Information injection-pump assembly
ZEXEL
101401-0771
1014010771

Rating:
Cross reference number
ZEXEL
101401-0771
1014010771
Zexel num
Bosch num
Firm num
Name
Calibration Data:
Adjustment conditions
Test oil
1404 Test oil ISO4113 or {SAEJ967d}
1404 Test oil ISO4113 or {SAEJ967d}
Test oil temperature
degC
40
40
45
Nozzle and nozzle holder
105780-8140
Bosch type code
EF8511/9A
Nozzle
105780-0000
Bosch type code
DN12SD12T
Nozzle holder
105780-2080
Bosch type code
EF8511/9
Opening pressure
MPa
17.2
Opening pressure
kgf/cm2
175
Injection pipe
Outer diameter - inner diameter - length (mm) mm 6-2-600
Outer diameter - inner diameter - length (mm) mm 6-2-600
Overflow valve
131424-4920
Overflow valve opening pressure
kPa
127
107
147
Overflow valve opening pressure
kgf/cm2
1.3
1.1
1.5
Tester oil delivery pressure
kPa
157
157
157
Tester oil delivery pressure
kgf/cm2
1.6
1.6
1.6
Direction of rotation (viewed from drive side)
Right R
Right R
Injection timing adjustment
Direction of rotation (viewed from drive side)
Right R
Right R
Injection order
1-3-4-2
Pre-stroke
mm
3.4
3.35
3.45
Beginning of injection position
Drive side NO.1
Drive side NO.1
Difference between angles 1
Cal 1-3 deg. 90 89.5 90.5
Cal 1-3 deg. 90 89.5 90.5
Difference between angles 2
Cal 1-4 deg. 180 179.5 180.5
Cal 1-4 deg. 180 179.5 180.5
Difference between angles 3
Cyl.1-2 deg. 270 269.5 270.5
Cyl.1-2 deg. 270 269.5 270.5
Injection quantity adjustment
Adjusting point
-
Rack position
11.6
Pump speed
r/min
950
950
950
Average injection quantity
mm3/st.
72.1
70.5
73.7
Max. variation between cylinders
%
0
-2.5
2.5
Basic
*
Fixing the rack
*
Standard for adjustment of the maximum variation between cylinders
*
Injection quantity adjustment_02
Adjusting point
H
Rack position
9.5+-0.5
Pump speed
r/min
325
325
325
Average injection quantity
mm3/st.
12.1
10.8
13.4
Max. variation between cylinders
%
0
-14
14
Fixing the rack
*
Standard for adjustment of the maximum variation between cylinders
*
Injection quantity adjustment_03
Adjusting point
A
Rack position
R1(11.6)
Pump speed
r/min
950
950
950
Average injection quantity
mm3/st.
72.1
71.1
73.1
Basic
*
Fixing the lever
*
Injection quantity adjustment_04
Adjusting point
B
Rack position
R1+0.2
Pump speed
r/min
1500
1500
1500
Average injection quantity
mm3/st.
82.6
79.4
85.8
Fixing the lever
*
Injection quantity adjustment_05
Adjusting point
C
Rack position
R1+0.1
Pump speed
r/min
500
500
500
Average injection quantity
mm3/st.
53.6
49.6
57.6
Fixing the lever
*
Injection quantity adjustment_06
Adjusting point
D
Rack position
(R1+0.1)
Pump speed
r/min
1100
1100
1100
Average injection quantity
mm3/st.
76.1
72.9
79.3
Fixing the lever
*
Injection quantity adjustment_07
Adjusting point
I
Rack position
-
Pump speed
r/min
150
150
150
Average injection quantity
mm3/st.
116
116
124
Fixing the lever
*
Rack limit
*
Timer adjustment
Pump speed
r/min
1000+-50
Advance angle
deg.
0
0
0
Remarks
Start
Start
Timer adjustment_02
Pump speed
r/min
1600
Advance angle
deg.
2
1.5
2.5
Remarks
Finish
Finish
Test data Ex:
Governor adjustment
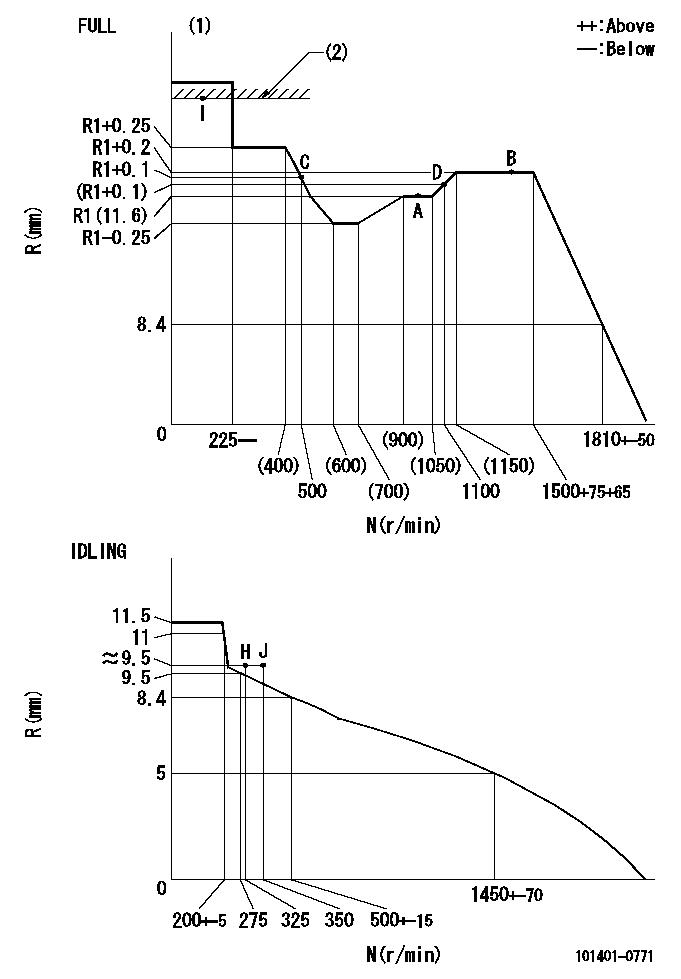
N:Pump speed
R:Rack position (mm)
(1)Torque cam stamping: T1
(2)RACK LIMIT
----------
T1=C52
----------
----------
T1=C52
----------
Speed control lever angle
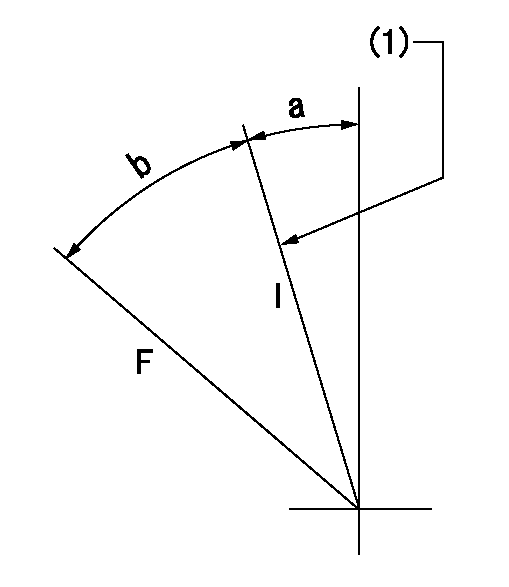
F:Full speed
I:Idle
(1)Stopper bolt set position 'H'
----------
----------
a=3.5deg+-5deg b=27deg+-3deg
----------
----------
a=3.5deg+-5deg b=27deg+-3deg
Stop lever angle
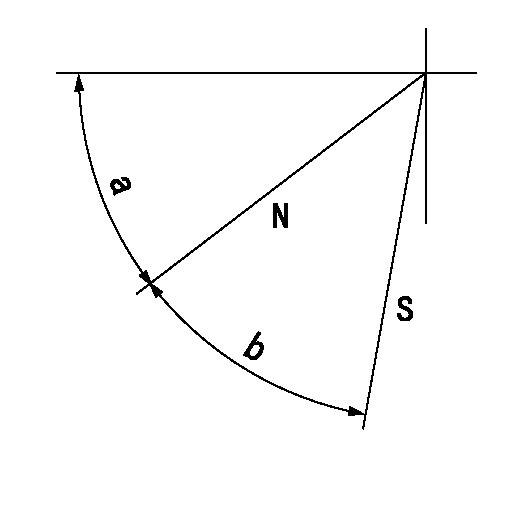
N:Pump normal
S:Stop the pump.
----------
----------
a=45deg+-5deg b=40deg+-5deg
----------
----------
a=45deg+-5deg b=40deg+-5deg
0000001501 ACS
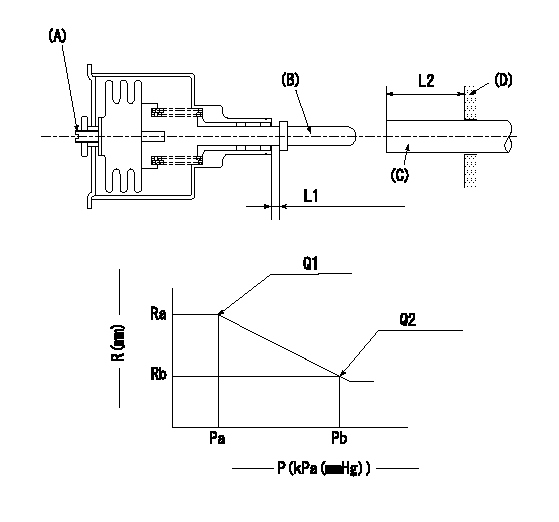
(A) Set screw
(B) Push rod 1
(C) Push rod 2
(D) Cover
1. Aneroid compensator unit adjustment
(1)Select the push rod 2 to obtain L2.
(2)Screw in (A) to obtain L1.
2. Adjustment when mounting the governor.
(1)Set the speed of the pump to N1 r/min and fix the control lever at the full set position.
(2)Screw in the aneroid compensator to obtain the performance shown in the graph above.
(3)As there is hysterisis, measure when the absolute pressure drops.
(4)Hysterisis must not exceed rack position = h1.
----------
N1=950r/min L1=(1.5)mm L2=11+-0.5mm h1=0.15mm
----------
Ra=R1(11.6)mm Rb=(R1-0.15)mm Pa=79.4+-2.7kPa(596+-20mmHg) Pb=70.1+-0.7kPa(526+-5mmHg) Q1=72.1+-1cm3/1000st Q2=69.8+-1.6cm3/1000st
----------
N1=950r/min L1=(1.5)mm L2=11+-0.5mm h1=0.15mm
----------
Ra=R1(11.6)mm Rb=(R1-0.15)mm Pa=79.4+-2.7kPa(596+-20mmHg) Pb=70.1+-0.7kPa(526+-5mmHg) Q1=72.1+-1cm3/1000st Q2=69.8+-1.6cm3/1000st
Timing setting

(1)Pump vertical direction
(2)Position of gear mark 'CC' at No 1 cylinder's beginning of injection
(3)B.T.D.C.: aa
(4)-
----------
aa=13deg
----------
a=(100deg)
----------
aa=13deg
----------
a=(100deg)
Information:
Removing delivery valve and spring(2) Inspection(a) Open the cock on the fuel filter. If the system has an electromagnetic pump, turn the key to the ON position. Fuel will flow out of the injection pipe. Make ready a container to catch it. If the system has an electromagnetic pump, caution is required since fuel will emerge with great force.(b) Slowly turn the crankshaft clockwise. The injection timing is reached when fuel stops flowing out. When fuel has stopped flowing out, turn the crankshaft slightly in the reverse direction such that fuel flows out. Then, slowly turn the crankshaft clockwise again to more accurately verify the point at which stops flowing out.
Fuel flow
End of fuel flow(c) If the IT mark on the crankshaft pulley and the mark on the gear case are aligned when fuel stops flowing out, the injection timing is normal.
Timing marks(3) Adjustment(a) If the injection timing is out of specification, make adjustments by increasing or decreasing the thickness of the injection pump's mounting shim. A change of 0.1 mm in the shim thickness yields a change of approximately 1° in the injection timing.(b) Increasing the shim thickness retards the injection timing, and decreasing the shim thickness advances it. Shims are available in thicknesses of 0.2 mm (0.008 in.), 0.3 mm (0.012 in.), 0.4 mm (0.016 in.), and 0.8 mm (0.031 in.). The thicknesses are not indicated on the shims, so any shim should be measured with a vernier caliper before being used.
Before using any shim, apply sealant to both sides to prevent oil leakage.
(c) After making adjustments, check that the injection timing is correct.(d) Close the cock on the fuel filter, then fit the delivery valve spring and injection pipe in their original positions.
Injection timing adjustment shim
Adjusting injection timing1.4 Adjusting Idle Speed(1) Preparation for Adjustment(a) Warm up the engine until the coolant reaches a temperature of 60°C (140°F) or higher.(b) Make sure the valve clearances, injection timing, and injectors are normal.(2) Adjusting Low-Idle SpeedLoosen the lock nut on the idling set bolt, turn the bolt to achieve the specified low-idle speed (1,000 25 min-1), then tighten the lock nut to hold the bolt in that position.(3) Adjusting No-Load Maximum SpeedLoosen the lock nut on the high-speed set bolt, turn the bolt to achieve the specified no-load maximum speed (2870+30-10 min-1), then tighten the lock nut to hold the bolt in that position.
Adjusting idle speed1.5 Adjusting Fan Belt Tension(1) Press the fan belt with the specified force mid-way between the alternator pulley and crankshaft pulley, and observe the extent of deflection. (2) If the extent of deflection is out of specification, loosen the adjusting bolt and adjust the fan belt tension by moving the alternator. Retighten the adjusting bolt securely.
Adjusting fan belt tension2. Running in the Engine
After an overhaul, the engine should be tested and inspected on a dynamometer. This operation serves to run in the engine's major moving parts.2.1 Starting the Engine(1) Before starting the engine, check the coolant, engine oil, and fuel levels and