Information injection-pump assembly
ZEXEL
101401-4931
1014014931
ISUZU
8971001100
8971001100
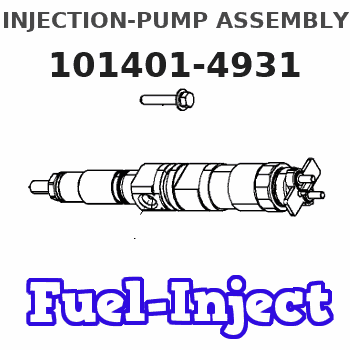
Rating:
Cross reference number
ZEXEL
101401-4931
1014014931
ISUZU
8971001100
8971001100
Zexel num
Bosch num
Firm num
Name
101401-4931
8971001100 ISUZU
INJECTION-PUMP ASSEMBLY
4HG1 * K
4HG1 * K
Calibration Data:
Adjustment conditions
Test oil
1404 Test oil ISO4113 or {SAEJ967d}
1404 Test oil ISO4113 or {SAEJ967d}
Test oil temperature
degC
40
40
45
Nozzle and nozzle holder
105780-8140
Bosch type code
EF8511/9A
Nozzle
105780-0000
Bosch type code
DN12SD12T
Nozzle holder
105780-2080
Bosch type code
EF8511/9
Opening pressure
MPa
17.2
Opening pressure
kgf/cm2
175
Injection pipe
Outer diameter - inner diameter - length (mm) mm 6-2-600
Outer diameter - inner diameter - length (mm) mm 6-2-600
Overflow valve
134424-3920
Overflow valve opening pressure
kPa
127
107
147
Overflow valve opening pressure
kgf/cm2
1.3
1.1
1.5
Tester oil delivery pressure
kPa
157
157
157
Tester oil delivery pressure
kgf/cm2
1.6
1.6
1.6
Direction of rotation (viewed from drive side)
Left L
Left L
Injection timing adjustment
Direction of rotation (viewed from drive side)
Left L
Left L
Injection order
1-3-4-2
Pre-stroke
mm
4.1
4.05
4.15
Rack position
Point A R=A
Point A R=A
Beginning of injection position
Governor side NO.1
Governor side NO.1
Difference between angles 1
Cal 1-3 deg. 90 89.5 90.5
Cal 1-3 deg. 90 89.5 90.5
Difference between angles 2
Cal 1-4 deg. 180 179.5 180.5
Cal 1-4 deg. 180 179.5 180.5
Difference between angles 3
Cyl.1-2 deg. 270 269.5 270.5
Cyl.1-2 deg. 270 269.5 270.5
Injection quantity adjustment
Adjusting point
-
Rack position
12.5
Pump speed
r/min
960
960
960
Average injection quantity
mm3/st.
74.5
72.9
76.1
Max. variation between cylinders
%
0
-4
4
Basic
*
Fixing the rack
*
Standard for adjustment of the maximum variation between cylinders
*
Injection quantity adjustment_02
Adjusting point
H
Rack position
9.8+-0.5
Pump speed
r/min
285
285
285
Average injection quantity
mm3/st.
10
8.7
11.3
Max. variation between cylinders
%
0
-10
10
Fixing the rack
*
Standard for adjustment of the maximum variation between cylinders
*
Injection quantity adjustment_03
Adjusting point
A
Rack position
R1(12.5)
Pump speed
r/min
960
960
960
Average injection quantity
mm3/st.
74.5
73.5
75.5
Basic
*
Fixing the lever
*
Injection quantity adjustment_04
Adjusting point
B
Rack position
R1+0.45
Pump speed
r/min
1600
1600
1600
Average injection quantity
mm3/st.
91
87
95
Fixing the lever
*
Injection quantity adjustment_05
Adjusting point
C
Rack position
R1-0.15
Pump speed
r/min
520
520
520
Average injection quantity
mm3/st.
53.5
49.5
57.5
Fixing the lever
*
Injection quantity adjustment_06
Adjusting point
D
Rack position
R1+0.25
Pump speed
r/min
1310
1310
1310
Average injection quantity
mm3/st.
85.5
81.5
89.5
Fixing the lever
*
Timer adjustment
Pump speed
r/min
1150--
Advance angle
deg.
0
0
0
Remarks
Start
Start
Timer adjustment_02
Pump speed
r/min
1100
Advance angle
deg.
0.5
Timer adjustment_03
Pump speed
r/min
1600
Advance angle
deg.
6
5.5
6.5
Remarks
Finish
Finish
Test data Ex:
Governor adjustment
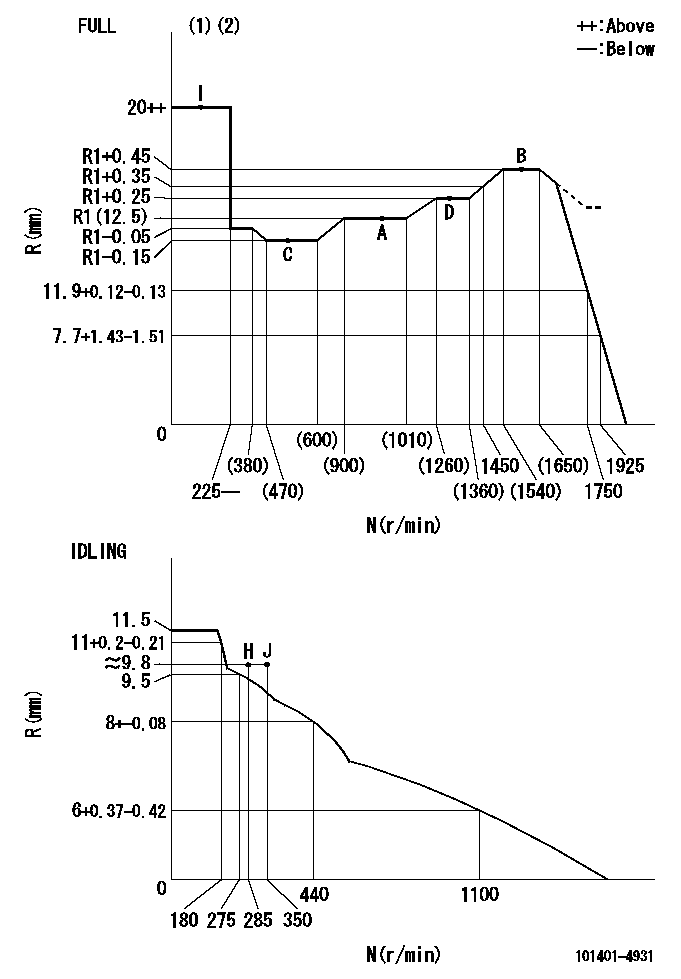
N:Pump speed
R:Rack position (mm)
(1)Torque cam stamping: T1
(2)Tolerance for racks not indicated: +-0.05mm.
----------
T1=J79
----------
----------
T1=J79
----------
Speed control lever angle

F:Full speed
I:Idle
(1)Stopper bolt set position 'H'
----------
----------
a=41deg+-5deg b=34deg+-3deg
----------
----------
a=41deg+-5deg b=34deg+-3deg
Stop lever angle
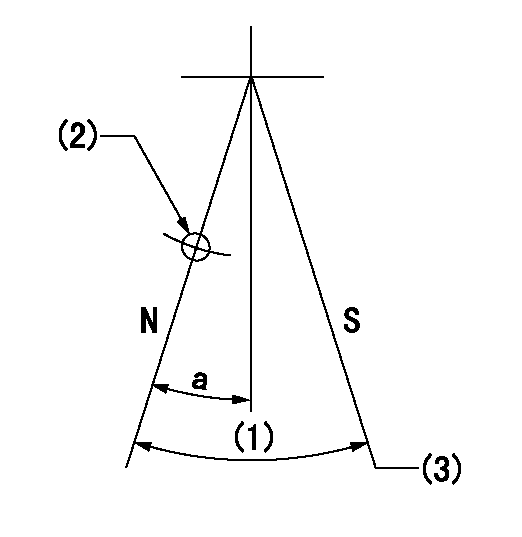
N:Pump normal
S:Stop the pump.
(1)(Actual measurement)
(2)Use the hole at R = aa
(3)At pump speed bb and rack position cc, set the stopper bolt.
----------
aa=25mm bb=1600r/min cc=5-0.5mm
----------
a=15deg+-5deg
----------
aa=25mm bb=1600r/min cc=5-0.5mm
----------
a=15deg+-5deg
0000001501 FICD
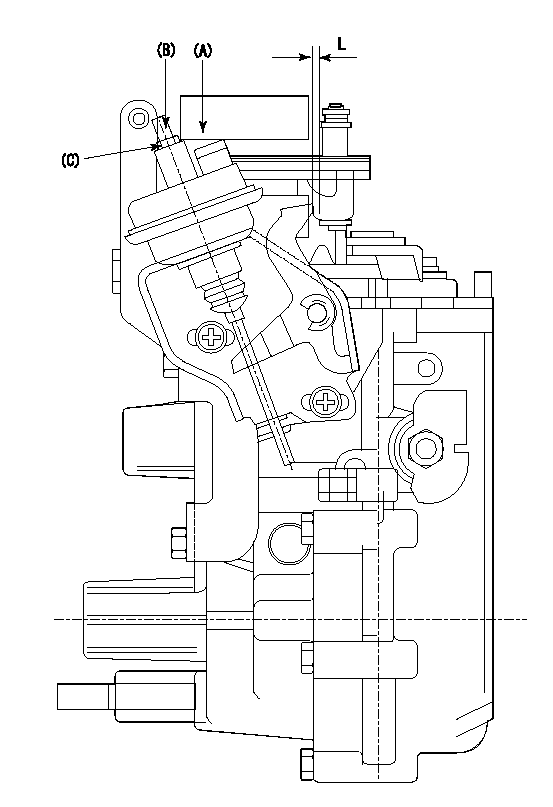
(A) applied negative pressure
(B) Screw
(c) Nut
1. Set the actuator as described below.
(1)Confirm that there is clearance between the actuator lever and the speed lever.
(2)Loosen the nut (C).
(3)Push in the screw (B).
(4)Apply P1 from the actuator (A) part.
(5)Pull out the screw (B) slowly.
(6)Tighten and fix the nut (C) when pump speed is Na and the rack position is Ra.
(7)Torque the nut (C) to T1.
(8)Apply P2 several times.
(9)Confirm that the actuator functions normally.
(10)Confirm that there is a clearance between the actuator lever and the speed lever at that time.
----------
P1=53.3kPa(400mmHg) P2=53.3kPa(400mmHg) Na=400r/min Ra=9.2+-0.1mm T1=1.2~1.6N-m(0.12~0.16kgf-m)
----------
L=(5)mm
----------
P1=53.3kPa(400mmHg) P2=53.3kPa(400mmHg) Na=400r/min Ra=9.2+-0.1mm T1=1.2~1.6N-m(0.12~0.16kgf-m)
----------
L=(5)mm
0000001601 RACK SENSOR
Rack sensor adjustment
(1)These types of rack sensors do not need adjustment. Confirm the output as described below.
(2)Mount the rack sensor main body to the pump main body.
(3)Measure the Vist at pump speed N1 and rack position Ra.
----------
N1=1600r/min Ra=R1(12.5)+0.45mm
----------
----------
N1=1600r/min Ra=R1(12.5)+0.45mm
----------
Timing setting

(1)Pump vertical direction
(2)Position of gear's standard threaded hole at No 1 cylinder's beginning of injection
(3)Timing device stamping
(4)At the No 1 cylinder's beginning of injection, align with the projection seen through the bracket's check hole and mark the A/T's bevel C1.
(5)B.T.D.C.: aa
----------
aa=7deg
----------
a=(60deg) b=(85deg)
----------
aa=7deg
----------
a=(60deg) b=(85deg)
Information:
Proper operation and maintenance are key factors in obtaining the maximum life and economy of the engine. Following the directions in this manual will lower operating costs.The time needed for the engine to reach the normal mode of operation is usually less than the time taken for a walk-around-inspection of the engine.After the engine is started and the cold low idle operation is completed, the engine can be operated at rated speed and low power. The engine will reach normal operating temperature faster when operated at rated speed and low power demand than when idled at no load. Typically the engine should be up to operating temperature in a few minutes.Gauges readings should be observed and the data record frequently while the engine is operating. Comparing the data over time will help determine normal readings for each gauge, and help detect abnormal operating developments. Significant changes in the readings should be investigated.Fuel Conservation Practices
The efficiency of your engine can affect the fuel economy. Caterpillar's state-of-the-art design and manufacturing technology provides maximum fuel efficiency in all applications. Follow the recommended operating and maintenance procedures to attain optimum performance for the life of your engine.* Avoid fuel spillage. Fuel expands when warmed, and may overflow from a too-full fuel tank. Inspect fuel lines for leaks, and repair immediately.* Be aware of the heat values of different fuels. Use only recommended fuels.* Avoid unnecessary idling. Shut the engine off rather than idle for long periods of time (unless the temperature is extremely cold).* Observe the air service indicator frequently, and keep the air cleaner elements clean.* Make sure that turbochargers are operating correctly so that the proper air/fuel ratio is maintained. Clean exhaust indicated proper functioning.* Maintain a good electrical system. One bad battery cell will overwork the alternator, consuming excess power and fuel.* Make sure that belts are properly adjusted and in good condition.* Make sure that all air hose connections are tight and do not leak.* Cold engines consume excess fuel. Utilize jacket water and exhaust system heat when possible. Keep radiator fins and water pumps clean and in good repair. Never operate without thermostats. All of these items will help maintain operating temperatures.* Fuel system settings and altitude limits are stamped on the engine Information Plate. If an engine is moved to a higher altitude, settings must be changed by a Caterpillar dealer in order to prevent turbocharger damage and provide maximum engine efficiency. Engines can be operated safely at lower altitudes, but will deliver less horsepower. The fuel settings should be changed by a Caterpillar dealer to obtain the rated horsepower.
The efficiency of your engine can affect the fuel economy. Caterpillar's state-of-the-art design and manufacturing technology provides maximum fuel efficiency in all applications. Follow the recommended operating and maintenance procedures to attain optimum performance for the life of your engine.* Avoid fuel spillage. Fuel expands when warmed, and may overflow from a too-full fuel tank. Inspect fuel lines for leaks, and repair immediately.* Be aware of the heat values of different fuels. Use only recommended fuels.* Avoid unnecessary idling. Shut the engine off rather than idle for long periods of time (unless the temperature is extremely cold).* Observe the air service indicator frequently, and keep the air cleaner elements clean.* Make sure that turbochargers are operating correctly so that the proper air/fuel ratio is maintained. Clean exhaust indicated proper functioning.* Maintain a good electrical system. One bad battery cell will overwork the alternator, consuming excess power and fuel.* Make sure that belts are properly adjusted and in good condition.* Make sure that all air hose connections are tight and do not leak.* Cold engines consume excess fuel. Utilize jacket water and exhaust system heat when possible. Keep radiator fins and water pumps clean and in good repair. Never operate without thermostats. All of these items will help maintain operating temperatures.* Fuel system settings and altitude limits are stamped on the engine Information Plate. If an engine is moved to a higher altitude, settings must be changed by a Caterpillar dealer in order to prevent turbocharger damage and provide maximum engine efficiency. Engines can be operated safely at lower altitudes, but will deliver less horsepower. The fuel settings should be changed by a Caterpillar dealer to obtain the rated horsepower.
Have questions with 101401-4931?
Group cross 101401-4931 ZEXEL
Isuzu
Isuzu
Isuzu
Isuzu
101401-4931
8971001100
INJECTION-PUMP ASSEMBLY
4HG1
4HG1