Information injection-pump assembly
BOSCH
9 400 613 961
9400613961
ZEXEL
101402-7341
1014027341
ISUZU
8972034761
8972034761
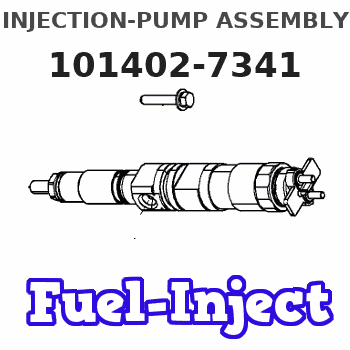
Rating:
Service parts 101402-7341 INJECTION-PUMP ASSEMBLY:
1.
_
5.
AUTOM. ADVANCE MECHANIS
6.
COUPLING PLATE
8.
_
9.
_
11.
Nozzle and Holder
8-97030-285-1
12.
Open Pre:MPa(Kqf/cm2)
14.7{150}
15.
NOZZLE SET
Cross reference number
BOSCH
9 400 613 961
9400613961
ZEXEL
101402-7341
1014027341
ISUZU
8972034761
8972034761
Zexel num
Bosch num
Firm num
Name
101402-7341
9 400 613 961
8972034761 ISUZU
INJECTION-PUMP ASSEMBLY
4BG1 K 14BC INJECTION PUMP ASSY PE4A,5A, PE
4BG1 K 14BC INJECTION PUMP ASSY PE4A,5A, PE
Calibration Data:
Adjustment conditions
Test oil
1404 Test oil ISO4113 or {SAEJ967d}
1404 Test oil ISO4113 or {SAEJ967d}
Test oil temperature
degC
40
40
45
Nozzle and nozzle holder
105780-8140
Bosch type code
EF8511/9A
Nozzle
105780-0000
Bosch type code
DN12SD12T
Nozzle holder
105780-2080
Bosch type code
EF8511/9
Opening pressure
MPa
17.2
Opening pressure
kgf/cm2
175
Injection pipe
Outer diameter - inner diameter - length (mm) mm 6-2-600
Outer diameter - inner diameter - length (mm) mm 6-2-600
Overflow valve
131424-4920
Overflow valve opening pressure
kPa
127
107
147
Overflow valve opening pressure
kgf/cm2
1.3
1.1
1.5
Tester oil delivery pressure
kPa
157
157
157
Tester oil delivery pressure
kgf/cm2
1.6
1.6
1.6
Direction of rotation (viewed from drive side)
Right R
Right R
Injection timing adjustment
Direction of rotation (viewed from drive side)
Right R
Right R
Injection order
1-3-4-2
Pre-stroke
mm
3.4
3.35
3.45
Beginning of injection position
Drive side NO.1
Drive side NO.1
Difference between angles 1
Cal 1-3 deg. 90 89.5 90.5
Cal 1-3 deg. 90 89.5 90.5
Difference between angles 2
Cal 1-4 deg. 180 179.5 180.5
Cal 1-4 deg. 180 179.5 180.5
Difference between angles 3
Cyl.1-2 deg. 270 269.5 270.5
Cyl.1-2 deg. 270 269.5 270.5
Injection quantity adjustment
Adjusting point
A
Rack position
8.8
Pump speed
r/min
1050
1050
1050
Average injection quantity
mm3/st.
77.5
76.4
78.6
Max. variation between cylinders
%
0
-2
2
Basic
*
Fixing the lever
*
Injection quantity adjustment_02
Adjusting point
C
Rack position
6.3+-0.5
Pump speed
r/min
425
425
425
Average injection quantity
mm3/st.
9
7.6
10.4
Max. variation between cylinders
%
0
-14
14
Fixing the rack
*
Injection quantity adjustment_03
Adjusting point
D
Rack position
-
Pump speed
r/min
100
100
100
Average injection quantity
mm3/st.
100
100
110
Fixing the lever
*
Rack limit
*
Test data Ex:
Governor adjustment
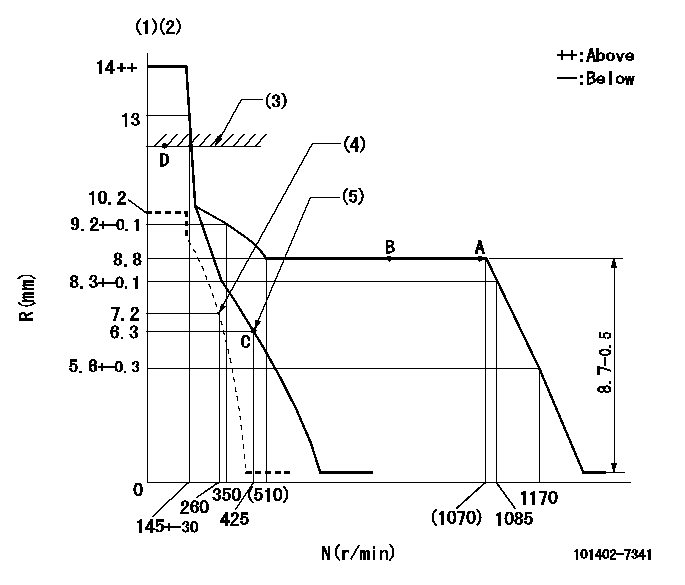
N:Pump speed
R:Rack position (mm)
(1)Target notch: K
(2)Tolerance for racks not indicated: +-0.05mm.
(3)RACK LIMIT
(4)Set idle sub-spring
(5)Main spring setting
----------
K=14
----------
----------
K=14
----------
Speed control lever angle
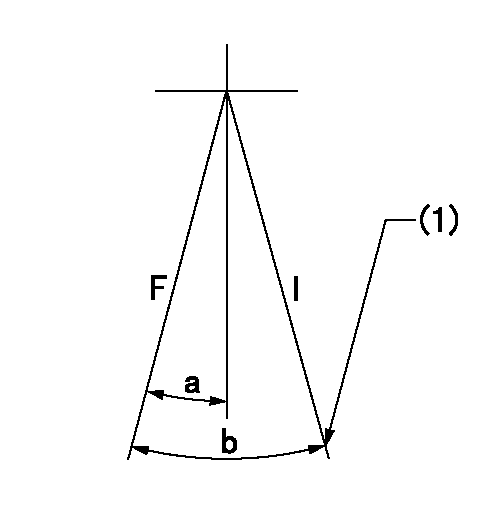
F:Full speed
I:Idle
(1)Stopper bolt setting
----------
----------
a=9deg+-5deg b=22deg+-5deg
----------
----------
a=9deg+-5deg b=22deg+-5deg
Stop lever angle

N:Pump normal
S:Stop the pump.
(1)Normal
----------
----------
a=12deg+-5deg b=46deg+-5deg
----------
----------
a=12deg+-5deg b=46deg+-5deg
Timing setting

(1)Pump vertical direction
(2)Position of gear mark 'CC' at No 1 cylinder's beginning of injection
(3)B.T.D.C.: aa
(4)-
----------
aa=15deg
----------
a=(100deg)
----------
aa=15deg
----------
a=(100deg)
Information:
Exhaust Manifold Removal And Installation
1-Inlet air pipe. 2-Exhaust elbow. 3-Turbocharger oil drain line. 4-Turbocharger oil supply line. 5-Turbocharger. 6-Fuel injection lines (six). 7-Heat shield. 8-Exhaust manifold (three sections).Turbocharger Removal And Installation
Refer to SERVICE GUIDE for Preliminary Information.
1-Exhaust elbow. 2-Turbocharger oil supply line. 3-Bolts and nuts (two each). 4-Bolts, locks and nuts (four each). 5-Turbocharger oil drain line. 6-Inlet air pipe. Apply 9M3710 Anti-Seize Compound to threads of bolts (3 and 4) when installing turbocharger.Turbocharger Disassembly And Assembly
8S9944 Turbine Holder.1,3,5 Remove nut (1). Position the compressor end of housing (5) in an oil bath so only impeller (3) is immersed in oil. Heat impeller to 350° F. (176° C.) for not longer than ten minutes. Remove unit from oil bath and press the shaft and turbine wheel from impeller (3).1,3,5 At installation, heat impeller (3) to a maximum of 350°F. (176°C.) for not longer than ten minutes and proceed as follows: For ease of impeller installation, place the turbine wheel end of center housing (5) in an 8S9944 Turbine Holder.a. Immediately install impeller (3) on shaft, install nut (1) and tighten it to 120 lb. in. (138,4 cm.kg).b. Allow impeller to cool to less than 150°F. (65, 49°C.) and remove nut (1).c. Clean and smooth the washer face of nut (1). Lightly oil the threads of turbine shaft and nut and install the nut.d. Tighten nut (1) to 20 lb. in. (23,0 cm.kg), then tighten an additional 120°.2 Coat threads with 9M3710 Anti-Seize Compound.4,5 Install thrust plate assembly (4) so oil hole aligns with oil hole in housing (5).
1-Inlet air pipe. 2-Exhaust elbow. 3-Turbocharger oil drain line. 4-Turbocharger oil supply line. 5-Turbocharger. 6-Fuel injection lines (six). 7-Heat shield. 8-Exhaust manifold (three sections).Turbocharger Removal And Installation
Refer to SERVICE GUIDE for Preliminary Information.
1-Exhaust elbow. 2-Turbocharger oil supply line. 3-Bolts and nuts (two each). 4-Bolts, locks and nuts (four each). 5-Turbocharger oil drain line. 6-Inlet air pipe. Apply 9M3710 Anti-Seize Compound to threads of bolts (3 and 4) when installing turbocharger.Turbocharger Disassembly And Assembly
8S9944 Turbine Holder.1,3,5 Remove nut (1). Position the compressor end of housing (5) in an oil bath so only impeller (3) is immersed in oil. Heat impeller to 350° F. (176° C.) for not longer than ten minutes. Remove unit from oil bath and press the shaft and turbine wheel from impeller (3).1,3,5 At installation, heat impeller (3) to a maximum of 350°F. (176°C.) for not longer than ten minutes and proceed as follows: For ease of impeller installation, place the turbine wheel end of center housing (5) in an 8S9944 Turbine Holder.a. Immediately install impeller (3) on shaft, install nut (1) and tighten it to 120 lb. in. (138,4 cm.kg).b. Allow impeller to cool to less than 150°F. (65, 49°C.) and remove nut (1).c. Clean and smooth the washer face of nut (1). Lightly oil the threads of turbine shaft and nut and install the nut.d. Tighten nut (1) to 20 lb. in. (23,0 cm.kg), then tighten an additional 120°.2 Coat threads with 9M3710 Anti-Seize Compound.4,5 Install thrust plate assembly (4) so oil hole aligns with oil hole in housing (5).
Have questions with 101402-7341?
Group cross 101402-7341 ZEXEL
Isuzu
101402-7341
9 400 613 961
8972034761
INJECTION-PUMP ASSEMBLY
4BG1
4BG1