Information injection-pump assembly
BOSCH
9 400 613 878
9400613878
ZEXEL
101402-3700
1014023700
KOMATSU
6135721620
6135721620
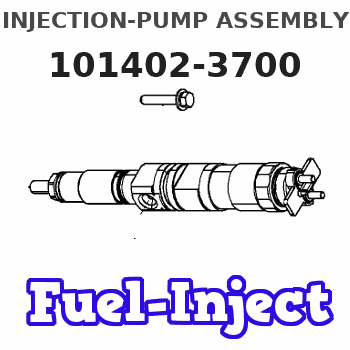
Rating:
Service parts 101402-3700 INJECTION-PUMP ASSEMBLY:
1.
_
5.
AUTOM. ADVANCE MECHANIS
6.
COUPLING PLATE
7.
COUPLING PLATE
8.
_
9.
_
11.
Nozzle and Holder
6137-12-3100
12.
Open Pre:MPa(Kqf/cm2)
22.1{225}
15.
NOZZLE SET
Cross reference number
BOSCH
9 400 613 878
9400613878
ZEXEL
101402-3700
1014023700
KOMATSU
6135721620
6135721620
Zexel num
Bosch num
Firm num
Name
101402-3700
9 400 613 878
6135721620 KOMATSU
INJECTION-PUMP ASSEMBLY
S4D105 * K 14BC INJECTION PUMP ASSY PE4A,5A, PE
S4D105 * K 14BC INJECTION PUMP ASSY PE4A,5A, PE
Calibration Data:
Adjustment conditions
Test oil
1404 Test oil ISO4113 or {SAEJ967d}
1404 Test oil ISO4113 or {SAEJ967d}
Test oil temperature
degC
40
40
45
Nozzle and nozzle holder
105780-8140
Bosch type code
EF8511/9A
Nozzle
105780-0000
Bosch type code
DN12SD12T
Nozzle holder
105780-2080
Bosch type code
EF8511/9
Opening pressure
MPa
17.2
Opening pressure
kgf/cm2
175
Injection pipe
Outer diameter - inner diameter - length (mm) mm 6-2-600
Outer diameter - inner diameter - length (mm) mm 6-2-600
Tester oil delivery pressure
kPa
157
157
157
Tester oil delivery pressure
kgf/cm2
1.6
1.6
1.6
Direction of rotation (viewed from drive side)
Right R
Right R
Injection timing adjustment
Direction of rotation (viewed from drive side)
Right R
Right R
Injection order
1-2-4-3
Pre-stroke
mm
3.3
3.25
3.35
Rack position
Point A R=A
Point A R=A
Beginning of injection position
Drive side NO.1
Drive side NO.1
Difference between angles 1
Cyl.1-2 deg. 90 89.5 90.5
Cyl.1-2 deg. 90 89.5 90.5
Difference between angles 2
Cal 1-4 deg. 180 179.5 180.5
Cal 1-4 deg. 180 179.5 180.5
Difference between angles 3
Cal 1-3 deg. 270 269.5 270.5
Cal 1-3 deg. 270 269.5 270.5
Injection quantity adjustment
Adjusting point
A
Rack position
9.1
Pump speed
r/min
1200
1200
1200
Average injection quantity
mm3/st.
73
72
74
Max. variation between cylinders
%
0
-2
2
Basic
*
Fixing the lever
*
Injection quantity adjustment_02
Adjusting point
B
Rack position
7+-0.5
Pump speed
r/min
400
400
400
Average injection quantity
mm3/st.
9.1
7.6
10.6
Max. variation between cylinders
%
0
-10
10
Fixing the rack
*
Test data Ex:
Governor adjustment
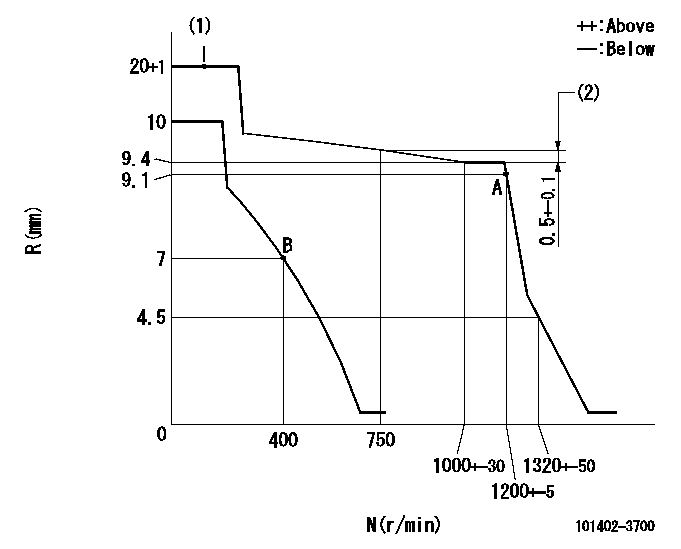
N:Pump speed
R:Rack position (mm)
(1)Target notch: K
(2)Rack difference between N = N1 and N = N2
----------
K=9 N1=1100r/min N2=750r/min
----------
----------
K=9 N1=1100r/min N2=750r/min
----------
Speed control lever angle
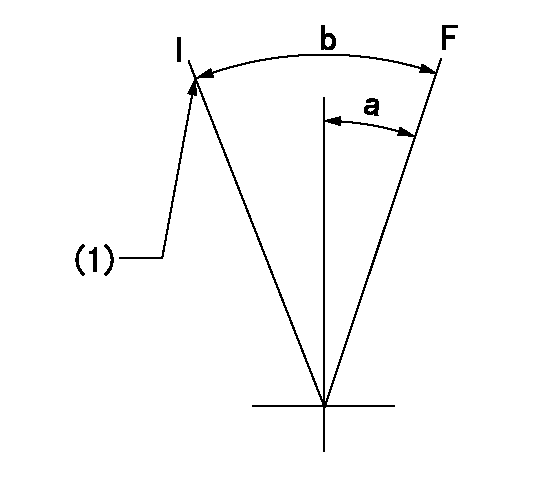
F:Full speed
I:Idle
(1)Stopper bolt setting
----------
----------
a=8deg+-5deg b=20deg+-5deg
----------
----------
a=8deg+-5deg b=20deg+-5deg
Stop lever angle
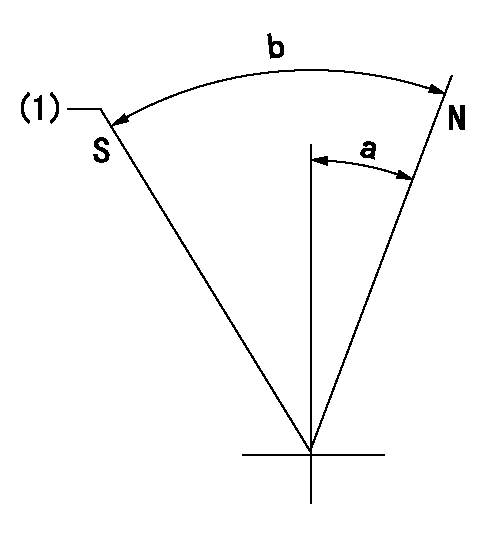
N:Pump normal
S:Stop the pump.
(1)At shipping
----------
----------
a=27deg+-5deg b=53deg+-5deg
----------
----------
a=27deg+-5deg b=53deg+-5deg
Timing setting

(1)Pump vertical direction
(2)Position of center of spline's wide tooth at No 1 cylinder's beginning of injection (key position)
(3)B.T.D.C.: aa
(4)-
----------
aa=19deg
----------
a=(1deg)
----------
aa=19deg
----------
a=(1deg)
Information:
Problem
The fuel injectors may fail on certain Challenger 75 Tractors and 3176 Truck Engines.
Affected Product
Model & Identification Number
Challenger 75 (4CJ1-406)
3176 (2YG1-Up; 7LG1-4822)
Parts Needed
Use the following parts in quantities needed to perform repairs. The application of each injector listed is noted. Use remanufactured injectors, unless it is not available.
0R3397 Injector Grp. (4P9510 if remanufactured is not available for 7LG 250-300 HP)0R3398 Injector Grp. (4P9520 if remanufactured is not available for 7LG 325 HP and Challenger 75 4CJ1-406)0R3399 Injector Grp. (4P9610 if remanufactured is not available for 2YG 250-275 HP)0R3400 Injector Grp. (4P9620 if remanufactured is not available for 2YG 300-325 HP)9X7317 Seal (injector tip O-ring)9X7557 Seal (injector upper O-ring)9X7722 Seal (injector lower O-ring)336044 Seal (injector thrust-pad-retaining O-ring)Action Required
See attached Rework Procedure.
Service Claim Allowances
Challenger 75 Tractors
This is a 2.5-hour job. Add 0.2 hours for 1st injector diagnostic test and 0.1 hours for each additional injector test. Add 1.2 hours for first injector sleeve replaced and 0.7 hours for each additional sleeve replaced.
3176 Truck Engines
Parts Disposition
Handle the parts in accordance with your Warranty Bulletin on warranty parts handling.
Attach. (1-Rework Procedure)Rework Procedure
1. Isolate the problem to the individual injector causing the problem. For this program only the failed injector(s) is covered so it is important to isolate the individual injector(s) causing the problem.A. For fuel dilution of the engine oil, first attempt to find the leak by pressurizing the low pressure system with the hand priming pump and the return line blocked off. Visually inspect each injector for leaks. It is also important to inspect the cylinder head casting for leaks around the injector bore, in the hold down bolt holes and along the gallery which crosses the camshaft compartment. If no leaks are found the injectors should be removed and leak tested using the 1U6661 Pop Tester. Drain the fuel manifold by removing the lower plug at the rear of the manifold. Remove the suspect injector(s). Test the injector(s) with the 1U6661 Pop Tester following the procedures in Special Instructions SEHS8867. Be sure to activate the solenoid valve and stroke the injector to create high pressure inside the injector when inspecting the high pressure plug for leaks. The plug is located at the base of the forged body.
The leak-down rate is a measure of plunger clearance leakage and should be checked when looking for fuel leaks.
Some small amount of leakage at the terminal post is permitted. Refer to Service Magazine September 21, 1991 or Truck Engine News October 1991.
B. For misfire or performance problems identification of a failed injector may require duplication of the conditions where the complaint exists. Interviewing the driver for the load and speed conditions where the problem occurs will be helpful. Diagnosis of the problem may require driving the truck with a load on or using a chassis dynomometer if the complaint arises only under loaded conditions.First attempt to diagnose the problem on the engine. Use the ECAP Tool to cut out cylinders under conditions which duplicate the complaint. Noticeable differences in the sound, fuel position (rack),
The fuel injectors may fail on certain Challenger 75 Tractors and 3176 Truck Engines.
Affected Product
Model & Identification Number
Challenger 75 (4CJ1-406)
3176 (2YG1-Up; 7LG1-4822)
Parts Needed
Use the following parts in quantities needed to perform repairs. The application of each injector listed is noted. Use remanufactured injectors, unless it is not available.
0R3397 Injector Grp. (4P9510 if remanufactured is not available for 7LG 250-300 HP)0R3398 Injector Grp. (4P9520 if remanufactured is not available for 7LG 325 HP and Challenger 75 4CJ1-406)0R3399 Injector Grp. (4P9610 if remanufactured is not available for 2YG 250-275 HP)0R3400 Injector Grp. (4P9620 if remanufactured is not available for 2YG 300-325 HP)9X7317 Seal (injector tip O-ring)9X7557 Seal (injector upper O-ring)9X7722 Seal (injector lower O-ring)336044 Seal (injector thrust-pad-retaining O-ring)Action Required
See attached Rework Procedure.
Service Claim Allowances
Challenger 75 Tractors
This is a 2.5-hour job. Add 0.2 hours for 1st injector diagnostic test and 0.1 hours for each additional injector test. Add 1.2 hours for first injector sleeve replaced and 0.7 hours for each additional sleeve replaced.
3176 Truck Engines
Parts Disposition
Handle the parts in accordance with your Warranty Bulletin on warranty parts handling.
Attach. (1-Rework Procedure)Rework Procedure
1. Isolate the problem to the individual injector causing the problem. For this program only the failed injector(s) is covered so it is important to isolate the individual injector(s) causing the problem.A. For fuel dilution of the engine oil, first attempt to find the leak by pressurizing the low pressure system with the hand priming pump and the return line blocked off. Visually inspect each injector for leaks. It is also important to inspect the cylinder head casting for leaks around the injector bore, in the hold down bolt holes and along the gallery which crosses the camshaft compartment. If no leaks are found the injectors should be removed and leak tested using the 1U6661 Pop Tester. Drain the fuel manifold by removing the lower plug at the rear of the manifold. Remove the suspect injector(s). Test the injector(s) with the 1U6661 Pop Tester following the procedures in Special Instructions SEHS8867. Be sure to activate the solenoid valve and stroke the injector to create high pressure inside the injector when inspecting the high pressure plug for leaks. The plug is located at the base of the forged body.
The leak-down rate is a measure of plunger clearance leakage and should be checked when looking for fuel leaks.
Some small amount of leakage at the terminal post is permitted. Refer to Service Magazine September 21, 1991 or Truck Engine News October 1991.
B. For misfire or performance problems identification of a failed injector may require duplication of the conditions where the complaint exists. Interviewing the driver for the load and speed conditions where the problem occurs will be helpful. Diagnosis of the problem may require driving the truck with a load on or using a chassis dynomometer if the complaint arises only under loaded conditions.First attempt to diagnose the problem on the engine. Use the ECAP Tool to cut out cylinders under conditions which duplicate the complaint. Noticeable differences in the sound, fuel position (rack),
Have questions with 101402-3700?
Group cross 101402-3700 ZEXEL
Komatsu
101402-3700
9 400 613 878
6135721620
INJECTION-PUMP ASSEMBLY
S4D105
S4D105