Information injection-pump assembly
ZEXEL
101401-4610
1014014610
ISUZU
8970903580
8970903580
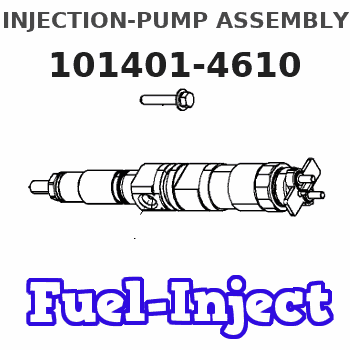
Rating:
Service parts 101401-4610 INJECTION-PUMP ASSEMBLY:
1.
_
6.
COUPLING PLATE
7.
COUPLING PLATE
8.
_
9.
_
11.
Nozzle and Holder
8-97114-016-0
12.
Open Pre:MPa(Kqf/cm2)
18.1{185}
15.
NOZZLE SET
Cross reference number
ZEXEL
101401-4610
1014014610
ISUZU
8970903580
8970903580
Zexel num
Bosch num
Firm num
Name
Calibration Data:
Adjustment conditions
Test oil
1404 Test oil ISO4113 or {SAEJ967d}
1404 Test oil ISO4113 or {SAEJ967d}
Test oil temperature
degC
40
40
45
Nozzle and nozzle holder
105780-8140
Bosch type code
EF8511/9A
Nozzle
105780-0000
Bosch type code
DN12SD12T
Nozzle holder
105780-2080
Bosch type code
EF8511/9
Opening pressure
MPa
17.2
Opening pressure
kgf/cm2
175
Injection pipe
Outer diameter - inner diameter - length (mm) mm 6-2-600
Outer diameter - inner diameter - length (mm) mm 6-2-600
Overflow valve
131424-4920
Overflow valve opening pressure
kPa
127
107
147
Overflow valve opening pressure
kgf/cm2
1.3
1.1
1.5
Tester oil delivery pressure
kPa
157
157
157
Tester oil delivery pressure
kgf/cm2
1.6
1.6
1.6
Direction of rotation (viewed from drive side)
Left L
Left L
Injection timing adjustment
Direction of rotation (viewed from drive side)
Left L
Left L
Injection order
1-3-4-2
Pre-stroke
mm
4.1
4.05
4.15
Rack position
Point A R=A
Point A R=A
Beginning of injection position
Governor side NO.1
Governor side NO.1
Difference between angles 1
Cal 1-3 deg. 90 89.5 90.5
Cal 1-3 deg. 90 89.5 90.5
Difference between angles 2
Cal 1-4 deg. 180 179.5 180.5
Cal 1-4 deg. 180 179.5 180.5
Difference between angles 3
Cyl.1-2 deg. 270 269.5 270.5
Cyl.1-2 deg. 270 269.5 270.5
Injection quantity adjustment
Adjusting point
-
Rack position
11.7
Pump speed
r/min
960
960
960
Average injection quantity
mm3/st.
74.7
73.1
76.3
Max. variation between cylinders
%
0
-2.5
2.5
Basic
*
Fixing the rack
*
Standard for adjustment of the maximum variation between cylinders
*
Injection quantity adjustment_02
Adjusting point
H
Rack position
9.8+-0.5
Pump speed
r/min
285
285
285
Average injection quantity
mm3/st.
15.5
14.2
16.8
Max. variation between cylinders
%
0
-14
14
Fixing the rack
*
Standard for adjustment of the maximum variation between cylinders
*
Injection quantity adjustment_03
Adjusting point
A
Rack position
R1(11.7)
Pump speed
r/min
960
960
960
Average injection quantity
mm3/st.
74.7
73.7
75.7
Basic
*
Fixing the lever
*
Injection quantity adjustment_04
Adjusting point
B
Rack position
R1+0.25
Pump speed
r/min
1600
1600
1600
Average injection quantity
mm3/st.
89.8
85.8
93.8
Fixing the lever
*
Injection quantity adjustment_05
Adjusting point
I
Rack position
-
Pump speed
r/min
150
150
150
Average injection quantity
mm3/st.
76
76
108
Fixing the lever
*
Timer adjustment
Pump speed
r/min
1375--
Advance angle
deg.
0
0
0
Remarks
Start
Start
Timer adjustment_02
Pump speed
r/min
1325
Advance angle
deg.
0.3
Timer adjustment_03
Pump speed
r/min
1500
Advance angle
deg.
3.3
2.8
3.8
Timer adjustment_04
Pump speed
r/min
1600--
Advance angle
deg.
5
4.5
5.5
Remarks
Finish
Finish
Test data Ex:
Governor adjustment
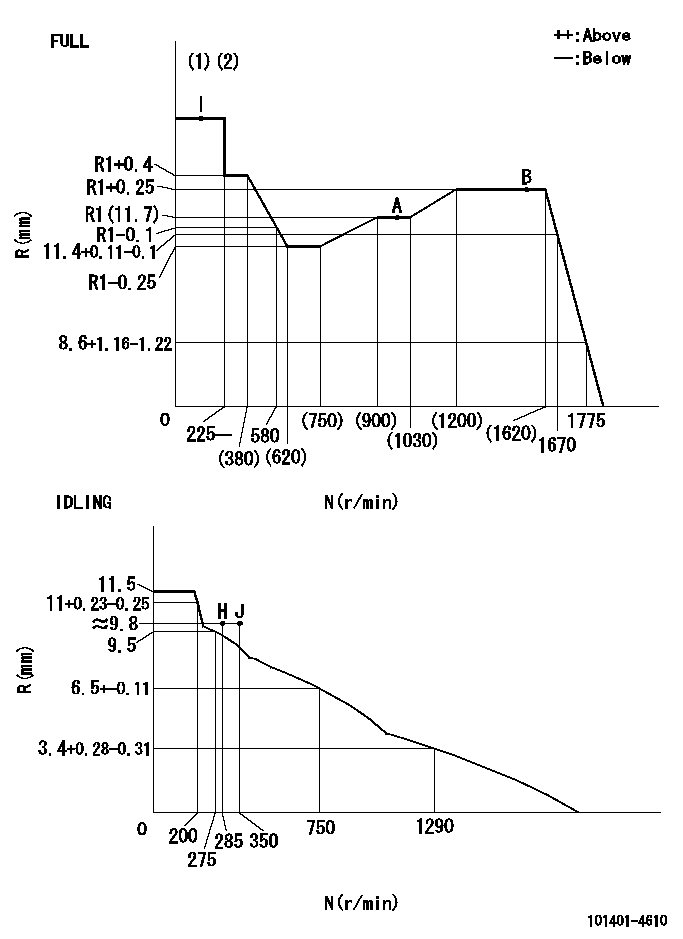
N:Pump speed
R:Rack position (mm)
(1)Torque cam stamping: T1
(2)Tolerance for racks not indicated: +-0.05mm.
----------
T1=H58
----------
----------
T1=H58
----------
Speed control lever angle

F:Full speed
I:Idle
(1)Stopper bolt set position 'H'
----------
----------
a=41deg+-5deg b=(38deg)+-3deg
----------
----------
a=41deg+-5deg b=(38deg)+-3deg
Stop lever angle

N:Pump normal
S:Stop the pump.
(1)Use the hole at R = aa
----------
aa=64mm
----------
a=20deg+-5deg b=29deg+-5deg
----------
aa=64mm
----------
a=20deg+-5deg b=29deg+-5deg
0000001501 MICRO SWITCH
Adjustment of the micro-switch
Adjust the bolt to obtain the following lever position when the micro-switch is ON.
(1)Speed N1
(2)Rack position Ra
----------
N1=1100r/min Ra=9.2+-0.1mm
----------
----------
N1=1100r/min Ra=9.2+-0.1mm
----------
0000001601 FICD
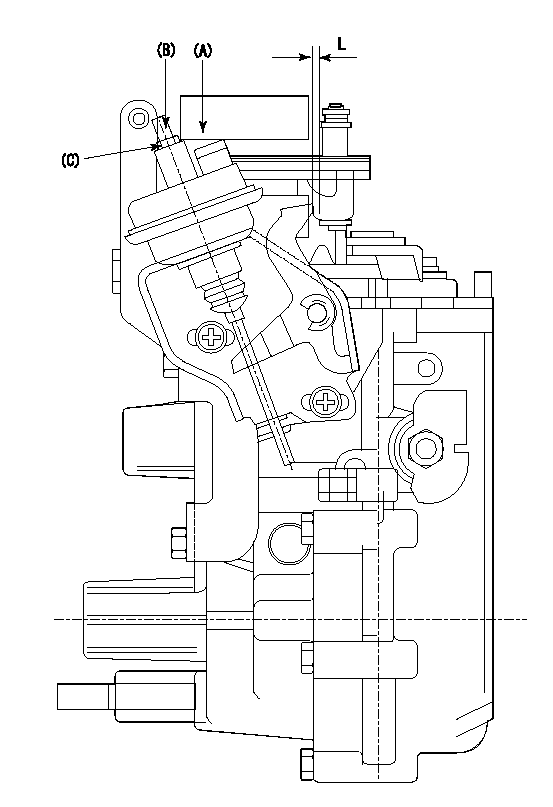
(A) applied negative pressure
(B) Screw
(c) Nut
1. Set the actuator as described below.
(1)Confirm that there is clearance between the actuator lever and the speed lever.
(2)Loosen the nut (C).
(3)Push in the screw (B).
(4)Apply P1 from the actuator (A) part.
(5)Pull out the screw (B) slowly.
(6)Tighten and fix the nut (C) when pump speed is Na and the rack position is Ra.
(7)Torque the nut (C) to T1.
(8)Apply P2 several times.
(9)Confirm that the actuator functions normally.
(10)Confirm that there is a clearance between the actuator lever and the speed lever at that time.
----------
P1=53.3kPa(400mmHg) P2=53.3kPa(400mmHg) Na=440r/min Ra=9.2+-0.1mm T1=1.2~1.6N-m(0.12~0.16kgf-m)
----------
L=(5)mm
----------
P1=53.3kPa(400mmHg) P2=53.3kPa(400mmHg) Na=440r/min Ra=9.2+-0.1mm T1=1.2~1.6N-m(0.12~0.16kgf-m)
----------
L=(5)mm
Timing setting
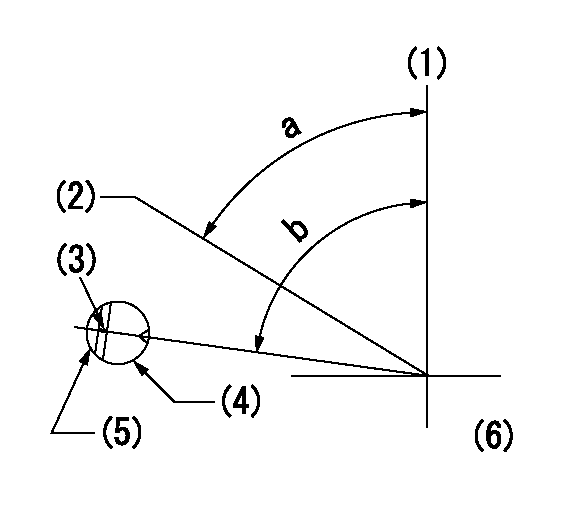
(1)Pump vertical direction
(2)Position of gear's standard threaded hole at No 1 cylinder's beginning of injection
(3)Stamping position on the A/T outer rim
(4)Pump bracket check hole position.
(5)At the No 1 cylinder's beginning of injection, align with the projection seen through the bracket's check hole and mark the A/T's bevel C1.
(6)B.T.D.C.: aa
----------
aa=10deg
----------
a=(60deg) b=(85deg)
----------
aa=10deg
----------
a=(60deg) b=(85deg)
Information:
Lubricant Viscosity Recommendations
See chart for recommended viscosity and temperature range. The required performance criteria for the oil is defined in the previous Lubricant Specification section.The minimum temperature for the viscosity grade provides guidelines for the lowest starting temperature with a "cold soaked" engine. Base stocks for blending the oil formulations do differ, and variations can exist within a viscosity grade on low temperature characteristics. Therefore, a particular oil may allow lower starting temperatures than given in the chart. Your oil supplier can provide additional information on oil properties.The recommendation is to use the highest viscosity oil possible. Even though the ambient temperature may be low, operating engines can still be subjected to normal oil temperatures because of regulated temperature components. Higher viscosity fluids provide better protection to all components contacted during the full day work cycle.Multi-viscosity oils are preferred because of full protection through a wider temperature range. See chart for recommended viscosity and temperature range.To determine if the oil in the crankcase will flow in cold weather, remove the oil dipstick before starting the engine. If the oil flows off, the oil is fluid enough to circulate properly.Lubricant Viscosity Chart
Refill Capacities
These refill capacities reflect the crankcase capacity plus filter. Auxiliary oil filter systems will require additional oil. For all auxiliary oil filter system information consult the OEM or auxiliary oil filter system manufacturer.In order to properly maintain the cooling system, Total Cooling System capacity must be known. This capacity information will be needed to determine the amount of antifreeze and coolant additive (conditioner) required for the cooling system.
See chart for recommended viscosity and temperature range. The required performance criteria for the oil is defined in the previous Lubricant Specification section.The minimum temperature for the viscosity grade provides guidelines for the lowest starting temperature with a "cold soaked" engine. Base stocks for blending the oil formulations do differ, and variations can exist within a viscosity grade on low temperature characteristics. Therefore, a particular oil may allow lower starting temperatures than given in the chart. Your oil supplier can provide additional information on oil properties.The recommendation is to use the highest viscosity oil possible. Even though the ambient temperature may be low, operating engines can still be subjected to normal oil temperatures because of regulated temperature components. Higher viscosity fluids provide better protection to all components contacted during the full day work cycle.Multi-viscosity oils are preferred because of full protection through a wider temperature range. See chart for recommended viscosity and temperature range.To determine if the oil in the crankcase will flow in cold weather, remove the oil dipstick before starting the engine. If the oil flows off, the oil is fluid enough to circulate properly.Lubricant Viscosity Chart
Refill Capacities
These refill capacities reflect the crankcase capacity plus filter. Auxiliary oil filter systems will require additional oil. For all auxiliary oil filter system information consult the OEM or auxiliary oil filter system manufacturer.In order to properly maintain the cooling system, Total Cooling System capacity must be known. This capacity information will be needed to determine the amount of antifreeze and coolant additive (conditioner) required for the cooling system.