Information injection-pump assembly
ZEXEL
101401-0620
1014010620
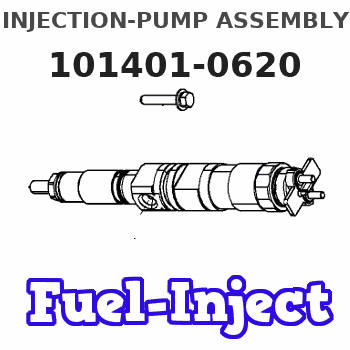
Rating:
Cross reference number
ZEXEL
101401-0620
1014010620
Zexel num
Bosch num
Firm num
Name
Calibration Data:
Adjustment conditions
Test oil
1404 Test oil ISO4113 or {SAEJ967d}
1404 Test oil ISO4113 or {SAEJ967d}
Test oil temperature
degC
40
40
45
Nozzle and nozzle holder
105780-8140
Bosch type code
EF8511/9A
Nozzle
105780-0000
Bosch type code
DN12SD12T
Nozzle holder
105780-2080
Bosch type code
EF8511/9
Opening pressure
MPa
17.2
Opening pressure
kgf/cm2
175
Injection pipe
Outer diameter - inner diameter - length (mm) mm 6-2-600
Outer diameter - inner diameter - length (mm) mm 6-2-600
Overflow valve
131424-4920
Overflow valve opening pressure
kPa
127
107
147
Overflow valve opening pressure
kgf/cm2
1.3
1.1
1.5
Tester oil delivery pressure
kPa
157
157
157
Tester oil delivery pressure
kgf/cm2
1.6
1.6
1.6
Direction of rotation (viewed from drive side)
Right R
Right R
Injection timing adjustment
Direction of rotation (viewed from drive side)
Right R
Right R
Injection order
1-3-4-2
Pre-stroke
mm
3.4
3.35
3.45
Beginning of injection position
Drive side NO.1
Drive side NO.1
Difference between angles 1
Cal 1-3 deg. 90 89.5 90.5
Cal 1-3 deg. 90 89.5 90.5
Difference between angles 2
Cal 1-4 deg. 180 179.5 180.5
Cal 1-4 deg. 180 179.5 180.5
Difference between angles 3
Cyl.1-2 deg. 270 269.5 270.5
Cyl.1-2 deg. 270 269.5 270.5
Injection quantity adjustment
Adjusting point
-
Rack position
12.3
Pump speed
r/min
950
950
950
Average injection quantity
mm3/st.
74.5
72.9
76.1
Max. variation between cylinders
%
0
-2.5
2.5
Basic
*
Fixing the rack
*
Standard for adjustment of the maximum variation between cylinders
*
Injection quantity adjustment_02
Adjusting point
-
Rack position
9.6+-0.5
Pump speed
r/min
300
300
300
Average injection quantity
mm3/st.
8
6.7
9.3
Max. variation between cylinders
%
0
-14
14
Fixing the rack
*
Standard for adjustment of the maximum variation between cylinders
*
Remarks
Adjust only variation between cylinders; adjust governor according to governor specifications.
Adjust only variation between cylinders; adjust governor according to governor specifications.
Injection quantity adjustment_03
Adjusting point
A
Rack position
R1(12.3)
Pump speed
r/min
950
950
950
Average injection quantity
mm3/st.
74.5
73.5
75.5
Basic
*
Fixing the lever
*
Injection quantity adjustment_04
Adjusting point
I
Rack position
14.4+-0.
5
Pump speed
r/min
150
150
150
Average injection quantity
mm3/st.
79
79
87
Fixing the lever
*
Rack limit
*
Timer adjustment
Pump speed
r/min
1150+-50
Advance angle
deg.
0
0
0
Remarks
Start
Start
Timer adjustment_02
Pump speed
r/min
1500
Advance angle
deg.
2
1.5
2.5
Remarks
Finish
Finish
Test data Ex:
Governor adjustment
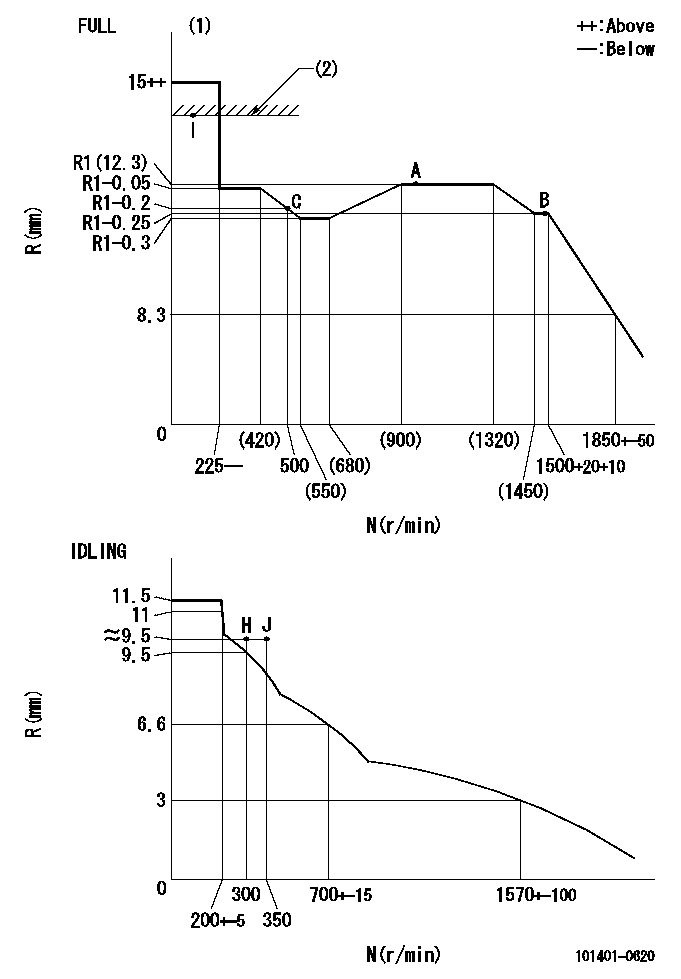
N:Pump speed
R:Rack position (mm)
(1)Torque cam stamping: T1
(2)RACK LIMIT
----------
T1=B19
----------
----------
T1=B19
----------
Speed control lever angle
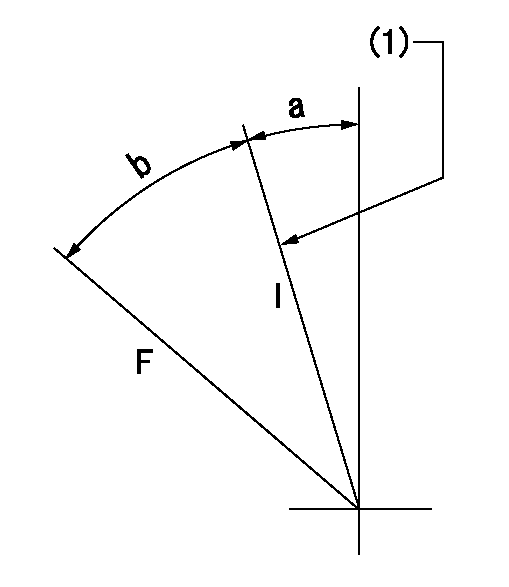
F:Full speed
I:Idle
(1)Stopper bolt set position 'H'
----------
----------
a=2.5deg+-5deg b=32deg+-3deg
----------
----------
a=2.5deg+-5deg b=32deg+-3deg
Stop lever angle
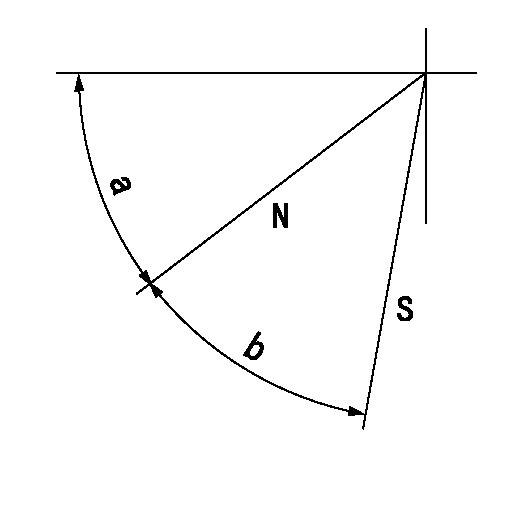
N:Pump normal
S:Stop the pump.
----------
----------
a=45deg+-5deg b=40deg+-5deg
----------
----------
a=45deg+-5deg b=40deg+-5deg
0000001501 ACS
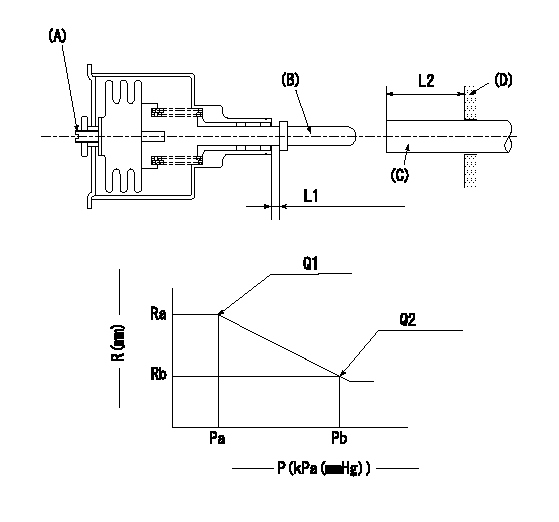
(A) Set screw
(B) Push rod 1
(C) Push rod 2
(D) Cover
1. Aneroid compensator unit adjustment
(1)Select the push rod 2 to obtain L2.
(2)Screw in (A) to obtain L1.
2. Adjustment when mounting the governor.
(1)Set the speed of the pump to N1 r/min and fix the control lever at the full set position.
(2)Screw in the aneroid compensator to obtain the performance shown in the graph above.
(3)As there is hysterisis, measure when the absolute pressure drops.
(4)Hysterisis must not exceed rack position = h1.
----------
N1=950r/min L1=(1.5)mm L2=11+-0.5mm h1=0.15mm
----------
Ra=R1(12.3)mm Rb=(R1-0.3)mm Pa=89.8+-2.7kPa(674+-20mmHg) Pb=70.1+-0.7kPa(526+-5mmHg) Q1=74.5+-1cm3/1000st Q2=71+-1.5cm3/1000st
----------
N1=950r/min L1=(1.5)mm L2=11+-0.5mm h1=0.15mm
----------
Ra=R1(12.3)mm Rb=(R1-0.3)mm Pa=89.8+-2.7kPa(674+-20mmHg) Pb=70.1+-0.7kPa(526+-5mmHg) Q1=74.5+-1cm3/1000st Q2=71+-1.5cm3/1000st
Timing setting

(1)Pump vertical direction
(2)Position of gear mark 'CC' at No 1 cylinder's beginning of injection
(3)B.T.D.C.: aa
(4)-
----------
aa=6deg
----------
a=(100deg)
----------
aa=6deg
----------
a=(100deg)
Information:
Removal
Disconnect battery negative (-) cable at the battery terminal.Allow engine to cool.Drain cooling system.Remove alternator, fan belts, fan and sheet metal fan pulley.
Fig. 1-Bypass HoseDisconnect cooling system bypass hose (Fig. 1) at top of water pump.Disconnect lower radiator hose at water pump and engine oil cooler hose at lower rear of water pump (1, Fig. 2).
Fig. 2-Water Pump RemovalRemove water pump attaching hardware (2, Fig. 2) and remove water pump from engine.Disassembly
Fig. 3-Cover Plate RemovalRemove cover plate cap screws (1, Fig. 3). Lift cover plate (2) and gasket (3) off water pump.3-164D, 3-179D, 4-219D, 4-239D, 4-276D, or 6-329D Engine
Fig. 4-D01200AA PullerUsing D01200AA Puller (Fig. 4), remove pulley or pulley hub.
Fig. 5-JD262A Bearing DriverSupport housing from impeller end. Using JD262A Bearing Driver (Fig. 5), push bearing and impeller out of housing from pulley end.
Fig. 6-0.5 in. (13 mm) DriftSupport impeller from bearing side. Using a 0.5 in. (13 mm) drift (Fig. 6), push bearing shaft out of impeller.Lift seal off bearing shaft.4-239T, 4-276T, 6-359D, 6-359T, 6-414D, or 6-414T Engine
Fig. 7-D01200AA PullerUsing D01200AA Puller, remove pulley. IMPORTANT: Do not attempt to push shaft from pulley end. A flange in the bearing bore prevents bearing passage through housing.
Fig. 8-D01200AA PullerUsing D01200AA Puller, remove impeller.
Fig. 9-Bearing ShaftSupport pulley end of housing. Select a 0.5 in. (13 mm) diameter by 3.0 in. (76 mm) drift. Push against impeller end of bearing shaft (Fig. 9) to push bearing out of housing. IMPORTANT: Always replace a bearing that has been removed from pump.Repair
Fig. 10-Seal and InsertsInspect seal (2, Fig. 10) and ceramic insert (1) for damage. The lapped surfaces can not be grooved, chipped, cracked, or scratched.If there are traces of coolant on bearing or if there was leakage from drain hole in bottom of housing, the seal is leaking.To remove metal type seal, use a punch to drive it out of the housing from the bearing side.To remove rubber type seal, peel it out of the housing from the impeller side.If seal is replaced, also remove ceramic insert and cupped rubber insert from counterbore in impeller.Inspect housing for damage behind impeller. Replace housing and impeller if metal has been scrapped away. IMPORTANT: Always replace bearing that has been removed from pump.Assembly
IMPORTANT: Do not push against end of bearing shaft. Push against outer race only.
Fig. 11-JD262A or JDE74 Bearing DriverFor water pumps on engines 3-164D, 3-179D, 4-219D, 4-239D, 4-276D and 6-329D, use JD262A Bearing Driver (Fig. 11).For water pumps on engines 4-239T, 4-276T, 6-359D, 6-359T, 6-414D and 6-414T, use JDE74 Bearing Driver (Fig. 11).Push bearing into housing until outer end of bearing is flush with the housing. IMPORTANT: Do not touch lapped surface of seal.
Fig. 12-SealSparingly coat the flange portion of the seal with joint sealing compound. Press seal into housing by hand until flange bottoms on housing (Fig. 12). Wipe away any excess joint sealing compound.
Fig. 13-InsertsPlace ceramic insert in cupped rubber insert with "V" groove on ceramic insert toward cupped rubber insert. Be sure parts are dry and clean.Dip inserts in light oil
Disconnect battery negative (-) cable at the battery terminal.Allow engine to cool.Drain cooling system.Remove alternator, fan belts, fan and sheet metal fan pulley.
Fig. 1-Bypass HoseDisconnect cooling system bypass hose (Fig. 1) at top of water pump.Disconnect lower radiator hose at water pump and engine oil cooler hose at lower rear of water pump (1, Fig. 2).
Fig. 2-Water Pump RemovalRemove water pump attaching hardware (2, Fig. 2) and remove water pump from engine.Disassembly
Fig. 3-Cover Plate RemovalRemove cover plate cap screws (1, Fig. 3). Lift cover plate (2) and gasket (3) off water pump.3-164D, 3-179D, 4-219D, 4-239D, 4-276D, or 6-329D Engine
Fig. 4-D01200AA PullerUsing D01200AA Puller (Fig. 4), remove pulley or pulley hub.
Fig. 5-JD262A Bearing DriverSupport housing from impeller end. Using JD262A Bearing Driver (Fig. 5), push bearing and impeller out of housing from pulley end.
Fig. 6-0.5 in. (13 mm) DriftSupport impeller from bearing side. Using a 0.5 in. (13 mm) drift (Fig. 6), push bearing shaft out of impeller.Lift seal off bearing shaft.4-239T, 4-276T, 6-359D, 6-359T, 6-414D, or 6-414T Engine
Fig. 7-D01200AA PullerUsing D01200AA Puller, remove pulley. IMPORTANT: Do not attempt to push shaft from pulley end. A flange in the bearing bore prevents bearing passage through housing.
Fig. 8-D01200AA PullerUsing D01200AA Puller, remove impeller.
Fig. 9-Bearing ShaftSupport pulley end of housing. Select a 0.5 in. (13 mm) diameter by 3.0 in. (76 mm) drift. Push against impeller end of bearing shaft (Fig. 9) to push bearing out of housing. IMPORTANT: Always replace a bearing that has been removed from pump.Repair
Fig. 10-Seal and InsertsInspect seal (2, Fig. 10) and ceramic insert (1) for damage. The lapped surfaces can not be grooved, chipped, cracked, or scratched.If there are traces of coolant on bearing or if there was leakage from drain hole in bottom of housing, the seal is leaking.To remove metal type seal, use a punch to drive it out of the housing from the bearing side.To remove rubber type seal, peel it out of the housing from the impeller side.If seal is replaced, also remove ceramic insert and cupped rubber insert from counterbore in impeller.Inspect housing for damage behind impeller. Replace housing and impeller if metal has been scrapped away. IMPORTANT: Always replace bearing that has been removed from pump.Assembly
IMPORTANT: Do not push against end of bearing shaft. Push against outer race only.
Fig. 11-JD262A or JDE74 Bearing DriverFor water pumps on engines 3-164D, 3-179D, 4-219D, 4-239D, 4-276D and 6-329D, use JD262A Bearing Driver (Fig. 11).For water pumps on engines 4-239T, 4-276T, 6-359D, 6-359T, 6-414D and 6-414T, use JDE74 Bearing Driver (Fig. 11).Push bearing into housing until outer end of bearing is flush with the housing. IMPORTANT: Do not touch lapped surface of seal.
Fig. 12-SealSparingly coat the flange portion of the seal with joint sealing compound. Press seal into housing by hand until flange bottoms on housing (Fig. 12). Wipe away any excess joint sealing compound.
Fig. 13-InsertsPlace ceramic insert in cupped rubber insert with "V" groove on ceramic insert toward cupped rubber insert. Be sure parts are dry and clean.Dip inserts in light oil