Information injection-pump assembly
BOSCH
F 01G 09U 012
f01g09u012
ZEXEL
101401-7304
1014017304
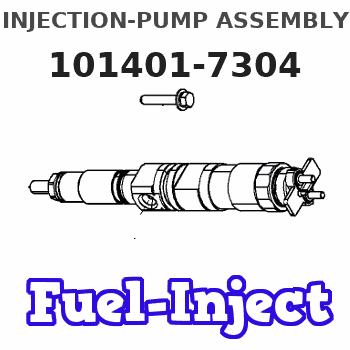
Rating:
Include in #1:
101601-5992
as _
Cross reference number
BOSCH
F 01G 09U 012
f01g09u012
ZEXEL
101401-7304
1014017304
Zexel num
Bosch num
Firm num
Name
Calibration Data:
Adjustment conditions
Test oil
1404 Test oil ISO4113 or {SAEJ967d}
1404 Test oil ISO4113 or {SAEJ967d}
Test oil temperature
degC
40
40
45
Nozzle and nozzle holder
105780-8250
Bosch type code
1 688 901 101
Nozzle
105780-0120
Bosch type code
1 688 901 990
Nozzle holder
105780-2190
Opening pressure
MPa
20.7
Opening pressure
kgf/cm2
211
Injection pipe
Outer diameter - inner diameter - length (mm) mm 6-2-600
Outer diameter - inner diameter - length (mm) mm 6-2-600
Overflow valve
134424-3920
Overflow valve opening pressure
kPa
127
107
147
Overflow valve opening pressure
kgf/cm2
1.3
1.1
1.5
Tester oil delivery pressure
kPa
255
255
255
Tester oil delivery pressure
kgf/cm2
2.6
2.6
2.6
Direction of rotation (viewed from drive side)
Left L
Left L
Injection timing adjustment
Direction of rotation (viewed from drive side)
Left L
Left L
Injection order
1-3-4-2
Pre-stroke
mm
3.8
3.75
3.85
Rack position
Point A R=A
Point A R=A
Beginning of injection position
Governor side NO.1
Governor side NO.1
Difference between angles 1
Cal 1-3 deg. 90 89.5 90.5
Cal 1-3 deg. 90 89.5 90.5
Difference between angles 2
Cal 1-4 deg. 180 179.5 180.5
Cal 1-4 deg. 180 179.5 180.5
Difference between angles 3
Cyl.1-2 deg. 270 269.5 270.5
Cyl.1-2 deg. 270 269.5 270.5
Injection quantity adjustment
Adjusting point
-
Rack position
13.1
Pump speed
r/min
1160
1160
1160
Average injection quantity
mm3/st.
97
95.4
98.6
Max. variation between cylinders
%
0
-4
4
Basic
*
Fixing the rack
*
Standard for adjustment of the maximum variation between cylinders
*
Injection quantity adjustment_02
Adjusting point
Z
Rack position
9.7+-0.5
Pump speed
r/min
285
285
285
Average injection quantity
mm3/st.
14.5
13.2
15.8
Max. variation between cylinders
%
0
-14
14
Fixing the rack
*
Standard for adjustment of the maximum variation between cylinders
*
Injection quantity adjustment_03
Adjusting point
A
Rack position
R1(13.1)
Pump speed
r/min
1160
1160
1160
Average injection quantity
mm3/st.
97
96
98
Basic
*
Fixing the lever
*
Boost pressure
kPa
60
Boost pressure
mmHg
450
Injection quantity adjustment_04
Adjusting point
B
Rack position
R1+0.35
Pump speed
r/min
1450
1450
1450
Average injection quantity
mm3/st.
96.5
92.5
100.5
Fixing the lever
*
Boost pressure
kPa
60
Boost pressure
mmHg
450
Injection quantity adjustment_05
Adjusting point
C
Rack position
R2-0.45
Pump speed
r/min
700
700
700
Average injection quantity
mm3/st.
86
82
90
Fixing the lever
*
Boost pressure
kPa
0
0
0
Boost pressure
mmHg
0
0
0
Injection quantity adjustment_06
Adjusting point
I
Rack position
-
Pump speed
r/min
150
150
150
Average injection quantity
mm3/st.
95
95
127
Fixing the lever
*
Boost pressure
kPa
0
0
0
Boost pressure
mmHg
0
0
0
Boost compensator adjustment
Pump speed
r/min
700
700
700
Rack position
R2-0.45
Boost pressure
kPa
27.3
26
28.6
Boost pressure
mmHg
205
195
215
Boost compensator adjustment_02
Pump speed
r/min
700
700
700
Rack position
R2(R1-0.
6)
Boost pressure
kPa
46.7
46.7
46.7
Boost pressure
mmHg
350
350
350
Timer adjustment
Pump speed
r/min
1185--
Advance angle
deg.
0
0
0
Remarks
Start
Start
Timer adjustment_02
Pump speed
r/min
1135
Advance angle
deg.
0.5
Timer adjustment_03
Pump speed
r/min
1450
Advance angle
deg.
4.8
4.75
4.85
Timer adjustment_04
Pump speed
r/min
-
Advance angle
deg.
5
4.5
5.5
Remarks
Measure the actual speed, stop
Measure the actual speed, stop
Test data Ex:
Governor adjustment
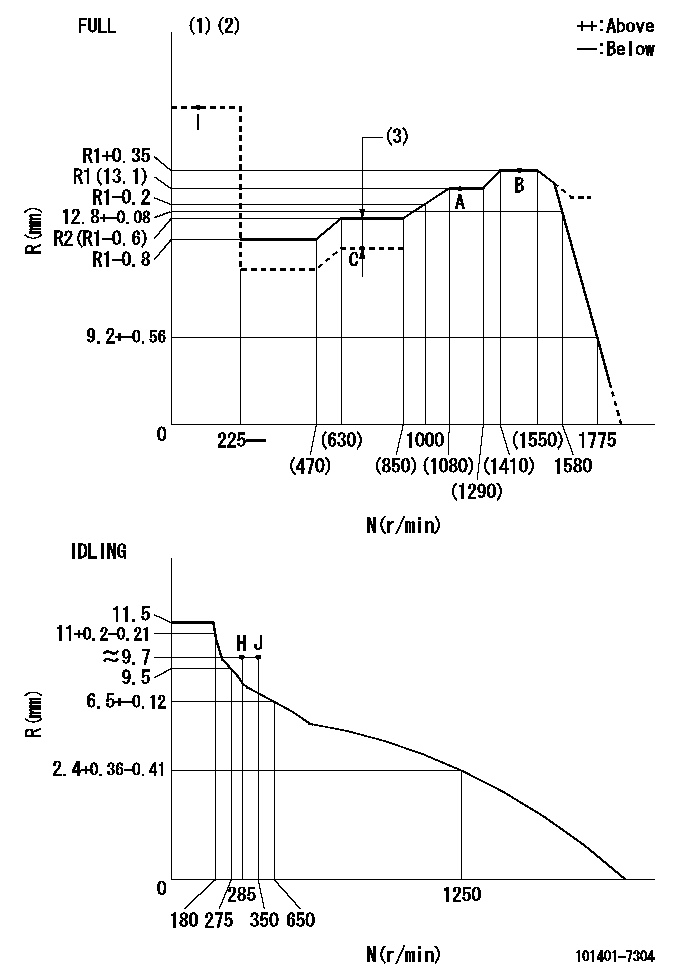
N:Pump speed
R:Rack position (mm)
(1)Torque cam stamping: T1
(2)Tolerance for racks not indicated: +-0.05mm.
(3)Boost compensator stroke: BCL
----------
T1=K06 BCL=0.45+-0.1mm
----------
----------
T1=K06 BCL=0.45+-0.1mm
----------
Speed control lever angle

F:Full speed
I:Idle
(1)Stopper bolt set position 'H'
----------
----------
a=42deg+-5deg b=(41deg)+-3deg
----------
----------
a=42deg+-5deg b=(41deg)+-3deg
Stop lever angle

N:Pump normal
S:Stop the pump.
(1)Use the hole at R = aa
----------
aa=64mm
----------
a=20deg+-5deg b=29deg+-5deg
----------
aa=64mm
----------
a=20deg+-5deg b=29deg+-5deg
0000001501 FICD
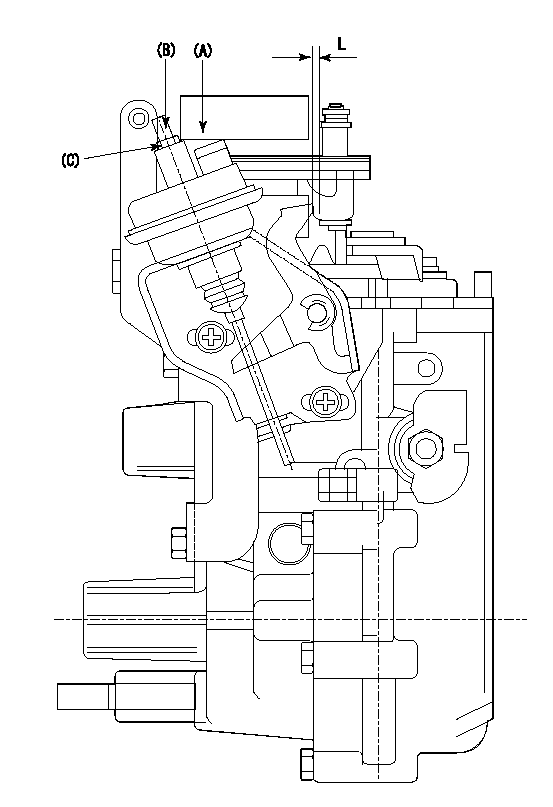
(A) applied negative pressure
(B) Screw
(c) Nut
1. Set the actuator as described below.
(1)Confirm that there is clearance between the actuator lever and the speed lever.
(2)Loosen the nut (C).
(3)Push in the screw (B).
(4)Apply P1 from the actuator (A) part.
(5)Pull out the screw (B) slowly.
(6)Tighten and fix the nut (C) when pump speed is Na and the rack position is Ra.
(7)Torque the nut (C) to T1.
(8)Apply P2 several times.
(9)Confirm that the actuator functions normally.
(10)Confirm that there is a clearance between the actuator lever and the speed lever at that time.
----------
P1=53.3kPa(400mmHg) P2=53.3kPa(400mmHg) Na=475r/min Ra=9.75+-0.1mm T1=1.2~1.6N-m(0.12~0.16kgf-m)
----------
L=(5)mm
----------
P1=53.3kPa(400mmHg) P2=53.3kPa(400mmHg) Na=475r/min Ra=9.75+-0.1mm T1=1.2~1.6N-m(0.12~0.16kgf-m)
----------
L=(5)mm
0000001601 MICRO SWITCH
Adjustment of the micro-switch
Adjust the bolt to obtain the following lever position when the micro-switch is ON.
(1)Speed N1
(2)Rack position Ra
----------
N1=1100r/min Ra=9.4+-0.1mm
----------
----------
N1=1100r/min Ra=9.4+-0.1mm
----------
Timing setting

(1)Pump vertical direction
(2)Position of gear's standard threaded hole at No 1 cylinder's beginning of injection
(3)Stamping position on the A/T outer rim
(4)At the No 1 cylinder's beginning of injection, align with the aligning mark seen through the bracket's check hole and mark the A/T's bevel C1.
(5)B.T.D.C.: aa
----------
aa=7deg
----------
a=(60deg) b=(85deg)
----------
aa=7deg
----------
a=(60deg) b=(85deg)
Information:
(1) Fuel pump adapter assembly diameter ... 88.864 to 88.887 mm (3.4986 to 3.4995 in.) Bore diameter in cylinder block for fuel pump adapter assembly and upper thrust collar ... 88.90 to 88.936 mm (3.500 to 3.5014 in.)Clearance of adapter assembly in cylinder block ... 0.013 to 0.071 mm (.0005 to .0028 in.)(2) Inside diameter of bushing in adapter assembly ... 47.625 to 47.666 mm (1.8750 to 1.8766 in.) Upper fuel pump drive shaft diameter ... 47.533 to 47.574 mm (1.8714 to 1.8730 in.)Clearance of drive shaft in adapter assembly bushing ... 0.05 to 0.132 mm (.002 to .0052 in.)(3) Outside diameter of upper thrust collar ... 88.80 to 88.85 mm (3.496 to 3.498 in.) Clearance of upper thrust collar in block ... 0.05 to 0.137 mm (.002 to .0054 in.)Inside diameter of upper thrust collar ... 47.90 to 48.01 mm (1.886 to 1.890 in.)Clearance of fuel pump drive shaft in thrust collar ... 0.33 to 0.472 mm (.013 to .0186 in.)Width of groove in upper thrust collar ... 2.431 to 2.456 mm (.0957 to .0967 in.)(4) Upper thrust collar sealing ring thickness ... 2.357 to 2.383 mm (.0928 to .0938 in.) Clearance of sealing ring in groove ... 0.048 to 0.099 mm (.0019 to .0039 in.)(5) Bore diameter in cylinder block for lower thrust bearing ... 57.127 to 57.147 mm (2.2491 to 2.2499 in.) Lower thrust bearing bore diameter for bushing ... 45.242 to 45.283 mm (1.7812 to 1.7828 in.)(6) Outer diameter of bushing ... 45.321 to 45.357 mm (1.7843 to 1.7857 in.) Interference fit of bushing in lower thrust bearing ... 0.038 to 0.114 mm (.0015 to .0045 in.)Inside diameter of bushing (after reaming) ... 41.288 to 41.316 mm (1.6255 to 1.6266 in.)Lower diameter of fuel pump drive shaft ... 41.184 to 41.209 mm (1.6214 to 1.6224 in.)Clearance of fuel pump drive shaft in bushing ... 0.079 to 0.132 mm (.0031 to .0052 in.)(7) Auxiliary drive shaft rear bushing: Outside diameter of bushing ... 35.778 to 35.827 mm (1.4086 to 1.4105 in.)Bore diameter in cylinder block for rear bushing ... 35.720 to 35.753 mm (1.4063 to 1.4076 in.)Interference fit of bushing in cylinder block ... 0.03 to 0.107 mm (.001 to .0042 in.)Inside diameter of installed bushing ... 31.75 to 31.799 mm (1.25 to 1.2519 in.)Running clearance of auxiliary drive shaft in bushing ... 0.03 to 0.099 mm (.001 to .0039 in.)(8) Torque for auxiliary drive shaft gear bolts ... 30 N m (22 lb.ft.)(9) Auxiliary drive shaft gear bore diameter ... 25.40 to 25.43 mm (1.000 to 1.001 in.)(10) Auxiliary drive shaft thrust washers: Thickness ... 4.763 to 4.839 mm (.1875 to .1905 in.)Cylinder block recess depth for thrust washer ... 4.67 to 4.75 mm (.184 to .187 in.)Projection of thrust washer above cylinder block front face ... 0.013 to 0.18 mm (.0005 to .007 in.)Outside