Information injection-pump assembly
BOSCH
9 400 610 361
9400610361
ZEXEL
101401-9361
1014019361
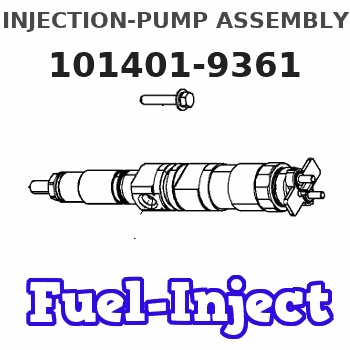
Rating:
Service parts 101401-9361 INJECTION-PUMP ASSEMBLY:
1.
_
6.
COUPLING PLATE
7.
COUPLING PLATE
8.
_
9.
_
11.
Nozzle and Holder
12.
Open Pre:MPa(Kqf/cm2)
21.6{220}
15.
NOZZLE SET
Cross reference number
BOSCH
9 400 610 361
9400610361
ZEXEL
101401-9361
1014019361
Zexel num
Bosch num
Firm num
Name
101401-9361
9 400 610 361
DPICO
INJECTION-PUMP ASSEMBLY
4D31T * Q 14CS PE
4D31T * Q 14CS PE
Calibration Data:
Adjustment conditions
Test oil
1404 Test oil ISO4113 or {SAEJ967d}
1404 Test oil ISO4113 or {SAEJ967d}
Test oil temperature
degC
40
40
45
Nozzle and nozzle holder
105780-8140
Bosch type code
EF8511/9A
Nozzle
105780-0000
Bosch type code
DN12SD12T
Nozzle holder
105780-2080
Bosch type code
EF8511/9
Opening pressure
MPa
17.2
Opening pressure
kgf/cm2
175
Injection pipe
Outer diameter - inner diameter - length (mm) mm 6-2-600
Outer diameter - inner diameter - length (mm) mm 6-2-600
Overflow valve
131424-6220
Overflow valve opening pressure
kPa
255
221
289
Overflow valve opening pressure
kgf/cm2
2.6
2.25
2.95
Tester oil delivery pressure
kPa
157
157
157
Tester oil delivery pressure
kgf/cm2
1.6
1.6
1.6
Direction of rotation (viewed from drive side)
Right R
Right R
Injection timing adjustment
Direction of rotation (viewed from drive side)
Right R
Right R
Injection order
1-3-4-2
Pre-stroke
mm
3.6
3.55
3.65
Beginning of injection position
Drive side NO.1
Drive side NO.1
Difference between angles 1
Cal 1-3 deg. 90 89.5 90.5
Cal 1-3 deg. 90 89.5 90.5
Difference between angles 2
Cal 1-4 deg. 180 179.5 180.5
Cal 1-4 deg. 180 179.5 180.5
Difference between angles 3
Cyl.1-2 deg. 270 269.5 270.5
Cyl.1-2 deg. 270 269.5 270.5
Injection quantity adjustment
Adjusting point
-
Rack position
11.3
Pump speed
r/min
1000
1000
1000
Average injection quantity
mm3/st.
69
68
70
Max. variation between cylinders
%
0
-2.5
2.5
Basic
*
Fixing the rack
*
Standard for adjustment of the maximum variation between cylinders
*
Injection quantity adjustment_02
Adjusting point
H
Rack position
9.5+-0.5
Pump speed
r/min
325
325
325
Average injection quantity
mm3/st.
10
8.7
11.3
Max. variation between cylinders
%
0
-13
13
Fixing the rack
*
Standard for adjustment of the maximum variation between cylinders
*
Injection quantity adjustment_03
Adjusting point
A
Rack position
R1(11.3)
Pump speed
r/min
1000
1000
1000
Average injection quantity
mm3/st.
69
68
70
Basic
*
Fixing the lever
*
Boost pressure
kPa
93.3
93.3
Boost pressure
mmHg
700
700
Injection quantity adjustment_04
Adjusting point
B
Rack position
R1+0.6
Pump speed
r/min
1700
1700
1700
Average injection quantity
mm3/st.
91
87
95
Fixing the lever
*
Boost pressure
kPa
93.3
93.3
Boost pressure
mmHg
700
700
Injection quantity adjustment_05
Adjusting point
C
Rack position
R2-1.1
Pump speed
r/min
680
680
680
Average injection quantity
mm3/st.
35
31
39
Fixing the lever
*
Boost pressure
kPa
0
0
0
Boost pressure
mmHg
0
0
0
Injection quantity adjustment_06
Adjusting point
I
Rack position
-
Pump speed
r/min
100
100
100
Average injection quantity
mm3/st.
67
67
72
Fixing the lever
*
Boost pressure
kPa
0
0
0
Boost pressure
mmHg
0
0
0
Rack limit
*
Boost compensator adjustment
Pump speed
r/min
700
700
700
Rack position
R2-1.1
Boost pressure
kPa
26.7
25.4
28
Boost pressure
mmHg
200
190
210
Boost compensator adjustment_02
Pump speed
r/min
700
700
700
Rack position
R2(R1-0.
3)
Boost pressure
kPa
80
73.3
80
Boost pressure
mmHg
600
550
600
Timer adjustment
Pump speed
r/min
1350--
Advance angle
deg.
0
0
0
Load
3/4
Remarks
Start
Start
Timer adjustment_02
Pump speed
r/min
1300
Advance angle
deg.
0.3
Load
3/4
Timer adjustment_03
Pump speed
r/min
1700
Advance angle
deg.
4.5
4
5
Load
4/4
Remarks
Finish
Finish
Test data Ex:
Governor adjustment
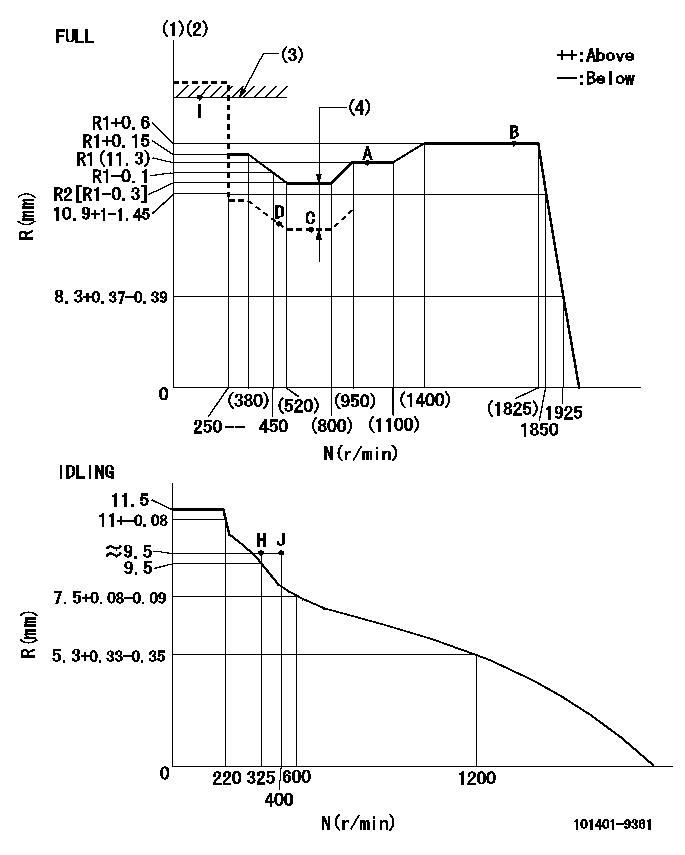
N:Pump speed
R:Rack position (mm)
(1)Torque cam stamping: T1
(2)Tolerance for racks not indicated: +-0.05mm.
(3)RACK LIMIT
(4)Boost compensator stroke: BCL
----------
T1=L36 BCL=1.1+-0.1mm
----------
----------
T1=L36 BCL=1.1+-0.1mm
----------
Speed control lever angle

F:Full speed
I:Idle
(1)Use the hole at R = aa
(2)Stopper bolt setting
----------
aa=40mm
----------
a=26deg+-5deg b=(42deg)+-3deg
----------
aa=40mm
----------
a=26deg+-5deg b=(42deg)+-3deg
Stop lever angle

N:Engine manufacturer's normal use
S:Stop the pump.
(1)Free (at delivery)
(2)Use the hole at R = aa
(3)Rack position corresponding to bb
(4)Set the stopper bolt so that speed = cc and rack position = dd. Confirm non-injection. After setting the stopper bolt, confirm non-injection at speed = ee (rack position = ff or less).
----------
aa=40mm bb=16mm cc=1700r/min dd=6.5-0.5mm ee=325r/min ff=(8)mm
----------
a=8deg+-5deg b=15deg+-5deg c=25deg+-5deg
----------
aa=40mm bb=16mm cc=1700r/min dd=6.5-0.5mm ee=325r/min ff=(8)mm
----------
a=8deg+-5deg b=15deg+-5deg c=25deg+-5deg
Timing setting
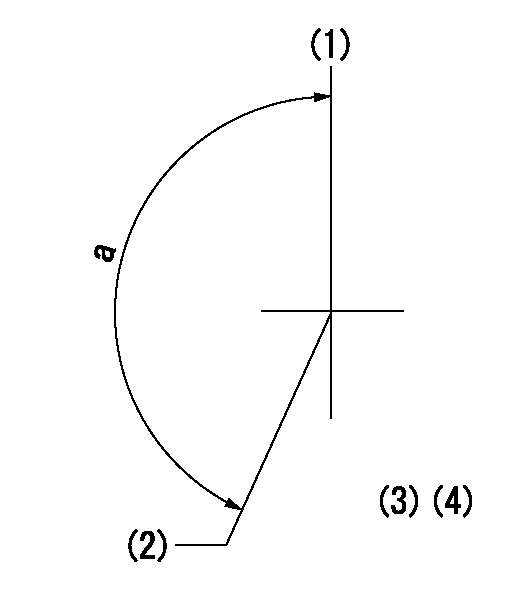
(1)Pump vertical direction
(2)Position of gear mark '3' at No 1 cylinder's beginning of injection
(3)B.T.D.C.: aa
(4)-
----------
aa=11deg
----------
a=(150deg)
----------
aa=11deg
----------
a=(150deg)
Information:
PARTS NEEDED
Qty
Part Number Description
1 4716029 MTG GP-INJECTOR (After Failure Only)
1 5548955 DEF SOFTWARE
1 ENGSOFTWARE ENGINE SOFTWARE
In order to allow equitable parts availability to all participating dealers, please limit your initial parts order to not exceed 25% of dealership population. This is an initial order recommendation only, and the ultimate responsibility for ordering the total number of parts needed to satisfy the program lies with the dealer.
ACTION REQUIRED
New DEF System software is available that reduces the risk of an internal DEF injector leak by improved temperature management. Please update the DEF system software at the next opportunity.
Ensure that all adjustments and repairs that are carried out to the Diesel Emission Fluid (DEF) system are performed by authorized personnel that have the correct training. Before beginning ANY work on the DEF system, refer to Operations and Maintenance Manual, "General Hazard" for safety information.
Before Failure:
Check that the engine software is the latest version before updating the DEF pump software.
If the engine software is not the latest version, update the Engine Software first.
If needed, update the engine software with the latest available in SIS WEB.
Flash the DEF Pump ECM with the software listed in the Parts Needed or latest available in SIS Web.
After Failure:
Ensure the appropriate steps have been followed when diagnosing a DEF injector failure. Refer to UENR0662.
If it is determined that replacement of DEF injector is required, refer to Disassembly and Assembly Manual - Diesel Fluid Injector - Remove and install.
After the DEF injector has been replaced, perform the DEF system software update as detailed in the "Before Failure" section above.
SERVICE CLAIM ALLOWANCES
Product smu/age whichever comes first Caterpillar Dealer Suggested Customer Suggested
Parts % Labor Hrs% Parts % Labor Hrs% Parts % Labor Hrs%
0-5000 hrs,
0-60 mo 100.0% 100.0% 0.0% 0.0% 0.0% 0.0%
This is a 0.5-hour job
An additional 1.5 hours is allowed for After failure.
PARTS DISPOSITION
Handle the parts in accordance with your Warranty Bulletin on warranty parts handling.
Have questions with 101401-9361?
Group cross 101401-9361 ZEXEL
Dpico
101401-9361
9 400 610 361
INJECTION-PUMP ASSEMBLY
4D31T
4D31T