Information injection-pump assembly
ZEXEL
101402-3821
1014023821
KOMATSU
6732711140
6732711140
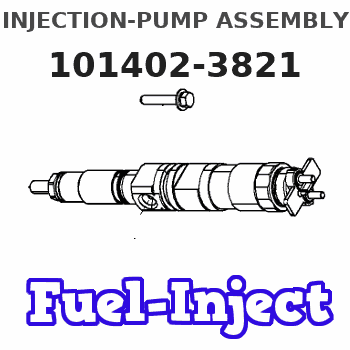
Rating:
Service parts 101402-3821 INJECTION-PUMP ASSEMBLY:
1.
_
5.
AUTOM. ADVANCE MECHANIS
6.
COUPLING PLATE
7.
COUPLING PLATE
8.
_
9.
_
10.
NOZZLE AND HOLDER ASSY
11.
Nozzle and Holder
12.
Open Pre:MPa(Kqf/cm2)
21.6{220}
13.
NOZZLE-HOLDER
14.
NOZZLE
15.
NOZZLE SET
Cross reference number
ZEXEL
101402-3821
1014023821
KOMATSU
6732711140
6732711140
Zexel num
Bosch num
Firm num
Name
Calibration Data:
Adjustment conditions
Test oil
1404 Test oil ISO4113 or {SAEJ967d}
1404 Test oil ISO4113 or {SAEJ967d}
Test oil temperature
degC
40
40
45
Nozzle and nozzle holder
105780-8140
Bosch type code
EF8511/9A
Nozzle
105780-0000
Bosch type code
DN12SD12T
Nozzle holder
105780-2080
Bosch type code
EF8511/9
Opening pressure
MPa
17.2
Opening pressure
kgf/cm2
175
Injection pipe
Outer diameter - inner diameter - length (mm) mm 6-2-600
Outer diameter - inner diameter - length (mm) mm 6-2-600
Overflow valve
131424-3420
Overflow valve opening pressure
kPa
255
221
289
Overflow valve opening pressure
kgf/cm2
2.6
2.25
2.95
Tester oil delivery pressure
kPa
157
157
157
Tester oil delivery pressure
kgf/cm2
1.6
1.6
1.6
Direction of rotation (viewed from drive side)
Right R
Right R
Injection timing adjustment
Direction of rotation (viewed from drive side)
Right R
Right R
Injection order
1-3-4-2
Pre-stroke
mm
2.5
2.45
2.55
Beginning of injection position
Drive side NO.1
Drive side NO.1
Difference between angles 1
Cal 1-3 deg. 90 89.5 90.5
Cal 1-3 deg. 90 89.5 90.5
Difference between angles 2
Cal 1-4 deg. 180 179.5 180.5
Cal 1-4 deg. 180 179.5 180.5
Difference between angles 3
Cyl.1-2 deg. 270 269.5 270.5
Cyl.1-2 deg. 270 269.5 270.5
Injection quantity adjustment
Adjusting point
A
Rack position
11.5
Pump speed
r/min
1200
1200
1200
Average injection quantity
mm3/st.
91.5
90.5
92.5
Max. variation between cylinders
%
0
-2.5
2.5
Basic
*
Fixing the lever
*
Boost pressure
kPa
44
44
Boost pressure
mmHg
330
330
Hydraulic cylinder ON
*
Injection quantity adjustment_02
Adjusting point
C
Rack position
8.6+-0.5
Pump speed
r/min
410
410
410
Average injection quantity
mm3/st.
8
7
9
Max. variation between cylinders
%
0
-15
15
Fixing the rack
*
Boost pressure
kPa
0
0
0
Boost pressure
mmHg
0
0
0
Hydraulic cylinder ON
*
Injection quantity adjustment_03
Adjusting point
D
Rack position
-
Pump speed
r/min
100
100
100
Average injection quantity
mm3/st.
65
65
75
Fixing the lever
*
Boost pressure
kPa
0
0
0
Boost pressure
mmHg
0
0
0
Hydraulic cylinder OFF
*
Rack limit
*
Boost compensator adjustment
Pump speed
r/min
800
800
800
Rack position
R1-0.65
Boost pressure
kPa
20
18.7
21.3
Boost pressure
mmHg
150
140
160
Boost compensator adjustment_02
Pump speed
r/min
800
800
800
Rack position
R1(11.5)
Boost pressure
kPa
30.7
24
37.4
Boost pressure
mmHg
230
180
280
Test data Ex:
Governor adjustment
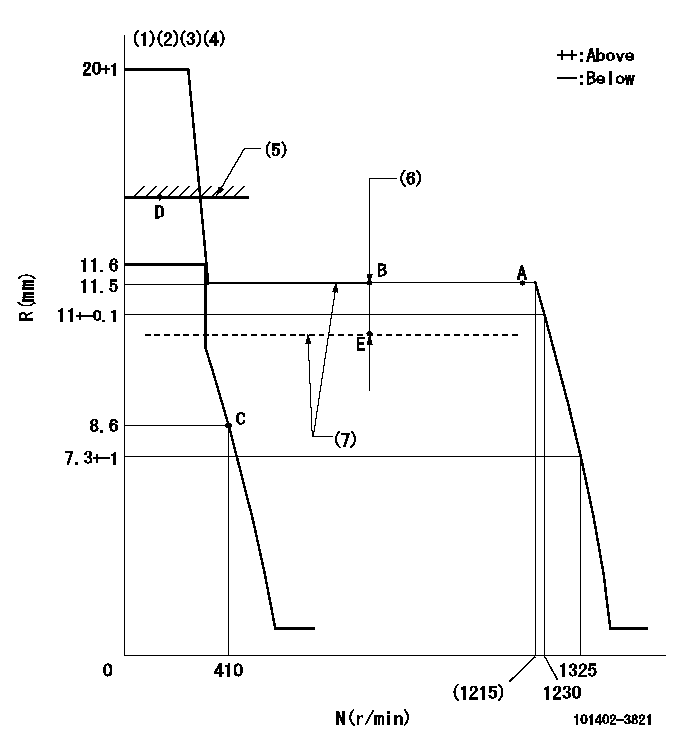
N:Pump speed
R:Rack position (mm)
(1)Target notch: K
(2)Tolerance for racks not indicated: +-0.05mm.
(3)The torque control spring does not operate.
(4)Adjust the secondary timing before adjusting the governor.
(5)RACK LIMIT (When hydraulic cylinder is OFF)
(6)Boost compensator stroke: BCL
(7)When the hydraulic cylinder is ON (P1)
----------
K=10 BCL=0.65+-0.1mm P1=((392)kPa{(4)kgf/cm2})
----------
----------
K=10 BCL=0.65+-0.1mm P1=((392)kPa{(4)kgf/cm2})
----------
Speed control lever angle
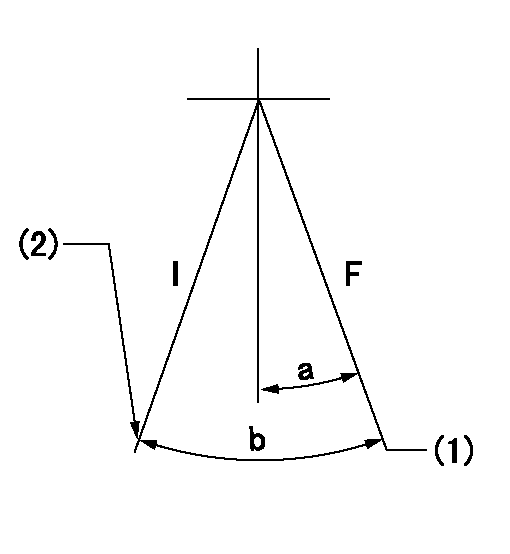
F:Full speed
I:Idle
(1)-
(2)Stopper bolt setting
----------
----------
a=14deg+-5deg b=27deg+-5deg
----------
----------
a=14deg+-5deg b=27deg+-5deg
Stop lever angle

N:Pump normal
S:Stop the pump.
----------
----------
a=0deg+-5deg b=53deg+-5deg
----------
----------
a=0deg+-5deg b=53deg+-5deg
Timing setting

(1)Pump vertical direction
(2)Key groove position at No. 1 cylinder's beginning of injection position (at BTDC: aa).
(3)Position of the key groove of the No. 1 cylinder at B.T.D.C. bb (fix the governor flyweight at this position for delivery).
(4)B.T.D.C.: aa
(5)At second timing adjustment, set the camshaft at the * position and tighten the flyweight locknut.
(6)Align the flyweight's timing gear position with the lockpin groove and then fully tighten the flyweight to the camshaft.
(7)Remove the lock pin and adjust the governor. Reinstall the lock pin to fix the flyweight for delivery.
----------
aa=15.5deg bb=0deg
----------
a=54deg54min+-3deg b=7deg45min+-30min
----------
aa=15.5deg bb=0deg
----------
a=54deg54min+-3deg b=7deg45min+-30min
Information:
The information supplied in this service letter may not be valid after the termination date of this program. Do not perform the work outlined in this Service Letter after the termination date without first contacting your Caterpillar product analyst.
This Program can only be administered after a failure occurs. The decision whether to apply the Program is made by the dealer. When reporting the repair, use "PS5331" as the Part Number and "7755" as the Group Number. Use "96" as the Warranty Claim Description Code and use "Z" as the SIMS Description Code.
Termination Date
October 31, 1998Problem
Some 3116 and 3126 HEUI Engines may have excessive oil consumption as a result of oil leaking past the intensifier piston o-ring inside the injector. Engine oil consumption becomes excessive and may increase rapidly. There are no traditional signs of oil consumption, smoke, blow-by, etc. The engine has no performance problem, has good power and normal exhaust smoke.
The problem seems to be very low frequency and is not batch related.
Affected Product
Model & Identification Number
3116 (8WL1-Up)
3126 (1WM1-Up 4ES1-Up )
Parts Needed
3116 Engines6 - 1162784 Injectors (for 170 Hp)6 - 1166706 Injectors (for 185, 195, 215, 230, 250 and 275 Hp) 3126 Engines6 - 0R4970 Injectors (for 230, 250, 275, 300 and 330 Hp)6 - 0R4972 Injectors (for 175, 190 and 210 Hp)Action Required
See the attached rework procedure.
Service Claim Allowances
Labor Hour Breakdown TK = TopKickMC = Medium Hood ConventionalClaim 1290-500 for an additional 1.6 hours if the repair is made in a motor home chassis, cab type (RV), or bus chassis, cab type (BU).
Parts Disposition
TEPS/MEPS Dealers must return the affected part(s) to their Caterpillar dealer.
Parts must be returned undamaged in the original shipping boxes to:
Caterpillar Inc.
Attn: Michael Mosley - PS5331
8401 N. University
Peoria, Illinois 61615
Injectors must be sealed in a plastic bag to prevent fuel from leaking out during shipment.
A clear, legible copy of the service report in a plastic page protector must be included in the box with the returned injectors. The report must be packaged to arrive free of oil, grease and diesel fuel.
Attach.(1 - Rework Procedure)Rework Procedure
Check to see if PS8826 (Jumper-tube Rework) is to be applied to the affected engine. Perform PS8826 if it has not been performed prior to oil consumption test.
Document the oil consumption for 30 days using the attached Oil Consumption Test Sheet, Form Number 01-081227.
All of the following steps must be followed in order to establish base line data for oil consumption for full warranty reimbursement.
1. Change oil and filter at the beginning of the test to establish base line at normal change interval. Use CG-4 oil and new oil filter. Oil and filter are not claimable under this letter.
2. Refill with the proper amount of oil; 27liters/29 quarts, and 18 liters/19 quarts per the July 1997 Operations Maintenance Manual.3. Inspect for external leaks around the gaskets and the front and rear main seals.4. Inspect the air compressor air tanks for excess oil.5. Inspect the turbo oil drain line for excessive oil indicating seal leak.6. At the completion of
This Program can only be administered after a failure occurs. The decision whether to apply the Program is made by the dealer. When reporting the repair, use "PS5331" as the Part Number and "7755" as the Group Number. Use "96" as the Warranty Claim Description Code and use "Z" as the SIMS Description Code.
Termination Date
October 31, 1998Problem
Some 3116 and 3126 HEUI Engines may have excessive oil consumption as a result of oil leaking past the intensifier piston o-ring inside the injector. Engine oil consumption becomes excessive and may increase rapidly. There are no traditional signs of oil consumption, smoke, blow-by, etc. The engine has no performance problem, has good power and normal exhaust smoke.
The problem seems to be very low frequency and is not batch related.
Affected Product
Model & Identification Number
3116 (8WL1-Up)
3126 (1WM1-Up 4ES1-Up )
Parts Needed
3116 Engines6 - 1162784 Injectors (for 170 Hp)6 - 1166706 Injectors (for 185, 195, 215, 230, 250 and 275 Hp) 3126 Engines6 - 0R4970 Injectors (for 230, 250, 275, 300 and 330 Hp)6 - 0R4972 Injectors (for 175, 190 and 210 Hp)Action Required
See the attached rework procedure.
Service Claim Allowances
Labor Hour Breakdown TK = TopKickMC = Medium Hood ConventionalClaim 1290-500 for an additional 1.6 hours if the repair is made in a motor home chassis, cab type (RV), or bus chassis, cab type (BU).
Parts Disposition
TEPS/MEPS Dealers must return the affected part(s) to their Caterpillar dealer.
Parts must be returned undamaged in the original shipping boxes to:
Caterpillar Inc.
Attn: Michael Mosley - PS5331
8401 N. University
Peoria, Illinois 61615
Injectors must be sealed in a plastic bag to prevent fuel from leaking out during shipment.
A clear, legible copy of the service report in a plastic page protector must be included in the box with the returned injectors. The report must be packaged to arrive free of oil, grease and diesel fuel.
Attach.(1 - Rework Procedure)Rework Procedure
Check to see if PS8826 (Jumper-tube Rework) is to be applied to the affected engine. Perform PS8826 if it has not been performed prior to oil consumption test.
Document the oil consumption for 30 days using the attached Oil Consumption Test Sheet, Form Number 01-081227.
All of the following steps must be followed in order to establish base line data for oil consumption for full warranty reimbursement.
1. Change oil and filter at the beginning of the test to establish base line at normal change interval. Use CG-4 oil and new oil filter. Oil and filter are not claimable under this letter.
2. Refill with the proper amount of oil; 27liters/29 quarts, and 18 liters/19 quarts per the July 1997 Operations Maintenance Manual.3. Inspect for external leaks around the gaskets and the front and rear main seals.4. Inspect the air compressor air tanks for excess oil.5. Inspect the turbo oil drain line for excessive oil indicating seal leak.6. At the completion of