Information injection-pump assembly
ZEXEL
101401-4100
1014014100
ISUZU
8970279942
8970279942
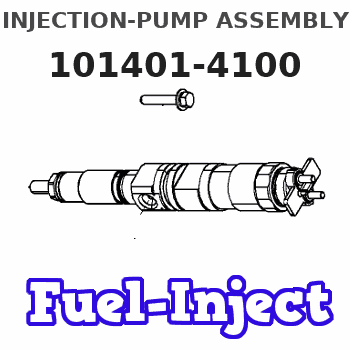
Rating:
Service parts 101401-4100 INJECTION-PUMP ASSEMBLY:
1.
_
6.
COUPLING PLATE
7.
COUPLING PLATE
8.
_
9.
_
11.
Nozzle and Holder
8-97114-015-0
12.
Open Pre:MPa(Kqf/cm2)
18.1{185}
15.
NOZZLE SET
Cross reference number
ZEXEL
101401-4100
1014014100
ISUZU
8970279942
8970279942
Zexel num
Bosch num
Firm num
Name
Calibration Data:
Adjustment conditions
Test oil
1404 Test oil ISO4113 or {SAEJ967d}
1404 Test oil ISO4113 or {SAEJ967d}
Test oil temperature
degC
40
40
45
Nozzle and nozzle holder
105780-8140
Bosch type code
EF8511/9A
Nozzle
105780-0000
Bosch type code
DN12SD12T
Nozzle holder
105780-2080
Bosch type code
EF8511/9
Opening pressure
MPa
17.2
Opening pressure
kgf/cm2
175
Injection pipe
Outer diameter - inner diameter - length (mm) mm 6-2-600
Outer diameter - inner diameter - length (mm) mm 6-2-600
Overflow valve
131424-4920
Overflow valve opening pressure
kPa
127
107
147
Overflow valve opening pressure
kgf/cm2
1.3
1.1
1.5
Tester oil delivery pressure
kPa
157
157
157
Tester oil delivery pressure
kgf/cm2
1.6
1.6
1.6
Direction of rotation (viewed from drive side)
Left L
Left L
Injection timing adjustment
Direction of rotation (viewed from drive side)
Left L
Left L
Injection order
1-3-4-2
Pre-stroke
mm
3.9
3.85
3.95
Rack position
Point A R=A
Point A R=A
Beginning of injection position
Governor side NO.1
Governor side NO.1
Difference between angles 1
Cal 1-3 deg. 90 89.5 90.5
Cal 1-3 deg. 90 89.5 90.5
Difference between angles 2
Cal 1-4 deg. 180 179.5 180.5
Cal 1-4 deg. 180 179.5 180.5
Difference between angles 3
Cyl.1-2 deg. 270 269.5 270.5
Cyl.1-2 deg. 270 269.5 270.5
Injection quantity adjustment
Adjusting point
-
Rack position
12.5
Pump speed
r/min
960
960
960
Average injection quantity
mm3/st.
69.8
68.2
71.4
Max. variation between cylinders
%
0
-2.5
2.5
Basic
*
Fixing the rack
*
Standard for adjustment of the maximum variation between cylinders
*
Injection quantity adjustment_02
Adjusting point
H
Rack position
9.5+-0.5
Pump speed
r/min
285
285
285
Average injection quantity
mm3/st.
8.4
7.1
9.7
Max. variation between cylinders
%
0
-10
10
Fixing the rack
*
Standard for adjustment of the maximum variation between cylinders
*
Injection quantity adjustment_03
Adjusting point
A
Rack position
R1(12.5)
Pump speed
r/min
960
960
960
Average injection quantity
mm3/st.
69.8
68.8
70.8
Basic
*
Fixing the lever
*
Injection quantity adjustment_04
Adjusting point
B
Rack position
R1+0.5
Pump speed
r/min
1600
1600
1600
Average injection quantity
mm3/st.
87.3
83.3
91.3
Fixing the lever
*
Injection quantity adjustment_05
Adjusting point
I
Rack position
-
Pump speed
r/min
150
150
150
Average injection quantity
mm3/st.
78
78
110
Fixing the lever
*
Timer adjustment
Pump speed
r/min
1375--
Advance angle
deg.
0
0
0
Remarks
Start
Start
Timer adjustment_02
Pump speed
r/min
1325
Advance angle
deg.
0.3
Timer adjustment_03
Pump speed
r/min
1500
Advance angle
deg.
3.3
2.8
3.8
Timer adjustment_04
Pump speed
r/min
1600--
Advance angle
deg.
5
4.5
5.5
Remarks
Finish
Finish
Test data Ex:
Governor adjustment
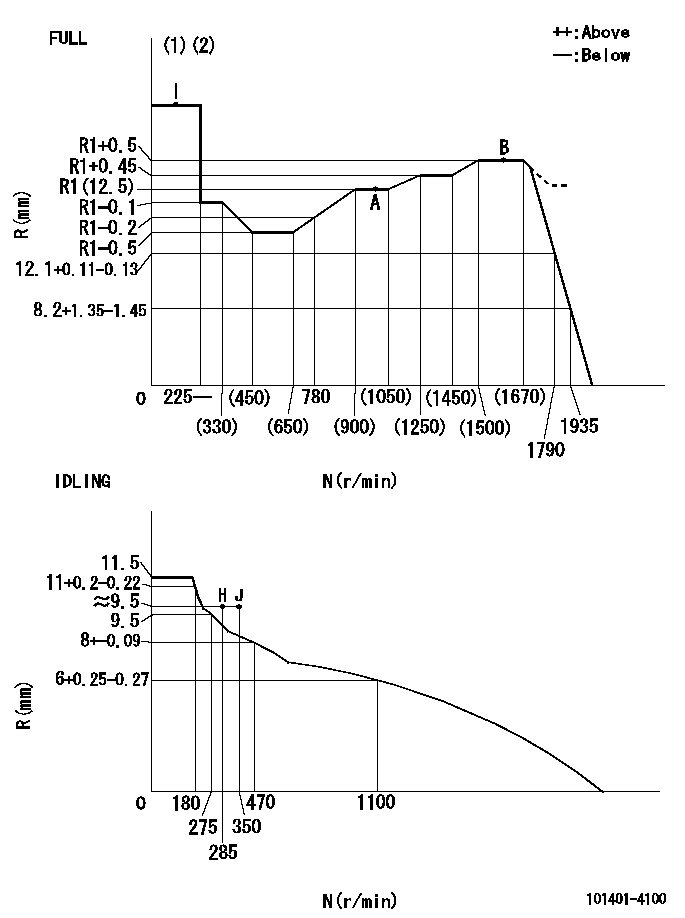
N:Pump speed
R:Rack position (mm)
(1)Torque cam stamping: T1
(2)Tolerance for racks not indicated: +-0.05mm.
----------
T1=F56
----------
----------
T1=F56
----------
Speed control lever angle

F:Full speed
I:Idle
(1)Stopper bolt set position 'H'
----------
----------
a=43deg+-5deg b=(37deg)+-3deg
----------
----------
a=43deg+-5deg b=(37deg)+-3deg
Stop lever angle

N:Pump normal
S:Stop the pump.
(1)Use the hole at R = aa
----------
aa=64mm
----------
a=20deg+-5deg b=29deg+-5deg
----------
aa=64mm
----------
a=20deg+-5deg b=29deg+-5deg
0000001501 FICD
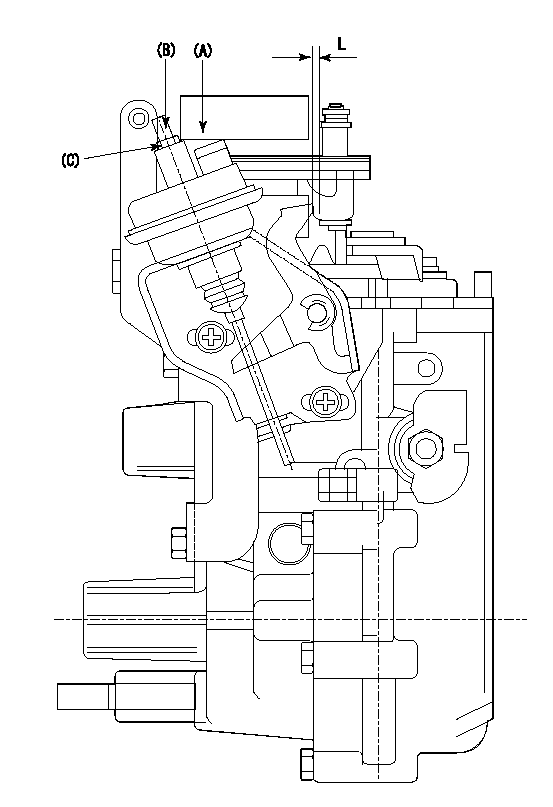
(A) applied negative pressure
(B) Screw
(c) Nut
1. Set the actuator as described below.
(1)Confirm that there is clearance between the actuator lever and the speed lever.
(2)Loosen the nut (C).
(3)Push in the screw (B).
(4)Apply P1 from the actuator (A) part.
(5)Pull out the screw (B) slowly.
(6)Tighten and fix the nut (C) when pump speed is Na and the rack position is Ra.
(7)Torque the nut (C) to T1.
(8)Apply P2 several times.
(9)Confirm that the actuator functions normally.
(10)Confirm that there is a clearance between the actuator lever and the speed lever at that time.
----------
P1=53.3kPa(400mmHg) P2=53.3kPa(400mmHg) Na=400r/min Ra=9.55+-0.1mm T1=1.2~1.6N-m(0.12~0.16kgf-m)
----------
L=(2)mm
----------
P1=53.3kPa(400mmHg) P2=53.3kPa(400mmHg) Na=400r/min Ra=9.55+-0.1mm T1=1.2~1.6N-m(0.12~0.16kgf-m)
----------
L=(2)mm
Timing setting
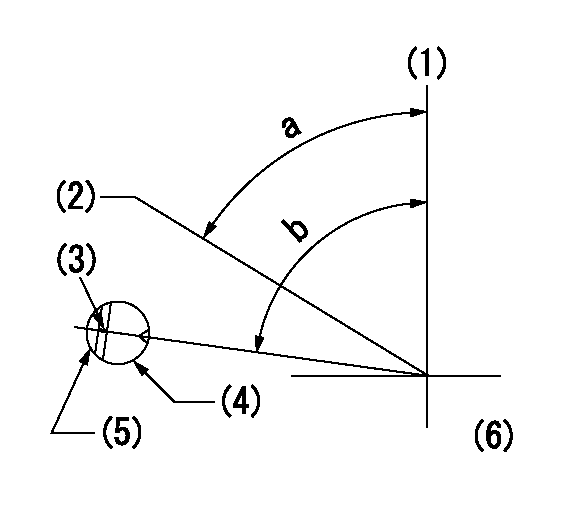
(1)Pump vertical direction
(2)Position of gear's standard threaded hole at No 1 cylinder's beginning of injection
(3)Stamping position on the A/T outer rim
(4)Pump bracket check hole position.
(5)At the No 1 cylinder's beginning of injection, align with the projection seen through the bracket's check hole and mark the A/T's bevel C1.
(6)B.T.D.C.: aa
----------
aa=11deg
----------
a=(60deg) b=(85deg)
----------
aa=11deg
----------
a=(60deg) b=(85deg)
Information:
D3, 910 and 931
(1) Use two S509 Bolts with 5P4116 Washers to fasten 5G657 Plate (1) to the inside of the radiator guard, in the holes drilled on either page 3 or 4.(2) Install 5P6315 Elbow (2) in 6N7673 Valve Assembly (3). Use 1C569 Bolts with 4B3849 Washers to fasten 6N7673 Valve Assembly (3) and 7N2059 Clamp (4) to plate (1). Use a 5P6314 Sleeve and 5P6313 Nut to connect 5G659 Tube (5) to elbow (2).(3) Remove the plug from the top of air inlet pipe (6) and install 6N7672 Atomizer (7) so the orifice is down (toward the manifold). Connect 7N140 Tube Assembly (8) and 5G660 Tube (9) to tube (5) and atomizer (7) as shown. Put a 3D5102 Grommet on tube (9) and use 8M2772 Clip (10) with an existing valve cover bolt for support of the tube. Tighten the bolt according to valve cover bolt specifications.(4) Remove plug (11) from the heater hose opening on the top left side of the engine timing gear housing (12). Install 6N5899 Switch (13) in the hole for plug (11). Connect 5G663 Wire (14) to switch (13) and one of the wires on valve assembly (3) as shown.(5) For D3 and 931 Machines, connect one end of 5G689 Wire Assembly (15) to the other wire from valve assembly (3). Use the clips that hold wiring harness (16) to fasten wire assembly (15) as shown, and pull the loose end of wire assembly (15) to the start switch. Do not connect wire assembly (15) to the start switch at this time. For 910 Machines, use 161.5" (41 dm) of 5P629 Wire, one 2L8076 Terminal and one 6K1828 Connector to make a wire assembly (15). (6) For all machines, install 3F1006 Switch (17) in the .656" Ø (16.7 Ø) hole that was drilled in the dash. For all earlier D3 and 931 Machines, and for 910 Machines, 80U1-80U3666, remove the 6S4355 Heat-Start Switch and install 6N8941 Start Switch (18). Put electrical tape on the end of the glow plug wire.(7) Connect 6S9586 Wire Assembly (19) to switch (17) and to the accessory (AC) connection on start switch (18). Connect wire (15), from 6N7673 Valve Assembly (3), to the other connection on switch (17) as shown.(8) Install the ether cylinder assembly and fasten it in position with the 7N2059 Clamp (4) that was installed in step 2.(9) Install a 6S9542 Instruction Film in the location that follows: D3, 931 - Install on the dash above switch (17); 910 - Install on the dash at the right side of switch (17).Installation Of 1W162 Engine Arrangement In 910 Machines As Replacement For: (4N303 Engine Arrangement - 80U1-80U6734), (7N3700 Engine Arrangement - 80U6735-up), (7N9433 Or 1W161 Engine Arrangement - 40Y), (7N9437 Or 1W163 Engine Arrangement - 41Y)
Before installation of the 1W162 Engine Arrangement as a replacement for any of the engine arrangements given above, some changes must be made to the new engine arrangement. See the information that follows. After engine installation is complete,
(1) Use two S509 Bolts with 5P4116 Washers to fasten 5G657 Plate (1) to the inside of the radiator guard, in the holes drilled on either page 3 or 4.(2) Install 5P6315 Elbow (2) in 6N7673 Valve Assembly (3). Use 1C569 Bolts with 4B3849 Washers to fasten 6N7673 Valve Assembly (3) and 7N2059 Clamp (4) to plate (1). Use a 5P6314 Sleeve and 5P6313 Nut to connect 5G659 Tube (5) to elbow (2).(3) Remove the plug from the top of air inlet pipe (6) and install 6N7672 Atomizer (7) so the orifice is down (toward the manifold). Connect 7N140 Tube Assembly (8) and 5G660 Tube (9) to tube (5) and atomizer (7) as shown. Put a 3D5102 Grommet on tube (9) and use 8M2772 Clip (10) with an existing valve cover bolt for support of the tube. Tighten the bolt according to valve cover bolt specifications.(4) Remove plug (11) from the heater hose opening on the top left side of the engine timing gear housing (12). Install 6N5899 Switch (13) in the hole for plug (11). Connect 5G663 Wire (14) to switch (13) and one of the wires on valve assembly (3) as shown.(5) For D3 and 931 Machines, connect one end of 5G689 Wire Assembly (15) to the other wire from valve assembly (3). Use the clips that hold wiring harness (16) to fasten wire assembly (15) as shown, and pull the loose end of wire assembly (15) to the start switch. Do not connect wire assembly (15) to the start switch at this time. For 910 Machines, use 161.5" (41 dm) of 5P629 Wire, one 2L8076 Terminal and one 6K1828 Connector to make a wire assembly (15). (6) For all machines, install 3F1006 Switch (17) in the .656" Ø (16.7 Ø) hole that was drilled in the dash. For all earlier D3 and 931 Machines, and for 910 Machines, 80U1-80U3666, remove the 6S4355 Heat-Start Switch and install 6N8941 Start Switch (18). Put electrical tape on the end of the glow plug wire.(7) Connect 6S9586 Wire Assembly (19) to switch (17) and to the accessory (AC) connection on start switch (18). Connect wire (15), from 6N7673 Valve Assembly (3), to the other connection on switch (17) as shown.(8) Install the ether cylinder assembly and fasten it in position with the 7N2059 Clamp (4) that was installed in step 2.(9) Install a 6S9542 Instruction Film in the location that follows: D3, 931 - Install on the dash above switch (17); 910 - Install on the dash at the right side of switch (17).Installation Of 1W162 Engine Arrangement In 910 Machines As Replacement For: (4N303 Engine Arrangement - 80U1-80U6734), (7N3700 Engine Arrangement - 80U6735-up), (7N9433 Or 1W161 Engine Arrangement - 40Y), (7N9437 Or 1W163 Engine Arrangement - 41Y)
Before installation of the 1W162 Engine Arrangement as a replacement for any of the engine arrangements given above, some changes must be made to the new engine arrangement. See the information that follows. After engine installation is complete,