Information injection-pump assembly
BOSCH
9 400 611 175
9400611175
ZEXEL
101402-7630
1014027630
ISUZU
8972278280
8972278280
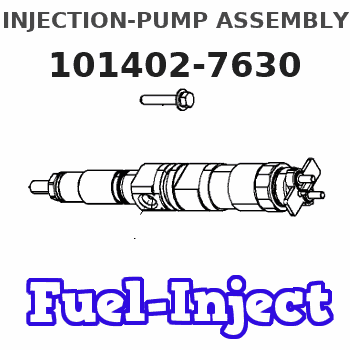
Rating:
Service parts 101402-7630 INJECTION-PUMP ASSEMBLY:
1.
_
5.
AUTOM. ADVANCE MECHANIS
6.
COUPLING PLATE
8.
_
9.
_
11.
Nozzle and Holder
8-97222-170-0
12.
Open Pre:MPa(Kqf/cm2)
18.1{185}
15.
NOZZLE SET
Include in #1:
101402-7630
as INJECTION-PUMP ASSEMBLY
Include in #2:
104748-0232
as _
Cross reference number
BOSCH
9 400 611 175
9400611175
ZEXEL
101402-7630
1014027630
ISUZU
8972278280
8972278280
Zexel num
Bosch num
Firm num
Name
9 400 611 175
8972278280 ISUZU
INJECTION-PUMP ASSEMBLY
4BG1-T * K 14BC PE4A,5A, PE
4BG1-T * K 14BC PE4A,5A, PE
Calibration Data:
Adjustment conditions
Test oil
1404 Test oil ISO4113 or {SAEJ967d}
1404 Test oil ISO4113 or {SAEJ967d}
Test oil temperature
degC
40
40
45
Nozzle and nozzle holder
105780-8140
Bosch type code
EF8511/9A
Nozzle
105780-0000
Bosch type code
DN12SD12T
Nozzle holder
105780-2080
Bosch type code
EF8511/9
Opening pressure
MPa
17.2
Opening pressure
kgf/cm2
175
Injection pipe
Outer diameter - inner diameter - length (mm) mm 6-2-600
Outer diameter - inner diameter - length (mm) mm 6-2-600
Overflow valve
131424-4920
Overflow valve opening pressure
kPa
127
107
147
Overflow valve opening pressure
kgf/cm2
1.3
1.1
1.5
Tester oil delivery pressure
kPa
157
157
157
Tester oil delivery pressure
kgf/cm2
1.6
1.6
1.6
RED4 control unit part number
407915-0
590
RED4 rack sensor specifications
mm
19
Direction of rotation (viewed from drive side)
Right R
Right R
Injection timing adjustment
Direction of rotation (viewed from drive side)
Right R
Right R
Injection order
1-3-4-2
Pre-stroke
mm
3.4
3.35
3.45
Beginning of injection position
Drive side NO.1
Drive side NO.1
Difference between angles 1
Cal 1-3 deg. 90 89.5 90.5
Cal 1-3 deg. 90 89.5 90.5
Difference between angles 2
Cal 1-4 deg. 180 179.5 180.5
Cal 1-4 deg. 180 179.5 180.5
Difference between angles 3
Cyl.1-2 deg. 270 269.5 270.5
Cyl.1-2 deg. 270 269.5 270.5
Injection quantity adjustment
Rack position
(7.7)
PWM
%
31.4
Pump speed
r/min
1050
1050
1050
Average injection quantity
mm3/st.
70.5
69.4
71.6
Max. variation between cylinders
%
0
-2
2
Basic
*
Injection quantity adjustment_02
Rack position
(5.8)
PWM
%
20.9+-2.
8
Pump speed
r/min
500
500
500
Average injection quantity
mm3/st.
11
9.6
12.4
Max. variation between cylinders
%
0
-14
14
Injection quantity adjustment_03
Rack position
(10.2)
PWM
%
(45.6)
Pump speed
r/min
100
100
100
Average injection quantity
mm3/st.
125
120
130
Rack limit
*
Test data Ex:
Speed control lever angle
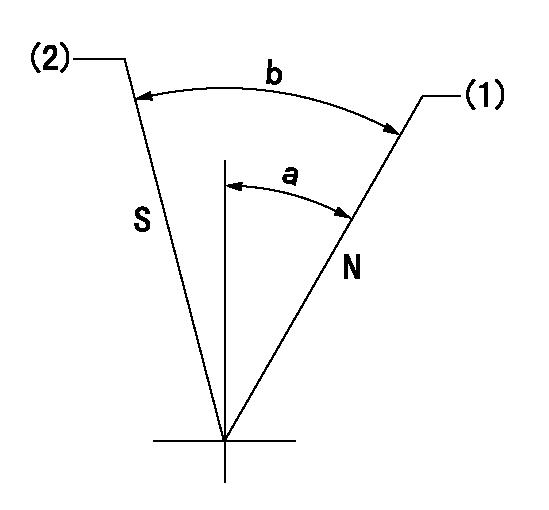
N:Pump normal
S:Stop the pump.
(1)Rack position = aa
(2)Rack position bb
----------
aa=20mm bb=1mm
----------
a=27deg+-5deg b=37deg+-5deg
----------
aa=20mm bb=1mm
----------
a=27deg+-5deg b=37deg+-5deg
0000000901

(1)Pump vertical direction
(2)Position of gear mark 'CC' at No 1 cylinder's beginning of injection
(3)B.T.D.C.: aa
(4)-
----------
aa=9deg
----------
a=(100deg)
----------
aa=9deg
----------
a=(100deg)
Stop lever angle

(PWM) Pulse width modulation (%)
(R) Rack position (mm)
Rack sensor output characteristics
1. Rack limit adjustment
(1)Measure the rack position R2 for PWM a2%.
(2)Confirm that it is within the range R2 = 15+-1 mm.
(3)Measure the rack position R1 at PWM a %.
(4)Confirm that it is within the range R2 - R1 = 10+-0.1 mm.
2. Check the limp home operation.
(1)Move the switch box's limp home switch to the limp home side.
(2)Confirm rack position L1 (mm ) and L2 (mm) for PWM in the above table.
3. Check the pull down operation.
(1)Confirm that the rack position is 19 mm at PWM B%.
(2)In the conditions described in the above table, move the switch box's pull down switch to the pull down side and confirm that the rack position momentarily becomes 1 mm or less.
----------
a1=16.25% a2=72.5% L1=1--mm L2=19++mm A=5 % B=95%
----------
----------
a1=16.25% a2=72.5% L1=1--mm L2=19++mm A=5 % B=95%
----------
Information:
WATER SLEEVE CLAMP
1. Clamp.3. Use water sleeve tool (2) to move water sleeve (3) into front cover.4. Remove the cylinder head retaining bolts (4) and (5).
MOVING WATER SLEEVE
2. 8S6692 Water Sleeve Tool. 3. Water sleeve.
CYLINDER HEAD
4. Bolts (four each head). 5. Bolts (eighteen each head).
Be sure fuel injection nozzles are removed before removing head. Nozzles extend through the head and nozzle tips can be broken off if nozzles are not removed from the head.
5. Install two 1P7407 Lifting Eye Bolts in the cylinder head. Attach a hoist and remove the cylinder head assembly, the weight is approx. 85 lbs. (39 kg).
REMOVING CYLINDER HEADInstall Cylinder Head Assemblies
1. Clean the mating surfaces of the cylinder head and cylinder block. Install new cylinder head gasket, clean and dry. Clean bores in cylinder head and inspect and lubricate O-rings for water sleeves.2. Install two 1P7407 Lifting Eye Bolts in the cylinder head. Attach a hoist and install the cylinder head assembly. Coat the cylinder head retaining bolt threads with 9M3710 Anti-Seize Compound. Install the bolts and tighten in the following Step sequence. Step A: Tighten bolts 1 through 18 in numerical order to 60 10 lb. ft. (8.3 1.4 mkg).Step B: Retighten bolts 1 through 18 in numerical order to 95 5 lb. ft. (13.1 0.7 mkg).Step C: Finally tighten bolts 1 through 18 in numerical order (hand tighten only) to 95 5 lb. ft. (13.1 0.7 mkg).Step D: Tighten bolts 19, 20, 21, and 22 in numerical order to 32 5 lb. ft. (4.4 0.7 mkg).
CYLINDER HEAD BOLT LOCATION3. Use the 8S6692 Water Sleeve Tool to slide water sleeve into cylinder head and install clamp.Disassemble Cylinder Head
1. Place head on the FT806 Cylinder Head Bench or the 8S6691 Cylinder Head Stand. Use FT967 Adapter Plates to mount head on the FT806 Cylinder Head Bench.2. Use a 5S1330 or 7F4291 Valve Spring Compressor (1) to remove the valves and valve springs.
REMOVING VALVES
1. 5S1330 Valve Spring Compressor illustrated.3. Use the 8S2263 Valve Spring Tester to check valve spring tension.4. The exhaust valve seats have replaceable inserts. To remove, use the 8S7170 Valve Seat Insert Puller Group.
REMOVING EXHAUST VALVE SEAT INSERTS The valve guides are cast in the cylinder head. If the guides show wear or bellmouthing, they can be restored to original tolerances through knurling.Assemble Cylinder Head
1. Lubricate valve stems with clean engine oil (SAE 30) before installing valves into cylinder head. Earlier engines use a valve spring retainer and washer combination instead of the one piece valve spring retainer shown.
CYLINDER HEAD