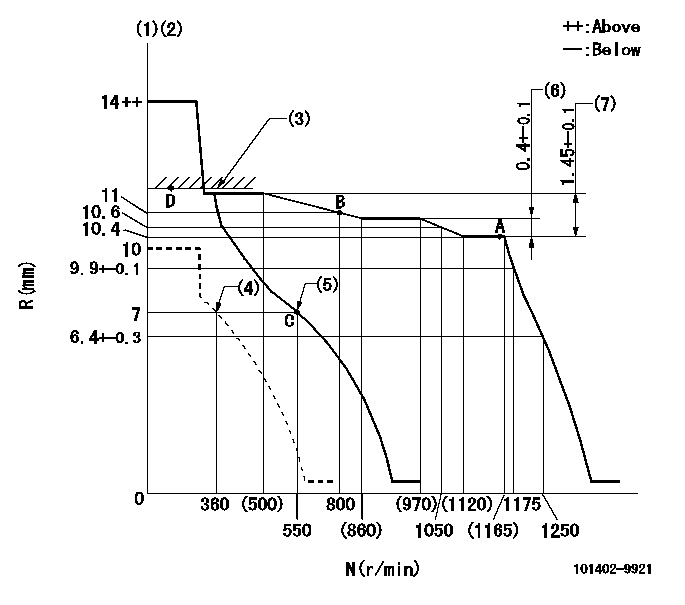
N:Pump speed
R:Rack position (mm)
(1)Target notch: K
(2)Tolerance for racks not indicated: +-0.05mm.
(3)RACK LIMIT
(4)Set idle sub-spring
(5)Main spring setting
(6)Rack difference between N = N1 and N = N2
(7)Rack difference between N = N3 and N = N4
----------
K=10 N1=1150r/min N2=900r/min N3=1150r/min N4=350r/min
----------
----------
K=10 N1=1150r/min N2=900r/min N3=1150r/min N4=350r/min
----------
Speed control lever angle

F:Full speed
I:Idle
(1)Stopper bolt setting
----------
----------
a=14deg+-5deg b=25deg+-5deg
----------
----------
a=14deg+-5deg b=25deg+-5deg
Stop lever angle
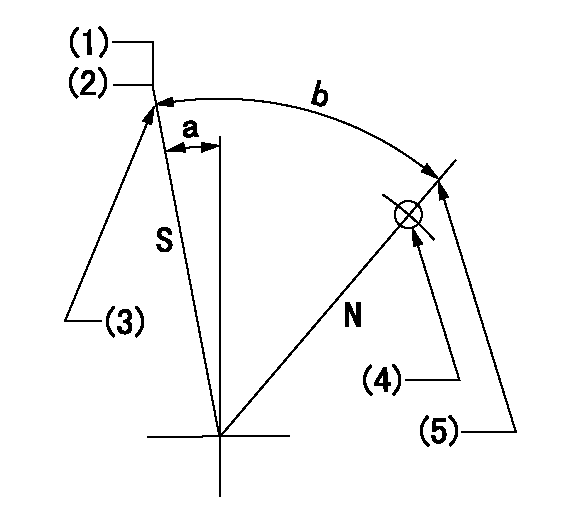
N:Pump normal
S:Stop the pump.
(1)Normal stop
(2)Rack position = aa, speed = bb.
(3)Stopper bolt setting
(4)Use the pin above R = cc
(5)Stopper bolt setting
----------
aa=1-0.5mm bb=0r/min cc=30mm
----------
a=13deg+-5deg b=(55deg)
----------
aa=1-0.5mm bb=0r/min cc=30mm
----------
a=13deg+-5deg b=(55deg)
Timing setting
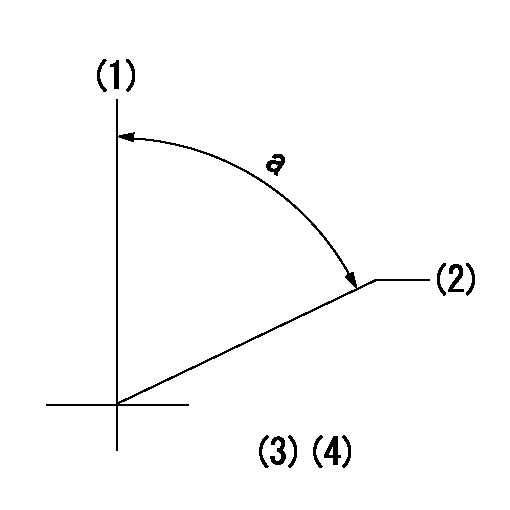
(1)Pump vertical direction
(2)Position of camshaft's key groove at No 1 cylinder's beginning of injection
(3)-
(4)-
----------
----------
a=(60deg)
----------
----------
a=(60deg)
Information:
Be sure to read the correct side of the dipstick. The ADD and FULL levels are not the same when checking the oil while stopped or while idling.
Checking Oil Pressure
Immediately after starting, and frequently during operation, observe the oil pressure gauge reading. The indicator should register in the NORMAL range. If the indicator fluctuates or registers below NORMAL range:1. Move the governor control to low idle position.2. Check the oil level. Be sure to read the ENGINE IDLING side of the dipstick.3. Add oil until the oil level is at the FULL mark on the ENGINE IDLING side of the dipstick. Do not overfill.4. Check for oil leaks.5. If necessary, stop the engine and have repairs made.Draining Engine Oil
With engine stopped and oil warm:1. Remove the crankcase oil drain plug.2. Allow the oil to drain. 3. Clean and install the drain plug.OR, if a sump pump is used:1. Connect a suitable drain line and container to the pump outlet.2. With engine stopped and oil warm, open the sump pump valve to the engine crankcase drain line: The two marks on the valve must be turned so that one mark points to the pump, and the second mark points to the engine drain line.3. Operate the sump pump handle until the crankcase is empty.4. Close the valve to the engine crankcase drain line.Cleaning the Breather
1. Release the hose clamp and disconnect the fumes disposal tube.2. Remove the breather assembly. 3. Wash the breather in solvent.4. Allow to drain dry and then wipe.5. Inspect the gasket. Install a new gasket if necessary.6. Install the breather.7. Connect the fumes disposal tube. Changing Oil Filter
1. Unscrew and remove the filter. 2. Be sure the old filter gasket did not remain attached inside the filter base: Leaking will occur between the new filter gasket and this old gasket.3. Wipe the filter base. 4. Apply a thin coat of clean oil to the gasket of the new filter. 5. Install the new filter: Hand tighten the filter 3/4turn after the filter gasket contacts the base. Use rotation index numbers, which are painted on the filter can, as a guide for proper tightening. Filling the Crankcase
1. Fill the crankcase to the safe starting range on the ENGINE STOPPED side of the dipstick. See the Lubrication Specifications for refill capacity and proper oil viscosity. 2. Start the engine and check for oil leaks.3. After the engine is warm, check the oil level with the engine idling.4. Add oil if necessary to maintain the oil level at the FULL mark on the ENGINE IDLING side of the dipstick.Fan Drive Bearings
Lubricate the fan drive bearings with lubricating grease through one fitting, 1 or 2 strokes.
LOCATION OF 4B4550 PRESSURE RELIEF FITTING AND 2D4867 FITTING SHOWN IN THE STANDARD LOCATION.If the grease fitting is not readily accessible, it may be necessary to1. Remove the 4B4550 Fitting (relief) from the fan mounting bracket assembly and install the 2D4867 Fitting in its place.2. Install the 4B4550 Fitting (relief) in place of the
Have questions with 101402-9921?
Group cross 101402-9921 ZEXEL
Daewoo
Daewoo
Yanmar
101402-9921
9 400 614 035
12391151020
INJECTION-PUMP ASSEMBLY
4TNE106
4TNE106