Information injection-pump assembly
BOSCH
9 400 613 544
9400613544
ZEXEL
101401-0040
1014010040
ISUZU
5156004742
5156004742
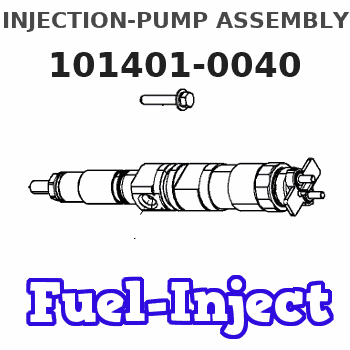
Rating:
Service parts 101401-0040 INJECTION-PUMP ASSEMBLY:
1.
_
6.
COUPLING PLATE
7.
COUPLING PLATE
8.
_
9.
_
11.
Nozzle and Holder
5-15300-065-1
12.
Open Pre:MPa(Kqf/cm2)
18.1{185}
15.
NOZZLE SET
Cross reference number
BOSCH
9 400 613 544
9400613544
ZEXEL
101401-0040
1014010040
ISUZU
5156004742
5156004742
Zexel num
Bosch num
Firm num
Name
101401-0040
9 400 613 544
5156004742 ISUZU
INJECTION-PUMP ASSEMBLY
4BB1-2 * K
4BB1-2 * K
Calibration Data:
Adjustment conditions
Test oil
1404 Test oil ISO4113 or {SAEJ967d}
1404 Test oil ISO4113 or {SAEJ967d}
Test oil temperature
degC
40
40
45
Nozzle and nozzle holder
105780-8140
Bosch type code
EF8511/9A
Nozzle
105780-0000
Bosch type code
DN12SD12T
Nozzle holder
105780-2080
Bosch type code
EF8511/9
Opening pressure
MPa
17.2
Opening pressure
kgf/cm2
175
Injection pipe
Outer diameter - inner diameter - length (mm) mm 6-2-600
Outer diameter - inner diameter - length (mm) mm 6-2-600
Overflow valve
132424-0620
Overflow valve opening pressure
kPa
157
123
191
Overflow valve opening pressure
kgf/cm2
1.6
1.25
1.95
Tester oil delivery pressure
kPa
157
157
157
Tester oil delivery pressure
kgf/cm2
1.6
1.6
1.6
Direction of rotation (viewed from drive side)
Right R
Right R
Injection timing adjustment
Direction of rotation (viewed from drive side)
Right R
Right R
Injection order
1-3-4-2
Pre-stroke
mm
3.6
3.55
3.65
Beginning of injection position
Drive side NO.1
Drive side NO.1
Difference between angles 1
Cal 1-3 deg. 90 89.5 90.5
Cal 1-3 deg. 90 89.5 90.5
Difference between angles 2
Cal 1-4 deg. 180 179.5 180.5
Cal 1-4 deg. 180 179.5 180.5
Difference between angles 3
Cyl.1-2 deg. 270 269.5 270.5
Cyl.1-2 deg. 270 269.5 270.5
Injection quantity adjustment
Adjusting point
A
Rack position
10.5+-0.
5
Pump speed
r/min
1000
1000
1000
Average injection quantity
mm3/st.
53
52
54
Max. variation between cylinders
%
0
-2.5
2.5
Basic
*
Fixing the lever
*
Injection quantity adjustment_02
Adjusting point
B
Rack position
10.25+-0
.5
Pump speed
r/min
1650
1650
1650
Average injection quantity
mm3/st.
49.8
48.2
51.4
Fixing the lever
*
Injection quantity adjustment_03
Adjusting point
C
Rack position
10.45+-0
.5
Pump speed
r/min
1350
1350
1350
Average injection quantity
mm3/st.
54.8
53.2
56.4
Fixing the lever
*
Injection quantity adjustment_04
Adjusting point
D
Rack position
10.35+-0
.5
Pump speed
r/min
700
700
700
Average injection quantity
mm3/st.
41.8
39.4
42.6
Fixing the lever
*
Injection quantity adjustment_05
Adjusting point
E
Rack position
11.15+-0
.5
Pump speed
r/min
500
500
500
Average injection quantity
mm3/st.
47.8
45.8
49.8
Fixing the lever
*
Injection quantity adjustment_06
Adjusting point
F
Rack position
10.7+-0.
5
Pump speed
r/min
600
600
600
Average injection quantity
mm3/st.
44
42
46
Fixing the lever
*
Injection quantity adjustment_07
Adjusting point
-
Rack position
9.5+-0.5
Pump speed
r/min
300
300
300
Average injection quantity
mm3/st.
8
6.7
9.3
Max. variation between cylinders
%
0
-14
14
Fixing the rack
*
Injection quantity adjustment_08
Adjusting point
I
Rack position
13.2+-0.
5
Pump speed
r/min
100
100
100
Average injection quantity
mm3/st.
72
72
77
Fixing the rack
*
Remarks
Rack limit setting
Rack limit setting
Timer adjustment
Pump speed
r/min
1100+-50
Advance angle
deg.
0
0
0
Remarks
Start
Start
Timer adjustment_02
Pump speed
r/min
1300
Advance angle
deg.
0.8
0.3
1.3
Timer adjustment_03
Pump speed
r/min
1500
Advance angle
deg.
2
1.5
2.5
Timer adjustment_04
Pump speed
r/min
1650
Advance angle
deg.
3
2.5
3.5
Timer adjustment_05
Pump speed
r/min
-
Advance angle
deg.
5
5
5
Remarks
Measure the actual speed, stop
Measure the actual speed, stop
Test data Ex:
Governor adjustment
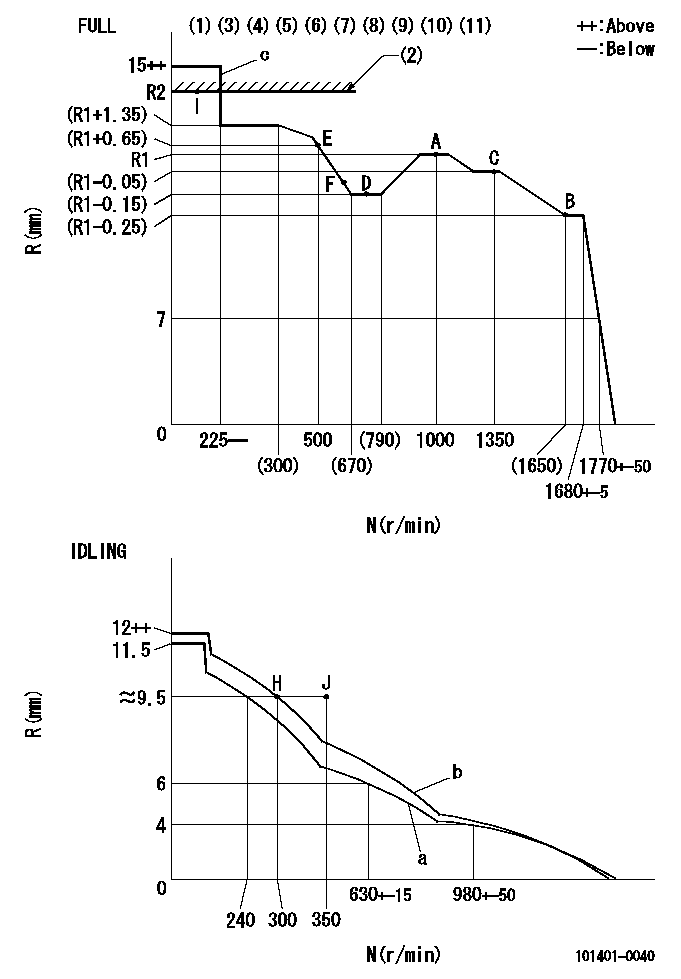
N:Pump speed
R:Rack position (mm)
(1)Torque cam stamping: T1
(2)RACK LIMIT
(3)Because the figures in brackets are the target values at torque cam adjustment, perform final adjustment in accordance with governor and injection quantity adjustment standards.
(4)Perform governor spring adjustment by setting lever a.
(5)After adjustment of the lever a setting, set the lever so that idle set point H can be obtained and confirm standard b.
(6)After completing final adjustment, set the lever to obtain J.
(7)Next, confirm rack position R1 or more is obtained when rotation is stopped.
(8)In this condition, move the lever to the full position and confirm standard c. (excess fuel for starting operation limit).
(9)After completing final adjustment, set speed at N1 using lever b.
(10)In this condition, after operating the lever to the full position, confirm no excess fuel for starting (black smoke prevention limit).
(11)For the excess fuel setting for starting rack position point I set the lever to obtain standard c in step (8) and then set the rack limit.
----------
T1=07 R1=12mm N1=225r/min
----------
----------
T1=07 R1=12mm N1=225r/min
----------
Speed control lever angle
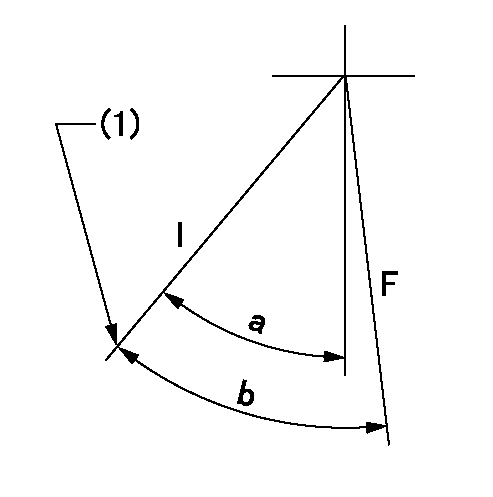
F:Full speed
I:Idle
(1)Stopper bolt set position 'b.'
----------
----------
a=30deg+-5deg b=41deg+-3deg
----------
----------
a=30deg+-5deg b=41deg+-3deg
Information:
* Select an appropriate cleaning method according to the condition of the cooling system as shown below.
* FUSO DIESEL LONGLIFE COOLANT is flammable. Keep them away from heat and flames.
* If you accidentally splash FUSO DIESEL LONGLIFE COOLANT, FUSO ANTIFREEZE, OR RADIATOR ANTIRUST (RADIPET 9) in your eyes, wash it out immediately with water and seek medical attention.
Air Bleeding of Cooling System
* With the pressure cap removed and the coolant temperature at 90°C, let the engine idle in order to bleed air completely out of the cooling system.* After air bleeding is completed, refill the reservoir tank with coolant as needed.Air/Gas Leakage Test
* Presence of air or exhaust gas in coolant accelerates corrosion of the cooling system components. To prevent this, carry out air/gas leakage tests in accordance with the following procedure.* Remove the pressure cap.
* If the engine is hot, boiling coolant may spurt out from the filler port when the pressure cap is loosened. To avoid being scold, make sure to remove the pressure cap only when the coolant is cold.
* Run the engine until the coolant temperature rises to approximately 90°C. * If air bubbles appear continuously through the filler port, there is air or exhaust gas penetrating into the cooling system.* Presence of air in coolant can be an indication of loose cylinder head bolts, loose water pump mounting bolts, loose hose connections, and/or a damaged hose.* Presence of exhaust gas in coolant can be an indication of a damaged cylinder head gasket and/or cracks in the cylinder head.Inspection of Coolant Leak
* With the engine idling, check the coolant passage (radiator hose, water hose, etc.) for coolant leak.* If any leak is found, check the installation condition of each part and retighten the loose part to the specified torque.If any crack or damage is found on a pipe or hose, replace it to a new one.Coolant Fan, Belt And Water Pump
Removal Sequence1 Cooling fan2 Fan spacer3 Belt4 Water pump pulley5 Water pump6 O-ringX: Non-reusable parts* The water pump cannot be disassembled. It must be replaced if defective. Installation SequenceFollow the removal sequence in reverse.
* The water pump pulley is driven by two belts. Always replace the two belts simultaneously to ensure that both belts have the same tension.* Make sure that there is no oil or grease on the belts. Belts soiled with oil or grease may easily slip, resulting in deteriorated performance of the cooling system.* Keep the O-ring free from engine oil. Engine oil will make the O-ring swell, which may cause leakage.
* After installation, check and adjust the belt tension. (See "GENERAL INSPECTION AND ADJUSTMENT".)Lubricant and/or sealant Water Hose And Pipe
Disassembly Sequence1 Heater return pipe2 O-ring3 Water temperature sensor4 Water outlet pipe5 Gasket*a: Thermostat caseX: Non-reusable parts Assembly SequenceFollow the disassembly sequence in reverse.
* Keep the O-ring free of engine oil. Engine oil will make the O-ring swell, which may cause leakage.
Tightening Torque (Unit: N m {kgf m}) Lubricant and/or sealant Thermostat
Disassembly Sequence1 Thermostat cover2 Thermostat3 Bypass Pipe4 O-ring5 Thermostat
* FUSO DIESEL LONGLIFE COOLANT is flammable. Keep them away from heat and flames.
* If you accidentally splash FUSO DIESEL LONGLIFE COOLANT, FUSO ANTIFREEZE, OR RADIATOR ANTIRUST (RADIPET 9) in your eyes, wash it out immediately with water and seek medical attention.
Air Bleeding of Cooling System
* With the pressure cap removed and the coolant temperature at 90°C, let the engine idle in order to bleed air completely out of the cooling system.* After air bleeding is completed, refill the reservoir tank with coolant as needed.Air/Gas Leakage Test
* Presence of air or exhaust gas in coolant accelerates corrosion of the cooling system components. To prevent this, carry out air/gas leakage tests in accordance with the following procedure.* Remove the pressure cap.
* If the engine is hot, boiling coolant may spurt out from the filler port when the pressure cap is loosened. To avoid being scold, make sure to remove the pressure cap only when the coolant is cold.
* Run the engine until the coolant temperature rises to approximately 90°C. * If air bubbles appear continuously through the filler port, there is air or exhaust gas penetrating into the cooling system.* Presence of air in coolant can be an indication of loose cylinder head bolts, loose water pump mounting bolts, loose hose connections, and/or a damaged hose.* Presence of exhaust gas in coolant can be an indication of a damaged cylinder head gasket and/or cracks in the cylinder head.Inspection of Coolant Leak
* With the engine idling, check the coolant passage (radiator hose, water hose, etc.) for coolant leak.* If any leak is found, check the installation condition of each part and retighten the loose part to the specified torque.If any crack or damage is found on a pipe or hose, replace it to a new one.Coolant Fan, Belt And Water Pump
Removal Sequence1 Cooling fan2 Fan spacer3 Belt4 Water pump pulley5 Water pump6 O-ringX: Non-reusable parts* The water pump cannot be disassembled. It must be replaced if defective. Installation SequenceFollow the removal sequence in reverse.
* The water pump pulley is driven by two belts. Always replace the two belts simultaneously to ensure that both belts have the same tension.* Make sure that there is no oil or grease on the belts. Belts soiled with oil or grease may easily slip, resulting in deteriorated performance of the cooling system.* Keep the O-ring free from engine oil. Engine oil will make the O-ring swell, which may cause leakage.
* After installation, check and adjust the belt tension. (See "GENERAL INSPECTION AND ADJUSTMENT".)Lubricant and/or sealant Water Hose And Pipe
Disassembly Sequence1 Heater return pipe2 O-ring3 Water temperature sensor4 Water outlet pipe5 Gasket*a: Thermostat caseX: Non-reusable parts Assembly SequenceFollow the disassembly sequence in reverse.
* Keep the O-ring free of engine oil. Engine oil will make the O-ring swell, which may cause leakage.
Tightening Torque (Unit: N m {kgf m}) Lubricant and/or sealant Thermostat
Disassembly Sequence1 Thermostat cover2 Thermostat3 Bypass Pipe4 O-ring5 Thermostat
Have questions with 101401-0040?
Group cross 101401-0040 ZEXEL
Isuzu
101401-0040
9 400 613 544
5156004742
INJECTION-PUMP ASSEMBLY
4BB1-2
4BB1-2