Information injection-pump assembly
BOSCH
F 019 Z10 569
f019z10569
ZEXEL
101402-1010
1014021010
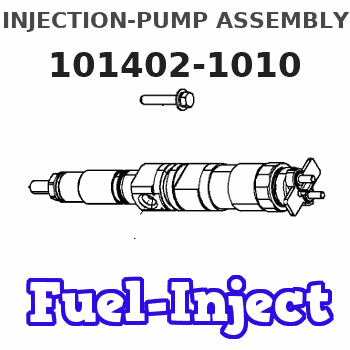
Rating:
Service parts 101402-1010 INJECTION-PUMP ASSEMBLY:
1.
_
5.
AUTOM. ADVANCE MECHANIS
6.
COUPLING PLATE
8.
_
9.
_
11.
Nozzle and Holder
ME080745
12.
Open Pre:MPa(Kqf/cm2)
17.7(180)
15.
NOZZLE SET
Cross reference number
BOSCH
F 019 Z10 569
f019z10569
ZEXEL
101402-1010
1014021010
Zexel num
Bosch num
Firm num
Name
Calibration Data:
Adjustment conditions
Test oil
1404 Test oil ISO4113 or {SAEJ967d}
1404 Test oil ISO4113 or {SAEJ967d}
Test oil temperature
degC
40
40
45
Nozzle and nozzle holder
105780-8140
Bosch type code
EF8511/9A
Nozzle
105780-0000
Bosch type code
DN12SD12T
Nozzle holder
105780-2080
Bosch type code
EF8511/9
Opening pressure
MPa
17.2
Opening pressure
kgf/cm2
175
Injection pipe
Outer diameter - inner diameter - length (mm) mm 6-2-600
Outer diameter - inner diameter - length (mm) mm 6-2-600
Overflow valve
131424-6220
Overflow valve opening pressure
kPa
255
221
289
Overflow valve opening pressure
kgf/cm2
2.6
2.25
2.95
Tester oil delivery pressure
kPa
157
157
157
Tester oil delivery pressure
kgf/cm2
1.6
1.6
1.6
Direction of rotation (viewed from drive side)
Right R
Right R
Injection timing adjustment
Direction of rotation (viewed from drive side)
Right R
Right R
Injection order
1-3-4-2
Pre-stroke
mm
3.5
3.45
3.55
Beginning of injection position
Drive side NO.1
Drive side NO.1
Difference between angles 1
Cal 1-3 deg. 90 89.5 90.5
Cal 1-3 deg. 90 89.5 90.5
Difference between angles 2
Cal 1-4 deg. 180 179.5 180.5
Cal 1-4 deg. 180 179.5 180.5
Difference between angles 3
Cyl.1-2 deg. 270 269.5 270.5
Cyl.1-2 deg. 270 269.5 270.5
Injection quantity adjustment
Adjusting point
A
Rack position
10.5
Pump speed
r/min
900
900
900
Average injection quantity
mm3/st.
70.5
69.5
71.5
Max. variation between cylinders
%
0
-2.5
2.5
Basic
*
Fixing the lever
*
Injection quantity adjustment_02
Adjusting point
-
Rack position
7.7+-0.5
Pump speed
r/min
375
375
375
Average injection quantity
mm3/st.
8
7
9
Max. variation between cylinders
%
0
-14
14
Fixing the rack
*
Remarks
Adjust only variation between cylinders; adjust governor according to governor specifications.
Adjust only variation between cylinders; adjust governor according to governor specifications.
Test data Ex:
Governor adjustment
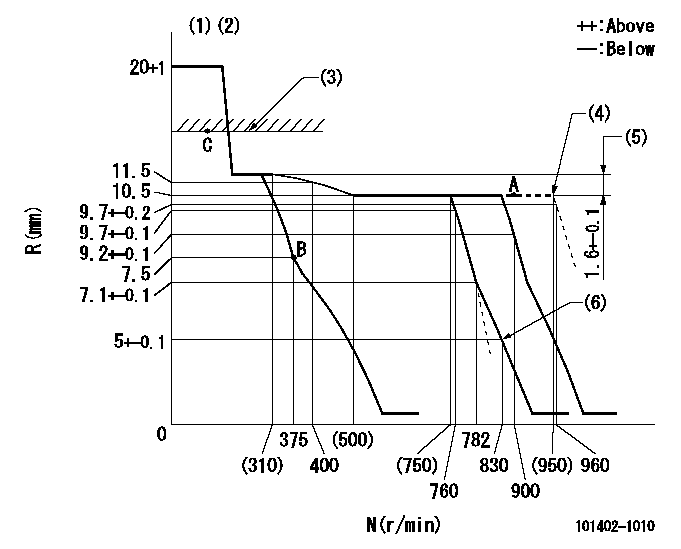
N:Pump speed
R:Rack position (mm)
(1)Notch: K
(2)Tolerance for racks not indicated: +-0.05mm.
(3)RACK LIMIT: RAL
(4)Set at delivery
(5)Rack difference between N = N1 and N = N2
(6)Set idle sub-spring
----------
K=16 RAL=13.3+-0.2mm N1=900r/min N2=260r/min
----------
----------
K=16 RAL=13.3+-0.2mm N1=900r/min N2=260r/min
----------
Speed control lever angle
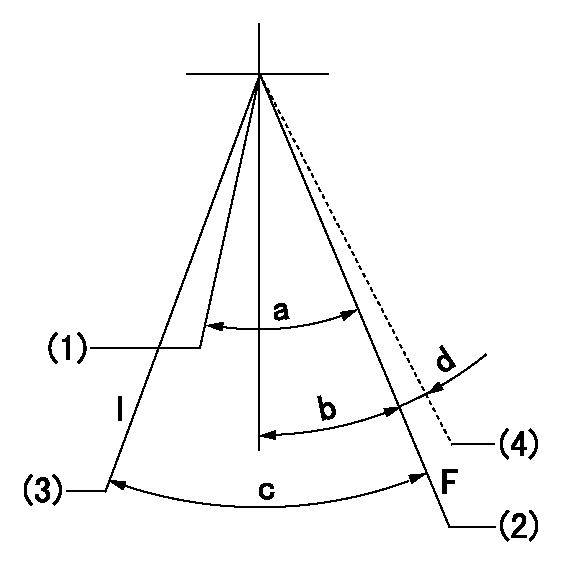
F:Full speed
I:Idle
(1)Pump speed = aa
(2)Pump speed = bb
(3)Stopper bolt setting
(4)At delivery
----------
aa=750r/min bb=900r/min
----------
a=(6deg)+-5deg b=(6deg)+-5deg c=(23deg)+-5deg d=(2deg)
----------
aa=750r/min bb=900r/min
----------
a=(6deg)+-5deg b=(6deg)+-5deg c=(23deg)+-5deg d=(2deg)
Stop lever angle

N:Pump normal
S:Stop the pump.
----------
----------
a=27deg+-5deg b=53deg+-5deg
----------
----------
a=27deg+-5deg b=53deg+-5deg
Timing setting

(1)Pump vertical direction
(2)Position of gear mark '3' at No 1 cylinder's beginning of injection
(3)B.T.D.C.: aa
(4)-
----------
aa=10deg
----------
a=(130deg)
----------
aa=10deg
----------
a=(130deg)
Information:
3406B and 3406C Non-Peec Engines
Steps 4 through 7 do not apply to PEEC engines.
Illustration 16. Install Lever Assembly
(1) 6N-3646 Lever. (2) 5P-0537 Washer. (3) 6V-8918 Bolt. (4) 9M-3858 Rack Preload Spring. (5) 1B-7182 Bolt.4. Install lever (1) with washer (2) and bolt (3).5. Install bolt (5) into hole as shown.6. Hook spring (4) between bolt (5) and lever (1).
Illustration 17. Install Rack Positioning Assembly
(1) 9U-5296 Rack Assembly. (2) Original cover mounting bolts or 4F-7957 Bolt.7. Install rack positioning assembly (1) with bolts (2). Use rack positioning assembly (1) as a "fuel ON" and "fuel OFF" control. Position the assembly to the full "fuel ON" position for all tests. Use the positioning assembly for rack adjustment.3406 Peec Engines
Steps 8 and 9 do not apply to Non-PEEC engines.
Illustration 18. Installing testing hardware for 3406 PEEC Engines
(1) 9U-5292 Rack Preload Assembly. (2) 9U-5120 Spanner Wrench. (3) 9U-5295 Positioning Assembly.8. Remove the BTM from the injection pump and install the 9U-5292 Rack Preload Assembly (1). Make sure the pin is properly located in the slot of the servo shaft. After installing the rack preload assembly, finger tighten the bolts.9. Remove the shut-off solenoid with a 9U-5120 Spanner Wrench (2) and install 9U-5295 Positioning Assembly (3). Use rack preload assembly (1) as a "fuel ON" and "fuel OFF" control. Position the assembly to the full "fuel ON" position for all tests. Use the positioning assembly for rack adjustment.Connect Hoses and Lines
Illustration 19. Connect Lube Oil Supply and Drain Hose
(1) 7G-7105 Hose. (2) 5P-6661 Fitting. (3) 9U-7709 Oil Drain Tube and two 5D-1026 Hose Clamps.
Illustration 20. Connect Fuel Supply and Return Lines
(4) 030-7947 Fitting, 3J-1907 O-ring Seal, and 7G-7105 Hose. (5) 8T-2160 Orifice Fitting, 3J-1907 O-ring Seal, and 7G-7105 Hose. (6) 9U-5298 Fuel Injection Line Tube Assembly (verify fuel line part number in TMI).1. Attach one end of hose (1) to the Lube Oil Supply fitting on the test stand. Attach the other end to the 5P-6661 Fitting on the rear support.2. Connect the oil drain tube (2) to the rear support and the test stand's stand-pipe with two hose clamps. On the AVM20-12C, the drain hose can be routed to the lube oil drain pan.3. Install fitting, O-ring, and hose (4) onto the fuel injection pump. Connect the other end of the hose to the "Test Oil Supply" connection on the test stand.4. Install fitting, O-ring, and hose (5) onto the fuel injection pump. Connect the other end of the hose to the "Test Oil Return" connection on the test stand.
Hold nut on 9U-6705 Master Nozzle when tightening fuel injection line tube assemblies (6). If the nut is not held in place during tightening, the master nozzle can be damaged.
5. Install six fuel injection line tube assemblies (6).Pre-Test Checks
1. Remove the lock-out on the electrical box, if installed.2. Release the Emergency Stop button.3. Start the bench and visually check for oil leaks from covers, hoses, etc.4. Check for oil flow through the drain tube. Also, check for oil flowing out of the oil
Steps 4 through 7 do not apply to PEEC engines.
Illustration 16. Install Lever Assembly
(1) 6N-3646 Lever. (2) 5P-0537 Washer. (3) 6V-8918 Bolt. (4) 9M-3858 Rack Preload Spring. (5) 1B-7182 Bolt.4. Install lever (1) with washer (2) and bolt (3).5. Install bolt (5) into hole as shown.6. Hook spring (4) between bolt (5) and lever (1).
Illustration 17. Install Rack Positioning Assembly
(1) 9U-5296 Rack Assembly. (2) Original cover mounting bolts or 4F-7957 Bolt.7. Install rack positioning assembly (1) with bolts (2). Use rack positioning assembly (1) as a "fuel ON" and "fuel OFF" control. Position the assembly to the full "fuel ON" position for all tests. Use the positioning assembly for rack adjustment.3406 Peec Engines
Steps 8 and 9 do not apply to Non-PEEC engines.
Illustration 18. Installing testing hardware for 3406 PEEC Engines
(1) 9U-5292 Rack Preload Assembly. (2) 9U-5120 Spanner Wrench. (3) 9U-5295 Positioning Assembly.8. Remove the BTM from the injection pump and install the 9U-5292 Rack Preload Assembly (1). Make sure the pin is properly located in the slot of the servo shaft. After installing the rack preload assembly, finger tighten the bolts.9. Remove the shut-off solenoid with a 9U-5120 Spanner Wrench (2) and install 9U-5295 Positioning Assembly (3). Use rack preload assembly (1) as a "fuel ON" and "fuel OFF" control. Position the assembly to the full "fuel ON" position for all tests. Use the positioning assembly for rack adjustment.Connect Hoses and Lines
Illustration 19. Connect Lube Oil Supply and Drain Hose
(1) 7G-7105 Hose. (2) 5P-6661 Fitting. (3) 9U-7709 Oil Drain Tube and two 5D-1026 Hose Clamps.
Illustration 20. Connect Fuel Supply and Return Lines
(4) 030-7947 Fitting, 3J-1907 O-ring Seal, and 7G-7105 Hose. (5) 8T-2160 Orifice Fitting, 3J-1907 O-ring Seal, and 7G-7105 Hose. (6) 9U-5298 Fuel Injection Line Tube Assembly (verify fuel line part number in TMI).1. Attach one end of hose (1) to the Lube Oil Supply fitting on the test stand. Attach the other end to the 5P-6661 Fitting on the rear support.2. Connect the oil drain tube (2) to the rear support and the test stand's stand-pipe with two hose clamps. On the AVM20-12C, the drain hose can be routed to the lube oil drain pan.3. Install fitting, O-ring, and hose (4) onto the fuel injection pump. Connect the other end of the hose to the "Test Oil Supply" connection on the test stand.4. Install fitting, O-ring, and hose (5) onto the fuel injection pump. Connect the other end of the hose to the "Test Oil Return" connection on the test stand.
Hold nut on 9U-6705 Master Nozzle when tightening fuel injection line tube assemblies (6). If the nut is not held in place during tightening, the master nozzle can be damaged.
5. Install six fuel injection line tube assemblies (6).Pre-Test Checks
1. Remove the lock-out on the electrical box, if installed.2. Release the Emergency Stop button.3. Start the bench and visually check for oil leaks from covers, hoses, etc.4. Check for oil flow through the drain tube. Also, check for oil flowing out of the oil