Information injection-pump assembly
ZEXEL
101401-9530
1014019530
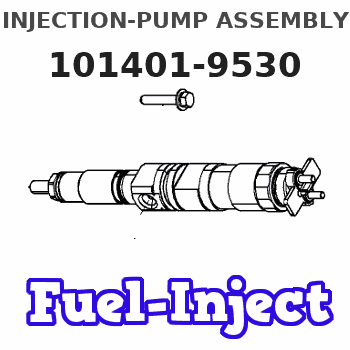
Rating:
Cross reference number
ZEXEL
101401-9530
1014019530
Zexel num
Bosch num
Firm num
Name
Calibration Data:
Adjustment conditions
Test oil
1404 Test oil ISO4113 or {SAEJ967d}
1404 Test oil ISO4113 or {SAEJ967d}
Test oil temperature
degC
40
40
45
Nozzle and nozzle holder
105780-8140
Bosch type code
EF8511/9A
Nozzle
105780-0000
Bosch type code
DN12SD12T
Nozzle holder
105780-2080
Bosch type code
EF8511/9
Opening pressure
MPa
17.2
Opening pressure
kgf/cm2
175
Injection pipe
Outer diameter - inner diameter - length (mm) mm 6-2-600
Outer diameter - inner diameter - length (mm) mm 6-2-600
Overflow valve
131424-6220
Overflow valve opening pressure
kPa
255
221
289
Overflow valve opening pressure
kgf/cm2
2.6
2.25
2.95
Tester oil delivery pressure
kPa
157
157
157
Tester oil delivery pressure
kgf/cm2
1.6
1.6
1.6
Direction of rotation (viewed from drive side)
Right R
Right R
Injection timing adjustment
Direction of rotation (viewed from drive side)
Right R
Right R
Injection order
1-3-4-2
Pre-stroke
mm
3.6
3.55
3.65
Rack position
Point A R=A
Point A R=A
Beginning of injection position
Drive side NO.1
Drive side NO.1
Difference between angles 1
Cal 1-3 deg. 90 89.5 90.5
Cal 1-3 deg. 90 89.5 90.5
Difference between angles 2
Cal 1-4 deg. 180 179.5 180.5
Cal 1-4 deg. 180 179.5 180.5
Difference between angles 3
Cyl.1-2 deg. 270 269.5 270.5
Cyl.1-2 deg. 270 269.5 270.5
Injection quantity adjustment
Adjusting point
-
Rack position
11.5
Pump speed
r/min
1000
1000
1000
Average injection quantity
mm3/st.
79.5
78.5
80.5
Max. variation between cylinders
%
0
-2.5
2.5
Basic
*
Fixing the rack
*
Standard for adjustment of the maximum variation between cylinders
*
Injection quantity adjustment_02
Adjusting point
H
Rack position
9.5+-0.5
Pump speed
r/min
375
375
375
Average injection quantity
mm3/st.
13
11.7
14.3
Max. variation between cylinders
%
0
-13
13
Fixing the rack
*
Standard for adjustment of the maximum variation between cylinders
*
Injection quantity adjustment_03
Adjusting point
A
Rack position
R1(11.5)
Pump speed
r/min
1000
1000
1000
Average injection quantity
mm3/st.
79.5
78.5
80.5
Basic
*
Fixing the lever
*
Boost pressure
kPa
89.3
89.3
Boost pressure
mmHg
670
670
Injection quantity adjustment_04
Adjusting point
B
Rack position
R1+0.15
Pump speed
r/min
1700
1700
1700
Average injection quantity
mm3/st.
86
82
90
Fixing the lever
*
Boost pressure
kPa
89.3
89.3
Boost pressure
mmHg
670
670
Injection quantity adjustment_05
Adjusting point
C
Rack position
R2-0.9
Pump speed
r/min
680
680
680
Average injection quantity
mm3/st.
48.5
44.5
52.5
Fixing the lever
*
Boost pressure
kPa
0
0
0
Boost pressure
mmHg
0
0
0
Boost compensator adjustment
Pump speed
r/min
700
700
700
Rack position
R2-0.9
Boost pressure
kPa
13.3
12
14.6
Boost pressure
mmHg
100
90
110
Boost compensator adjustment_02
Pump speed
r/min
700
700
700
Rack position
R2(R1-0.
25)
Boost pressure
kPa
76
76
76
Boost pressure
mmHg
570
570
570
Timer adjustment
Pump speed
r/min
1150--
Advance angle
deg.
0
0
0
Remarks
Start
Start
Timer adjustment_02
Pump speed
r/min
1100
Advance angle
deg.
0.5
Timer adjustment_03
Pump speed
r/min
1700
Advance angle
deg.
4.5
4
5
Remarks
Finish
Finish
Test data Ex:
Governor adjustment
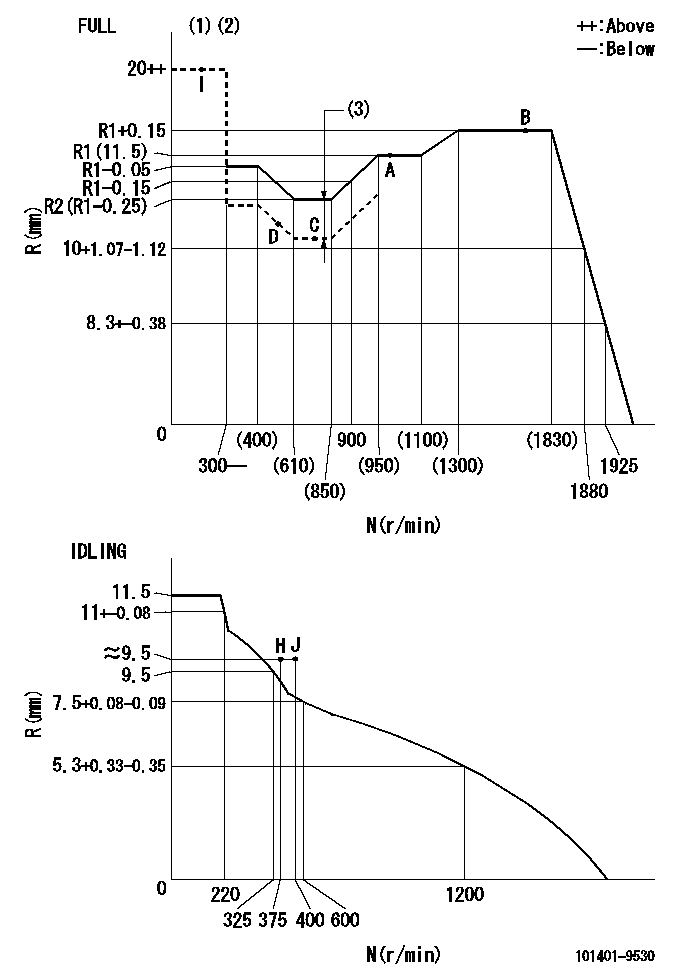
N:Pump speed
R:Rack position (mm)
(1)Torque cam stamping: T1
(2)Tolerance for racks not indicated: +-0.05mm.
(3)Boost compensator stroke: BCL
----------
T1=L45 BCL=0.9+-0.1mm
----------
----------
T1=L45 BCL=0.9+-0.1mm
----------
Speed control lever angle

F:Full speed
I:Idle
(1)Use the hole at R = aa
(2)Stopper bolt set position 'H'
----------
aa=40mm
----------
a=24deg+-5deg b=(40deg)+-3deg
----------
aa=40mm
----------
a=24deg+-5deg b=(40deg)+-3deg
Stop lever angle

N:Engine manufacturer's normal use
S:Stop the pump.
(1)Free (at delivery)
(2)Use the hole at R = aa
(3)Rack position corresponding to bb
(4)Set the stopper bolt at speed = cc and rack position = dd (non-injection rack position). Confirm non-injection.
(5)After setting the stopper bolt, confirm non-injection at speed ee. Rack position = ff or less (non-injection rack position).
----------
aa=40mm bb=16mm cc=1700r/min dd=(6.5)-0.5mm ee=375r/min ff=(8)mm
----------
a=(8deg)+-5deg b=(15deg)+-5deg c=(25deg)+-5deg
----------
aa=40mm bb=16mm cc=1700r/min dd=(6.5)-0.5mm ee=375r/min ff=(8)mm
----------
a=(8deg)+-5deg b=(15deg)+-5deg c=(25deg)+-5deg
0000001501 ACTUATOR
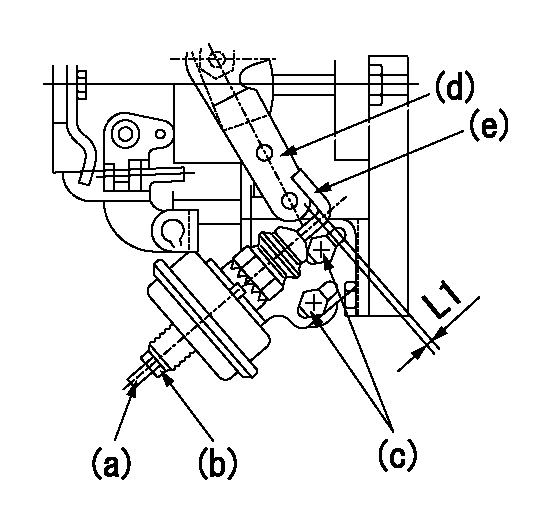
(a) Screw
(B) Nut
Bolt c
(d) Speed lever
(e) Actuator shaft
1. Actuator adjustment procedure
(1)Position the speed lever (d) in the idle position.
(2)Set bolt (c) so that the clearance between the speed lever (d)'s pin and the actuator shaft (e) is approximately L1.
(3)Loosen the nut (b) and fully tighten the screw (a).
(4)Set the pump speed at N1 and read the rack position when negative pressure P1 is applied to the actuator.
(5)Gradually loosen screw (a) and fix the nut (b) when the pump speed is N2 and the rack position is R1.
(6)Apply negative pressure several times and confirm that the lever (d) returns to the idle position at negative pressure '0.'
(7)Confirm that rack position is R2 when negative pressure is P2.
----------
L1=2mm N1=500r/min P1=66.7kPa(500mmHg) N2=500r/min R1=9.1mm P2=66.7kPa(500mmHg) R2=9.1mm
----------
----------
L1=2mm N1=500r/min P1=66.7kPa(500mmHg) N2=500r/min R1=9.1mm P2=66.7kPa(500mmHg) R2=9.1mm
----------
Timing setting

(1)Pump vertical direction
(2)Position of gear mark '3' at No 1 cylinder's beginning of injection
(3)B.T.D.C.: aa
(4)-
----------
aa=9deg
----------
a=(130deg)
----------
aa=9deg
----------
a=(130deg)
Information:
PROBLEM
The Diesel Particulate Filter core may fail on certain C3.4B Industrial Engines. The failures may result in loss of power and a blocked Diesel Particulate Filter.
AFFECTED PRODUCT
Model Identification Number
C3.4B CJG01859-01865, 1867, 1869-1870, 1901-1910, 1994, 2268, 2272, 2323-2324, 2364-2365, 2367-2374, 2376-2377, 2414, 2430-2439, 2441-2446, 2454-2456, 2458-2460, 2462-2463, 2482, 2529, 4411-4414, 4453-4465, 4999-5025, 5048-5050, 5069-5088, 5090-5095
CNW00578-00579, 581-587, 666, 668-674, 677, 680, 684, 708, 730-738, 740-744, 746, 748-750
PARTS NEEDED
Qty
Part Number Description
1 20R3615 KIT-FILTER (After Failure Only)
1 3793061 SEAL (After Failure Only)
1 3793064 SEAL-O-RING (After Failure Only)
1 3879343 CLIP (After Failure Only)
1 4732321 ENGINE SOFTWARE
1 4813598 FILTER AS (After Failure Only)
1 GND_WIRE_KIT Regen Interlock GND Wire Kit (See Action Required)
In order to allow equitable parts availability to all participating dealers, please limit your initial parts order to not exceed 26% of dealership population. This is an initial order recommendation only, and the ultimate responsibility for ordering the total number of parts needed to satisfy the program lies with the dealer.
ACTION REQUIRED
Before Failure:
1 - Update Engine Software, refer to Troubleshooting ? ECM Software ? Install, ensure to follow the steps to save the Engine Configuration data.
2 - Apply Carlson Service Number 14CP-013 - Regeneration Interlock Ground Wire Kit, contact a Carlson Paving Products Dealer for Kit Part Number 14CP-013.
After Failure:
1 - Refer to Steps 1 and 2 of the Before Failure actions.
2 - Service CCB Filter and replace with new filter, refer to Operation and Maintenance Manual ? Engine Crankcase Breather element ? Replace.
3 - Remove Diesel Particulate Filter, Refer to Disassembly and Assembly - Diesel Particulate Filter - Remove - wall Flow Diesel Particulate Filter.
4 - Move the Diesel Particulate Filter Assembly to a suitable work surface.
5 - Refer to Specifications - Diesel Particulate Filter (Wall Flow Diesel Particulate Filter(DPF)), remove V Band Clamps (1) and (4), carefully split assembly and remove DPF Canister element.
6 - Using new DPF Kit Filter, reassemble the Diesel Particulate Filter Assembly noting the alignment marks previously made in Step 3, refer to Specifications - Diesel Particulate Filter (Wall Flow Diesel Particulate Filter(DPF)).
7 - Reinstall the Diesel Particulate Filter assembly, Refer to Disassembly and Assembly - Diesel Particulate Filter - Install - wall Flow Diesel Particulate Filter.
8 - As the DPF has been replaced, ensure the ?DPF Replacement Reset? procedure is performed using CAT ET, refer to Troubleshooting - Service Tool Features - Components Replacement Resets.
SERVICE CLAIM ALLOWANCES
Product smu/age whichever comes first Caterpillar Dealer Suggested Customer Suggested
Parts % Labor Hrs% Parts % Labor Hrs% Parts % Labor Hrs%
0-5000 hrs,
0-60 mo 100.0% 100.0% 0.0% 0.0% 0.0% 0.0%
This is a 1.5-hour job
Note an additional 4.5 hours is allowed for After Failure.
PARTS DISPOSITION
Handle the parts in accordance with your Warranty Bulletin on warranty parts handling.