Information injection-pump assembly
BOSCH
9 400 613 677
9400613677
ZEXEL
101401-4122
1014014122
ISUZU
8970279965
8970279965
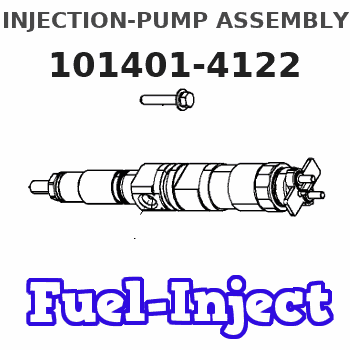
Rating:
Service parts 101401-4122 INJECTION-PUMP ASSEMBLY:
1.
_
6.
COUPLING PLATE
7.
COUPLING PLATE
8.
_
9.
_
11.
Nozzle and Holder
8-97114-015-0
12.
Open Pre:MPa(Kqf/cm2)
18.1{185}
15.
NOZZLE SET
Cross reference number
BOSCH
9 400 613 677
9400613677
ZEXEL
101401-4122
1014014122
ISUZU
8970279965
8970279965
Zexel num
Bosch num
Firm num
Name
9 400 613 677
8970279965 ISUZU
INJECTION-PUMP ASSEMBLY
4HF1 * K 14BC INJECTION PUMP ASSY PE4A,5A, PE
4HF1 * K 14BC INJECTION PUMP ASSY PE4A,5A, PE
Calibration Data:
Adjustment conditions
Test oil
1404 Test oil ISO4113 or {SAEJ967d}
1404 Test oil ISO4113 or {SAEJ967d}
Test oil temperature
degC
40
40
45
Nozzle and nozzle holder
105780-8140
Bosch type code
EF8511/9A
Nozzle
105780-0000
Bosch type code
DN12SD12T
Nozzle holder
105780-2080
Bosch type code
EF8511/9
Opening pressure
MPa
17.2
Opening pressure
kgf/cm2
175
Injection pipe
Outer diameter - inner diameter - length (mm) mm 6-2-600
Outer diameter - inner diameter - length (mm) mm 6-2-600
Overflow valve
134424-3920
Overflow valve opening pressure
kPa
127
107
147
Overflow valve opening pressure
kgf/cm2
1.3
1.1
1.5
Tester oil delivery pressure
kPa
157
157
157
Tester oil delivery pressure
kgf/cm2
1.6
1.6
1.6
Direction of rotation (viewed from drive side)
Left L
Left L
Injection timing adjustment
Direction of rotation (viewed from drive side)
Left L
Left L
Injection order
1-3-4-2
Pre-stroke
mm
3.9
3.85
3.95
Rack position
Point A R=A
Point A R=A
Beginning of injection position
Governor side NO.1
Governor side NO.1
Difference between angles 1
Cal 1-3 deg. 90 89.5 90.5
Cal 1-3 deg. 90 89.5 90.5
Difference between angles 2
Cal 1-4 deg. 180 179.5 180.5
Cal 1-4 deg. 180 179.5 180.5
Difference between angles 3
Cyl.1-2 deg. 270 269.5 270.5
Cyl.1-2 deg. 270 269.5 270.5
Injection quantity adjustment
Adjusting point
-
Rack position
12.6
Pump speed
r/min
960
960
960
Average injection quantity
mm3/st.
69.8
68.2
71.4
Max. variation between cylinders
%
0
-4
4
Basic
*
Fixing the rack
*
Standard for adjustment of the maximum variation between cylinders
*
Injection quantity adjustment_02
Adjusting point
H
Rack position
9.5+-0.5
Pump speed
r/min
325
325
325
Average injection quantity
mm3/st.
8.8
7.5
10.1
Max. variation between cylinders
%
0
-10
10
Fixing the rack
*
Standard for adjustment of the maximum variation between cylinders
*
Injection quantity adjustment_03
Adjusting point
A
Rack position
R1(12.6)
Pump speed
r/min
960
960
960
Average injection quantity
mm3/st.
69.8
68.8
70.8
Basic
*
Fixing the lever
*
Injection quantity adjustment_04
Adjusting point
B
Rack position
R1+0.5
Pump speed
r/min
1600
1600
1600
Average injection quantity
mm3/st.
87.3
83.3
91.3
Fixing the lever
*
Injection quantity adjustment_05
Adjusting point
I
Rack position
-
Pump speed
r/min
150
150
150
Average injection quantity
mm3/st.
78
78
110
Fixing the lever
*
Timer adjustment
Pump speed
r/min
1375--
Advance angle
deg.
0
0
0
Remarks
Start
Start
Timer adjustment_02
Pump speed
r/min
1325
Advance angle
deg.
0.3
Timer adjustment_03
Pump speed
r/min
1500
Advance angle
deg.
3.3
2.8
3.8
Timer adjustment_04
Pump speed
r/min
1600--
Advance angle
deg.
5
4.5
5.5
Remarks
Finish
Finish
Test data Ex:
Governor adjustment
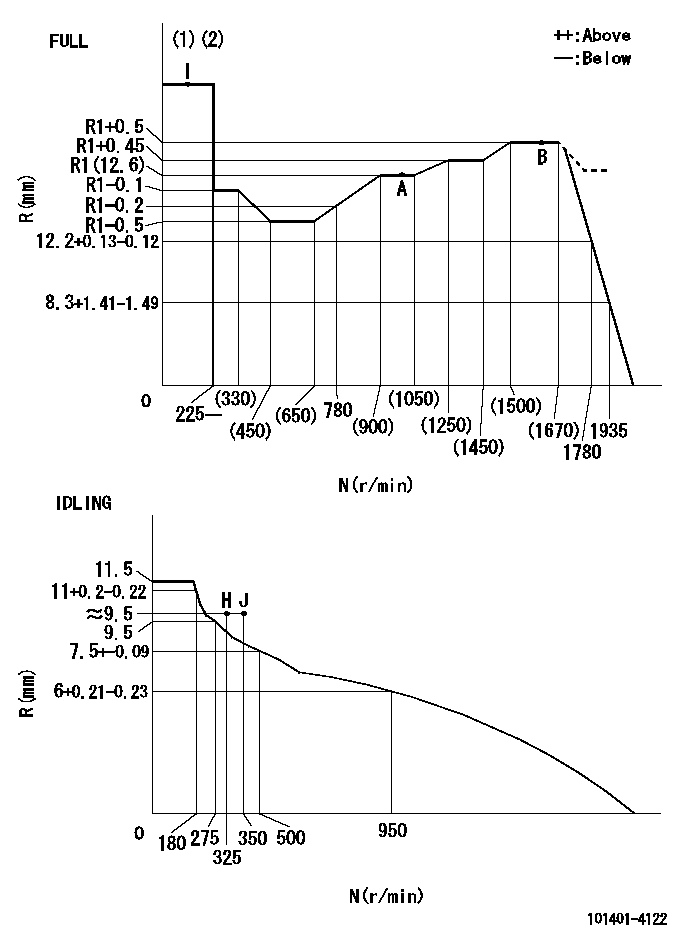
N:Pump speed
R:Rack position (mm)
(1)Torque cam stamping: T1
(2)Tolerance for racks not indicated: +-0.05mm.
----------
T1=F85
----------
----------
T1=F85
----------
Speed control lever angle

F:Full speed
I:Idle
(1)Stopper bolt set position 'H'
----------
----------
a=41deg+-5deg b=(37deg)+-3deg
----------
----------
a=41deg+-5deg b=(37deg)+-3deg
Stop lever angle

N:Pump normal
S:Stop the pump.
(1)Use the hole at R = aa
----------
aa=64mm
----------
a=20deg+-5deg b=29deg+-5deg
----------
aa=64mm
----------
a=20deg+-5deg b=29deg+-5deg
0000001501 FICD
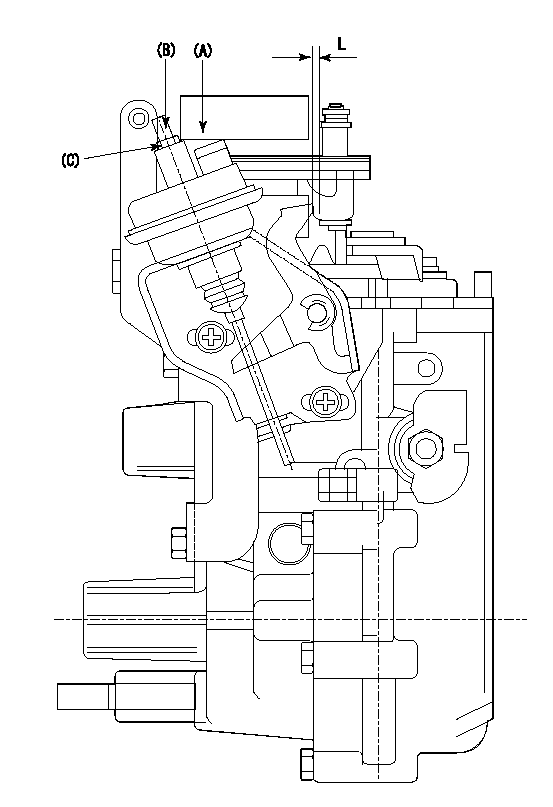
(A) applied negative pressure
(B) Screw
(c) Nut
1. Set the actuator as described below.
(1)Confirm that there is clearance between the actuator lever and the speed lever.
(2)Loosen the nut (C).
(3)Push in the screw (B).
(4)Apply P1 from the actuator (A) part.
(5)Pull out the screw (B) slowly.
(6)Tighten and fix the nut (C) when pump speed is Na and the rack position is Ra.
(7)Torque the nut (C) to T1.
(8)Apply P2 several times.
(9)Confirm that the actuator functions normally.
(10)Confirm that there is a clearance between the actuator lever and the speed lever at that time.
----------
P1=53.3kPa(400mmHg) P2=53.3kPa(400mmHg) Na=450r/min Ra=9.55+-0.1mm T1=1.2~1.6N-m(0.12~0.16kgf-m)
----------
L=(2)mm
----------
P1=53.3kPa(400mmHg) P2=53.3kPa(400mmHg) Na=450r/min Ra=9.55+-0.1mm T1=1.2~1.6N-m(0.12~0.16kgf-m)
----------
L=(2)mm
Timing setting
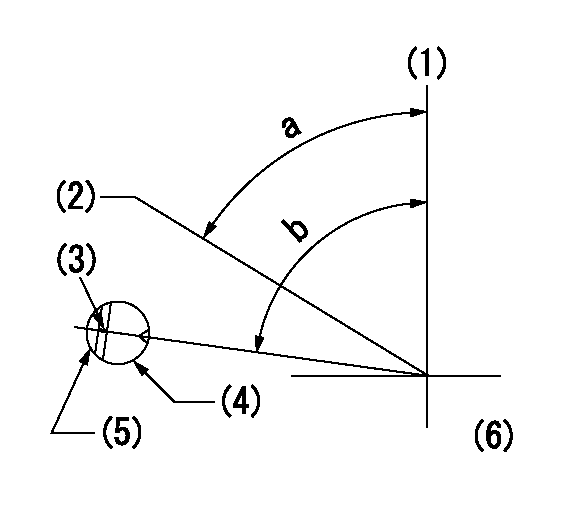
(1)Pump vertical direction
(2)Position of gear's standard threaded hole at No 1 cylinder's beginning of injection
(3)Stamping position on the A/T outer rim
(4)Pump bracket check hole position.
(5)At the No 1 cylinder's beginning of injection, align with the projection seen through the bracket's check hole and mark the A/T's bevel C1.
(6)B.T.D.C.: aa
----------
aa=11deg
----------
a=(60deg) b=(85deg)
----------
aa=11deg
----------
a=(60deg) b=(85deg)
Information:
Test Points (Voltages And Waveforms)
dc Voltages Conditions: 1. dc input voltage applied to POWER connector as shown.2. CALIBRATION CHECK/OPERATE switch in the OPERATE position.3. Neither transducer connected to indicator.4. TPI is reference for all voltages.Equipment Required: 6V3030 Digital Multimeterdc Input Voltages Waveforms Conditions: 1. dc power input voltage of 25 1 Volts.2. CALIBRATION CHECK/OPERATE switch in the CHECK position (can be held in CHECK position with tape).3. Neither transducer connected to indicator.4. TPI is reference for all waveforms.Equipment Required: dc oscilloscope (dual channel preferred). Waveform Time Relationships
VOLTAGES MAY VARY 10%, PULSE DURATIONS BY 20% EXCEPT 2.66 ms WHICH IS BASED ON A 12.000 kHz OSCILLATOR FREQ. (1C202). SIGNAL SOURCE IS INTERNAL CALIBRATOR. ALL TEST POINTS REFERENCED TO TP1.Waveform Time Relationships (enlarged scale)
VOLTAGES MAY VARY 10%, PULSE DURATIONS BY 20% EXCEPT 83.3 ?s AND 2.66 ms WHICH ARE EXACT BASED ON A 12.000 kHZ OSCILLATOR. (1C202) SIGNAL SOURCE IS INTERNAL CALIBRATOR. ALL TEST POINTS REFERENCED TO TP1.Disassembly Procedure
1 Remove six screws (1) from front panel (2), and remove panel (2) from case (3). Remove four screws (4) from the PC board, and also remove the locknuts from the two front panel switches (5) and (6). Carefully lift front panel (2) from PC (printed circuit) board (7).Calibration Procedure
To make sure the 6V3100 Timing Indicator Group (1) has good accuracy, check its calibration at a minimum of every six months. Also, the timing indicator will need calibration if: A. It does not show 2000 30 R/MIN at (A) and 32.0 .2 DEG at (B), when the CALIBRATION CHECK-OPERATE Switch (C) is in the CALIBRATION CHECK position. With no input signal at (D) or (E), the reading at R/MIN location (A) must show three zeros (000). If four zeros (0000) show, it is an indication of a possible need for calibration of the unit. This error only is not reason enough to do a complete calibration procedure. It is also not necessary to do a complete calibration procedure if the reading at the DEG location (B) has a decimal point as shown, (00.0) in addition to the three zeros.B. Reading is different than (000) at either location (A) or (B).All calibrations can be done with the use of a small screwdriver, a frequency counter and
dc Voltages Conditions: 1. dc input voltage applied to POWER connector as shown.2. CALIBRATION CHECK/OPERATE switch in the OPERATE position.3. Neither transducer connected to indicator.4. TPI is reference for all voltages.Equipment Required: 6V3030 Digital Multimeterdc Input Voltages Waveforms Conditions: 1. dc power input voltage of 25 1 Volts.2. CALIBRATION CHECK/OPERATE switch in the CHECK position (can be held in CHECK position with tape).3. Neither transducer connected to indicator.4. TPI is reference for all waveforms.Equipment Required: dc oscilloscope (dual channel preferred). Waveform Time Relationships
VOLTAGES MAY VARY 10%, PULSE DURATIONS BY 20% EXCEPT 2.66 ms WHICH IS BASED ON A 12.000 kHz OSCILLATOR FREQ. (1C202). SIGNAL SOURCE IS INTERNAL CALIBRATOR. ALL TEST POINTS REFERENCED TO TP1.Waveform Time Relationships (enlarged scale)
VOLTAGES MAY VARY 10%, PULSE DURATIONS BY 20% EXCEPT 83.3 ?s AND 2.66 ms WHICH ARE EXACT BASED ON A 12.000 kHZ OSCILLATOR. (1C202) SIGNAL SOURCE IS INTERNAL CALIBRATOR. ALL TEST POINTS REFERENCED TO TP1.Disassembly Procedure
1 Remove six screws (1) from front panel (2), and remove panel (2) from case (3). Remove four screws (4) from the PC board, and also remove the locknuts from the two front panel switches (5) and (6). Carefully lift front panel (2) from PC (printed circuit) board (7).Calibration Procedure
To make sure the 6V3100 Timing Indicator Group (1) has good accuracy, check its calibration at a minimum of every six months. Also, the timing indicator will need calibration if: A. It does not show 2000 30 R/MIN at (A) and 32.0 .2 DEG at (B), when the CALIBRATION CHECK-OPERATE Switch (C) is in the CALIBRATION CHECK position. With no input signal at (D) or (E), the reading at R/MIN location (A) must show three zeros (000). If four zeros (0000) show, it is an indication of a possible need for calibration of the unit. This error only is not reason enough to do a complete calibration procedure. It is also not necessary to do a complete calibration procedure if the reading at the DEG location (B) has a decimal point as shown, (00.0) in addition to the three zeros.B. Reading is different than (000) at either location (A) or (B).All calibrations can be done with the use of a small screwdriver, a frequency counter and