Information injection-pump assembly
ZEXEL
101401-1623
1014011623
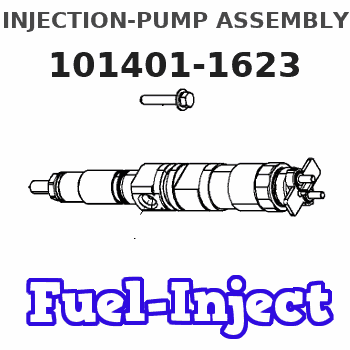
Rating:
Service parts 101401-1623 INJECTION-PUMP ASSEMBLY:
1.
_
6.
COUPLING PLATE
7.
COUPLING PLATE
8.
_
9.
_
11.
Nozzle and Holder
ME016989
12.
Open Pre:MPa(Kqf/cm2)
21.6{220}
15.
NOZZLE SET
Cross reference number
ZEXEL
101401-1623
1014011623
Zexel num
Bosch num
Firm num
Name
101401-1623
INJECTION-PUMP ASSEMBLY
Calibration Data:
Adjustment conditions
Test oil
1404 Test oil ISO4113 or {SAEJ967d}
1404 Test oil ISO4113 or {SAEJ967d}
Test oil temperature
degC
40
40
45
Nozzle and nozzle holder
105780-8140
Bosch type code
EF8511/9A
Nozzle
105780-0000
Bosch type code
DN12SD12T
Nozzle holder
105780-2080
Bosch type code
EF8511/9
Opening pressure
MPa
17.2
Opening pressure
kgf/cm2
175
Injection pipe
Outer diameter - inner diameter - length (mm) mm 6-2-600
Outer diameter - inner diameter - length (mm) mm 6-2-600
Overflow valve
131424-8820
Overflow valve opening pressure
kPa
157
123
191
Overflow valve opening pressure
kgf/cm2
1.6
1.25
1.95
Tester oil delivery pressure
kPa
157
157
157
Tester oil delivery pressure
kgf/cm2
1.6
1.6
1.6
Direction of rotation (viewed from drive side)
Right R
Right R
Injection timing adjustment
Direction of rotation (viewed from drive side)
Right R
Right R
Injection order
1-3-4-2
Pre-stroke
mm
3.2
3.15
3.25
Beginning of injection position
Drive side NO.1
Drive side NO.1
Difference between angles 1
Cal 1-3 deg. 90 89.5 90.5
Cal 1-3 deg. 90 89.5 90.5
Difference between angles 2
Cal 1-4 deg. 180 179.5 180.5
Cal 1-4 deg. 180 179.5 180.5
Difference between angles 3
Cyl.1-2 deg. 270 269.5 270.5
Cyl.1-2 deg. 270 269.5 270.5
Injection quantity adjustment
Adjusting point
-
Rack position
11.9
Pump speed
r/min
900
900
900
Average injection quantity
mm3/st.
73.9
72.3
75.5
Max. variation between cylinders
%
0
-2.5
2.5
Basic
*
Fixing the rack
*
Standard for adjustment of the maximum variation between cylinders
*
Injection quantity adjustment_02
Adjusting point
H
Rack position
9.5+-0.5
Pump speed
r/min
325
325
325
Average injection quantity
mm3/st.
11.2
9.9
12.5
Max. variation between cylinders
%
0
-10
10
Fixing the rack
*
Standard for adjustment of the maximum variation between cylinders
*
Injection quantity adjustment_03
Adjusting point
A
Rack position
R1(11.9)
Pump speed
r/min
900
900
900
Average injection quantity
mm3/st.
73.9
72.9
74.9
Basic
*
Fixing the lever
*
Boost pressure
kPa
24.7
24.7
Boost pressure
mmHg
185
185
Injection quantity adjustment_04
Adjusting point
B
Rack position
R1+1.8
Pump speed
r/min
1600
1600
1600
Average injection quantity
mm3/st.
92.5
88.5
96.5
Fixing the lever
*
Boost pressure
kPa
24.7
24.7
Boost pressure
mmHg
185
185
Injection quantity adjustment_05
Adjusting point
C
Rack position
(R1-1)
Pump speed
r/min
500
500
500
Average injection quantity
mm3/st.
46.3
42.3
50.3
Fixing the lever
*
Boost pressure
kPa
24.7
24.7
Boost pressure
mmHg
185
185
Injection quantity adjustment_06
Adjusting point
D
Rack position
R2-0.65
Pump speed
r/min
300
300
300
Average injection quantity
mm3/st.
18.7
14.7
22.7
Fixing the lever
*
Boost pressure
kPa
0
0
0
Boost pressure
mmHg
0
0
0
Boost compensator adjustment
Pump speed
r/min
300
300
300
Rack position
R2-0.65
Boost pressure
kPa
4
2.7
5.3
Boost pressure
mmHg
30
20
40
Boost compensator adjustment_02
Pump speed
r/min
300
300
300
Rack position
R2(R1-0.
65)
Boost pressure
kPa
11.3
11.3
11.3
Boost pressure
mmHg
85
85
85
Timer adjustment
Pump speed
r/min
1250--
Advance angle
deg.
0
0
0
Remarks
Start
Start
Timer adjustment_02
Pump speed
r/min
1200
Advance angle
deg.
0.5
Timer adjustment_03
Pump speed
r/min
1600
Advance angle
deg.
4.5
4
5
Remarks
Finish
Finish
Test data Ex:
Governor adjustment
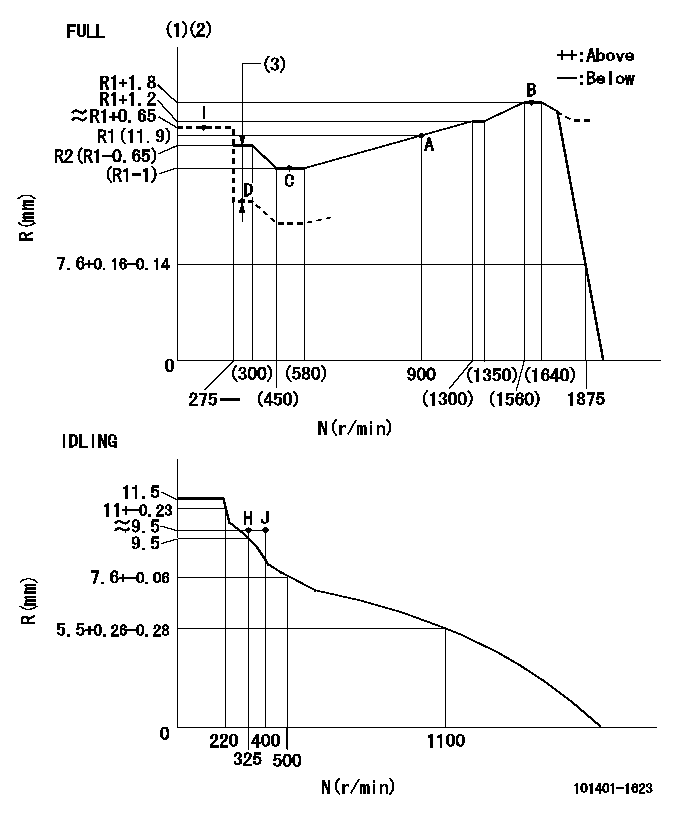
N:Pump speed
R:Rack position (mm)
(1)Torque cam stamping: T1
(2)Tolerance for racks not indicated: +-0.05mm.
(3)Boost compensator stroke: BCL
----------
T1=J00 BCL=0.65+-0.1mm
----------
----------
T1=J00 BCL=0.65+-0.1mm
----------
Speed control lever angle

F:Full speed
I:Idle
(1)Use the hole at R = aa
(2)Stopper bolt set position 'H'
----------
aa=40mm
----------
a=26deg+-5deg b=40deg+-3deg
----------
aa=40mm
----------
a=26deg+-5deg b=40deg+-3deg
Stop lever angle
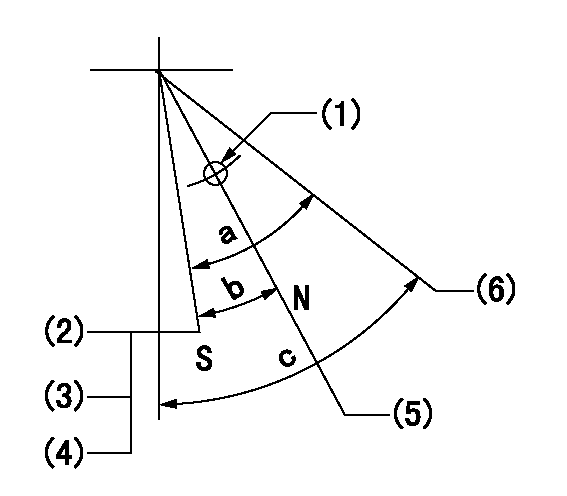
N:Engine manufacturer's normal use
S:Stop the pump.
(1)Use the hole at R = aa
(2)Set the stopper bolt at speed = bb and rack position = cc (non-injection rack position). Confirm non-injection.
(3)After setting the stopper bolt, confirm non-injection at speed dd. Rack position = ee or less (non-injection rack position).
(4)-
(5)Rack position corresponding to ff
(6)Free (at delivery)
----------
aa=40mm bb=1600r/min cc=5-0.5mm dd=325r/min ee=(8)mm ff=16mm
----------
a=29deg+-5deg b=19deg+-5deg c=33deg+-5deg
----------
aa=40mm bb=1600r/min cc=5-0.5mm dd=325r/min ee=(8)mm ff=16mm
----------
a=29deg+-5deg b=19deg+-5deg c=33deg+-5deg
0000001501 MICRO SWITCH
Adjustment of the micro-switch
Adjust the bolt to obtain the following lever position when the micro-switch is ON.
(1)Speed N1
(2)Rack position Ra
----------
N1=1025r/min Ra=8.5+-0.1mm
----------
----------
N1=1025r/min Ra=8.5+-0.1mm
----------
Timing setting

(1)Pump vertical direction
(2)Position of gear mark '3' at No 1 cylinder's beginning of injection
(3)B.T.D.C.: aa
(4)-
----------
aa=12deg
----------
a=(130deg)
----------
aa=12deg
----------
a=(130deg)
Information:
AUGUST 2010
INFORMATION RELEASE MEMO
Reman
PELJ1207 ?2010 Caterpillar CAT REMAN ANNOUNCES AN APPEARANCE CHANGE TO CERTAIN 3406 AND 3500 ELECTRONIC UNIT INJECTORS
Announcement
Cat Reman announces an appearance change to certain 3406 and 3500 electronic unit injectors. Effective immediately, certain remanufactured electronic unit injectors for 3406 and 3500 engines will be produced with stators, which have been ground slightly around the outside to remove potentially obsolete identification information. In many cases, these remanufactured injectors were previously produced with a metal sleeve around the outside of the stator to cover any potentially obsolete identifying information. Dealers will see both sleeved and ground stators for some period of time. This change will not impact quality, performance, form, fit, or function.
Effective immediately, Figure 1 and Figure 2 willboth represent acceptable appearance for the affected electronic unit injector part numbers. Table 1 lists all affected part numbers.
Core Acceptance
Core Acceptance Criteria for Cat Reman parts is simple, visual, and requires no special tools. Consult the Unit Injectors Electronic Core Acceptance Criteria (SELD0226) for complete details.
Warranty
Please consult the appropriate Caterpillar parts warranty statement for your area.
Core Management
Please refer to the Cat Core Management Information System (CMIS 2) Parts Information application describing all Cat Reman part/CAF and related information. Also refer to other CMIS 2 inquiry applications such as Customer Profiles, Inspection Reason Codes, Inspection Line Inquiry, Add Charge Information, Entitlement Activity, Entitlement Inquiry, CCR Inquiry, CCR Entry, Shipment Processing; Process Packaging Grief; and Reporting to properly manage core returns and monitor inspection performance. This information will be available to all dealers worldwide after your CMIS 2 conversion date. In the meantime, please continue to use the current CMIS Entitlement Parts Inquiry Screen describing the list of parts in a Core Acceptability Family (CAF) and related part number detail.
For the latest updates of Reman Policies and Core Management (SELD0122), Core Management Systems & Operations Procedures (SELD0040), and Shipping Instructions (SELD0039), go to the Reman Dealer website https://catreman.cat.com. If you have any questions regarding core return processing, feel free to call Corinth toll free at (800) 537-2928. Outside the US please refer to the Core section of the Reman website for appropriate contact information for your region.
For assistance with technical questions, call the Peoria Reman Technical Help Line also toll free at (888) 88-REMAN (outside the US call non-toll free +1-309-494-4342), or use our E-mail address--Reman_Help.
Have questions with 101401-1623?
Group cross 101401-1623 ZEXEL
101401-1623
INJECTION-PUMP ASSEMBLY