Information injection-pump assembly
ZEXEL
101401-0621
1014010621
ISUZU
8941778750
8941778750
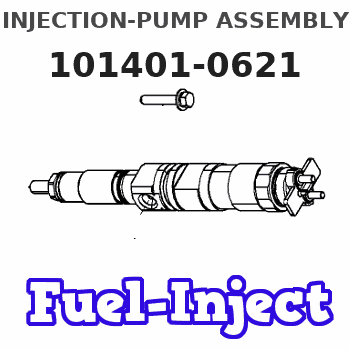
Rating:
Cross reference number
ZEXEL
101401-0621
1014010621
ISUZU
8941778750
8941778750
Zexel num
Bosch num
Firm num
Name
Calibration Data:
Adjustment conditions
Test oil
1404 Test oil ISO4113 or {SAEJ967d}
1404 Test oil ISO4113 or {SAEJ967d}
Test oil temperature
degC
40
40
45
Nozzle and nozzle holder
105780-8140
Bosch type code
EF8511/9A
Nozzle
105780-0000
Bosch type code
DN12SD12T
Nozzle holder
105780-2080
Bosch type code
EF8511/9
Opening pressure
MPa
17.2
Opening pressure
kgf/cm2
175
Injection pipe
Outer diameter - inner diameter - length (mm) mm 6-2-600
Outer diameter - inner diameter - length (mm) mm 6-2-600
Overflow valve
131424-4920
Overflow valve opening pressure
kPa
127
107
147
Overflow valve opening pressure
kgf/cm2
1.3
1.1
1.5
Tester oil delivery pressure
kPa
157
157
157
Tester oil delivery pressure
kgf/cm2
1.6
1.6
1.6
Direction of rotation (viewed from drive side)
Right R
Right R
Injection timing adjustment
Direction of rotation (viewed from drive side)
Right R
Right R
Injection order
1-3-4-2
Pre-stroke
mm
3.4
3.35
3.45
Beginning of injection position
Drive side NO.1
Drive side NO.1
Difference between angles 1
Cal 1-3 deg. 90 89.5 90.5
Cal 1-3 deg. 90 89.5 90.5
Difference between angles 2
Cal 1-4 deg. 180 179.5 180.5
Cal 1-4 deg. 180 179.5 180.5
Difference between angles 3
Cyl.1-2 deg. 270 269.5 270.5
Cyl.1-2 deg. 270 269.5 270.5
Injection quantity adjustment
Adjusting point
-
Rack position
11.8
Pump speed
r/min
950
950
950
Average injection quantity
mm3/st.
72.6
71
74.2
Max. variation between cylinders
%
0
-2.5
2.5
Basic
*
Fixing the rack
*
Standard for adjustment of the maximum variation between cylinders
*
Injection quantity adjustment_02
Adjusting point
H
Rack position
9.5+-0.5
Pump speed
r/min
300
300
300
Average injection quantity
mm3/st.
11.4
10.1
12.7
Max. variation between cylinders
%
0
-14
14
Fixing the rack
*
Standard for adjustment of the maximum variation between cylinders
*
Injection quantity adjustment_03
Adjusting point
A
Rack position
R1(11.8)
Pump speed
r/min
950
950
950
Average injection quantity
mm3/st.
72.6
71.6
73.6
Basic
*
Fixing the lever
*
Injection quantity adjustment_04
Adjusting point
B
Rack position
R1+0.05
Pump speed
r/min
1500
1500
1500
Average injection quantity
mm3/st.
80.1
76.9
83.3
Fixing the lever
*
Injection quantity adjustment_05
Adjusting point
C
Rack position
R1+0.05
Pump speed
r/min
500
500
500
Average injection quantity
mm3/st.
56
52.8
59.2
Fixing the lever
*
Injection quantity adjustment_06
Adjusting point
I
Rack position
-
Pump speed
r/min
150
150
150
Average injection quantity
mm3/st.
116.5
116.5
124.5
Fixing the lever
*
Rack limit
*
Timer adjustment
Pump speed
r/min
1150+-50
Advance angle
deg.
0
0
0
Remarks
Start
Start
Timer adjustment_02
Pump speed
r/min
1500
Advance angle
deg.
2
1.5
2.5
Remarks
Finish
Finish
Test data Ex:
Governor adjustment
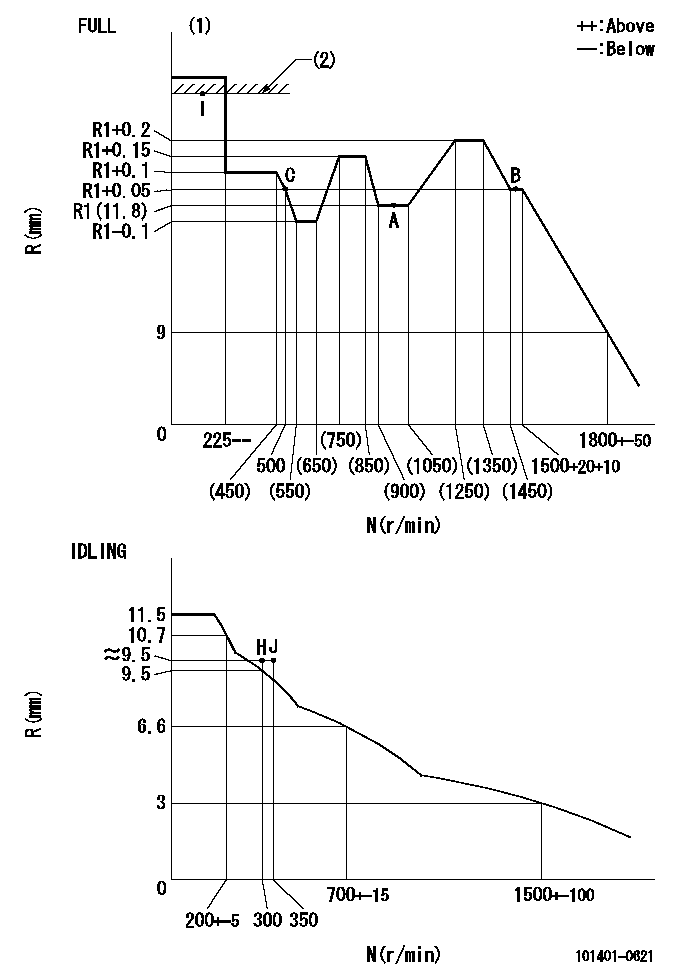
N:Pump speed
R:Rack position (mm)
(1)Torque cam stamping: T1
(2)RACK LIMIT
----------
T1=B39
----------
----------
T1=B39
----------
Speed control lever angle
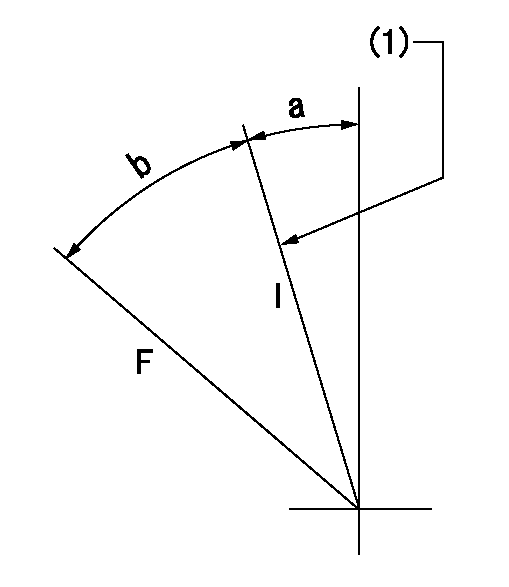
F:Full speed
I:Idle
(1)Stopper bolt set position 'H'
----------
----------
a=2.5deg+-5deg b=34deg+-3deg
----------
----------
a=2.5deg+-5deg b=34deg+-3deg
Stop lever angle
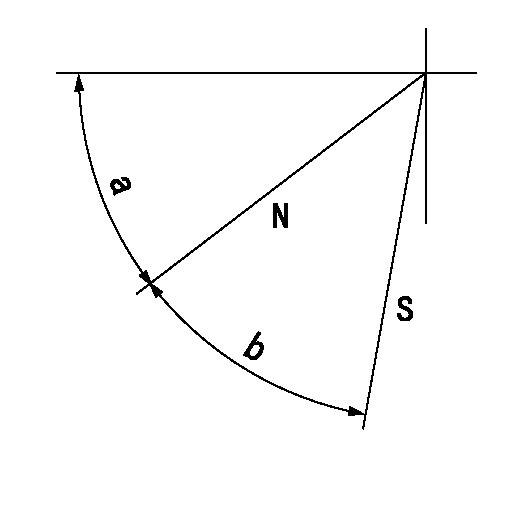
N:Pump normal
S:Stop the pump.
----------
----------
a=45deg+-5deg b=40deg+-5deg
----------
----------
a=45deg+-5deg b=40deg+-5deg
0000001501 ACS
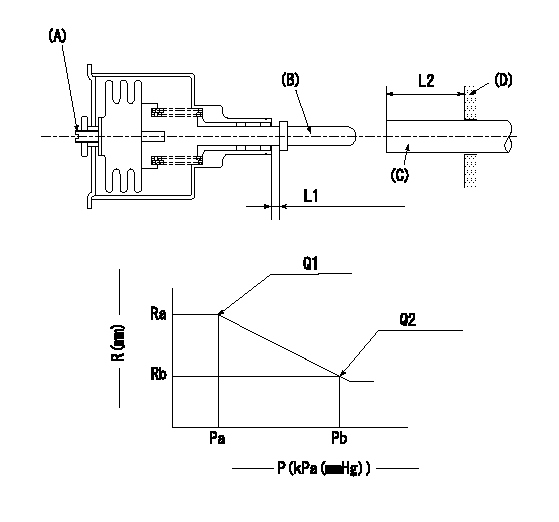
(A) Set screw
(B) Push rod 1
(C) Push rod 2
(D) Cover
1. Aneroid compensator unit adjustment
(1)Select the push rod 2 to obtain L2.
(2)Screw in (A) to obtain L1.
2. Adjustment when mounting the governor.
(1)Set the speed of the pump to N1 r/min and fix the control lever at the full set position.
(2)Screw in the aneroid compensator to obtain the performance shown in the graph above.
(3)As there is hysterisis, measure when the absolute pressure drops.
(4)Hysterisis must not exceed rack position = h1.
----------
N1=950r/min L1=(1.5)mm L2=11+-0.5mm h1=0.15mm
----------
Ra=R1(11.8)mm Rb=(R1-0.3)mm Pa=89.8+-2.7kPa(674+-20mmHg) Pb=70.1+-0.7kPa(526+-5mmHg) Q1=72.6+-1cm3/1000st Q2=67+-1.5cm3/1000st
----------
N1=950r/min L1=(1.5)mm L2=11+-0.5mm h1=0.15mm
----------
Ra=R1(11.8)mm Rb=(R1-0.3)mm Pa=89.8+-2.7kPa(674+-20mmHg) Pb=70.1+-0.7kPa(526+-5mmHg) Q1=72.6+-1cm3/1000st Q2=67+-1.5cm3/1000st
Timing setting

(1)Pump vertical direction
(2)Position of gear mark 'CC' at No 1 cylinder's beginning of injection
(3)B.T.D.C.: aa
(4)-
----------
aa=6deg
----------
a=(100deg)
----------
aa=6deg
----------
a=(100deg)
Information:
Thermostat Removal
Stop engine.Disconnect negative (-) battery cable at battery.
Do not drain engine coolant until the coolant temperature is below operating temperature. Then loosen drain cock slowly to relieve any excess pressure.
Remove coolant from cooling system.
Fig. 1-Thermostat CoverDisconnect upper radiator hose from thermostat cover (Fig. 1).Remove thermostat cover.Remove gasket.
Fig. 2-ThermostatLift thermostat (Fig. 2) out of thermostat housing.Repair
Fig. 3-Thermostat OpenIf engine is running too hot or too cold inspect thermostat for defects. Test in hot water for proper opening and closing.Installation
Some thermostats are marked "TO RAD", "THIS SIDE TOWARD RADIATOR", or "TOWARD RADIATOR" to indicate the top side. Put thermostat in housing so that top side is toward thermostat cover.
Fig. 4-Top SideIf thermostat is not marked, find the top side (Fig. 4). Put thermostat in housing so that top side is toward thermostat cover.
Fig. 5-Cap ScrewUsing a new gasket, install thermostat cover. Put cap screws (Fig. 5) through thermostat cover into thermostat housing. Tighten cap screws to 35 lb-ft (47 N m) (5 kg-m).Connect upper radiator hose to thermostat cover.Fill cooling system to proper level with proper coolant.Connect negative (-) battery cable to battery negative (-) terminal.Start engine.Check for leaks at hose connection and around gasket area.
Stop engine.Disconnect negative (-) battery cable at battery.
Do not drain engine coolant until the coolant temperature is below operating temperature. Then loosen drain cock slowly to relieve any excess pressure.
Remove coolant from cooling system.
Fig. 1-Thermostat CoverDisconnect upper radiator hose from thermostat cover (Fig. 1).Remove thermostat cover.Remove gasket.
Fig. 2-ThermostatLift thermostat (Fig. 2) out of thermostat housing.Repair
Fig. 3-Thermostat OpenIf engine is running too hot or too cold inspect thermostat for defects. Test in hot water for proper opening and closing.Installation
Some thermostats are marked "TO RAD", "THIS SIDE TOWARD RADIATOR", or "TOWARD RADIATOR" to indicate the top side. Put thermostat in housing so that top side is toward thermostat cover.
Fig. 4-Top SideIf thermostat is not marked, find the top side (Fig. 4). Put thermostat in housing so that top side is toward thermostat cover.
Fig. 5-Cap ScrewUsing a new gasket, install thermostat cover. Put cap screws (Fig. 5) through thermostat cover into thermostat housing. Tighten cap screws to 35 lb-ft (47 N m) (5 kg-m).Connect upper radiator hose to thermostat cover.Fill cooling system to proper level with proper coolant.Connect negative (-) battery cable to battery negative (-) terminal.Start engine.Check for leaks at hose connection and around gasket area.