Information injection-pump assembly
BOSCH
9 400 613 679
9400613679
ZEXEL
101401-4140
1014014140
ISUZU
8970331541
8970331541
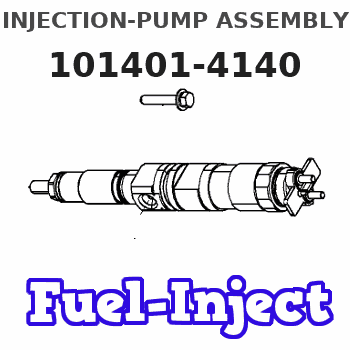
Rating:
Service parts 101401-4140 INJECTION-PUMP ASSEMBLY:
1.
_
6.
COUPLING PLATE
7.
COUPLING PLATE
8.
_
9.
_
11.
Nozzle and Holder
5-15300-089-1
12.
Open Pre:MPa(Kqf/cm2)
18.1{185}
15.
NOZZLE SET
Cross reference number
BOSCH
9 400 613 679
9400613679
ZEXEL
101401-4140
1014014140
ISUZU
8970331541
8970331541
Zexel num
Bosch num
Firm num
Name
101401-4140
9 400 613 679
8970331541 ISUZU
INJECTION-PUMP ASSEMBLY
4BD1 * K
4BD1 * K
Calibration Data:
Adjustment conditions
Test oil
1404 Test oil ISO4113 or {SAEJ967d}
1404 Test oil ISO4113 or {SAEJ967d}
Test oil temperature
degC
40
40
45
Nozzle and nozzle holder
105780-8140
Bosch type code
EF8511/9A
Nozzle
105780-0000
Bosch type code
DN12SD12T
Nozzle holder
105780-2080
Bosch type code
EF8511/9
Opening pressure
MPa
17.2
Opening pressure
kgf/cm2
175
Injection pipe
Outer diameter - inner diameter - length (mm) mm 6-2-600
Outer diameter - inner diameter - length (mm) mm 6-2-600
Overflow valve opening pressure
kPa
157
123
191
Overflow valve opening pressure
kgf/cm2
1.6
1.25
1.95
Tester oil delivery pressure
kPa
157
157
157
Tester oil delivery pressure
kgf/cm2
1.6
1.6
1.6
Direction of rotation (viewed from drive side)
Right R
Right R
Injection timing adjustment
Direction of rotation (viewed from drive side)
Right R
Right R
Injection order
1-3-4-2
Pre-stroke
mm
3.6
3.55
3.65
Beginning of injection position
Drive side NO.1
Drive side NO.1
Difference between angles 1
Cal 1-3 deg. 90 89.5 90.5
Cal 1-3 deg. 90 89.5 90.5
Difference between angles 2
Cal 1-4 deg. 180 179.5 180.5
Cal 1-4 deg. 180 179.5 180.5
Difference between angles 3
Cyl.1-2 deg. 270 269.5 270.5
Cyl.1-2 deg. 270 269.5 270.5
Injection quantity adjustment
Adjusting point
-
Rack position
11.2
Pump speed
r/min
950
950
950
Average injection quantity
mm3/st.
66.7
65.1
68.3
Max. variation between cylinders
%
0
-4
4
Basic
*
Fixing the rack
*
Standard for adjustment of the maximum variation between cylinders
*
Injection quantity adjustment_02
Adjusting point
H
Rack position
9.5+-0.5
Pump speed
r/min
290
290
290
Average injection quantity
mm3/st.
8
6.7
9.3
Max. variation between cylinders
%
0
-14
14
Fixing the rack
*
Standard for adjustment of the maximum variation between cylinders
*
Injection quantity adjustment_03
Adjusting point
A
Rack position
R1(11.2)
Pump speed
r/min
950
950
950
Average injection quantity
mm3/st.
66.7
65.7
67.7
Basic
*
Fixing the lever
*
Injection quantity adjustment_04
Adjusting point
B
Rack position
R1-0.4
Pump speed
r/min
1600
1600
1600
Average injection quantity
mm3/st.
63.3
60.1
66.5
Fixing the lever
*
Injection quantity adjustment_05
Adjusting point
C
Rack position
R1-0.1
Pump speed
r/min
1300
1300
1300
Average injection quantity
mm3/st.
70.7
67.5
73.9
Fixing the lever
*
Injection quantity adjustment_06
Adjusting point
D
Rack position
R1-0.25
Pump speed
r/min
650
650
650
Average injection quantity
mm3/st.
49.6
46.4
52.8
Fixing the lever
*
Injection quantity adjustment_07
Adjusting point
E
Rack position
R1+0.1
Pump speed
r/min
500
500
500
Average injection quantity
mm3/st.
49
45
53
Fixing the lever
*
Injection quantity adjustment_08
Adjusting point
I
Rack position
-
Pump speed
r/min
150
150
150
Average injection quantity
mm3/st.
95
95
103
Fixing the lever
*
Rack limit
*
Timer adjustment
Pump speed
r/min
1250
Advance angle
deg.
0.5
Timer adjustment_02
Pump speed
r/min
1350
Advance angle
deg.
1.1
Timer adjustment_03
Pump speed
r/min
1400
Advance angle
deg.
1.6
Timer adjustment_04
Pump speed
r/min
1600
Advance angle
deg.
5
4
5
Remarks
Finish
Finish
Test data Ex:
Governor adjustment
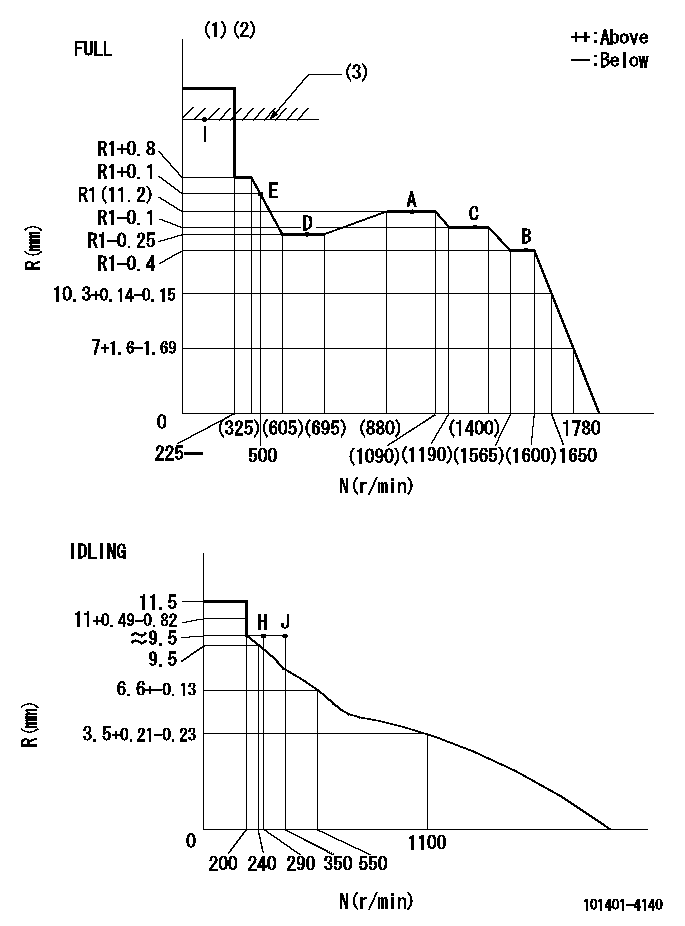
N:Pump speed
R:Rack position (mm)
(1)Torque cam stamping: T1
(2)Tolerance for racks not indicated: +-0.05mm.
(3)RACK LIMIT
----------
T1=47
----------
----------
T1=47
----------
Speed control lever angle

F:Full speed
I:Idle
(1)Stopper bolt set position 'H'
----------
----------
a=30deg+-5deg b=41deg+-3deg
----------
----------
a=30deg+-5deg b=41deg+-3deg
0000001501 ACS
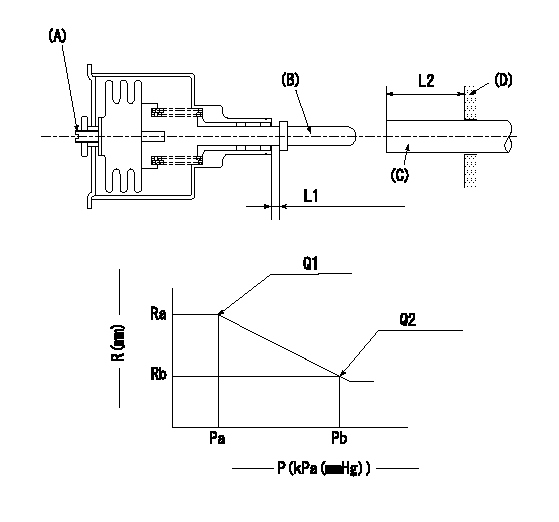
(A) Set screw
(B) Push rod 1
(C) Push rod 2
(D) Cover
1. Aneroid compensator unit adjustment
(1)Select the push rod 2 to obtain L2.
(2)Screw in (A) to obtain L1.
2. Adjustment when mounting the governor.
(1)Set the speed of the pump to N1 r/min and fix the control lever at the full set position.
(2)Screw in the aneroid compensator to obtain the performance shown in the graph above.
(3)As there is hysterisis, measure when the absolute pressure drops.
(4)Hysterisis must not exceed rack position = h1.
----------
N1=950r/min L1=(1.5)mm L2=11+-0.5mm h1=0.15mm
----------
Ra=R1(11.2)mm Rb=- Pa=89.8+-2.7kPa(674+-20mmHg) Pb=79.4+-0.7kPa(596+-5mmHg) Q1=66.7+-1cm3/1000st Q2=(59)+-1.6cm3/1000st
----------
N1=950r/min L1=(1.5)mm L2=11+-0.5mm h1=0.15mm
----------
Ra=R1(11.2)mm Rb=- Pa=89.8+-2.7kPa(674+-20mmHg) Pb=79.4+-0.7kPa(596+-5mmHg) Q1=66.7+-1cm3/1000st Q2=(59)+-1.6cm3/1000st
Timing setting

(1)Pump vertical direction
(2)Position of gear mark 'CC' at No 1 cylinder's beginning of injection
(3)B.T.D.C.: aa
(4)-
----------
aa=13deg
----------
a=(100deg)
----------
aa=13deg
----------
a=(100deg)
Information:
Fuel Filter Group
(1) Remove clips (1) and (2). Remove tube assembly (3) and elbow (4) from the fuel transfer pump on the replacement engine. Installation of new line is shown in Fuel Lines Group, Page 8.Fuel Tank Group
(1) Remove the fuel tank from the machine; see the Service Manual. (2) Fabricate boss (1) to the dimensions shown. Make 1/8" - 27 NPTF threads in one end. (3) Drill a 20.0 mm Ø (0.78" Ø) hole (A) through the bottom of the tank as shown. (4) Put boss (1) in hole (A) with the threaded end extending below the bottom of the full tank as shown. Make a 3.0 mm (0.12") fillet weld all around the boss.(5) Clean and install the fuel tank; see the Service Manual.Fuel Lines Group
(1) Remove fuel inlet hose (1) and tube assembly (2) from tube (A). (2) Install 307946 Elbow (3) and a 3J7354 Seal in the fuel transfer pump. Install 2V4869 Fitting (4) on elbow (3). Cut a 360.0 mm (14.17") length of 5P1465 Hose (5), and connect it to fitting (4) and tube assembly (A) with the former clamps.(3) Install 6D238 Valve Assembly (7) in the boss installed in the fuel tank (see Step 4, Page 7). Fasten 5G5681 Tube (8) to valve assembly (7). Use L2072 Clamp (9) to hold the other end of tube (8) in position. Install clamp (9) under bolt (10).(4) Install 307941 Elbow (11) and a 3J7354 Seal in the fuel return port of the fuel injection pump housing. Install 2V4869 Fitting (12) on elbow (11).(5) Cut a 520.0 mm (20.47") length of 5P1465 Hose (13), and connect it to fitting (12) and tube (8) with a 1P4278 Clamp (14). An optional step to the above procedure is to connect a 60.0 mm (2.36") length of 5P189 Tube to valve assembly (7). Cut a 2000.0 mm (78.75") length of 5P6442 Hose and connect it to 2V4869 Fitting (12) and to the 5P189 Tube with a 1P4278 Clamp. Tie the hose to the machine to prevent damage to the hose.Electrical System
(1) For all machines, connect the alternator wire of the harness to the alternator.(2) For machines 80U1-80U6734, remove the original voltage regulator. Put tape over the wire connection to the wiring harness so it will be out of the way. The alternator for this engine has a built in voltage regulator so the original voltage regulator is not needed for the electrical system.Flywheel Group (For Replacement of 7N9437, 1W163 or 2W7488 Engine Arrangements)
(1) Remove the flywheel from the new replacement engine.(2) Install a new 7W2290 Flywheel Assembly, and fasten it to the crankshaft with four T489 Bolts. See the Service Manual for the procedure and the bolt torque. If necessary, use of the former flywheel from the engine being replaced is acceptable.Installation Of Ether Starting Aid Group
The ether starting aid is no longer a required component of direct injection engine arrangements.(1) If the machine is equipped with an ether starting aid group, its reuse is optional. To reuse,
(1) Remove clips (1) and (2). Remove tube assembly (3) and elbow (4) from the fuel transfer pump on the replacement engine. Installation of new line is shown in Fuel Lines Group, Page 8.Fuel Tank Group
(1) Remove the fuel tank from the machine; see the Service Manual. (2) Fabricate boss (1) to the dimensions shown. Make 1/8" - 27 NPTF threads in one end. (3) Drill a 20.0 mm Ø (0.78" Ø) hole (A) through the bottom of the tank as shown. (4) Put boss (1) in hole (A) with the threaded end extending below the bottom of the full tank as shown. Make a 3.0 mm (0.12") fillet weld all around the boss.(5) Clean and install the fuel tank; see the Service Manual.Fuel Lines Group
(1) Remove fuel inlet hose (1) and tube assembly (2) from tube (A). (2) Install 307946 Elbow (3) and a 3J7354 Seal in the fuel transfer pump. Install 2V4869 Fitting (4) on elbow (3). Cut a 360.0 mm (14.17") length of 5P1465 Hose (5), and connect it to fitting (4) and tube assembly (A) with the former clamps.(3) Install 6D238 Valve Assembly (7) in the boss installed in the fuel tank (see Step 4, Page 7). Fasten 5G5681 Tube (8) to valve assembly (7). Use L2072 Clamp (9) to hold the other end of tube (8) in position. Install clamp (9) under bolt (10).(4) Install 307941 Elbow (11) and a 3J7354 Seal in the fuel return port of the fuel injection pump housing. Install 2V4869 Fitting (12) on elbow (11).(5) Cut a 520.0 mm (20.47") length of 5P1465 Hose (13), and connect it to fitting (12) and tube (8) with a 1P4278 Clamp (14). An optional step to the above procedure is to connect a 60.0 mm (2.36") length of 5P189 Tube to valve assembly (7). Cut a 2000.0 mm (78.75") length of 5P6442 Hose and connect it to 2V4869 Fitting (12) and to the 5P189 Tube with a 1P4278 Clamp. Tie the hose to the machine to prevent damage to the hose.Electrical System
(1) For all machines, connect the alternator wire of the harness to the alternator.(2) For machines 80U1-80U6734, remove the original voltage regulator. Put tape over the wire connection to the wiring harness so it will be out of the way. The alternator for this engine has a built in voltage regulator so the original voltage regulator is not needed for the electrical system.Flywheel Group (For Replacement of 7N9437, 1W163 or 2W7488 Engine Arrangements)
(1) Remove the flywheel from the new replacement engine.(2) Install a new 7W2290 Flywheel Assembly, and fasten it to the crankshaft with four T489 Bolts. See the Service Manual for the procedure and the bolt torque. If necessary, use of the former flywheel from the engine being replaced is acceptable.Installation Of Ether Starting Aid Group
The ether starting aid is no longer a required component of direct injection engine arrangements.(1) If the machine is equipped with an ether starting aid group, its reuse is optional. To reuse,
Have questions with 101401-4140?
Group cross 101401-4140 ZEXEL
Isuzu
101401-4140
9 400 613 679
8970331541
INJECTION-PUMP ASSEMBLY
4BD1
4BD1