Information injection-pump assembly
BOSCH
9 400 611 740
9400611740
ZEXEL
101402-9920
1014029920
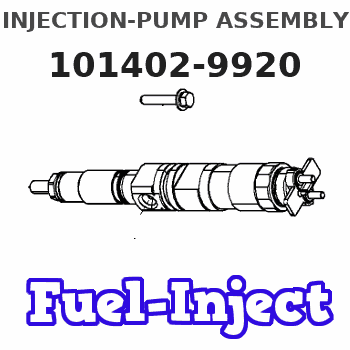
Rating:
Service parts 101402-9920 INJECTION-PUMP ASSEMBLY:
1.
_
5.
AUTOM. ADVANCE MECHANIS
6.
COUPLING PLATE
7.
COUPLING PLATE
8.
_
9.
_
10.
NOZZLE AND HOLDER ASSY
11.
Nozzle and Holder
12.
Open Pre:MPa(Kqf/cm2)
21.6{220}
13.
NOZZLE-HOLDER
14.
NOZZLE
15.
NOZZLE SET
Cross reference number
BOSCH
9 400 611 740
9400611740
ZEXEL
101402-9920
1014029920
Zexel num
Bosch num
Firm num
Name
Calibration Data:
Adjustment conditions
Test oil
1404 Test oil ISO4113 or {SAEJ967d}
1404 Test oil ISO4113 or {SAEJ967d}
Test oil temperature
degC
40
40
45
Nozzle and nozzle holder
105780-8140
Bosch type code
EF8511/9A
Nozzle
105780-0000
Bosch type code
DN12SD12T
Nozzle holder
105780-2080
Bosch type code
EF8511/9
Opening pressure
MPa
17.2
Opening pressure
kgf/cm2
175
Injection pipe
Outer diameter - inner diameter - length (mm) mm 6-2-600
Outer diameter - inner diameter - length (mm) mm 6-2-600
Overflow valve
131424-1520
Overflow valve opening pressure
kPa
157
123
191
Overflow valve opening pressure
kgf/cm2
1.6
1.25
1.95
Tester oil delivery pressure
kPa
157
157
157
Tester oil delivery pressure
kgf/cm2
1.6
1.6
1.6
Direction of rotation (viewed from drive side)
Right R
Right R
Injection timing adjustment
Direction of rotation (viewed from drive side)
Right R
Right R
Injection order
1-3-4-2
Pre-stroke
mm
3.3
3.25
3.35
Beginning of injection position
Drive side NO.1
Drive side NO.1
Difference between angles 1
Cal 1-3 deg. 90 89.5 90.5
Cal 1-3 deg. 90 89.5 90.5
Difference between angles 2
Cal 1-4 deg. 180 179.5 180.5
Cal 1-4 deg. 180 179.5 180.5
Difference between angles 3
Cyl.1-2 deg. 270 269.5 270.5
Cyl.1-2 deg. 270 269.5 270.5
Injection quantity adjustment
Adjusting point
A
Rack position
10.4
Pump speed
r/min
1150
1150
1150
Average injection quantity
mm3/st.
66.5
65.5
67.5
Max. variation between cylinders
%
0
-2.5
2.5
Basic
*
Fixing the lever
*
Injection quantity adjustment_02
Adjusting point
C
Rack position
7+-0.5
Pump speed
r/min
550
550
550
Average injection quantity
mm3/st.
9
8
10
Max. variation between cylinders
%
0
-15
15
Fixing the rack
*
Injection quantity adjustment_03
Adjusting point
D
Rack position
-
Pump speed
r/min
100
100
100
Average injection quantity
mm3/st.
90
90
100
Fixing the lever
*
Rack limit
*
Test data Ex:
Governor adjustment
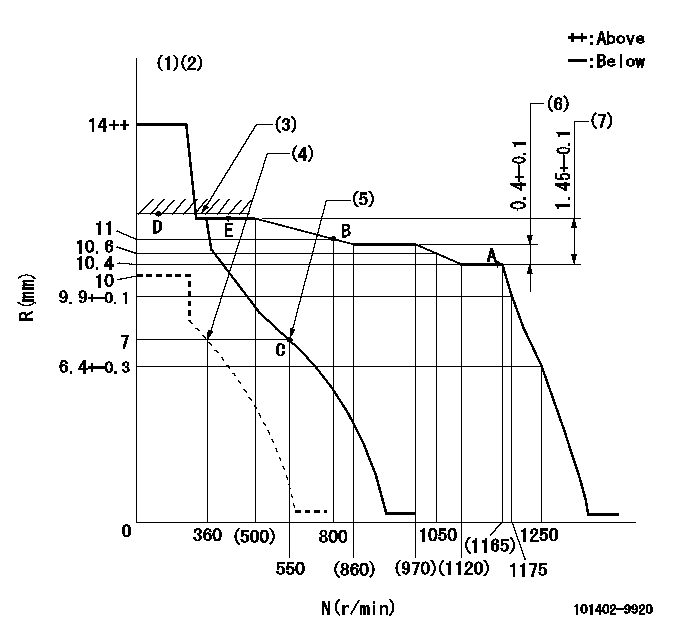
N:Pump speed
R:Rack position (mm)
(1)Target notch: K
(2)Tolerance for racks not indicated: +-0.05mm.
(3)RACK LIMIT
(4)Set idle sub-spring
(5)Main spring setting
(6)Rack difference between N = N1 and N = N2
(7)Rack difference between N = N3 and N = N4
----------
K=10 N1=1150r/min N2=900r/min N3=1150r/min N4=350r/min
----------
----------
K=10 N1=1150r/min N2=900r/min N3=1150r/min N4=350r/min
----------
Speed control lever angle
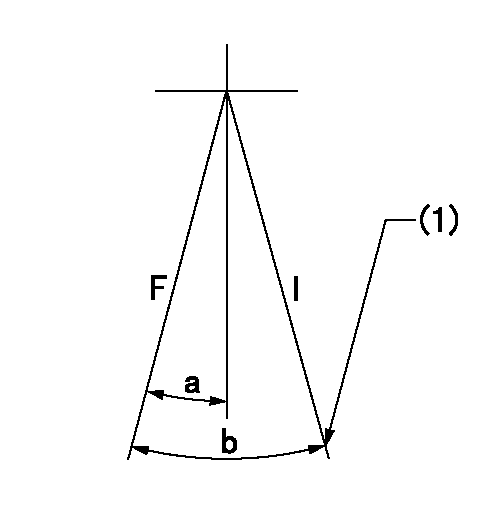
F:Full speed
I:Idle
(1)Stopper bolt setting
----------
----------
a=14deg+-5deg b=25deg+-5deg
----------
----------
a=14deg+-5deg b=25deg+-5deg
Stop lever angle
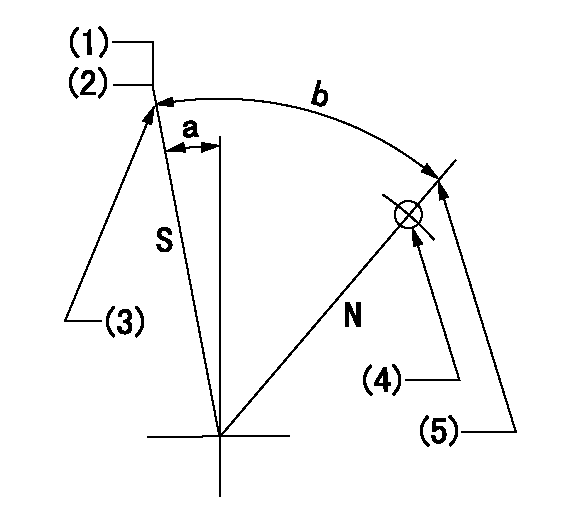
N:Pump normal
S:Stop the pump.
(1)Normal stop
(2)Rack position = aa, speed = bb.
(3)Stopper bolt setting
(4)Stopper bolt setting
(5)Use the pin above R = cc
----------
aa=1-0.5mm bb=0r/min cc=30mm
----------
a=13deg+-5deg b=(55deg)
----------
aa=1-0.5mm bb=0r/min cc=30mm
----------
a=13deg+-5deg b=(55deg)
Timing setting
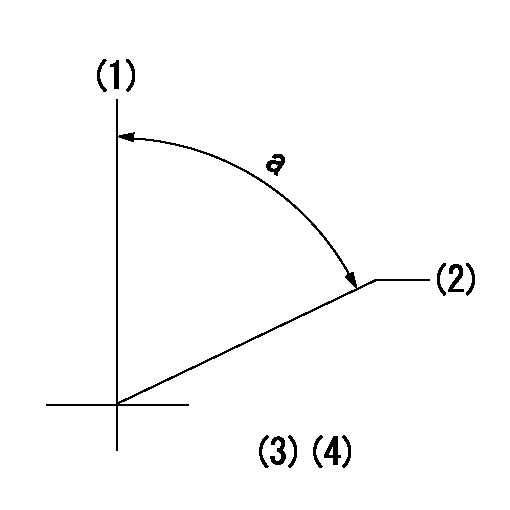
(1)Pump vertical direction
(2)Position of camshaft's key groove at No 1 cylinder's beginning of injection
(3)-
(4)-
----------
----------
a=(60deg)
----------
----------
a=(60deg)
Information:
Regular service intervals, along with close daily visual inspection and the adherence to the instructions and schedules, will assure many hours of trouble-free service. If correction steps are taken immediately on discovery of any abnormal condition, fewer forced stops and more economical operation will result.The Lubrication and Maintenance Chart is intended as a guide and adjustments in the schedule may be necessary, depending on conditions under which the engine is operating. A thorough analysis should be made before adjusting the maintenance schedule.Some items to consider in establishing a new schedule are: Severe dust or dirty conditions, fuel consumption (a good measurement to establish intervals as it indicates the amount of work performed). As a guideline, the 3408 Engine with a 12 gal. (45 litre) (10 imp. gal.) capacity crankcase will use approximately 4000 gal. (15,000 litre) (3332 imp. gal.) between oil changes.* The 3412 Engine with a 16 gal. (60.5 litre) (13 imp. gal.) capacity crankcase will use approximately 5100 gal. (19,200 litre) (4248 imp. gal.) between oil changes. *Reducing or extending the maintenance intervals should be done only after complete study and enough time to gain adequate experience to meet specific operations.*With 0.5% or less fuel sulphur content.Caterpillar scheduled oil sampling: Scheduled oil sampling is a program which analyzes oil samples taken from an engine at regular intervals (usually at oil change periods). This oil analysis does not indicate the condition of the oil; but rather, it is a scheduled procedure to determine engine condition at regular intervals by analyzing lubricating oil for foreign and wear particles.The scheduled oil sampling will give the following benefits:It assures the owner that maintenance has been performed.It will show the first signs of excessive wear, meaning a possible upcoming failure, allowing time for a scheduled repair.It will warm maintenance personnel of improper or lack of maintenance and presence of fuel dilution or antifreeze in oil.It is particularly helpful in preventing wear due to dirt entry from air cleaner or inlet piping.Regular sampling is especially advantageous for new engines to establish wear trends from the beginning. The results of the oil analysis are interpreted by experienced, highly trained personnel. Contact your Caterpillar dealer for detailed information.