Information injection-pump assembly
ZEXEL
101401-1310
1014011310
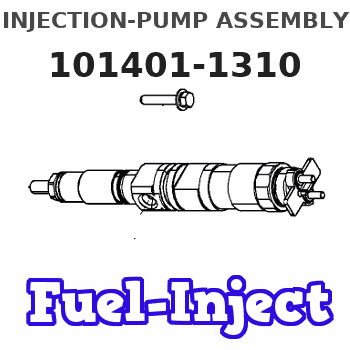
Rating:
Cross reference number
ZEXEL
101401-1310
1014011310
Zexel num
Bosch num
Firm num
Name
Calibration Data:
Adjustment conditions
Test oil
1404 Test oil ISO4113 or {SAEJ967d}
1404 Test oil ISO4113 or {SAEJ967d}
Test oil temperature
degC
40
40
45
Nozzle and nozzle holder
105780-8140
Bosch type code
EF8511/9A
Nozzle
105780-0000
Bosch type code
DN12SD12T
Nozzle holder
105780-2080
Bosch type code
EF8511/9
Opening pressure
MPa
17.2
Opening pressure
kgf/cm2
175
Injection pipe
Outer diameter - inner diameter - length (mm) mm 6-2-600
Outer diameter - inner diameter - length (mm) mm 6-2-600
Overflow valve
131424-6220
Overflow valve opening pressure
kPa
255
221
289
Overflow valve opening pressure
kgf/cm2
2.6
2.25
2.95
Tester oil delivery pressure
kPa
157
157
157
Tester oil delivery pressure
kgf/cm2
1.6
1.6
1.6
Direction of rotation (viewed from drive side)
Right R
Right R
Injection timing adjustment
Direction of rotation (viewed from drive side)
Right R
Right R
Injection order
1-3-4-2
Pre-stroke
mm
3.6
3.55
3.65
Beginning of injection position
Drive side NO.1
Drive side NO.1
Difference between angles 1
Cal 1-3 deg. 90 89.5 90.5
Cal 1-3 deg. 90 89.5 90.5
Difference between angles 2
Cal 1-4 deg. 180 179.5 180.5
Cal 1-4 deg. 180 179.5 180.5
Difference between angles 3
Cyl.1-2 deg. 270 269.5 270.5
Cyl.1-2 deg. 270 269.5 270.5
Injection quantity adjustment
Adjusting point
-
Rack position
12.5
Pump speed
r/min
1000
1000
1000
Average injection quantity
mm3/st.
72.1
70.5
73.7
Max. variation between cylinders
%
0
-2.5
2.5
Basic
*
Fixing the rack
*
Standard for adjustment of the maximum variation between cylinders
*
Injection quantity adjustment_02
Adjusting point
H
Rack position
9.5+-0.5
Pump speed
r/min
325
325
325
Average injection quantity
mm3/st.
10.2
8.9
11.5
Max. variation between cylinders
%
0
-10
10
Fixing the rack
*
Standard for adjustment of the maximum variation between cylinders
*
Injection quantity adjustment_03
Adjusting point
A
Rack position
R1(12.5)
Pump speed
r/min
1000
1000
1000
Average injection quantity
mm3/st.
72.1
71.1
73.1
Basic
*
Fixing the lever
*
Boost pressure
kPa
84
84
Boost pressure
mmHg
630
630
Injection quantity adjustment_04
Adjusting point
B
Rack position
R1+0.3
Pump speed
r/min
1750
1750
1750
Average injection quantity
mm3/st.
75.5
71.5
79.5
Fixing the lever
*
Boost pressure
kPa
84
84
Boost pressure
mmHg
630
630
Injection quantity adjustment_05
Adjusting point
C
Rack position
R1-1.5
Pump speed
r/min
700
700
700
Average injection quantity
mm3/st.
46.5
42.5
50.5
Fixing the lever
*
Boost pressure
kPa
0
0
0
Boost pressure
mmHg
0
0
0
Injection quantity adjustment_06
Adjusting point
D
Rack position
-
Pump speed
r/min
500
500
500
Average injection quantity
mm3/st.
53.4
49.4
57.4
Fixing the lever
*
Boost pressure
kPa
0
0
0
Boost pressure
mmHg
0
0
0
Injection quantity adjustment_07
Adjusting point
I
Rack position
-
Pump speed
r/min
100
100
100
Average injection quantity
mm3/st.
72
72
77
Fixing the lever
*
Rack limit
*
Boost compensator adjustment
Pump speed
r/min
700
700
700
Rack position
R1-1.5
Boost pressure
kPa
9.3
9.3
9.3
Boost pressure
mmHg
70
70
70
Boost compensator adjustment_02
Pump speed
r/min
700
700
700
Rack position
R1-1
Boost pressure
kPa
32
30.7
33.3
Boost pressure
mmHg
240
230
250
Boost compensator adjustment_03
Pump speed
r/min
700
700
700
Rack position
R1-0.3
Boost pressure
kPa
70.6
70.6
70.6
Boost pressure
mmHg
530
530
530
Timer adjustment
Pump speed
r/min
1500--
Advance angle
deg.
0
0
0
Load
3/4
Remarks
Start
Start
Timer adjustment_02
Pump speed
r/min
1450
Advance angle
deg.
0.3
Load
3/4
Timer adjustment_03
Pump speed
r/min
1750
Advance angle
deg.
4.5
4
5
Load
4/4
Remarks
Finish
Finish
Test data Ex:
Governor adjustment
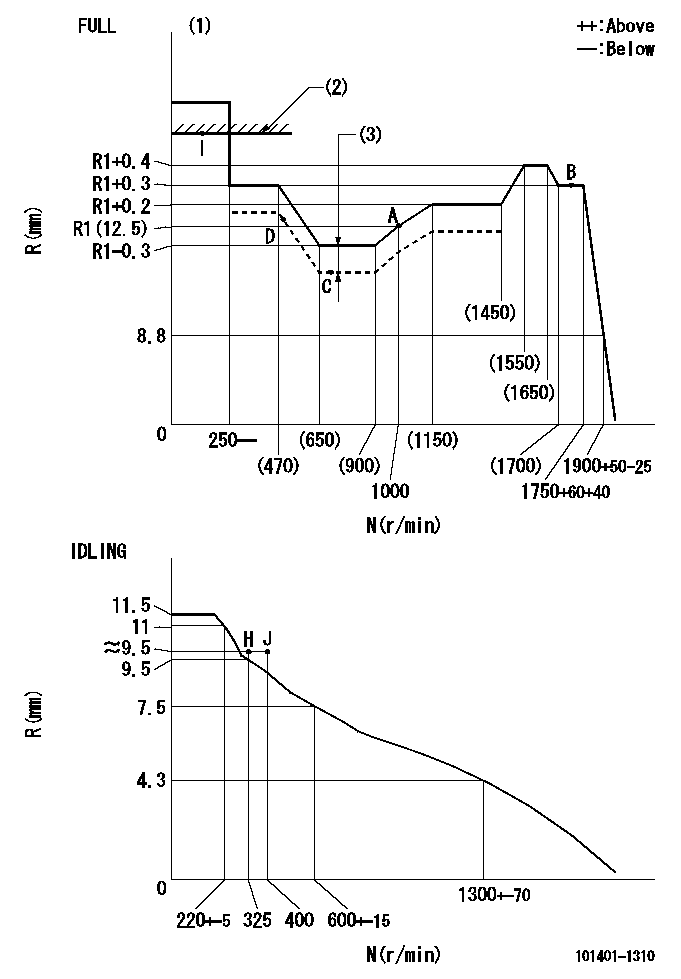
N:Pump speed
R:Rack position (mm)
(1)Torque cam stamping: T1
(2)RACK LIMIT
(3)Boost compensator stroke: BCL
----------
T1=C93 BCL=1.2+-0.1mm
----------
----------
T1=C93 BCL=1.2+-0.1mm
----------
Speed control lever angle

F:Full speed
I:Idle
(1)Use the hole at R = aa
(2)Stopper bolt set position 'H'
----------
aa=40mm
----------
a=26deg+-5deg b=(44deg)+-3deg
----------
aa=40mm
----------
a=26deg+-5deg b=(44deg)+-3deg
Stop lever angle

N:Engine manufacturer's normal use
S:Stop the pump.
(1)Free (at shipping)
(2)Use the hole at R = aa
(3)Rack position corresponding to bb
(4)Set the stopper bolt at speed = cc and rack position = dd.
(5)After setting the stopper bolt, confirm non-injection at speed ee. Rack position = ff or less.
----------
aa=40mm bb=16mm cc=1700r/min dd=6.5-0.5mm ee=325r/min ff=8mm
----------
a=8deg+-5deg b=15deg+-5deg c=25deg+-5deg
----------
aa=40mm bb=16mm cc=1700r/min dd=6.5-0.5mm ee=325r/min ff=8mm
----------
a=8deg+-5deg b=15deg+-5deg c=25deg+-5deg
0000001501 MICRO SWITCH
Adjustment of the micro-switch
Adjust the bolt to obtain the following lever position when the micro-switch is ON.
(1)Speed N1
(2)Rack position Ra
----------
N1=950+-5r/min Ra=8mm
----------
----------
N1=950+-5r/min Ra=8mm
----------
Timing setting

(1)Pump vertical direction
(2)Position of gear mark '3' at No 1 cylinder's beginning of injection
(3)B.T.D.C.: aa
(4)-
----------
aa=11deg
----------
a=(130deg)
----------
aa=11deg
----------
a=(130deg)
Information:
Determination Of Overhaul Timing
Generally, the engine needs an overhaul when the compression pressure of the engine becomes low, and the amounts of engine oil consumption and blow-by gas increase.Reduced power output, increased fuel consumption, low oil pressure, difficult in starting, and increased operating noise are also signs that suggest the need for an overhaul; however, since these problems can be caused by various factors, they do not serve as reliable criteria for determining the need for an overhaul.Reduced compression pressure manifests a variety of symptoms, thus making it difficult to accurately determine when the engine needs an overhaul. The following shows typical problems caused by reduced compression pressure.(1) Decreased output power(2) Increased fuel consumption(3) Increased engine oil consumption(4) Increased blow-by gas from breather due to leakage of combustion gas through worn cylinder liners and piston rings(5) Increased gas leakage due to poor seating of inlet and exhaust valves(6) Difficulty in starting(7) Increased noise from engine parts(8) Abnormal exhaust color after warm-up operationThe engine can exhibit these conditions in various combinations.Some of the problems are directly caused by worn engine parts, while others are not.Phenomena described in (2) and (6) can also result from improper injection volume, incorrect fuel injection timing, worn plungers, defective nozzles, and faulty conditions of electrical devices such as battery, starter and alternator.The most valid reason to overhaul an engine is a decrease in the compression pressure due to worn cylinder liners and pistons, as described in (4), and once this is determined, other symptoms should be taken into consideration in order to make the final judgement of whether the engine needs an overhaul.Measurement of Compression Pressure
Preparation For Inspection
Check the following before inspection.(1) Make sure that the engine oil, air cleaner, starter, battery, etc. are in normal operating condition.Inspection
(1) Move the control lever to the STOP position.(2) Remove the glow plugs from all cylinders, and attach the gage adapter and compression gage to the cylinder to be tested. (3) Crank the engine with the starter, and read the compression gage indication when the indication stabilizes.(4) If the measured compression pressure is lower than the limit, consider overhauling the engine.
(a) Measure the compression pressure in all cylinders.(b) As compression pressure varies with the engine speed, measure the engine speed at the same time.
Measure the compression pressure while the engine is running at 150 to 200 min-1. The oil and coolant temperatures should be between 20 and 30 °C [68 and 86°F].
(a) Measure the compression pressure at regular intervals and keep the record of changes in compression pressure.(b) Compression pressure will be slightly higher when the engine is new or immediately after an overhaul due to tight clearances of piston rings and valve seats, but it decreases to the standard level after the parts break in.
Preparation For Disassembly
Removing Electrical Wiring
Removing electrical wiringDisconnect harness and wires from the following devices.Before disconnecting, attach tags or other indications on the terminals to facilitate reconnection.* Starter* SwitchesDraining Coolant
Draining coolantLoosen the coolant drain plug on the right-hand side of the cylinder block
Generally, the engine needs an overhaul when the compression pressure of the engine becomes low, and the amounts of engine oil consumption and blow-by gas increase.Reduced power output, increased fuel consumption, low oil pressure, difficult in starting, and increased operating noise are also signs that suggest the need for an overhaul; however, since these problems can be caused by various factors, they do not serve as reliable criteria for determining the need for an overhaul.Reduced compression pressure manifests a variety of symptoms, thus making it difficult to accurately determine when the engine needs an overhaul. The following shows typical problems caused by reduced compression pressure.(1) Decreased output power(2) Increased fuel consumption(3) Increased engine oil consumption(4) Increased blow-by gas from breather due to leakage of combustion gas through worn cylinder liners and piston rings(5) Increased gas leakage due to poor seating of inlet and exhaust valves(6) Difficulty in starting(7) Increased noise from engine parts(8) Abnormal exhaust color after warm-up operationThe engine can exhibit these conditions in various combinations.Some of the problems are directly caused by worn engine parts, while others are not.Phenomena described in (2) and (6) can also result from improper injection volume, incorrect fuel injection timing, worn plungers, defective nozzles, and faulty conditions of electrical devices such as battery, starter and alternator.The most valid reason to overhaul an engine is a decrease in the compression pressure due to worn cylinder liners and pistons, as described in (4), and once this is determined, other symptoms should be taken into consideration in order to make the final judgement of whether the engine needs an overhaul.Measurement of Compression Pressure
Preparation For Inspection
Check the following before inspection.(1) Make sure that the engine oil, air cleaner, starter, battery, etc. are in normal operating condition.Inspection
(1) Move the control lever to the STOP position.(2) Remove the glow plugs from all cylinders, and attach the gage adapter and compression gage to the cylinder to be tested. (3) Crank the engine with the starter, and read the compression gage indication when the indication stabilizes.(4) If the measured compression pressure is lower than the limit, consider overhauling the engine.
(a) Measure the compression pressure in all cylinders.(b) As compression pressure varies with the engine speed, measure the engine speed at the same time.
Measure the compression pressure while the engine is running at 150 to 200 min-1. The oil and coolant temperatures should be between 20 and 30 °C [68 and 86°F].
(a) Measure the compression pressure at regular intervals and keep the record of changes in compression pressure.(b) Compression pressure will be slightly higher when the engine is new or immediately after an overhaul due to tight clearances of piston rings and valve seats, but it decreases to the standard level after the parts break in.
Preparation For Disassembly
Removing Electrical Wiring
Removing electrical wiringDisconnect harness and wires from the following devices.Before disconnecting, attach tags or other indications on the terminals to facilitate reconnection.* Starter* SwitchesDraining Coolant
Draining coolantLoosen the coolant drain plug on the right-hand side of the cylinder block