Information injection-pump assembly
BOSCH
9 400 611 378
9400611378
ZEXEL
101402-7700
1014027700
ISUZU
8972410320
8972410320

Rating:
Service parts 101402-7700 INJECTION-PUMP ASSEMBLY:
1.
_
5.
AUTOM. ADVANCE MECHANIS
6.
COUPLING PLATE
8.
_
9.
_
11.
Nozzle and Holder
1-15300-394-0
12.
Open Pre:MPa(Kqf/cm2)
18.1{185}
15.
NOZZLE SET
Cross reference number
BOSCH
9 400 611 378
9400611378
ZEXEL
101402-7700
1014027700
ISUZU
8972410320
8972410320
Zexel num
Bosch num
Firm num
Name
Calibration Data:
Adjustment conditions
Test oil
1404 Test oil ISO4113 or {SAEJ967d}
1404 Test oil ISO4113 or {SAEJ967d}
Test oil temperature
degC
40
40
45
Nozzle and nozzle holder
105780-8140
Bosch type code
EF8511/9A
Nozzle
105780-0000
Bosch type code
DN12SD12T
Nozzle holder
105780-2080
Bosch type code
EF8511/9
Opening pressure
MPa
17.2
Opening pressure
kgf/cm2
175
Injection pipe
Outer diameter - inner diameter - length (mm) mm 6-2-600
Outer diameter - inner diameter - length (mm) mm 6-2-600
Overflow valve
134424-4120
Overflow valve opening pressure
kPa
255
221
289
Overflow valve opening pressure
kgf/cm2
2.6
2.25
2.95
Tester oil delivery pressure
kPa
157
157
157
Tester oil delivery pressure
kgf/cm2
1.6
1.6
1.6
Direction of rotation (viewed from drive side)
Right R
Right R
Injection timing adjustment
Direction of rotation (viewed from drive side)
Right R
Right R
Injection order
1-3-4-2
Pre-stroke
mm
4.2
4.15
4.25
Beginning of injection position
Drive side NO.1
Drive side NO.1
Difference between angles 1
Cal 1-3 deg. 90 89.5 90.5
Cal 1-3 deg. 90 89.5 90.5
Difference between angles 2
Cal 1-4 deg. 180 179.5 180.5
Cal 1-4 deg. 180 179.5 180.5
Difference between angles 3
Cyl.1-2 deg. 270 269.5 270.5
Cyl.1-2 deg. 270 269.5 270.5
Injection quantity adjustment
Adjusting point
A
Rack position
11.2
Pump speed
r/min
1100
1100
1100
Average injection quantity
mm3/st.
118
116.9
119.1
Max. variation between cylinders
%
0
-2
2
Basic
*
Fixing the lever
*
Boost pressure
kPa
72
72
Boost pressure
mmHg
540
540
Injection quantity adjustment_02
Adjusting point
-
Rack position
7.7+-0.5
Pump speed
r/min
475
475
475
Average injection quantity
mm3/st.
8.8
7.4
10.2
Max. variation between cylinders
%
0
-14
14
Fixing the rack
*
Boost pressure
kPa
0
0
0
Boost pressure
mmHg
0
0
0
Remarks
Adjust only variation between cylinders; adjust governor according to governor specifications.
Adjust only variation between cylinders; adjust governor according to governor specifications.
Injection quantity adjustment_03
Adjusting point
E
Rack position
-
Pump speed
r/min
100
100
100
Average injection quantity
mm3/st.
120
115
125
Fixing the lever
*
Boost pressure
kPa
0
0
0
Boost pressure
mmHg
0
0
0
Rack limit
*
Boost compensator adjustment
Pump speed
r/min
500
500
500
Rack position
R1-1.5
Boost pressure
kPa
22
19.3
24.7
Boost pressure
mmHg
165
145
185
Boost compensator adjustment_02
Pump speed
r/min
500
500
500
Rack position
R1(11.2)
Boost pressure
kPa
58.7
52
65.4
Boost pressure
mmHg
440
390
490
Test data Ex:
Governor adjustment
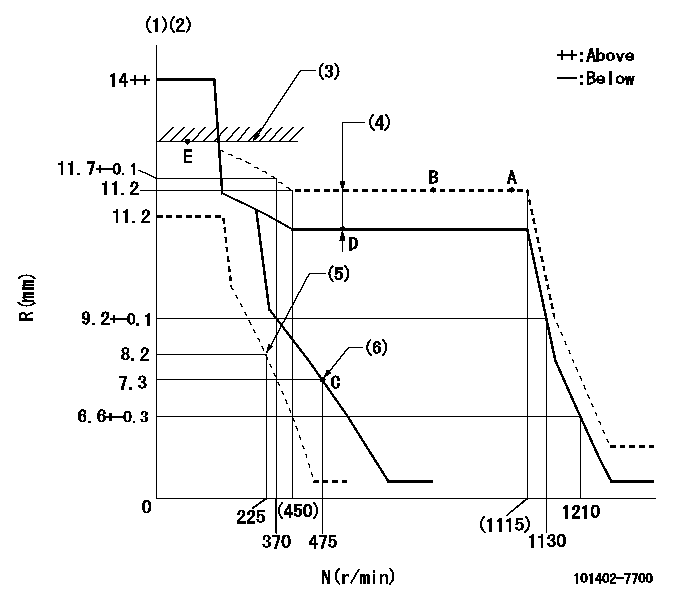
N:Pump speed
R:Rack position (mm)
(1)Target notch: K
(2)Tolerance for racks not indicated: +-0.05mm.
(3)RACK LIMIT
(4)Boost compensator stroke: BCL
(5)Set idle sub-spring
(6)Main spring setting
----------
K=10 BCL=1.5+-0.1mm
----------
----------
K=10 BCL=1.5+-0.1mm
----------
Speed control lever angle
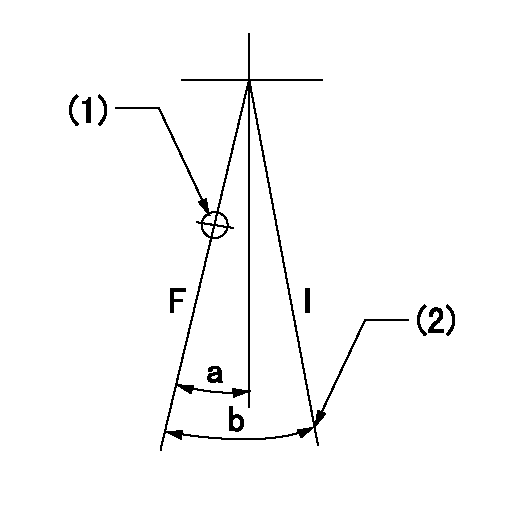
F:Full speed
I:Idle
(1)Use the hole at R = aa
(2)Stopper bolt setting
----------
aa=70mm
----------
a=7deg+-5deg b=20deg+-5deg
----------
aa=70mm
----------
a=7deg+-5deg b=20deg+-5deg
Stop lever angle

N:Pump normal
S:Stop the pump.
(1)Pump speed aa and rack position bb (to be sealed at delivery)
(2)Normal
----------
aa=0r/min bb=1-0.5mm
----------
a=32deg+-5deg b=(55deg)
----------
aa=0r/min bb=1-0.5mm
----------
a=32deg+-5deg b=(55deg)
0000001501 TAMPER PROOF

Tamperproofing-equipped boost compensator cover installation procedure
(A) After adjusting the boost compensator, tighten the bolts to remove the heads.
(1)Before adjusting the governor and the boost compensator, tighten the screw to the specified torque.
(Tightening torque T = T1 maximum)
(2)After adjusting the governor and the boost compensator, tighten to the specified torque to break off the bolt heads.
(Tightening torque T = T2)
----------
T1=2.5N-m(0.25kgf-m) T2=2.9~4.4N-m(0.3~0.45kgf-m)
----------
----------
T1=2.5N-m(0.25kgf-m) T2=2.9~4.4N-m(0.3~0.45kgf-m)
----------
Timing setting

(1)Pump vertical direction
(2)Position of gear mark 'CC' at No 1 cylinder's beginning of injection
(3)B.T.D.C.: aa
(4)-
----------
aa=9deg
----------
a=(100deg)
----------
aa=9deg
----------
a=(100deg)
Information:
Shunt-Type Cooling System
A shunt-type cooling system for the engine is recommended. A shunt-type cooling system radiator has a normal top tank (9) above the radiator core (10) and an expansion tank (2) above (any location) the top tank.An air and coolant tube (7) allows excess air and coolant in the radiator top tank to flow into the expansion tank. The expansion tank has a shunt line (3) which connects to the water pump (11) inlet. The shunt system maintains a positive head of coolant at the pump inlet to prevent cavitation in the pump under all operating conditions.When initially filling the cooling system, the coolant in expansion tank (2) flows through shunt line (3) to the water pump inlet, flows through pump (11), and fills engine cylinder block (13) from the bottom. Coolant flowing into the bottom of the block forces the air out through the top of temperature regulator housing (4), through tube (7) into expansion tank (2).It is a good procedure, after filling the system, to immediately start the engine and make certain the cooling system is full after a few minutes of engine operation. The operating water pump circulates the coolant through the engine, to drive out any air that could have been trapped in the engine. It may be necessary to add more coolant to fill the system.
SHUNT-TYPE RADIATOR COOLING SYSTEM-SCHEMATIC (Temperature regulator partially open)
1-Radiator cap (pressure regulating valve). 2-Expansion tank. 3-Shunt line tube. 4-Temperature regulator (thermostat) housing. 5-Cylinder liners (six). 6-Cylinder head. 7-Air and coolant bleed tube (between radiator top tank and expansion tank). 8-Radiator coolant bypass tube. 9-Radiator top tank. 10-Radiator core. 11-Water pump. 12-Engine lubricating oil cooler. 13-Cylinder block.Cylinder Head
CYLINDER HEAD-END VIEW
1-Precombustion chamber (six). 2-Spring (twelve). 3-Lock (twenty four). 4-Rotocoil assembly (twelve). 5-Rocker arm (twelve). 6-Push rod (twelve). 7-Air inlet manifold (in head). 8-Valve seat insert (six inlet, six exhaust). 9-Valve (six inlet, six exhaust).This overhead valve (OHV) cylinder head has one inlet and one exhaust valve for each engine cylinder. Rocker arms (5) are operated by the camshaft, in the engine cylinder block, cam followers (lifters) and push rods (6) which open and close valves (9) at the proper time. Each rocker arm has an adjustable contact to obtain the recommended valve lash (valve clearance). Each valve spring (2), to close a valve, is retained by locks (3) and a rotocoil assembly (4). The rotocoil will rotate a valve stem approximately one third of a degree each time the valve opens and closes. This will rotate the valve about one revolution per minute when the engine is operating at full load RPM.The valve bushings (guides) and valve seat inserts (8) can be removed, if necessary, and new ones installed. The valve seats are ground at 30° angles. The high heat resistant steel inlet valves and stellite exhaust valves are gound slightly less (about one fourth of a degree) than 30° angles. The interference angles between the valves and valve seats provide for better seating for longer periods of time.The inlet
A shunt-type cooling system for the engine is recommended. A shunt-type cooling system radiator has a normal top tank (9) above the radiator core (10) and an expansion tank (2) above (any location) the top tank.An air and coolant tube (7) allows excess air and coolant in the radiator top tank to flow into the expansion tank. The expansion tank has a shunt line (3) which connects to the water pump (11) inlet. The shunt system maintains a positive head of coolant at the pump inlet to prevent cavitation in the pump under all operating conditions.When initially filling the cooling system, the coolant in expansion tank (2) flows through shunt line (3) to the water pump inlet, flows through pump (11), and fills engine cylinder block (13) from the bottom. Coolant flowing into the bottom of the block forces the air out through the top of temperature regulator housing (4), through tube (7) into expansion tank (2).It is a good procedure, after filling the system, to immediately start the engine and make certain the cooling system is full after a few minutes of engine operation. The operating water pump circulates the coolant through the engine, to drive out any air that could have been trapped in the engine. It may be necessary to add more coolant to fill the system.
SHUNT-TYPE RADIATOR COOLING SYSTEM-SCHEMATIC (Temperature regulator partially open)
1-Radiator cap (pressure regulating valve). 2-Expansion tank. 3-Shunt line tube. 4-Temperature regulator (thermostat) housing. 5-Cylinder liners (six). 6-Cylinder head. 7-Air and coolant bleed tube (between radiator top tank and expansion tank). 8-Radiator coolant bypass tube. 9-Radiator top tank. 10-Radiator core. 11-Water pump. 12-Engine lubricating oil cooler. 13-Cylinder block.Cylinder Head
CYLINDER HEAD-END VIEW
1-Precombustion chamber (six). 2-Spring (twelve). 3-Lock (twenty four). 4-Rotocoil assembly (twelve). 5-Rocker arm (twelve). 6-Push rod (twelve). 7-Air inlet manifold (in head). 8-Valve seat insert (six inlet, six exhaust). 9-Valve (six inlet, six exhaust).This overhead valve (OHV) cylinder head has one inlet and one exhaust valve for each engine cylinder. Rocker arms (5) are operated by the camshaft, in the engine cylinder block, cam followers (lifters) and push rods (6) which open and close valves (9) at the proper time. Each rocker arm has an adjustable contact to obtain the recommended valve lash (valve clearance). Each valve spring (2), to close a valve, is retained by locks (3) and a rotocoil assembly (4). The rotocoil will rotate a valve stem approximately one third of a degree each time the valve opens and closes. This will rotate the valve about one revolution per minute when the engine is operating at full load RPM.The valve bushings (guides) and valve seat inserts (8) can be removed, if necessary, and new ones installed. The valve seats are ground at 30° angles. The high heat resistant steel inlet valves and stellite exhaust valves are gound slightly less (about one fourth of a degree) than 30° angles. The interference angles between the valves and valve seats provide for better seating for longer periods of time.The inlet