Information injection-pump assembly
ZEXEL
101401-4820
1014014820
ISUZU
8971076500
8971076500

Rating:
Service parts 101401-4820 INJECTION-PUMP ASSEMBLY:
1.
_
6.
COUPLING PLATE
7.
COUPLING PLATE
8.
_
9.
_
11.
Nozzle and Holder
8-97114-016-0
12.
Open Pre:MPa(Kqf/cm2)
18.1{185}
15.
NOZZLE SET
Cross reference number
ZEXEL
101401-4820
1014014820
ISUZU
8971076500
8971076500
Zexel num
Bosch num
Firm num
Name
Calibration Data:
Adjustment conditions
Test oil
1404 Test oil ISO4113 or {SAEJ967d}
1404 Test oil ISO4113 or {SAEJ967d}
Test oil temperature
degC
40
40
45
Nozzle and nozzle holder
105780-8140
Bosch type code
EF8511/9A
Nozzle
105780-0000
Bosch type code
DN12SD12T
Nozzle holder
105780-2080
Bosch type code
EF8511/9
Opening pressure
MPa
17.2
Opening pressure
kgf/cm2
175
Injection pipe
Outer diameter - inner diameter - length (mm) mm 6-2-600
Outer diameter - inner diameter - length (mm) mm 6-2-600
Overflow valve
131424-4920
Overflow valve opening pressure
kPa
127
107
147
Overflow valve opening pressure
kgf/cm2
1.3
1.1
1.5
Tester oil delivery pressure
kPa
157
157
157
Tester oil delivery pressure
kgf/cm2
1.6
1.6
1.6
Direction of rotation (viewed from drive side)
Left L
Left L
Injection timing adjustment
Direction of rotation (viewed from drive side)
Left L
Left L
Injection order
1-3-4-2
Pre-stroke
mm
4.1
4.05
4.15
Rack position
Point A R=A
Point A R=A
Beginning of injection position
Governor side NO.1
Governor side NO.1
Difference between angles 1
Cal 1-3 deg. 90 89.5 90.5
Cal 1-3 deg. 90 89.5 90.5
Difference between angles 2
Cal 1-4 deg. 180 179.5 180.5
Cal 1-4 deg. 180 179.5 180.5
Difference between angles 3
Cyl.1-2 deg. 270 269.5 270.5
Cyl.1-2 deg. 270 269.5 270.5
Injection quantity adjustment
Adjusting point
-
Rack position
12.1
Pump speed
r/min
960
960
960
Average injection quantity
mm3/st.
59
57.4
60.6
Max. variation between cylinders
%
0
-2.5
2.5
Basic
*
Fixing the rack
*
Standard for adjustment of the maximum variation between cylinders
*
Injection quantity adjustment_02
Adjusting point
H
Rack position
9.8+-0.5
Pump speed
r/min
285
285
285
Average injection quantity
mm3/st.
15.5
14.2
16.8
Max. variation between cylinders
%
0
-10
10
Fixing the rack
*
Standard for adjustment of the maximum variation between cylinders
*
Injection quantity adjustment_03
Adjusting point
A
Rack position
R1(12.1)
Pump speed
r/min
960
960
960
Average injection quantity
mm3/st.
59
58
60
Basic
*
Fixing the lever
*
Injection quantity adjustment_04
Adjusting point
B
Rack position
R1+0.4
Pump speed
r/min
1600
1600
1600
Average injection quantity
mm3/st.
79
75
83
Fixing the lever
*
Injection quantity adjustment_05
Adjusting point
I
Rack position
-
Pump speed
r/min
150
150
150
Average injection quantity
mm3/st.
80
80
112
Fixing the lever
*
Timer adjustment
Pump speed
r/min
1375--
Advance angle
deg.
0
0
0
Remarks
Start
Start
Timer adjustment_02
Pump speed
r/min
1325
Advance angle
deg.
0.3
Timer adjustment_03
Pump speed
r/min
1500
Advance angle
deg.
3.3
2.8
3.8
Timer adjustment_04
Pump speed
r/min
1600--
Advance angle
deg.
5
4.5
5.5
Remarks
Finish
Finish
Test data Ex:
Governor adjustment
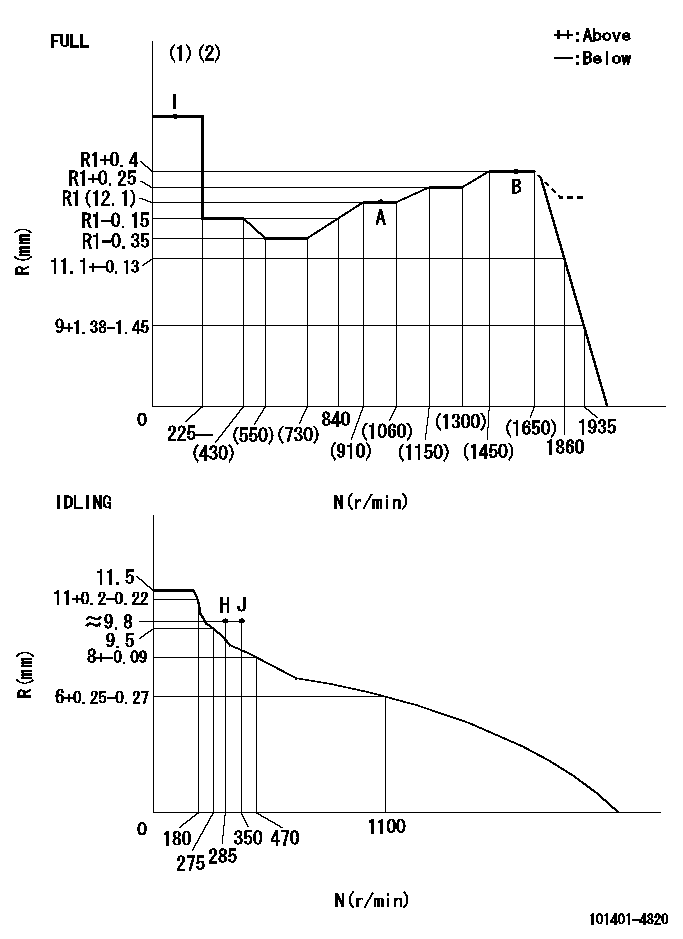
N:Pump speed
R:Rack position (mm)
(1)Torque cam stamping: T1
(2)Tolerance for racks not indicated: +-0.05mm.
----------
T1=J25
----------
----------
T1=J25
----------
Speed control lever angle

F:Full speed
I:Idle
(1)Stopper bolt set position 'H'
----------
----------
a=41deg+-5deg b=37deg+-3deg
----------
----------
a=41deg+-5deg b=37deg+-3deg
Stop lever angle

N:Pump normal
S:Stop the pump.
(1)Use the hole at R = aa
----------
aa=64mm
----------
a=20deg+-5deg b=29deg+-5deg
----------
aa=64mm
----------
a=20deg+-5deg b=29deg+-5deg
0000001501 FICD
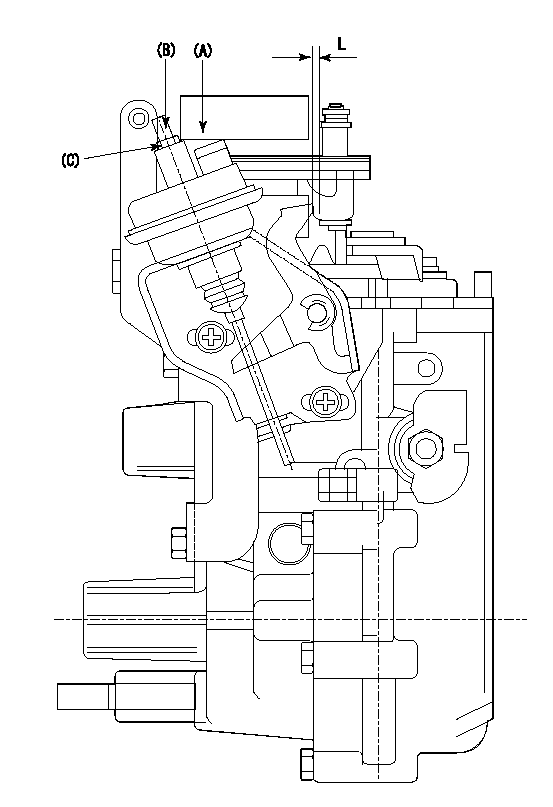
(A) applied negative pressure
(B) Screw
(c) Nut
1. Set the actuator as described below.
(1)Confirm that there is clearance between the actuator lever and the speed lever.
(2)Loosen the nut (C).
(3)Push in the screw (B).
(4)Apply P1 from the actuator (A) part.
(5)Pull out the screw (B) slowly.
(6)Tighten and fix the nut (C) when pump speed is Na and the rack position is Ra.
(7)Torque the nut (C) to T1.
(8)Apply P2 several times.
(9)Confirm that the actuator functions normally.
(10)Confirm that there is a clearance between the actuator lever and the speed lever at that time.
----------
P1=53.3kPa(400mmHg) P2=53.3kPa(400mmHg) Na=440r/min Ra=9.2+-0.1mm T1=1.2~1.6N-m(0.12~0.16kgf-m)
----------
L=(5)mm
----------
P1=53.3kPa(400mmHg) P2=53.3kPa(400mmHg) Na=440r/min Ra=9.2+-0.1mm T1=1.2~1.6N-m(0.12~0.16kgf-m)
----------
L=(5)mm
Timing setting
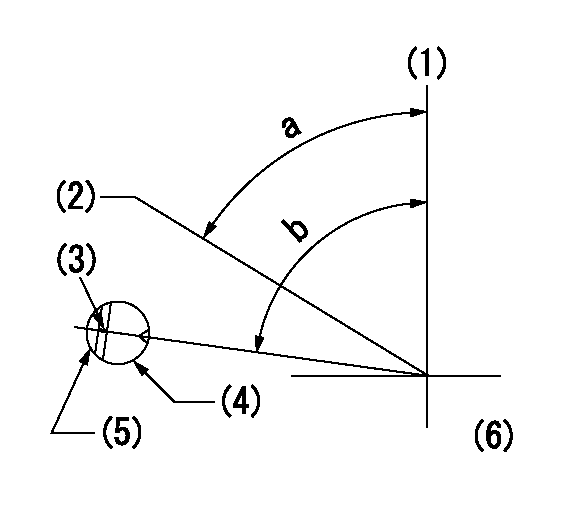
(1)Pump vertical direction
(2)Position of gear's standard threaded hole at No 1 cylinder's beginning of injection
(3)Stamping position on the A/T outer rim
(4)Pump bracket check hole position.
(5)At the No 1 cylinder's beginning of injection, align with the projection seen through the bracket's check hole and mark the A/T's bevel C1.
(6)B.T.D.C.: aa
----------
aa=10deg
----------
a=(60deg) b=(85deg)
----------
aa=10deg
----------
a=(60deg) b=(85deg)
Information:
3.1 Service Standards Table
3.2 Tightening torque table
4. Special Tool
5. Service Procedures
5.1 Removal and Installation
(1) Removal (a) When removing the pressure plate and lever assembly, fix the pressure plate using the special tools, Stopper Bolt and Washer. (C4 and C8 only) (b) Install the special tool, Clutch Alignment Arbor to prevent drop of the clutch disc and then remove the pressure plate and lever assembly.(2) Installation (a) Install the clutch disc using the special tool, Clutch Alignment Arbor. When installing the clutch disc, use care not to confuse the front and reverse sides. Install with the side bearing the part No. facing outside. (b) Install the pressure plate and lever assembly, aligning with the knock pins of the fly wheel. In the case of C4 and C8, install after fixing the pressure plate using special tools, Stopper Bolt and Washer. 1. Before installing the clutch, check and clean the flywheel. If faulty, correct or replace.2. When tightening the bolts, do so in diagonal order and uniformly.3. After installation, be sure to remove the Stopper Bolt and Washer. (C4 and C8 only)(c) Inspection of release lever plate height (at clutch disc replacement only) Using special tool, Clutch Release Lever Aligner, check the height of the clutch cover and release lever plate.If adjustment is necessary, adjust referring to 5.2.2 (3).(d) Adjustment after installation of bearing case. After installation, adjust the free travel (clearance between the release bearing and release lever). 1) Move the lever in the direction to engage the clutch. At a position where a click is heard in the clutch, turn the adjusting bolt A until it is blocked by the stopper, and lock it by turning down the bolt another two or three threads.2) From the position where the release bearing has touched the release lever, turn the adjusting screw B in the direction to disengage the clutch and check to see that the clutch is in disengaged position. Then lock the bolt. When making adjustment, lock in position the ratchet of the lever of the opposite side. 1) Loosen the control ling lock nut and from the position where the release bearing is in contact with the release lever, move back by B1 mm and lock in position (clutch lever setting position when clutch is engaged).2) In the direction to disengage the clutch, lock the air cylinder adjusting bolt at a position B2 mm from the position where the release bearing is in contact with the release lever.5.2 Clutch Proper
Disassembly and inspection
Disassembly and Inspection(1) Removal of clutch cover (a) Matchmark the clutch cover and pressure plate and using special tool, Clutch Installer, compress the pressure spring and remove support lever nut, strap bolt, etc.(b) Slowly loosen the handle of the Clutch Installer to remove the clutch cover.(2) Wear of facing Measure the depth from facing surface to rivet head. If the depth is smaller than the limit, replace the clutch disc assembly.(3) Runout of clutch disc Using a runout tester, measure the runout of the clutch
3.2 Tightening torque table
4. Special Tool
5. Service Procedures
5.1 Removal and Installation
(1) Removal (a) When removing the pressure plate and lever assembly, fix the pressure plate using the special tools, Stopper Bolt and Washer. (C4 and C8 only) (b) Install the special tool, Clutch Alignment Arbor to prevent drop of the clutch disc and then remove the pressure plate and lever assembly.(2) Installation (a) Install the clutch disc using the special tool, Clutch Alignment Arbor. When installing the clutch disc, use care not to confuse the front and reverse sides. Install with the side bearing the part No. facing outside. (b) Install the pressure plate and lever assembly, aligning with the knock pins of the fly wheel. In the case of C4 and C8, install after fixing the pressure plate using special tools, Stopper Bolt and Washer. 1. Before installing the clutch, check and clean the flywheel. If faulty, correct or replace.2. When tightening the bolts, do so in diagonal order and uniformly.3. After installation, be sure to remove the Stopper Bolt and Washer. (C4 and C8 only)(c) Inspection of release lever plate height (at clutch disc replacement only) Using special tool, Clutch Release Lever Aligner, check the height of the clutch cover and release lever plate.If adjustment is necessary, adjust referring to 5.2.2 (3).(d) Adjustment after installation of bearing case. After installation, adjust the free travel (clearance between the release bearing and release lever). 1) Move the lever in the direction to engage the clutch. At a position where a click is heard in the clutch, turn the adjusting bolt A until it is blocked by the stopper, and lock it by turning down the bolt another two or three threads.2) From the position where the release bearing has touched the release lever, turn the adjusting screw B in the direction to disengage the clutch and check to see that the clutch is in disengaged position. Then lock the bolt. When making adjustment, lock in position the ratchet of the lever of the opposite side. 1) Loosen the control ling lock nut and from the position where the release bearing is in contact with the release lever, move back by B1 mm and lock in position (clutch lever setting position when clutch is engaged).2) In the direction to disengage the clutch, lock the air cylinder adjusting bolt at a position B2 mm from the position where the release bearing is in contact with the release lever.5.2 Clutch Proper
Disassembly and inspection
Disassembly and Inspection(1) Removal of clutch cover (a) Matchmark the clutch cover and pressure plate and using special tool, Clutch Installer, compress the pressure spring and remove support lever nut, strap bolt, etc.(b) Slowly loosen the handle of the Clutch Installer to remove the clutch cover.(2) Wear of facing Measure the depth from facing surface to rivet head. If the depth is smaller than the limit, replace the clutch disc assembly.(3) Runout of clutch disc Using a runout tester, measure the runout of the clutch