Information injection-pump assembly
ZEXEL
101402-1001
1014021001
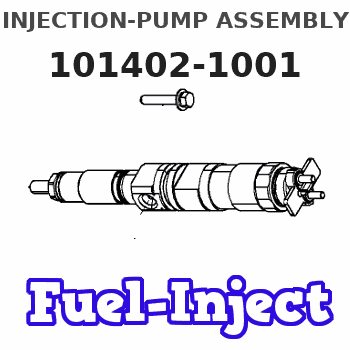
Rating:
Cross reference number
ZEXEL
101402-1001
1014021001
Zexel num
Bosch num
Firm num
Name
101402-1001
INJECTION-PUMP ASSEMBLY
Calibration Data:
Adjustment conditions
Test oil
1404 Test oil ISO4113 or {SAEJ967d}
1404 Test oil ISO4113 or {SAEJ967d}
Test oil temperature
degC
40
40
45
Nozzle and nozzle holder
105780-8140
Bosch type code
EF8511/9A
Nozzle
105780-0000
Bosch type code
DN12SD12T
Nozzle holder
105780-2080
Bosch type code
EF8511/9
Opening pressure
MPa
17.2
Opening pressure
kgf/cm2
175
Injection pipe
Outer diameter - inner diameter - length (mm) mm 6-2-600
Outer diameter - inner diameter - length (mm) mm 6-2-600
Overflow valve
131424-6220
Overflow valve opening pressure
kPa
255
221
289
Overflow valve opening pressure
kgf/cm2
2.6
2.25
2.95
Tester oil delivery pressure
kPa
157
157
157
Tester oil delivery pressure
kgf/cm2
1.6
1.6
1.6
Direction of rotation (viewed from drive side)
Right R
Right R
Injection timing adjustment
Direction of rotation (viewed from drive side)
Right R
Right R
Injection order
1-3-4-2
Pre-stroke
mm
3.5
3.45
3.55
Beginning of injection position
Drive side NO.1
Drive side NO.1
Difference between angles 1
Cal 1-3 deg. 90 89.5 90.5
Cal 1-3 deg. 90 89.5 90.5
Difference between angles 2
Cal 1-4 deg. 180 179.5 180.5
Cal 1-4 deg. 180 179.5 180.5
Difference between angles 3
Cyl.1-2 deg. 270 269.5 270.5
Cyl.1-2 deg. 270 269.5 270.5
Injection quantity adjustment
Adjusting point
A
Rack position
10.1
Pump speed
r/min
1100
1100
1100
Average injection quantity
mm3/st.
65
64
66
Max. variation between cylinders
%
0
-2.5
2.5
Basic
*
Fixing the lever
*
Injection quantity adjustment_02
Adjusting point
-
Rack position
7.7+-0.5
Pump speed
r/min
375
375
375
Average injection quantity
mm3/st.
8
7
9
Max. variation between cylinders
%
0
-14
14
Fixing the rack
*
Remarks
Adjust only variation between cylinders; adjust governor according to governor specifications.
Adjust only variation between cylinders; adjust governor according to governor specifications.
Injection quantity adjustment_03
Adjusting point
C
Rack position
-
Pump speed
r/min
100
100
100
Average injection quantity
mm3/st.
68
68
73
Fixing the lever
*
Rack limit
*
Test data Ex:
Governor adjustment
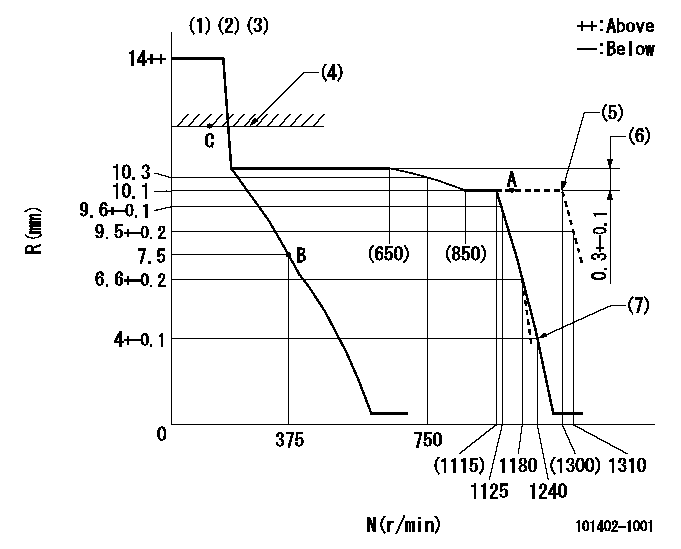
N:Pump speed
R:Rack position (mm)
(1)Notch: K
(2)Tolerance for racks not indicated: +-0.05mm.
(3)Torque spring does not operate.
(4)RACK LIMIT
(5)Set at delivery
(6)Rack difference between N = N1 and N = N2
(7)Set idle sub-spring
----------
K=14 N1=1100r/min N2=600r/min
----------
----------
K=14 N1=1100r/min N2=600r/min
----------
Speed control lever angle

F:Full speed
I:Idle
(1)At delivery
(2)Stopper bolt setting
----------
----------
a=(24deg)+-5deg b=(13deg)+-5deg c=(8deg)
----------
----------
a=(24deg)+-5deg b=(13deg)+-5deg c=(8deg)
Stop lever angle

N:Pump normal
S:Stop the pump.
----------
----------
a=27deg+-5deg b=53deg+-5deg
----------
----------
a=27deg+-5deg b=53deg+-5deg
Timing setting

(1)Pump vertical direction
(2)Position of gear mark '3' at No 1 cylinder's beginning of injection
(3)B.T.D.C.: aa
(4)-
----------
aa=12deg
----------
a=(130deg)
----------
aa=12deg
----------
a=(130deg)
Information:
Illustration 5 g01380327
Install support (18) with two bolts (1) and two hard washers (13). Tighten the two bolts to a torque of 47 9 N m (35 7 lb ft).
Install support assembly (21) with three bolts (14) and three hard washers (13). Tighten the three bolts to a torque of 47 9 N m (35 7 lb ft).
Install elbow assembly (22) with two bolts (9) and two hard washers (6). Install the elbow assembly to the turbocharger outlet by using the proper seals and the proper procedure. Tighten the two bolts to a torque of 55 10 N m (40 7 lb ft).
Position clamp assembly (20) between support assembly (21) and elbow assembly (22). Secure the clamp assembly with two bolts (9), four hard washers (6), and two nuts (7). Tighten the two bolts to a torque of 55 10 N m (40 7 lb ft).
Illustration 6 g01380335
Illustration 7 g01380344
Position Diesel Particulate Filter Gp (17) on the brackets.Note: Remove material from the hood assembly, as necessary, to avoid interference with the diesel particulate filter. Refer to Illustration 6.
Secure the Diesel Particulate Filter by using clamp (19). Secure clamp (19) to clamp assembly (20) with one bolt (4), two hard washers (13), and one nut (2). Tighten the bolt to a torque of 47 9 N m (35 7 lb ft).
Secure the other end of clamp (19) to clamp assembly (20) and support assembly (21) with one bolt (15), two hard washers (13), and one nut (2). Tighten the bolt to a torque of 47 9 N m (35 7 lb ft).Note: The inlet and outlet caps can be rotated in order to align with the elbow and the exhaust stack by loosening the band clamps. Tighten the band clamps after alignment is correct.
Install clamp assembly (16) in order to secure the Diesel Particulate Filter to the elbow assembly.
Illustration 8 g01380346
Install the other end of the Diesel Particulate Filter to support (18) with two bolts (10), four hard washers (6), and two nuts (7). Tighten the two bolts to a torque of 55 10 N m (40 7 lb ft).
Secure support (18) to support assembly (25) with two bolts (8), four hard washers (11), and two nuts (12). Tighten the two bolts to a torque of 100 20 N m (75 15 lb ft).
Secure ejector line (26) with two bolts (5), four hard washers (13), and two nuts (2). Tighten the two bolts to a torque of 47 9 N m (35 7 lb ft).
Illustration 9 g01383124
Typical Example for Installing the Exhaust Monitor Group
Illustration 10 g01425177
Typical Example for Installing the Exhaust Monitor Group (Shown With Pipe Elbow (3) Installed)
Install 302-1563 Exhaust Monitor Gp (25) (from Exhaust Monitor Group (23) ) in the cab.
Illustration 11 g01380354
Install the thermocouple and the pressure sensor tube (part of the 216-7990 Installation Assembly ) at the Diesel Particulate Filter. Refer to Special Instruction, REHS1807 under the topic "Connection for the Thermocouple and
Have questions with 101402-1001?
Group cross 101402-1001 ZEXEL
101402-1001
INJECTION-PUMP ASSEMBLY