Information injection-pump assembly
BOSCH
9 400 613 590
9400613590
ZEXEL
101401-0950
1014010950
ISUZU
8943777451
8943777451
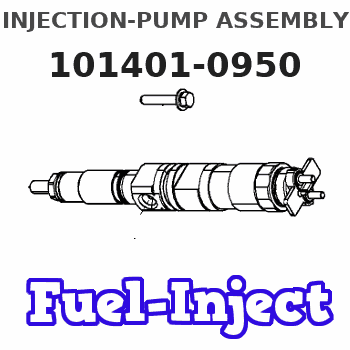
Rating:
Service parts 101401-0950 INJECTION-PUMP ASSEMBLY:
1.
_
6.
COUPLING PLATE
7.
COUPLING PLATE
8.
_
9.
_
11.
Nozzle and Holder
8-94479-578-3
12.
Open Pre:MPa(Kqf/cm2)
21.6{220}
15.
NOZZLE SET
Cross reference number
BOSCH
9 400 613 590
9400613590
ZEXEL
101401-0950
1014010950
ISUZU
8943777451
8943777451
Zexel num
Bosch num
Firm num
Name
Calibration Data:
Adjustment conditions
Test oil
1404 Test oil ISO4113 or {SAEJ967d}
1404 Test oil ISO4113 or {SAEJ967d}
Test oil temperature
degC
40
40
45
Nozzle and nozzle holder
105780-8140
Bosch type code
EF8511/9A
Nozzle
105780-0000
Bosch type code
DN12SD12T
Nozzle holder
105780-2080
Bosch type code
EF8511/9
Opening pressure
MPa
17.2
Opening pressure
kgf/cm2
175
Injection pipe
Outer diameter - inner diameter - length (mm) mm 6-2-600
Outer diameter - inner diameter - length (mm) mm 6-2-600
Overflow valve
131424-4920
Overflow valve opening pressure
kPa
127
107
147
Overflow valve opening pressure
kgf/cm2
1.3
1.1
1.5
Tester oil delivery pressure
kPa
157
157
157
Tester oil delivery pressure
kgf/cm2
1.6
1.6
1.6
Direction of rotation (viewed from drive side)
Right R
Right R
Injection timing adjustment
Direction of rotation (viewed from drive side)
Right R
Right R
Injection order
1-3-4-2
Pre-stroke
mm
3.6
3.55
3.65
Rack position
Point A R=A
Point A R=A
Beginning of injection position
Drive side NO.1
Drive side NO.1
Difference between angles 1
Cal 1-3 deg. 90 89.5 90.5
Cal 1-3 deg. 90 89.5 90.5
Difference between angles 2
Cal 1-4 deg. 180 179.5 180.5
Cal 1-4 deg. 180 179.5 180.5
Difference between angles 3
Cyl.1-2 deg. 270 269.5 270.5
Cyl.1-2 deg. 270 269.5 270.5
Injection quantity adjustment
Adjusting point
-
Rack position
11.2
Pump speed
r/min
900
900
900
Average injection quantity
mm3/st.
69.6
68
71.2
Max. variation between cylinders
%
0
-4
4
Basic
*
Fixing the rack
*
Standard for adjustment of the maximum variation between cylinders
*
Injection quantity adjustment_02
Adjusting point
H
Rack position
9.5+-0.5
Pump speed
r/min
300
300
300
Average injection quantity
mm3/st.
9.5
8.2
10.8
Max. variation between cylinders
%
0
-14
14
Fixing the rack
*
Standard for adjustment of the maximum variation between cylinders
*
Injection quantity adjustment_03
Adjusting point
A
Rack position
R1(11.2)
Pump speed
r/min
900
900
900
Average injection quantity
mm3/st.
69.6
68.6
70.6
Basic
*
Fixing the lever
*
Injection quantity adjustment_04
Adjusting point
B
Rack position
R1+0.15
Pump speed
r/min
1525
1525
1525
Average injection quantity
mm3/st.
82.1
78.9
85.3
Fixing the lever
*
Injection quantity adjustment_05
Adjusting point
C
Rack position
R1(11.2)
Pump speed
r/min
600
600
600
Average injection quantity
mm3/st.
53.1
49.9
56.3
Fixing the lever
*
Injection quantity adjustment_06
Adjusting point
I
Rack position
-
Pump speed
r/min
150
150
150
Average injection quantity
mm3/st.
86
78
94
Fixing the lever
*
Timer adjustment
Pump speed
r/min
1370--
Advance angle
deg.
0
0
0
Remarks
Start
Start
Timer adjustment_02
Pump speed
r/min
1320
Advance angle
deg.
0.3
Timer adjustment_03
Pump speed
r/min
1600
Advance angle
deg.
5
4.5
5.5
Remarks
Finish
Finish
Test data Ex:
Governor adjustment
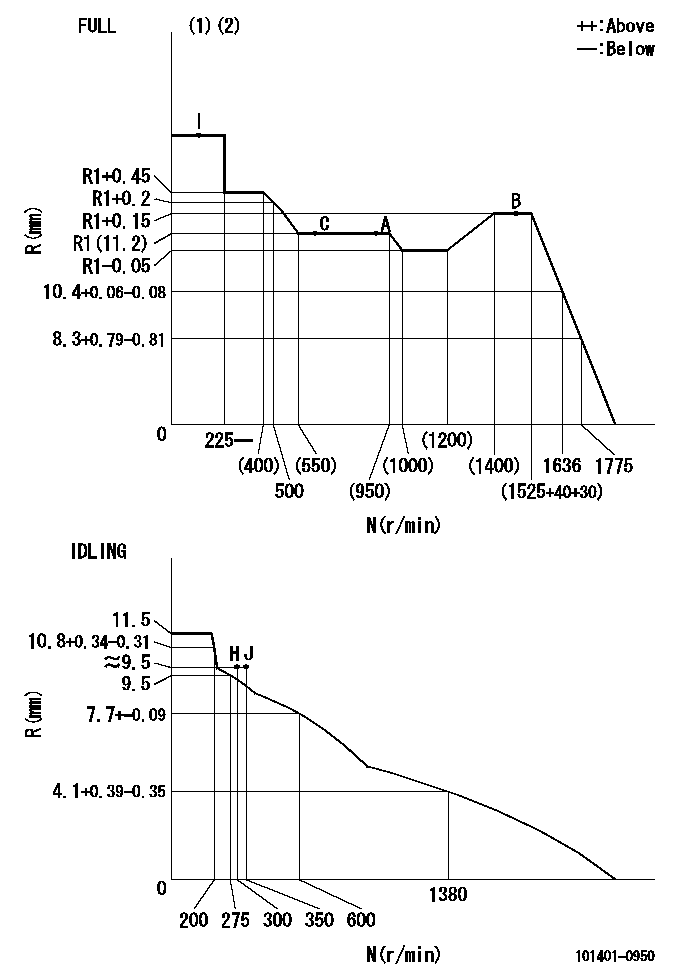
N:Pump speed
R:Rack position (mm)
(1)Torque cam stamping: T1
(2)Tolerance for racks not indicated: +-0.05mm.
----------
T1=D65
----------
----------
T1=D65
----------
Speed control lever angle
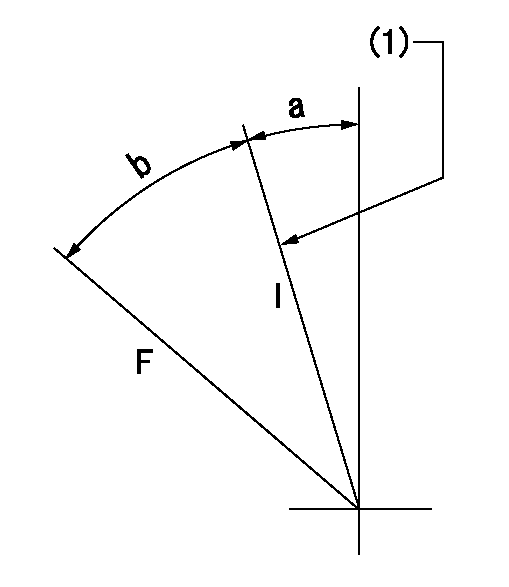
F:Full speed
I:Idle
(1)Stopper bolt set position 'H'
----------
----------
a=2.5deg+-5deg b=33.5deg+-3deg
----------
----------
a=2.5deg+-5deg b=33.5deg+-3deg
0000001501 FICD
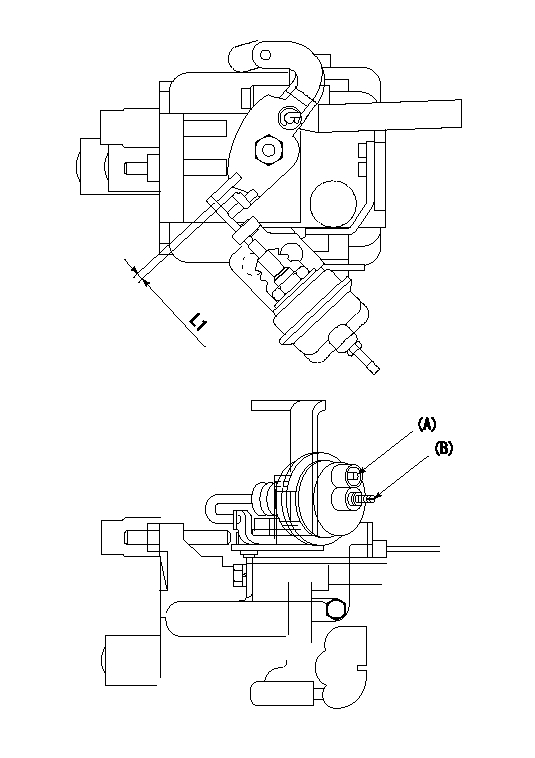
Negative pressure port A
(B) Screw
1. FICD adjustment
(1)Set the clearance between the actuator and the speed lever at L1.
(2)Fully screw in screw B.
(3)Apply P1 to negative pressure port A and gradually tighten screw B.
(4)Fix the screw (B) at pump speed N1 and rack position R1. (Tightening torque = T1)
(5)Apply P2 to negative pressure port A and confirm that the FICD operates normally.
----------
L1=(3)mm P1=53.3kPa(400mmHg) P2=53.3kPa(400mmHg) N1=600r/min R1=9.2+-0.1mm T1=1.2~1.6N-m(0.12~0.16kgf-m)
----------
----------
L1=(3)mm P1=53.3kPa(400mmHg) P2=53.3kPa(400mmHg) N1=600r/min R1=9.2+-0.1mm T1=1.2~1.6N-m(0.12~0.16kgf-m)
----------
Timing setting

(1)Pump vertical direction
(2)Position of gear mark 'CC' at No 1 cylinder's beginning of injection
(3)B.T.D.C.: aa
(4)-
----------
aa=12deg
----------
a=(100deg)
----------
aa=12deg
----------
a=(100deg)
Information:
Water Pump
Disassembly of Water Pump
Inspection of Water Pump
If the inspection of the impeller and shaft finds abnormal noise or rough rotation, replace the assembly.
Inspection of impeller and shaft rotation conditionThermostat
Disassembly of Thermostat
Inspection of Thermostat
To test the thermostat operation, immerse the thermostat in a container filled with water, and heat the water while measuring the water temperature. Record the temperature at which the valve starts to open and the temperature at which the valve lift becomes 8 mm [0.3 in.] or more. (a) Stir the water in the container to ensure uniform temperature distribution.(b) When installing the thermostat, be sure to check the valve opening temperature indication stamped on the upper face of the thermostat mounting flange.
Inspection of thermostatThermo Switch
Inspection of Thermo Switch
Immerse the temperature sensor in oil, and measure the resistance while increasing the oil temperature. If the temperature measurement exceeds the standard value significantly, replace the thermo switch.
Since the inspection requires heating of oil to high temperatures, be careful not to get burns or start a fire.
Inspection of thermo switch
Disassembly of Water Pump
Inspection of Water Pump
If the inspection of the impeller and shaft finds abnormal noise or rough rotation, replace the assembly.
Inspection of impeller and shaft rotation conditionThermostat
Disassembly of Thermostat
Inspection of Thermostat
To test the thermostat operation, immerse the thermostat in a container filled with water, and heat the water while measuring the water temperature. Record the temperature at which the valve starts to open and the temperature at which the valve lift becomes 8 mm [0.3 in.] or more. (a) Stir the water in the container to ensure uniform temperature distribution.(b) When installing the thermostat, be sure to check the valve opening temperature indication stamped on the upper face of the thermostat mounting flange.
Inspection of thermostatThermo Switch
Inspection of Thermo Switch
Immerse the temperature sensor in oil, and measure the resistance while increasing the oil temperature. If the temperature measurement exceeds the standard value significantly, replace the thermo switch.
Since the inspection requires heating of oil to high temperatures, be careful not to get burns or start a fire.
Inspection of thermo switch