Information injection-pump assembly
ZEXEL
101402-9650
1014029650
MITSUBISHI-HEAV
3426103080
3426103080
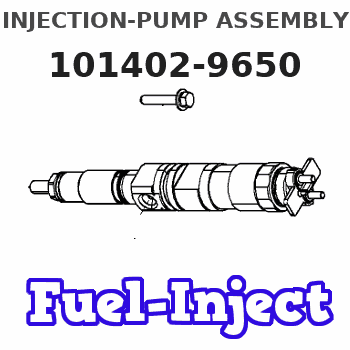
Rating:
Cross reference number
ZEXEL
101402-9650
1014029650
MITSUBISHI-HEAV
3426103080
3426103080
Zexel num
Bosch num
Firm num
Name
Calibration Data:
Adjustment conditions
Test oil
1404 Test oil ISO4113 or {SAEJ967d}
1404 Test oil ISO4113 or {SAEJ967d}
Test oil temperature
degC
40
40
45
Nozzle and nozzle holder
105780-8140
Bosch type code
EF8511/9A
Nozzle
105780-0000
Bosch type code
DN12SD12T
Nozzle holder
105780-2080
Bosch type code
EF8511/9
Opening pressure
MPa
17.2
Opening pressure
kgf/cm2
175
Injection pipe
Outer diameter - inner diameter - length (mm) mm 6-2-600
Outer diameter - inner diameter - length (mm) mm 6-2-600
Overflow valve
131424-5720
Overflow valve opening pressure
kPa
255
221
289
Overflow valve opening pressure
kgf/cm2
2.6
2.25
2.95
Tester oil delivery pressure
kPa
157
157
157
Tester oil delivery pressure
kgf/cm2
1.6
1.6
1.6
Direction of rotation (viewed from drive side)
Right R
Right R
Injection timing adjustment
Direction of rotation (viewed from drive side)
Right R
Right R
Injection order
1-3-4-2
Pre-stroke
mm
3.2
3.15
3.25
Beginning of injection position
Drive side NO.1
Drive side NO.1
Difference between angles 1
Cal 1-3 deg. 90 89.5 90.5
Cal 1-3 deg. 90 89.5 90.5
Difference between angles 2
Cal 1-4 deg. 180 179.5 180.5
Cal 1-4 deg. 180 179.5 180.5
Difference between angles 3
Cyl.1-2 deg. 270 269.5 270.5
Cyl.1-2 deg. 270 269.5 270.5
Injection quantity adjustment
Adjusting point
A
Rack position
9.1
Pump speed
r/min
1100
1100
1100
Average injection quantity
mm3/st.
80.5
79.5
81.5
Max. variation between cylinders
%
0
-2.5
2.5
Basic
*
Fixing the rack
*
Injection quantity adjustment_02
Adjusting point
C
Rack position
6+-0.5
Pump speed
r/min
450
450
450
Average injection quantity
mm3/st.
11
9.7
12.3
Max. variation between cylinders
%
0
-14
14
Fixing the rack
*
Injection quantity adjustment_03
Adjusting point
D
Rack position
-
Pump speed
r/min
100
100
100
Average injection quantity
mm3/st.
80
80
85
Fixing the lever
*
Rack limit
*
Test data Ex:
Governor adjustment
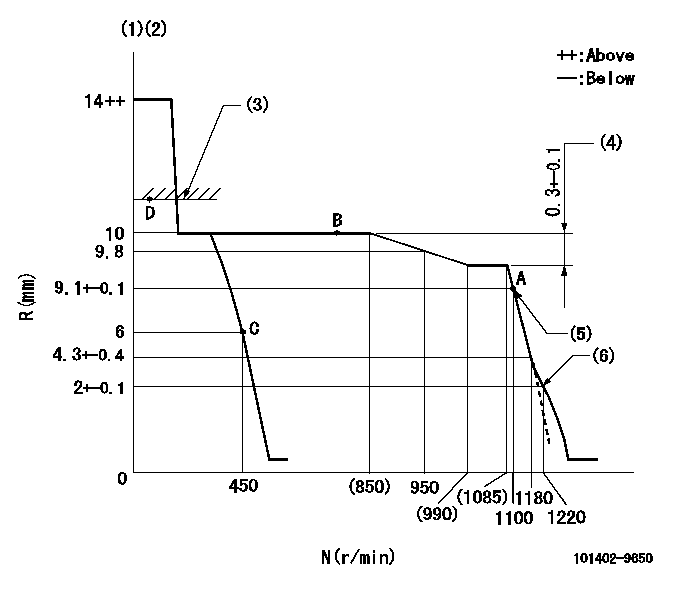
N:Pump speed
R:Rack position (mm)
(1)Target notch: K
(2)Tolerance for racks not indicated: +-0.05mm.
(3)RACK LIMIT
(4)Rack difference between N = N1 and N = N2
(5)Main spring setting
(6)Set idle sub-spring
----------
K=11 N1=1030r/min N2=700r/min
----------
----------
K=11 N1=1030r/min N2=700r/min
----------
Speed control lever angle
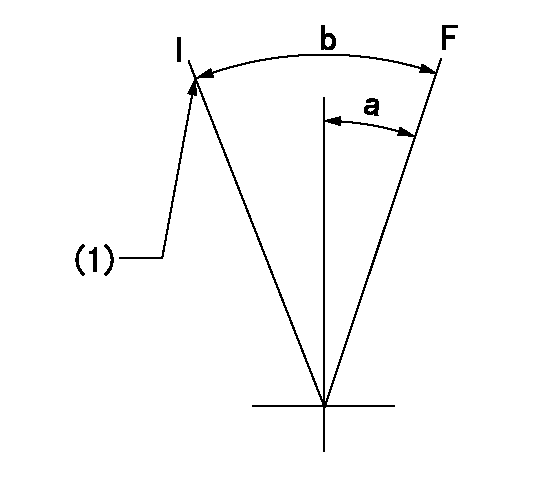
F:Full speed
I:Idle
(1)Stopper bolt setting
----------
----------
a=6deg+-5deg b=20deg+-5deg
----------
----------
a=6deg+-5deg b=20deg+-5deg
Stop lever angle
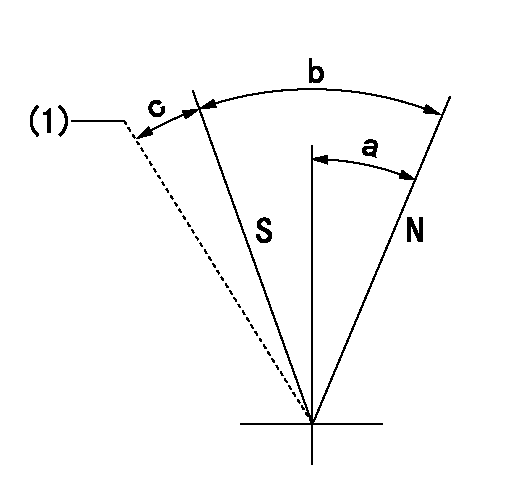
N:Pump normal
S:Stop the pump.
(1)Hold the boss against the stop side
----------
----------
a=26.5deg+-5deg b=53deg+-5deg c=(9deg)
----------
----------
a=26.5deg+-5deg b=53deg+-5deg c=(9deg)
Timing setting
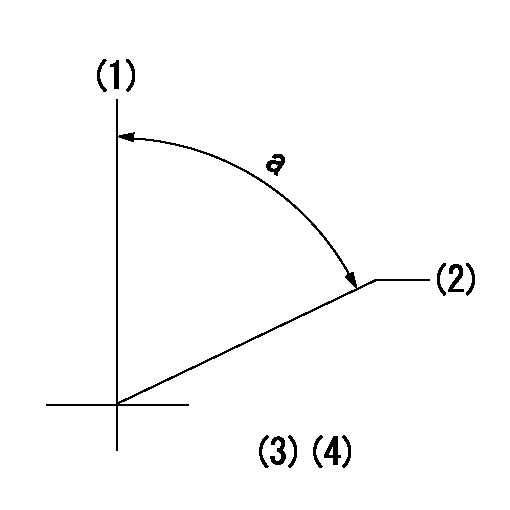
(1)Pump vertical direction
(2)Position of camshaft's key groove at No 1 cylinder's beginning of injection
(3)-
(4)-
----------
----------
a=(50deg)
----------
----------
a=(50deg)
Information:
Fuel Injection Line Without Support Bracket Two different fuel injection line arrangements are utilized. One arrangement uses a support bracket, the other does not.
Be sure the fuel injection line clamps are installed in the correct locations. Incorrectly installed clamps may allow the fuel injection lines to vibrate and become damaged. The damaged lines may leak and cause a fire.
(1) Clamp location dimensions are in reference to a vertical line (1) through the center of the number one fuel pump outlet. Align brackets in position to fuel lines such that when the fasteners are tightened no strain will be added to the fuel lines while tightening fasteners.(A) ... 35 3 mm (1.38 .12 in)(B) ... 165 13 mm (6.50 .51 in)(C) ... 187 1 mm (7.36 .04 in)(D) ... 187 3 mm (7.36 .12 in)(E) ... 282 3 mm (11.10 .12 in)(F) ... 314 13 mm (12.36 .51 in)(G) ... 457 3 mm (17.99 .12 in)(H) ... 529 3 mm (17.99 .12 in)Tighten metal-to-metal clamps to a torque of ... 2.3 N m (20 lb in) The 6V4980 Torque Screwdriver Tool Group is available for applying the correct torque. (2) Tighten fuel injection line nuts to ... 42 7 N m (31 5 lb ft)(3) Tighten nuts to ... 14 3 N m (10 2 lb ft)(4) Tighten retainer on adapter to ... 48 7 N m (35 5 lb ft)
Fuel Injection Line With Support Bracket
Be sure the fuel injection line clamps are installed in the correct locations. Incorrectly installed clamps may allow the fuel injection lines to vibrate and become damaged. The damaged lines may leak and cause a fire.
(1) Clamp location dimensions are in reference to a vertical line (1) through the center of the number one fuel pump outlet.Align brackets in position to fuel lines such that when the fasteners are tightened no strain will be added to the fuel lines while tightening fasteners.(A) ... 35 3 mm (1.38 .12 in)(B) ... 165 13 mm (6.50 .51 in)(C) ... 187 1 mm (7.36 .04 in)(D) ... 187 3 mm (7.36 .12 in)(E) ... 282 3 mm (11.10 .12 in)(F) ... 283 3 mm (11.14 .12 in)(G) ... 529 3 mm (17.99 .12 in)Tighten metal-to-metal clamps to a torque of ... 2.3 N m (20 lb in) The 6V4980 Torque Screwdriver Tool Group is available for applying the correct torque. (2) Tighten fuel injection line nuts to ... 42 7 N m (31 5 lb ft)(3) Tighten nuts to ... 14 3 N m (10 2 lb ft)(4) Tighten retainer on adapter to ... 48 7 N m (35 5 lb ft)