Information injection-pump assembly
BOSCH
9 400 610 400
9400610400
ZEXEL
101401-4900
1014014900
ISUZU
8971153610
8971153610
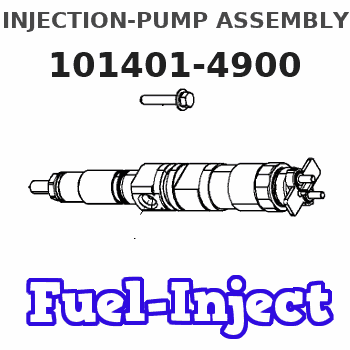
Rating:
Service parts 101401-4900 INJECTION-PUMP ASSEMBLY:
1.
_
6.
COUPLING PLATE
7.
COUPLING PLATE
8.
_
9.
_
11.
Nozzle and Holder
8-97114-017-0
12.
Open Pre:MPa(Kqf/cm2)
18.1{185}
15.
NOZZLE SET
Cross reference number
BOSCH
9 400 610 400
9400610400
ZEXEL
101401-4900
1014014900
ISUZU
8971153610
8971153610
Zexel num
Bosch num
Firm num
Name
101401-4900
9 400 610 400
8971153610 ISUZU
INJECTION-PUMP ASSEMBLY
4HF1 * K 14BC PE4A,5A, PE
4HF1 * K 14BC PE4A,5A, PE
Calibration Data:
Adjustment conditions
Test oil
1404 Test oil ISO4113 or {SAEJ967d}
1404 Test oil ISO4113 or {SAEJ967d}
Test oil temperature
degC
40
40
45
Nozzle and nozzle holder
105780-8140
Bosch type code
EF8511/9A
Nozzle
105780-0000
Bosch type code
DN12SD12T
Nozzle holder
105780-2080
Bosch type code
EF8511/9
Opening pressure
MPa
17.2
Opening pressure
kgf/cm2
175
Injection pipe
Outer diameter - inner diameter - length (mm) mm 6-2-600
Outer diameter - inner diameter - length (mm) mm 6-2-600
Overflow valve
131424-4920
Overflow valve opening pressure
kPa
127
107
147
Overflow valve opening pressure
kgf/cm2
1.3
1.1
1.5
Tester oil delivery pressure
kPa
157
157
157
Tester oil delivery pressure
kgf/cm2
1.6
1.6
1.6
Direction of rotation (viewed from drive side)
Left L
Left L
Injection timing adjustment
Direction of rotation (viewed from drive side)
Left L
Left L
Injection order
1-3-4-2
Pre-stroke
mm
4.1
4.05
4.15
Rack position
Point A R=A
Point A R=A
Beginning of injection position
Governor side NO.1
Governor side NO.1
Difference between angles 1
Cal 1-3 deg. 90 89.5 90.5
Cal 1-3 deg. 90 89.5 90.5
Difference between angles 2
Cal 1-4 deg. 180 179.5 180.5
Cal 1-4 deg. 180 179.5 180.5
Difference between angles 3
Cyl.1-2 deg. 270 269.5 270.5
Cyl.1-2 deg. 270 269.5 270.5
Injection quantity adjustment
Adjusting point
-
Rack position
12.6
Pump speed
r/min
1100
1100
1100
Average injection quantity
mm3/st.
75.4
73.8
77
Max. variation between cylinders
%
0
-4
4
Basic
*
Fixing the rack
*
Standard for adjustment of the maximum variation between cylinders
*
Injection quantity adjustment_02
Adjusting point
H
Rack position
9.8+-0.5
Pump speed
r/min
285
285
285
Average injection quantity
mm3/st.
15.5
14.2
16.8
Max. variation between cylinders
%
0
-10
10
Fixing the rack
*
Standard for adjustment of the maximum variation between cylinders
*
Injection quantity adjustment_03
Adjusting point
A
Rack position
R1(12.6)
Pump speed
r/min
1100
1100
1100
Average injection quantity
mm3/st.
75.4
74.4
76.4
Basic
*
Fixing the lever
*
Injection quantity adjustment_04
Adjusting point
B
Rack position
R1+0.2
Pump speed
r/min
1600
1600
1600
Average injection quantity
mm3/st.
86.3
82.3
90.3
Fixing the lever
*
Injection quantity adjustment_05
Adjusting point
I
Rack position
-
Pump speed
r/min
150
150
150
Average injection quantity
mm3/st.
80
80
112
Fixing the lever
*
Timer adjustment
Pump speed
r/min
1375--
Advance angle
deg.
0
0
0
Remarks
Start
Start
Timer adjustment_02
Pump speed
r/min
1325
Advance angle
deg.
0.3
Timer adjustment_03
Pump speed
r/min
1500
Advance angle
deg.
3.3
2.8
3.8
Timer adjustment_04
Pump speed
r/min
1600--
Advance angle
deg.
5
4.5
5.5
Remarks
Finish
Finish
Test data Ex:
Governor adjustment
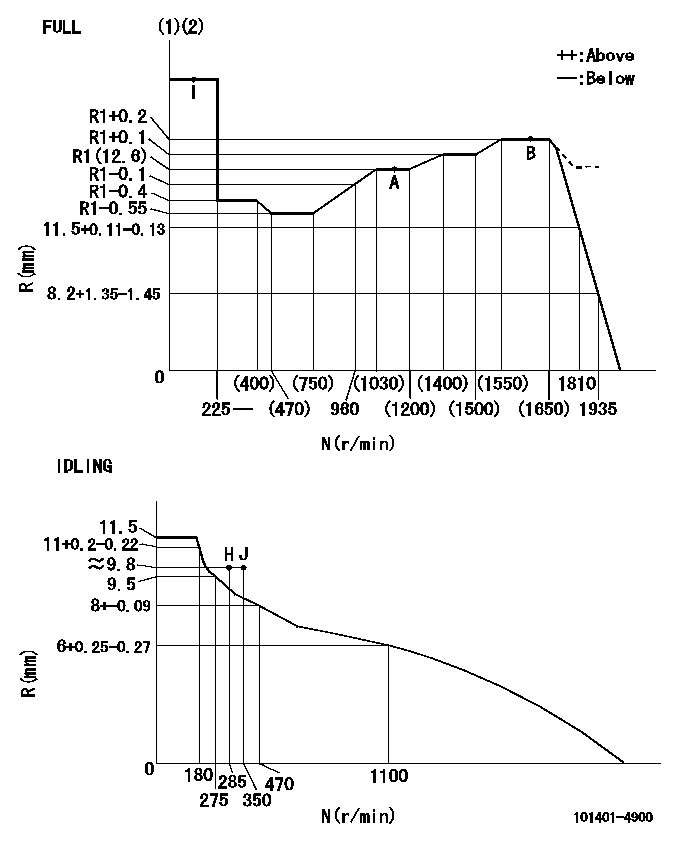
N:Pump speed
R:Rack position (mm)
(1)Torque cam stamping: T1
(2)Tolerance for racks not indicated: +-0.05mm.
----------
T1=H96
----------
----------
T1=H96
----------
Speed control lever angle

F:Full speed
I:Idle
(1)Stopper bolt setting
----------
----------
a=41deg+-5deg b=35deg+-3deg
----------
----------
a=41deg+-5deg b=35deg+-3deg
Stop lever angle
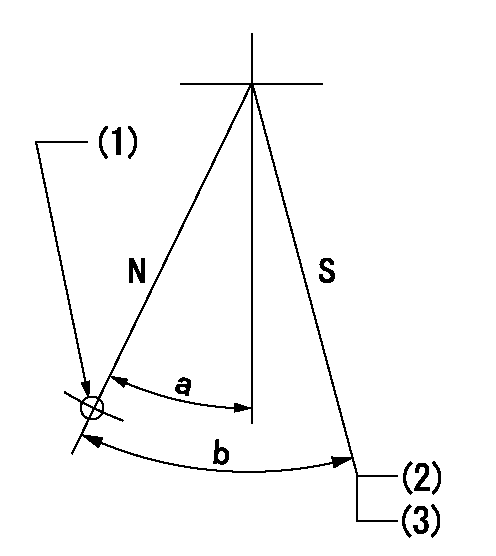
N:Pump normal
S:Stop the pump.
(1)Use the hole at R = aa
(2)At pump speed bb and rack position cc, set the stopper bolt.
(3)After setting, confirm non-injection at speed = dd.
----------
aa=58mm bb=1600r/min cc-5+-0.2mm dd=285r/min
----------
a=23deg+-5deg b=29deg+-3deg
----------
aa=58mm bb=1600r/min cc-5+-0.2mm dd=285r/min
----------
a=23deg+-5deg b=29deg+-3deg
0000001501 FICD
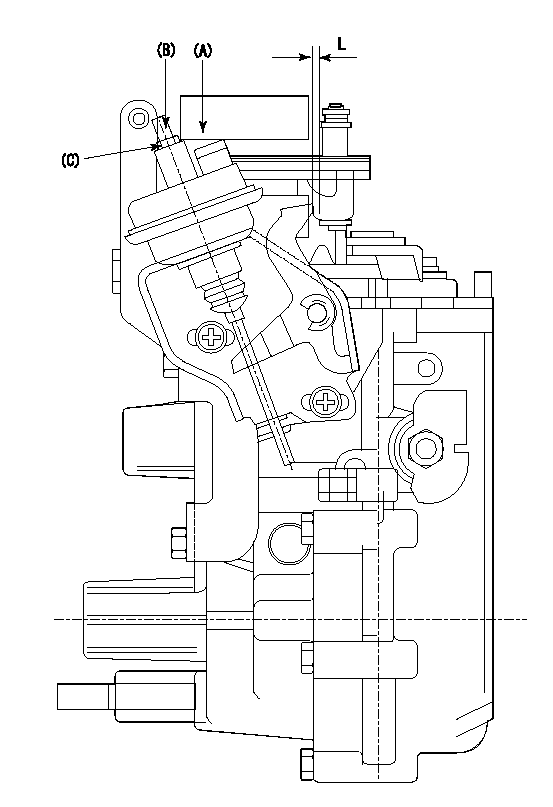
(A) applied negative pressure
(B) Screw
(c) Nut
1. Set the actuator as described below.
(1)Confirm that there is clearance between the actuator lever and the speed lever.
(2)Loosen the nut (C).
(3)Push in the screw (B).
(4)Apply P1 from the actuator (A) part.
(5)Pull out the screw (B) slowly.
(6)Tighten and fix the nut (C) when pump speed is Na and the rack position is Ra.
(7)Torque the nut (C) to T1.
(8)Apply P2 several times.
(9)Confirm that the actuator functions normally.
(10)Confirm that there is a clearance between the actuator lever and the speed lever at that time.
----------
P1=53.3kPa(400mmHg) P2=53.3kPa(400mmHg) Na=440r/min Ra=9.2+-0.1mm T1=1.2~1.6N-m(0.12~0.16kgf-m)
----------
L=(5)mm
----------
P1=53.3kPa(400mmHg) P2=53.3kPa(400mmHg) Na=440r/min Ra=9.2+-0.1mm T1=1.2~1.6N-m(0.12~0.16kgf-m)
----------
L=(5)mm
Timing setting
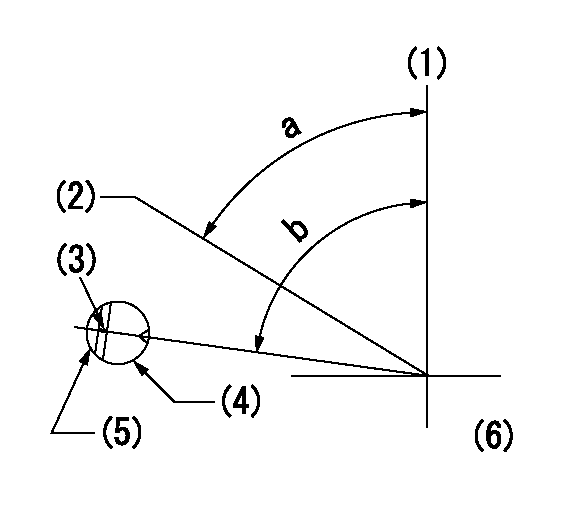
(1)Pump vertical direction
(2)Position of gear's standard threaded hole at No 1 cylinder's beginning of injection
(3)Stamping position on the A/T outer rim
(4)Pump bracket check hole position.
(5)At the No 1 cylinder's beginning of injection, align with the projection seen through the bracket's check hole and mark the A/T's bevel C1.
(6)B.T.D.C.: aa
----------
aa=10deg
----------
a=(60deg) b=(85deg)
----------
aa=10deg
----------
a=(60deg) b=(85deg)
Information:
Failure to follow these oil recommendations can cause shortened engine life due to deposits and or excessive wear.
Total Base Number (TBN) and Fuel Sulfur Levels For Caterpillar Prechamber Combustion (PC) Diesel Engines
New engine oil must have a TBN of 20 times (for Precombustion Chamber engines) and ten times (for direct injection engines) the percent fuel sulfur as measured by ASTM D2896 method. Refer to the following chart.
Y=oil TBN shown by ASTM D2896. X=percent of fuel sulfur by weight. New oil TBN (1). Change oil when the used oil TBN limit (2) is reached.Caterpillar's 20 times rule for TBN (Reference: Oil and Your Engine, SEBD0640) versus fuel sulfur was a general requirement developed in the early 1980's for Cat prechamber combustion (PC) system engines. Caterpillar still maintains 20 times TBN value for PC engines when using API CE or CF-4 oil (related to fuel sulfur above 0.5 percent). Engines built prior to 1990 can continue to use single grade viscosity oil or commercial oils, provided the engine operates to user satisfaction.Fuel sulfur neutralization of new oil formulations in direct injection (DI) system engines are more effective. Field results indicate that direct injection combustion (DI) systems and the oils now recommended for those engines will operate at an oil TBN equal to ten times the fuel sulfur.Total Base Number (TBN) and Fuel Sulfur Levels For Caterpillar Direct Injection (DI) Diesel Engines
The TBN for a new oil is dependent on the sulfur level of the fuel used. For direct injection engines running distillate diesel fuel, the minimum new oil TBN (by ASTM D 2896) must be 10 times the fuel sulfur level, and the minimum TBN is 5 regardless of sulfur level, see the chart below.TBN vs Fuel Sulfur for Caterpillar DI Diesel Engines
Y=oil TBN shown by ASTM D2896. X=percent of fuel sulfur by weight. New oil TBN (1). Change oil when the used oil TBN limit (2) is reached.In areas where the fuel sulfur exceeds 1.5 percent, choose an oil with the highest TBN that is within the API CF-4 or CG-4 categories, and shorten the oil change period based on oil analysis. The oil analysis should evaluate oil condition and wear metals. High TBN oils that are not within the API CF-4 or CG-4 categories can produce excessive piston deposits leading to a loss of oil control and bore polishing.
Operation at fuel sulfur levels over 1.5 percent may require shortened oil change periods to maintain adequate wear protection.
Lubricant Viscosity Recommendations
The proper SAE viscosity grade oil is determined by the minimum outside temperature at cold engine start up, and the maximum outside temperature during engine operation. Use the minimum temperature column on the chart to determine the oil viscosity required for starting a "cold soaked" engine. Use the maximum temperature column on the chart to select the viscosity for operation at the highest temperature anticipated. In general, use the highest viscosity oil available that still meets the start up temperature requirements. Synthetic Base Stock Oils
Synthetic base stock oils are acceptable
Have questions with 101401-4900?
Group cross 101401-4900 ZEXEL
Isuzu
101401-4900
9 400 610 400
8971153610
INJECTION-PUMP ASSEMBLY
4HF1
4HF1