Information injection-pump assembly
BOSCH
F 019 Z10 305
f019z10305
ZEXEL
101401-1632
1014011632
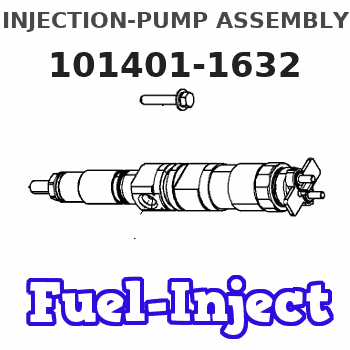
Rating:
Service parts 101401-1632 INJECTION-PUMP ASSEMBLY:
1.
_
6.
COUPLING PLATE
7.
COUPLING PLATE
8.
_
9.
_
11.
Nozzle and Holder
ME016989
12.
Open Pre:MPa(Kqf/cm2)
21.6{220}
15.
NOZZLE SET
Cross reference number
BOSCH
F 019 Z10 305
f019z10305
ZEXEL
101401-1632
1014011632
Zexel num
Bosch num
Firm num
Name
Calibration Data:
Adjustment conditions
Test oil
1404 Test oil ISO4113 or {SAEJ967d}
1404 Test oil ISO4113 or {SAEJ967d}
Test oil temperature
degC
40
40
45
Nozzle and nozzle holder
105780-8140
Bosch type code
EF8511/9A
Nozzle
105780-0000
Bosch type code
DN12SD12T
Nozzle holder
105780-2080
Bosch type code
EF8511/9
Opening pressure
MPa
17.2
Opening pressure
kgf/cm2
175
Injection pipe
Outer diameter - inner diameter - length (mm) mm 6-2-600
Outer diameter - inner diameter - length (mm) mm 6-2-600
Overflow valve
131424-8820
Overflow valve opening pressure
kPa
157
123
191
Overflow valve opening pressure
kgf/cm2
1.6
1.25
1.95
Tester oil delivery pressure
kPa
157
157
157
Tester oil delivery pressure
kgf/cm2
1.6
1.6
1.6
Direction of rotation (viewed from drive side)
Right R
Right R
Injection timing adjustment
Direction of rotation (viewed from drive side)
Right R
Right R
Injection order
1-3-4-2
Pre-stroke
mm
3.2
3.15
3.25
Beginning of injection position
Drive side NO.1
Drive side NO.1
Difference between angles 1
Cal 1-3 deg. 90 89.5 90.5
Cal 1-3 deg. 90 89.5 90.5
Difference between angles 2
Cal 1-4 deg. 180 179.5 180.5
Cal 1-4 deg. 180 179.5 180.5
Difference between angles 3
Cyl.1-2 deg. 270 269.5 270.5
Cyl.1-2 deg. 270 269.5 270.5
Injection quantity adjustment
Adjusting point
-
Rack position
11.9
Pump speed
r/min
900
900
900
Average injection quantity
mm3/st.
73.9
72.3
75.5
Max. variation between cylinders
%
0
-2.5
2.5
Basic
*
Fixing the rack
*
Standard for adjustment of the maximum variation between cylinders
*
Injection quantity adjustment_02
Adjusting point
H
Rack position
9.5+-0.5
Pump speed
r/min
325
325
325
Average injection quantity
mm3/st.
11.2
9.9
12.5
Max. variation between cylinders
%
0
-10
10
Fixing the rack
*
Standard for adjustment of the maximum variation between cylinders
*
Injection quantity adjustment_03
Adjusting point
A
Rack position
R1(11.9)
Pump speed
r/min
900
900
900
Average injection quantity
mm3/st.
73.9
72.9
74.9
Basic
*
Fixing the lever
*
Boost pressure
kPa
24.7
24.7
Boost pressure
mmHg
185
185
Injection quantity adjustment_04
Adjusting point
B
Rack position
R1+1.8
Pump speed
r/min
1600
1600
1600
Average injection quantity
mm3/st.
92.5
88.5
96.5
Fixing the lever
*
Boost pressure
kPa
24.7
24.7
Boost pressure
mmHg
185
185
Injection quantity adjustment_05
Adjusting point
C
Rack position
(R1-1)
Pump speed
r/min
500
500
500
Average injection quantity
mm3/st.
46.3
42.3
50.3
Fixing the lever
*
Boost pressure
kPa
24.7
24.7
Boost pressure
mmHg
185
185
Injection quantity adjustment_06
Adjusting point
D
Rack position
R2-0.65
Pump speed
r/min
300
300
300
Average injection quantity
mm3/st.
35.8
31.8
39.8
Fixing the lever
*
Boost pressure
kPa
0
0
0
Boost pressure
mmHg
0
0
0
Boost compensator adjustment
Pump speed
r/min
300
300
300
Rack position
R2-0.65
Boost pressure
kPa
4
2.7
5.3
Boost pressure
mmHg
30
20
40
Boost compensator adjustment_02
Pump speed
r/min
300
300
300
Rack position
R2(R1-0.
25)
Boost pressure
kPa
11.3
11.3
11.3
Boost pressure
mmHg
85
85
85
Timer adjustment
Pump speed
r/min
1250--
Advance angle
deg.
0
0
0
Remarks
Start
Start
Timer adjustment_02
Pump speed
r/min
1200
Advance angle
deg.
0.5
Timer adjustment_03
Pump speed
r/min
1600
Advance angle
deg.
4.5
4
5
Remarks
Finish
Finish
Test data Ex:
Governor adjustment
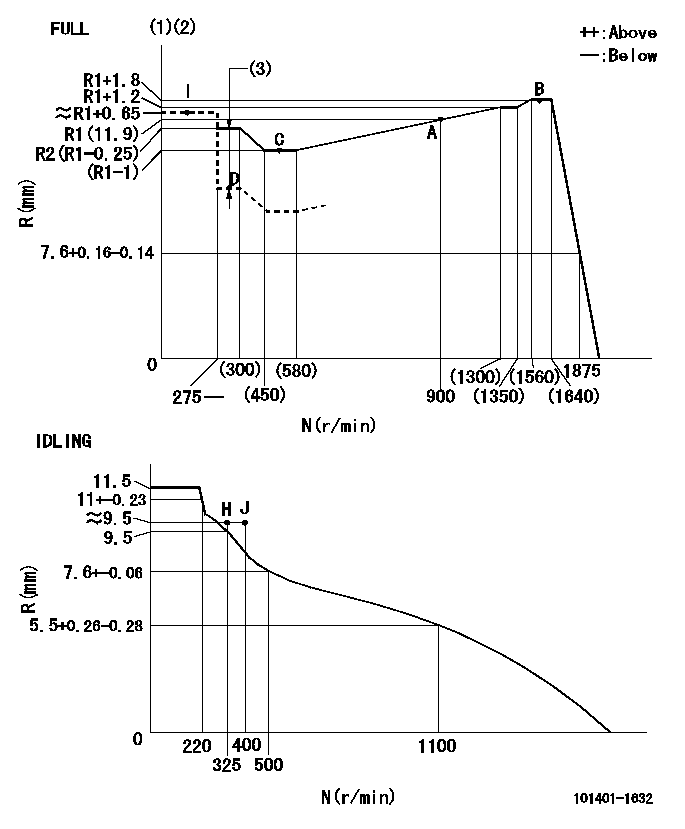
N:Pump speed
R:Rack position (mm)
(1)Torque cam stamping: T1
(2)Tolerance for racks not indicated: +-0.05mm.
(3)Boost compensator stroke: BCL
----------
T1=H90 BCL=0.65+-0.1mm
----------
----------
T1=H90 BCL=0.65+-0.1mm
----------
Speed control lever angle

F:Full speed
I:Idle
(1)Use the hole at R = aa
(2)Stopper bolt set position 'H'
----------
aa=40mm
----------
a=26deg+-5deg b=40deg+-3deg
----------
aa=40mm
----------
a=26deg+-5deg b=40deg+-3deg
Stop lever angle
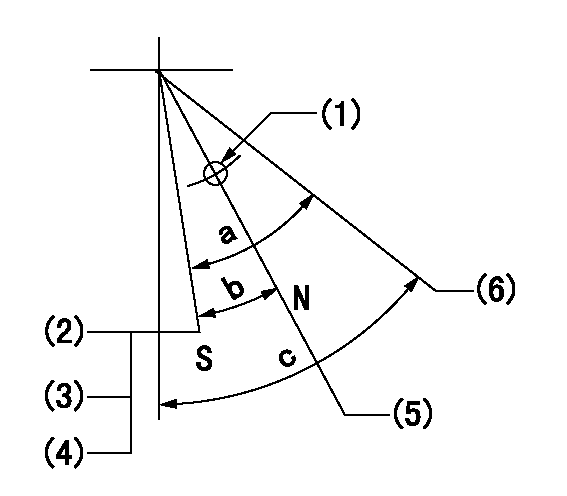
N:Engine manufacturer's normal use
S:Stop the pump.
(1)Use the hole at R = aa
(2)Set the stopper bolt at speed = bb and rack position = cc (non-injection rack position). Confirm non-injection.
(3)After setting the stopper bolt, confirm non-injection at speed dd. Rack position = ee or less (non-injection rack position).
(4)-
(5)Rack position corresponding to ff
(6)Free (at delivery)
----------
aa=40mm bb=1600r/min cc=5-0.5mm dd=325r/min ee=(8)mm ff=16mm
----------
a=29deg+-5deg b=19deg+-5deg c=33deg+-5deg
----------
aa=40mm bb=1600r/min cc=5-0.5mm dd=325r/min ee=(8)mm ff=16mm
----------
a=29deg+-5deg b=19deg+-5deg c=33deg+-5deg
0000001501 MICRO SWITCH
Adjustment of the micro-switch
Adjust the bolt to obtain the following lever position when the micro-switch is ON.
(1)Speed N1
(2)Rack position Ra
----------
N1=1025r/min Ra=8.5+-0.1mm
----------
----------
N1=1025r/min Ra=8.5+-0.1mm
----------
Timing setting

(1)Pump vertical direction
(2)Position of gear mark '3' at No 1 cylinder's beginning of injection
(3)B.T.D.C.: aa
(4)-
----------
aa=12deg
----------
a=(130deg)
----------
aa=12deg
----------
a=(130deg)
Information:
Image1.1.1
5. Attach a hose to the other end of the fuel rail and hold the free end of the hose in a cup/bucket of water. Hose shown is a JIC 37o ?6 hose. Refer to Illustration 1.2.1
Image1.2.1
6. Pressurize the cooling system with compressed air and regulate pressure between 5-15 psi.
Do Not Exceed 15 psi or Cooling System Damage Can Result.
7. Submerse the hose in a cup/bucket of water.
8. Monitor for 10 minutes and check for a steady rate of air bubbles coming out of the hose that is submersed in the cup/bucket of water.
9. If steady stream of air is present, replace the cylinder head, coolant regulators, and both 030-7937 port connectors. Depending on the application, you will need to replace some cooling system seals. (List of seals by application to be included)
10. Once the cylinder heads have been replaced pressure test the head again using the same procedure. Once this has been completed the cooling system should be flushed using instructions listed below.
Cleaning the Cooling System
1. Drain all of the coolant form cooling system.
2. Fill the cooling system with clean water.
3. Start engine and run it until the thermostat opens.
4. Add two cups of non-foaming liquid automatic dish washer soap.
Note: Do not use plain dish soap. Aeration of the cooling system and resultant damage could occur.
5. After the soap has bee added run engine for approximately twenty minutes. Check to see if the fuel is breaking up.
6. If the fuel is still not breaking up than add two more cups of soap and run for 10 minutes. Drain mixture from cooling system.
7. Fill cooling system with clean water and check surface for fuel. If fuel is present, repeat steps 3 through 7. When water is clear, drain and rinse the cooling system one more time. Then add coolant and conditioner.