Information injection-pump assembly
ZEXEL
101402-3820
1014023820

Rating:
Service parts 101402-3820 INJECTION-PUMP ASSEMBLY:
1.
_
5.
AUTOM. ADVANCE MECHANIS
6.
COUPLING PLATE
7.
COUPLING PLATE
8.
_
9.
_
10.
NOZZLE AND HOLDER ASSY
11.
Nozzle and Holder
12.
Open Pre:MPa(Kqf/cm2)
21.6{220}
13.
NOZZLE-HOLDER
14.
NOZZLE
15.
NOZZLE SET
Cross reference number
ZEXEL
101402-3820
1014023820
Zexel num
Bosch num
Firm num
Name
101402-3820
INJECTION-PUMP ASSEMBLY
Calibration Data:
Adjustment conditions
Test oil
1404 Test oil ISO4113 or {SAEJ967d}
1404 Test oil ISO4113 or {SAEJ967d}
Test oil temperature
degC
40
40
45
Nozzle and nozzle holder
105780-8140
Bosch type code
EF8511/9A
Nozzle
105780-0000
Bosch type code
DN12SD12T
Nozzle holder
105780-2080
Bosch type code
EF8511/9
Opening pressure
MPa
17.2
Opening pressure
kgf/cm2
175
Injection pipe
Outer diameter - inner diameter - length (mm) mm 6-2-600
Outer diameter - inner diameter - length (mm) mm 6-2-600
Overflow valve
131424-3420
Overflow valve opening pressure
kPa
255
221
289
Overflow valve opening pressure
kgf/cm2
2.6
2.25
2.95
Tester oil delivery pressure
kPa
157
157
157
Tester oil delivery pressure
kgf/cm2
1.6
1.6
1.6
Direction of rotation (viewed from drive side)
Right R
Right R
Injection timing adjustment
Direction of rotation (viewed from drive side)
Right R
Right R
Injection order
1-3-4-2
Pre-stroke
mm
2.5
2.45
2.55
Beginning of injection position
Drive side NO.1
Drive side NO.1
Difference between angles 1
Cal 1-3 deg. 90 89.5 90.5
Cal 1-3 deg. 90 89.5 90.5
Difference between angles 2
Cal 1-4 deg. 180 179.5 180.5
Cal 1-4 deg. 180 179.5 180.5
Difference between angles 3
Cyl.1-2 deg. 270 269.5 270.5
Cyl.1-2 deg. 270 269.5 270.5
Injection quantity adjustment
Adjusting point
A
Rack position
9.8
Pump speed
r/min
1200
1200
1200
Average injection quantity
mm3/st.
69.5
68.5
70.5
Max. variation between cylinders
%
0
-2.5
2.5
Basic
*
Fixing the lever
*
Boost pressure
kPa
48.7
48.7
Boost pressure
mmHg
365
365
Hydraulic cylinder ON
*
Injection quantity adjustment_02
Adjusting point
C
Rack position
8.5+-0.5
Pump speed
r/min
385
385
385
Average injection quantity
mm3/st.
8
7
9
Max. variation between cylinders
%
0
-15
15
Fixing the rack
*
Boost pressure
kPa
0
0
0
Boost pressure
mmHg
0
0
0
Hydraulic cylinder ON
*
Injection quantity adjustment_03
Adjusting point
D
Rack position
-
Pump speed
r/min
100
100
100
Average injection quantity
mm3/st.
85
85
95
Fixing the lever
*
Boost pressure
kPa
0
0
0
Boost pressure
mmHg
0
0
0
Hydraulic cylinder OFF
*
Rack limit
*
Boost compensator adjustment
Pump speed
r/min
800
800
800
Rack position
9.6
Boost pressure
kPa
24.7
23.4
26
Boost pressure
mmHg
185
175
195
Boost compensator adjustment_02
Pump speed
r/min
800
800
800
Rack position
10.6
Boost pressure
kPa
38
34
42
Boost pressure
mmHg
285
255
315
Test data Ex:
Governor adjustment
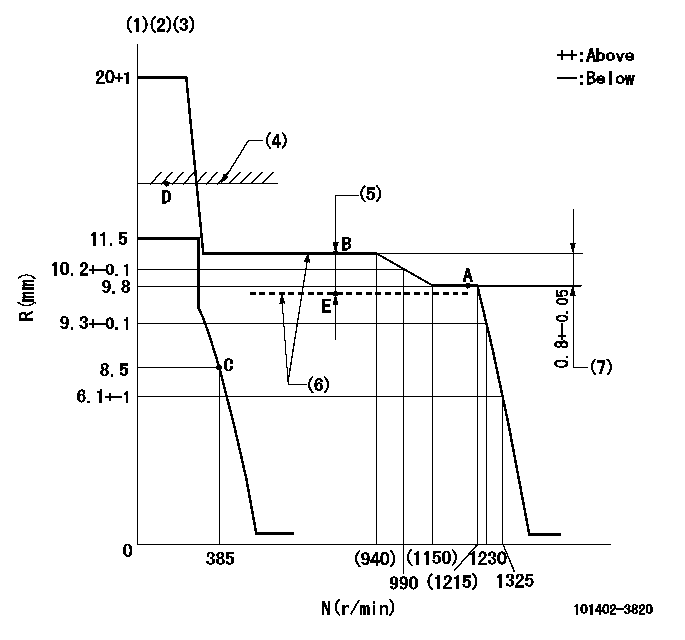
N:Pump speed
R:Rack position (mm)
(1)Notch fixed: K
(2)Tolerance for racks not indicated: +-0.05mm.
(3)Adjust the secondary timing before adjusting the governor.
(4)RACK LIMIT (When hydraulic cylinder is OFF)
(5)Boost compensator stroke: BCL
(6)When hydraulic cylinder ON: P1
(7)Rack difference between N = N1 and N = N2
----------
K=13 BCL=1+-0.1mm P1=((392)kPa{(4)kgf/cm2}) N1=1200r/min N2=800r/min
----------
----------
K=13 BCL=1+-0.1mm P1=((392)kPa{(4)kgf/cm2}) N1=1200r/min N2=800r/min
----------
Speed control lever angle

F:Full speed
I:Idle
(1)Stopper bolt setting
----------
----------
a=21deg+-5deg b=23deg+-5deg
----------
----------
a=21deg+-5deg b=23deg+-5deg
Stop lever angle
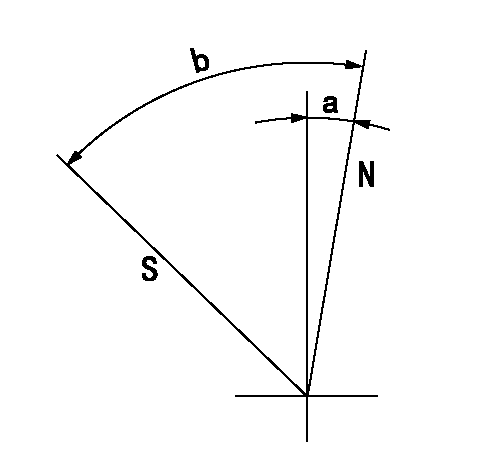
N:Pump normal
S:Stop the pump.
----------
----------
a=0deg+-5deg b=53deg+-5deg
----------
----------
a=0deg+-5deg b=53deg+-5deg
Timing setting

(1)Pump vertical direction
(2)Key groove position at No. 1 cylinder's beginning of injection position (at BTDC: aa).
(3)Position of the key groove of the No. 1 cylinder at B.T.D.C. bb (fix the governor flyweight at this position for delivery).
(4)B.T.D.C.: aa
(5)At second timing adjustment, set the camshaft at the * position and tighten the flyweight locknut.
(6)Align the flyweight's timing gear position with the lockpin groove and then fully tighten the flyweight to the camshaft.
(7)Remove the lock pin and adjust the governor. Reinstall the lock pin to fix the flyweight for delivery.
----------
aa=16deg bb=0deg
----------
a=54deg54min+-3deg b=8deg+-30min
----------
aa=16deg bb=0deg
----------
a=54deg54min+-3deg b=8deg+-30min
Information:
Problem
Some connecting rod assemblies may have been machined incorrectly. A machining discrepancy in the rod eye bore may not allow the rod eye bushing outside diameter to make complete contact with the rod eye bore. This can reduce the life of the bushing.
Affected Product
Model & Identification Number
3508 (7YG2069, 95Y1016, 96Y1725-1727, 23Z6865, 23Z6867-6871, 23Z6884-6885, 23Z6889, 23Z6892, 68Z903-906, 68Z909 , 68Z912, 68Z914, 69Z745-761)
3508B (7SM77, 7SM82-83)
G3508 (9TG141-144)
3512 (49Y835, 51Y760, 24Z7930-7932, 24Z7935-7948, 24Z7951, 24Z7953-7965, 24Z7969, 24Z7971, 24Z7980-7982, 24Z7985, 24Z7990-7991, 66Z718-721, 66Z1444-1445)
3512B (4TN99, 8RM201-202, 6WN137, 6FL145)
G3512 (7NJ287-290, 7NJ297)
3516 (5SJ542-543, 7CL416, 7CL419-421, 4XF673, 25Z5550-5551, 25Z5553-5555, 25Z5559, 25Z5567, 25Z5569-5574, 25Z5577, 25Z5584-5585, 28Z646, 29Z1227-1230, 67Z1447-1449)
3516B (9AN121, 8KN146-149, 8KN153-154, 7RN464-470)
G3516 (8LD46, 4EK1304-1305, 4EK1307-1313, 4EK1327, 4EK1334)
777D (3PR466-468, 3PR472-478, 3PR480)
Parts Needed
1 - 6I1356 Seal1 - 6I1357 Seal1 - 1013281 Rod Assembly1 - 1077330 Bearing (if necessary)1 - 1106991 Gasket-Head1 - 1106992 Gasket The parts are listed as one per failure. As many as 8, 12, or 16 parts may be required depending on the engine model. Additional parts not listed may be required depending on arrangement.
Action Required
See the attached procedure.
Owner Notification
U.S. and Canadian owners will receive the attached Owner Notification.
Service Claim Allowances
Labor Hour Breakdown For repairs of less than a complete set, 6.0 hours of labor per cylinder are reimbursable.
Allow 1.0 hour labor for testing of an engine and an additional 2.0 hours for setup/tear down.
The rod inspection, rod replacement and engine testing setup/tear down labor hours listed above are based on a basic 3500 Series Commercial Engine repaired in a dealer shop. Engines with various attachments, at customer sites or in a vehicle chassis may require additional labor hours. Those additional hours must be explained in the claim details.Costs incurred for emergency parts orders, for return of connecting rods, oil analysis, equipment needs to complete repairs or engine testing should be listed as other expenses and explained.
Parts Disposition
Return the removed defective connecting rod(s) to:
Caterpillar, Inc.
Attn: Jack Sanders - PI3047
Building B Claims Room
3701 State Road 26 East
Lafayette, Indiana 47905
Package the defective connecting rod(s) in it's original packaging carton for return shipment to Lafayette. Return defective parts within 24 hours of completion of removal from the engine. Call Matt Hannon at (765) 448-5138 or e-mail HANNOMJ with shipping Bill Number, part number, quantity in shipment, and Dealer name and location.
Dealers outside of North America should ship by Air Freight.
MAKE EVERY EFFORT TO COMPLETE THIS PROGRAM AS SOON AS POSSIBLE.
Attach.(1-Owner Notification)(2-Rework Procedure)Copy Of Owner Notification For U.S. And Canadian Owners
Rework Procedure
Connecting Rod Inspection
- The inspection of the connecting rod date code can be performed by removing the cylinder block side covers (left side typically most accessible) and viewing the date code. Rotation of the crankshaft and use of a mirror and a flash light will assist in viewing the date code on some rods. The date code is located on the side of the side of the rod cap at cap to rod joint. The date code format is YYMXXXX where (YY) is the year, (M) is a letter denoting the month, and (XXXX) is a sequence number. Rods with date
Some connecting rod assemblies may have been machined incorrectly. A machining discrepancy in the rod eye bore may not allow the rod eye bushing outside diameter to make complete contact with the rod eye bore. This can reduce the life of the bushing.
Affected Product
Model & Identification Number
3508 (7YG2069, 95Y1016, 96Y1725-1727, 23Z6865, 23Z6867-6871, 23Z6884-6885, 23Z6889, 23Z6892, 68Z903-906, 68Z909 , 68Z912, 68Z914, 69Z745-761)
3508B (7SM77, 7SM82-83)
G3508 (9TG141-144)
3512 (49Y835, 51Y760, 24Z7930-7932, 24Z7935-7948, 24Z7951, 24Z7953-7965, 24Z7969, 24Z7971, 24Z7980-7982, 24Z7985, 24Z7990-7991, 66Z718-721, 66Z1444-1445)
3512B (4TN99, 8RM201-202, 6WN137, 6FL145)
G3512 (7NJ287-290, 7NJ297)
3516 (5SJ542-543, 7CL416, 7CL419-421, 4XF673, 25Z5550-5551, 25Z5553-5555, 25Z5559, 25Z5567, 25Z5569-5574, 25Z5577, 25Z5584-5585, 28Z646, 29Z1227-1230, 67Z1447-1449)
3516B (9AN121, 8KN146-149, 8KN153-154, 7RN464-470)
G3516 (8LD46, 4EK1304-1305, 4EK1307-1313, 4EK1327, 4EK1334)
777D (3PR466-468, 3PR472-478, 3PR480)
Parts Needed
1 - 6I1356 Seal1 - 6I1357 Seal1 - 1013281 Rod Assembly1 - 1077330 Bearing (if necessary)1 - 1106991 Gasket-Head1 - 1106992 Gasket The parts are listed as one per failure. As many as 8, 12, or 16 parts may be required depending on the engine model. Additional parts not listed may be required depending on arrangement.
Action Required
See the attached procedure.
Owner Notification
U.S. and Canadian owners will receive the attached Owner Notification.
Service Claim Allowances
Labor Hour Breakdown For repairs of less than a complete set, 6.0 hours of labor per cylinder are reimbursable.
Allow 1.0 hour labor for testing of an engine and an additional 2.0 hours for setup/tear down.
The rod inspection, rod replacement and engine testing setup/tear down labor hours listed above are based on a basic 3500 Series Commercial Engine repaired in a dealer shop. Engines with various attachments, at customer sites or in a vehicle chassis may require additional labor hours. Those additional hours must be explained in the claim details.Costs incurred for emergency parts orders, for return of connecting rods, oil analysis, equipment needs to complete repairs or engine testing should be listed as other expenses and explained.
Parts Disposition
Return the removed defective connecting rod(s) to:
Caterpillar, Inc.
Attn: Jack Sanders - PI3047
Building B Claims Room
3701 State Road 26 East
Lafayette, Indiana 47905
Package the defective connecting rod(s) in it's original packaging carton for return shipment to Lafayette. Return defective parts within 24 hours of completion of removal from the engine. Call Matt Hannon at (765) 448-5138 or e-mail HANNOMJ with shipping Bill Number, part number, quantity in shipment, and Dealer name and location.
Dealers outside of North America should ship by Air Freight.
MAKE EVERY EFFORT TO COMPLETE THIS PROGRAM AS SOON AS POSSIBLE.
Attach.(1-Owner Notification)(2-Rework Procedure)Copy Of Owner Notification For U.S. And Canadian Owners
Rework Procedure
Connecting Rod Inspection
- The inspection of the connecting rod date code can be performed by removing the cylinder block side covers (left side typically most accessible) and viewing the date code. Rotation of the crankshaft and use of a mirror and a flash light will assist in viewing the date code on some rods. The date code is located on the side of the side of the rod cap at cap to rod joint. The date code format is YYMXXXX where (YY) is the year, (M) is a letter denoting the month, and (XXXX) is a sequence number. Rods with date
Have questions with 101402-3820?
Group cross 101402-3820 ZEXEL
Komatsu
Komatsu
101402-3820
INJECTION-PUMP ASSEMBLY