Information injection-pump assembly
BOSCH
9 400 613 713
9400613713
ZEXEL
101401-4581
1014014581
ISUZU
8971140070
8971140070
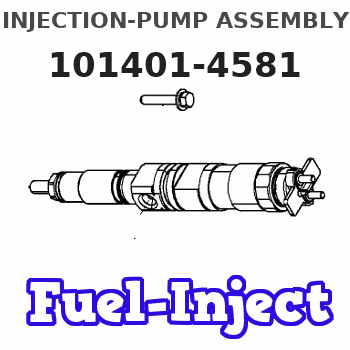
Rating:
Service parts 101401-4581 INJECTION-PUMP ASSEMBLY:
1.
_
6.
COUPLING PLATE
7.
COUPLING PLATE
8.
_
9.
_
11.
Nozzle and Holder
8-97114-017-0
12.
Open Pre:MPa(Kqf/cm2)
18.1{185}
15.
NOZZLE SET
Cross reference number
BOSCH
9 400 613 713
9400613713
ZEXEL
101401-4581
1014014581
ISUZU
8971140070
8971140070
Zexel num
Bosch num
Firm num
Name
101401-4581
9 400 613 713
8971140070 ISUZU
INJECTION-PUMP ASSEMBLY
4HF1 * K 14BC INJECTION PUMP ASSY PE4A,5A, PE
4HF1 * K 14BC INJECTION PUMP ASSY PE4A,5A, PE
Calibration Data:
Adjustment conditions
Test oil
1404 Test oil ISO4113 or {SAEJ967d}
1404 Test oil ISO4113 or {SAEJ967d}
Test oil temperature
degC
40
40
45
Nozzle and nozzle holder
105780-8140
Bosch type code
EF8511/9A
Nozzle
105780-0000
Bosch type code
DN12SD12T
Nozzle holder
105780-2080
Bosch type code
EF8511/9
Opening pressure
MPa
17.2
Opening pressure
kgf/cm2
175
Injection pipe
Outer diameter - inner diameter - length (mm) mm 6-2-600
Outer diameter - inner diameter - length (mm) mm 6-2-600
Overflow valve
131424-4920
Overflow valve opening pressure
kPa
127
107
147
Overflow valve opening pressure
kgf/cm2
1.3
1.1
1.5
Tester oil delivery pressure
kPa
157
157
157
Tester oil delivery pressure
kgf/cm2
1.6
1.6
1.6
Direction of rotation (viewed from drive side)
Left L
Left L
Injection timing adjustment
Direction of rotation (viewed from drive side)
Left L
Left L
Injection order
1-3-4-2
Pre-stroke
mm
4.1
4.05
4.15
Rack position
Point A R=A
Point A R=A
Beginning of injection position
Governor side NO.1
Governor side NO.1
Difference between angles 1
Cal 1-3 deg. 90 89.5 90.5
Cal 1-3 deg. 90 89.5 90.5
Difference between angles 2
Cal 1-4 deg. 180 179.5 180.5
Cal 1-4 deg. 180 179.5 180.5
Difference between angles 3
Cyl.1-2 deg. 270 269.5 270.5
Cyl.1-2 deg. 270 269.5 270.5
Injection quantity adjustment
Adjusting point
-
Rack position
12.6
Pump speed
r/min
1100
1100
1100
Average injection quantity
mm3/st.
75.4
73.8
77
Max. variation between cylinders
%
0
-4
4
Basic
*
Fixing the rack
*
Standard for adjustment of the maximum variation between cylinders
*
Injection quantity adjustment_02
Adjusting point
H
Rack position
10.3+-0.
5
Pump speed
r/min
285
285
285
Average injection quantity
mm3/st.
23.5
22.2
24.8
Max. variation between cylinders
%
0
-10
10
Fixing the rack
*
Standard for adjustment of the maximum variation between cylinders
*
Injection quantity adjustment_03
Adjusting point
A
Rack position
R1(12.6)
Pump speed
r/min
1100
1100
1100
Average injection quantity
mm3/st.
75.4
74.4
76.4
Basic
*
Fixing the lever
*
Injection quantity adjustment_04
Adjusting point
B
Rack position
R1+0.2
Pump speed
r/min
1600
1600
1600
Average injection quantity
mm3/st.
86.3
82.3
90.3
Fixing the lever
*
Injection quantity adjustment_05
Adjusting point
I
Rack position
-
Pump speed
r/min
150
150
150
Average injection quantity
mm3/st.
80
80
112
Fixing the lever
*
Timer adjustment
Pump speed
r/min
1375--
Advance angle
deg.
0
0
0
Remarks
Start
Start
Timer adjustment_02
Pump speed
r/min
1325
Advance angle
deg.
0.3
Timer adjustment_03
Pump speed
r/min
1500
Advance angle
deg.
3.3
2.8
3.8
Timer adjustment_04
Pump speed
r/min
1600--
Advance angle
deg.
5
4.5
5.5
Remarks
Finish
Finish
Test data Ex:
Governor adjustment
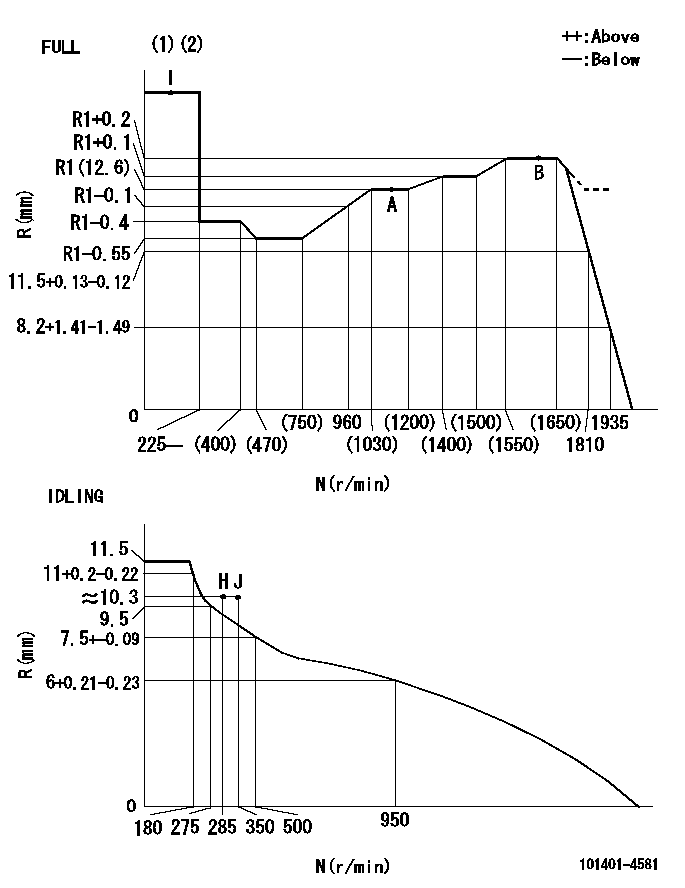
N:Pump speed
R:Rack position (mm)
(1)Torque cam stamping: T1
(2)Tolerances for racks not indicated: +-0.05mm.
----------
T1=H97
----------
----------
T1=H97
----------
Speed control lever angle

F:Full speed
I:Idle
(1)Stopper bolt set position 'H'
----------
----------
a=40deg+-5deg b=(34deg)+-3deg
----------
----------
a=40deg+-5deg b=(34deg)+-3deg
Stop lever angle

N:Pump normal
S:Stop the pump.
(1)Use the hole at R = aa
----------
aa=64mm
----------
a=20deg+-5deg b=29deg+-5deg
----------
aa=64mm
----------
a=20deg+-5deg b=29deg+-5deg
0000001501 FICD
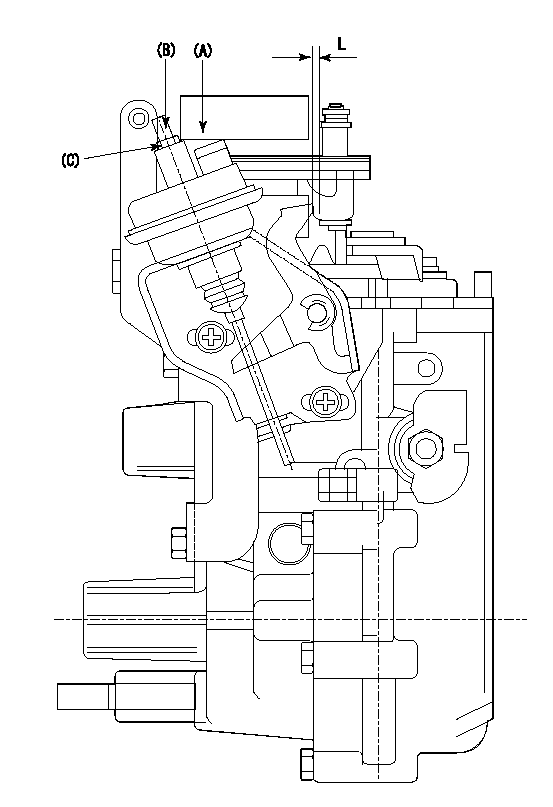
(A) applied negative pressure
(B) Screw
(c) Nut
1. Set the actuator as described below.
(1)Confirm that there is clearance between the actuator lever and the speed lever.
(2)Loosen the nut (C).
(3)Push in the screw (B).
(4)Apply P1 from the actuator (A) part.
(5)Pull out the screw (B) slowly.
(6)Tighten and fix the nut (C) when pump speed is Na and the rack position is Ra.
(7)Torque the nut (C) to T1.
(8)Apply P2 several times.
(9)Confirm that the actuator functions normally.
(10)Confirm that there is a clearance between the actuator lever and the speed lever at that time.
----------
P1=53.3kPa(400mmHg) P2=53.3kPa(400mmHg) Na=440r/min Ra=9.2+-0.1mm T1=1.2~1.6N-m(0.12~0.16kgf-m)
----------
L=(5)mm
----------
P1=53.3kPa(400mmHg) P2=53.3kPa(400mmHg) Na=440r/min Ra=9.2+-0.1mm T1=1.2~1.6N-m(0.12~0.16kgf-m)
----------
L=(5)mm
Timing setting
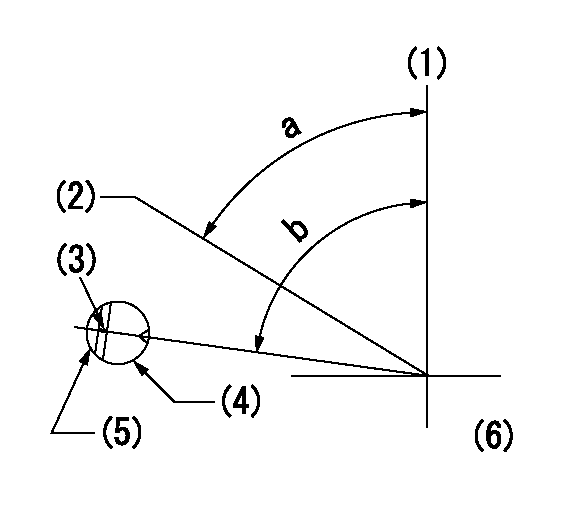
(1)Pump vertical direction
(2)Position of gear's standard threaded hole at No 1 cylinder's beginning of injection
(3)Stamping position on the A/T outer rim
(4)Pump bracket check hole position.
(5)At the No 1 cylinder's beginning of injection, align with the projection seen through the bracket's check hole and mark the A/T's bevel C1.
(6)B.T.D.C.: aa
----------
aa=10deg
----------
a=(60deg) b=(85deg)
----------
aa=10deg
----------
a=(60deg) b=(85deg)
Information:
Calibration
Refer to the complete Oil and Filter change procedure before performing Calibration (if applicable).Your engine may use a dipstick that has a FULL RANGE zone rather than the traditional FULL mark. The FULL RANGE is between the ADD and FULL marks (X-Y). This dipstick allows for variations in engine installations. Engine oil level will vary, depending on angle (front to back tilt) and slant sideways tilt).To determine the correct FULL mark in the FULL RANGE zone and prevent overfilling or under filling the crankcase, it is important to calibrate (or verify the calibration of) the dipstick at the first oil change.To verify the ADD mark and establish the actual FULL mark in the FULL RANGE zone of the dipstick, use the following procedure. This procedure is correct for use with either the non-spacer plate oil pan or the spacer plate oil pan. Sump capacities and oil levels are the same for each oil pan. The engine must rest on a level surface for this procedure.
Hot oil and hot components can cause personal injury. Do not allow hot oil or hot components to contact the skin.
1. Operate the engine until it reaches normal operating temperature.2. Stop the engine. Remove the crankcase drain plug(s). Let the oil drain from the crankcase for 20 minutes.3. Remove the used oil filter(s). Install the new oil filter(s). Install the crankcase drain plug(s) and tighten to 70 14 N m (50 10 lb ft).4. Add 18 L (19 qt) of oil for 3306B engines or 16 L (17 qt) of oil for 3304B engines. Allow the oil to drain back to the sump for a minimum of five minutes.5. Ensure that the oil level gauge is seated. Check the oil level on the oil level gauge. The oil level should be at the ADD mark. If the oil level is not at the existing ADD mark, use an engraving tool to grind off the mark and engrave the new ADD level.6. Add 6 L (6 qt) of oil for 3306B engines or 2.5 L (2.5 qt) of oil for 3304B engines into the sump. Allow enough time for the oil to drain into the sump.7. Ensure that the oil level gauge is seated. Check the oil level on the oil level gauge. The oil level should be at the FULL mark. If the oil level is not at the existing FULL mark, use an engraving tool to grind off the mark and engrave the new FULL level.
Remote mounted or auxiliary oil filters require additional oil. For all information about auxiliary oil filters, refer to the OEM instructions.
8. Add an additional 4 L (4 qt) of oil into the sump for both the 3306B and the 3304B engines. Total fill capacity for the 3306B engine is 27.5 L (29 qt) Total fill capacity for the 3304B engine is 22.5 L (23.5 qt).
To prevent crankshaft or bearing damage, crank the engine with the fuel OFF in order to fill all of the oil
Refer to the complete Oil and Filter change procedure before performing Calibration (if applicable).Your engine may use a dipstick that has a FULL RANGE zone rather than the traditional FULL mark. The FULL RANGE is between the ADD and FULL marks (X-Y). This dipstick allows for variations in engine installations. Engine oil level will vary, depending on angle (front to back tilt) and slant sideways tilt).To determine the correct FULL mark in the FULL RANGE zone and prevent overfilling or under filling the crankcase, it is important to calibrate (or verify the calibration of) the dipstick at the first oil change.To verify the ADD mark and establish the actual FULL mark in the FULL RANGE zone of the dipstick, use the following procedure. This procedure is correct for use with either the non-spacer plate oil pan or the spacer plate oil pan. Sump capacities and oil levels are the same for each oil pan. The engine must rest on a level surface for this procedure.
Hot oil and hot components can cause personal injury. Do not allow hot oil or hot components to contact the skin.
1. Operate the engine until it reaches normal operating temperature.2. Stop the engine. Remove the crankcase drain plug(s). Let the oil drain from the crankcase for 20 minutes.3. Remove the used oil filter(s). Install the new oil filter(s). Install the crankcase drain plug(s) and tighten to 70 14 N m (50 10 lb ft).4. Add 18 L (19 qt) of oil for 3306B engines or 16 L (17 qt) of oil for 3304B engines. Allow the oil to drain back to the sump for a minimum of five minutes.5. Ensure that the oil level gauge is seated. Check the oil level on the oil level gauge. The oil level should be at the ADD mark. If the oil level is not at the existing ADD mark, use an engraving tool to grind off the mark and engrave the new ADD level.6. Add 6 L (6 qt) of oil for 3306B engines or 2.5 L (2.5 qt) of oil for 3304B engines into the sump. Allow enough time for the oil to drain into the sump.7. Ensure that the oil level gauge is seated. Check the oil level on the oil level gauge. The oil level should be at the FULL mark. If the oil level is not at the existing FULL mark, use an engraving tool to grind off the mark and engrave the new FULL level.
Remote mounted or auxiliary oil filters require additional oil. For all information about auxiliary oil filters, refer to the OEM instructions.
8. Add an additional 4 L (4 qt) of oil into the sump for both the 3306B and the 3304B engines. Total fill capacity for the 3306B engine is 27.5 L (29 qt) Total fill capacity for the 3304B engine is 22.5 L (23.5 qt).
To prevent crankshaft or bearing damage, crank the engine with the fuel OFF in order to fill all of the oil
Have questions with 101401-4581?
Group cross 101401-4581 ZEXEL
Isuzu
101401-4581
9 400 613 713
8971140070
INJECTION-PUMP ASSEMBLY
4HF1
4HF1